Given Dave Aldred has kindly done the previous updates whilst we were getting things organised for the build, I thought it time that I wrote a piece for the website by way of introducing myself as the Driver and Project Lead of Longbow to those following our venture. So as Dave would say, make yourself a brew, grab a biscuit and sit down for a minute to have a read as follows.
Last year and going into this year has been busy with my day job as a Royal Navy pilot (albeit based at an RAF station….), where I have combined my primary role of conducting routine competence tests on military flying instructors, with bringing a new turboprop training aircraft (the Grob 120TP Prefect as shown with yours truly below) into service for the military:
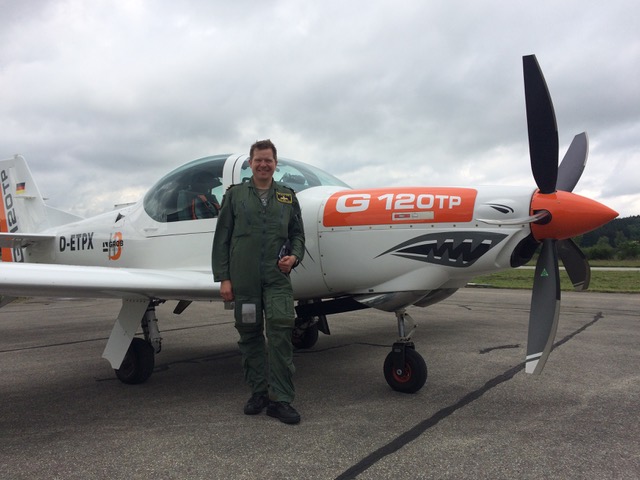
This has been an undoubted career highlight, and involved a lot of time at the manufacturers facility in Germany performing evaluation flights to explore what the aircraft was capable of, although the associated paperwork compensated for all the airborne fun. I have also been busy in my occasional Saturday jobs of flying vintage propeller aeroplanes and teaching people to fly the vintage Jet Provost.
Incidentally, my connections in the classic jet community have proved invaluable in not only sourcing a pair of Rolls-Royce Viper jet engines, but also in obtaining the necessary ancillaries needed to run them. Away from the air I was able to race my Formula 4 powerboat whenever time has allowed, which sadly was not as much as I would have liked last season, and have been getting my head back into the old Aeronautical Engineering degree textbooks in the loft, which are proving invaluable in the design of Longbow.
Something from work worth expanding on was a training session at the infamous centrifuge at Farnborough, where pilots are sat in a capsule at the end of a long arm and spun around by a massive electric motor, in order to expose them to various levels of G force. It is worth a brief explanation of G forces, as they have a relevance to our jet hydroplane Longbow.
We have all experienced G forces, probably without realising it. If you get in your car and accelerate hard, you feel a force pushing you back in to your seat. If you go around a corner quickly you feel yourself being pushed sideways, and if you go over a humpback bridge you feel a little heavier as you go up the slope, and a little bit of weightless as you go over the top of the hump. These are all G forces acting in the fore and aft, sideways and up and down directions respectively. The force of 1G is the force that gravity exerts to a body at rest; G forces are measured in multiples of this force. Sitting in your chair reading this you are experiencing 1G in the downward direction (known as normal acceleration) by Engineers but believe me, when that G loading increases significantly it feels anything but normal. Lying on your side you are experiencing 1G in a sideways (called lateral) direction and if you were to accelerate really hard in a high performance car you will experience almost 1G in the fore and aft direction.
A car and powerboat racer can experience 4 or 5 lateral G during cornering. By far the worst direction for a human body is the normal acceleration case, and this is what the centrifuge generates. Pilots experience this in steeply banked turns (unlike a car or powerboat an aeroplane banks into a turn so the G forces act straight down, not laterally) and during aerobatics, where normal accelerations of 5 or 6 G are often achieved. If this acceleration is sustained for more than a few seconds blood tends to pool in the legs and abdomen, lowering blood pressure to the brain leading initially to a greying of vision, followed by a complete loss of vision and then unconsciousness, all over the period of a few seconds.
By tensing the legs and abdomen and using special breathing techniques the blood pressure in the head, and hence full compos mentis can be maintained, You can see from the photos below of me looking relaxed (relatively!) at 1G prior to the start of my centrifuge run, and straining hard (yes laugh away all you like at my expression but say that when you have experienced it) at a sustained 5G to maintain consciousness.
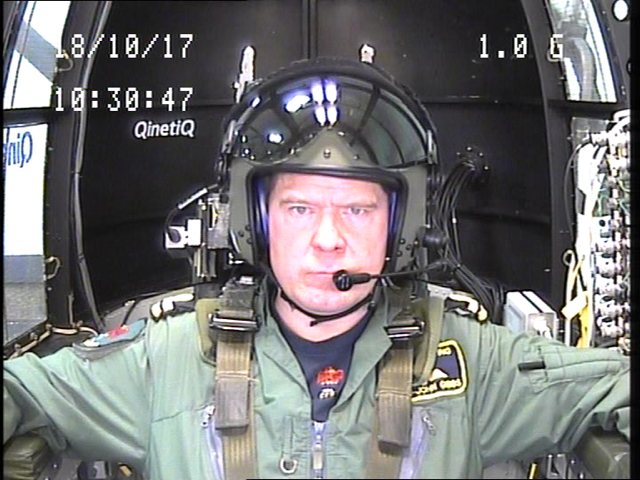
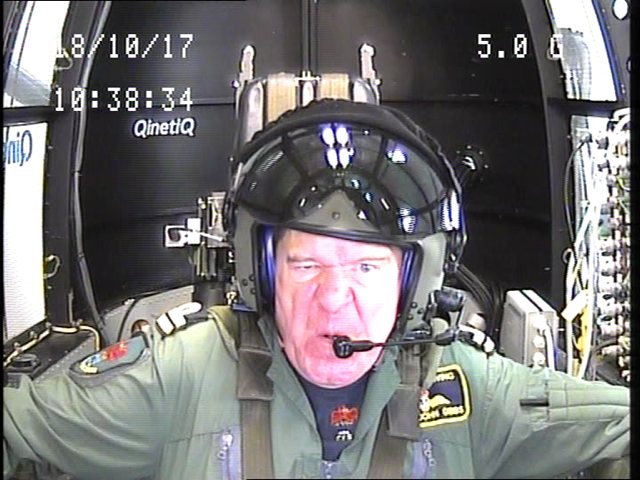
Fortunately for Longbow the predominant forces will be in the fore and aft direction as the boat accelerates and decelerates, which has little effect on consciousness, as blood pressure in the head is largely unaffected. In fact, the human body is extremely well adapted for these accelerations, and can tolerate a massive amount for a very short time; in the 1950s US Air Force Colonel Paul Stapp conducted experiments on himself using a rocket sled: he survived a massive 45G deceleration on one run, which is probably more than experienced in most head-on car crashes.
Although time and effort is primarily being spent upon ensuring the craft does not become airborne or suffer a tumble, we did however ask Dr. Ben Evans who did much of the CFD work for the Bloodhound land speed car and his students to look at forces involved with the floatable breakaway driver capsule and in particular the G forces involved in the case of a catastrophic event occurring at a sample speed of 400mph:
Simulation parameters:
o CAD geometry provided by Longbow project.
o Speed – 400mph, 178.8m/s.
o Fluid density – 1,000kg/m³
o Fluid kinematic viscosity – 1.0e-6 m²/s.
o Surface tension coefficient – 0.0728.
o Number of lattice cells – 143,584,000.
o Physical time simulated – 0.0378s.
o Number of iterations – 54,200.
o Run time – ~40 hours on 256 cores with 8GB memory per CPU.
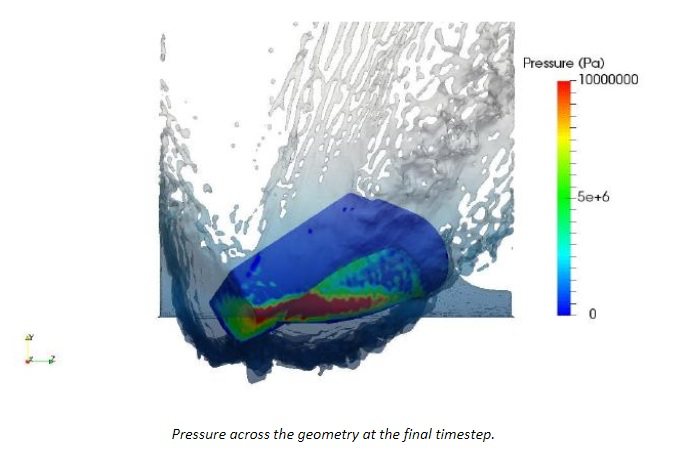
The geometry was positioned based roughly on video footage of drag boat capsule incidents:
https://www.youtube.com/watch?v=t43zdpJuwIM#t=22s
The solver is currently only capable of running static geometries, and as a result rigid body FluidStructure Interaction (FSI) is not fully modelled. The static geometry position and degree of submergence (indicated by the blue area) is shown below:
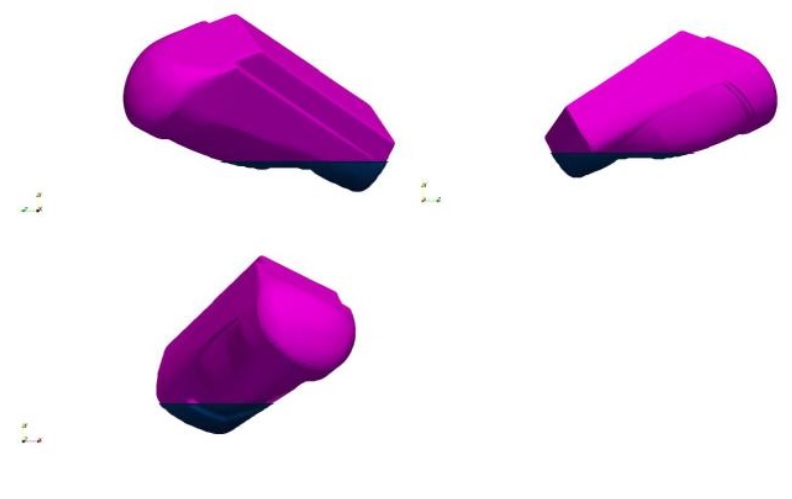
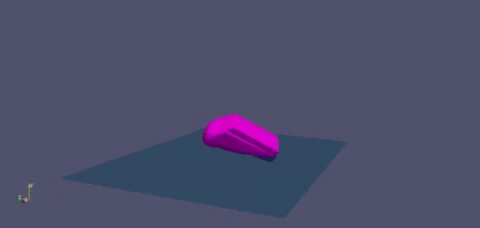
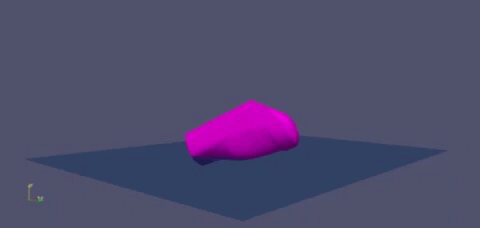
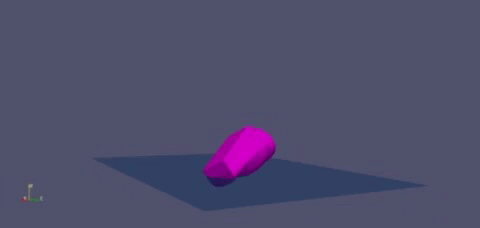
The results of the analysis are currently not being published by ourselves as the analysis is not yet complete. However even to a layperson it should be obvious that having an accident occur at 400mph is clearly something to be avoided and it is therefore essential that we adopt the same risk averse approach to the venture that reflects ones military training as a pilot.
As we move to the construction phase of the craft itself it was necessary to have all the gas turbines, jet pipes, interpipes and ancillaries at the main workshop and these were duly collected by Dave and Fred from storage and delivered to site with the help of Rob whilst Alice and Riley look on through the window given it is not everyday a jet engine arrives.
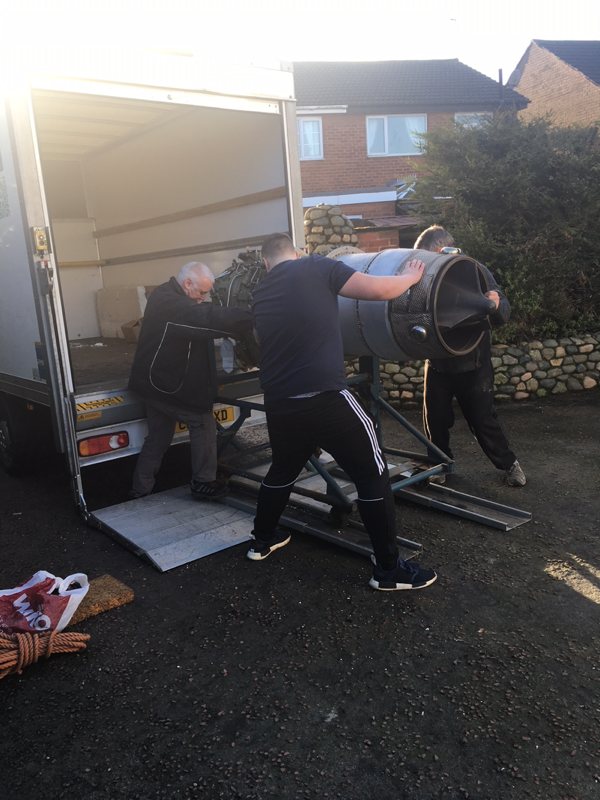
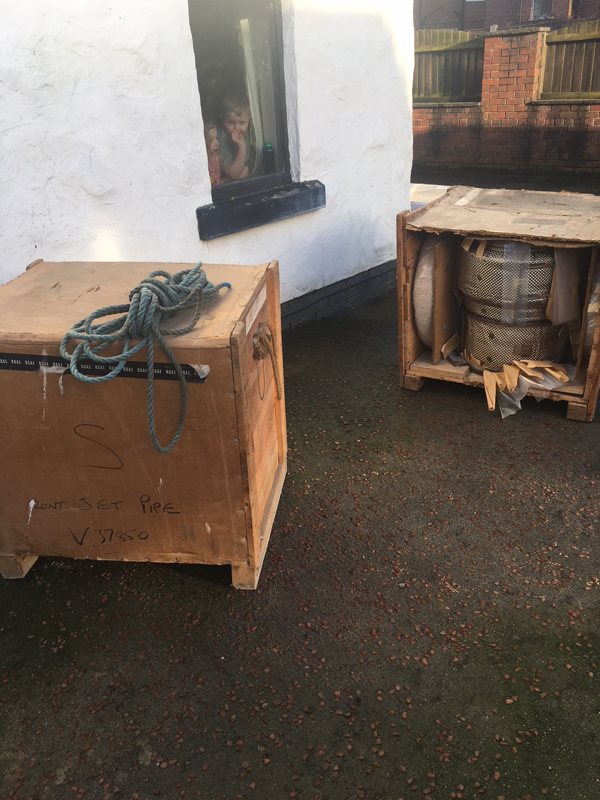
The jet pipes from the Strikemaster aircraft for the Viper gas turbine, have a bend to them part way along in order to get over a spar within the airframe. Whether we retain this feature within the craft is currently something we are looking at. in any case with space limited within the workshop they were safely hauled up by Tom and Dave on pulleys and lashed to the steel purlins, out of harms way:
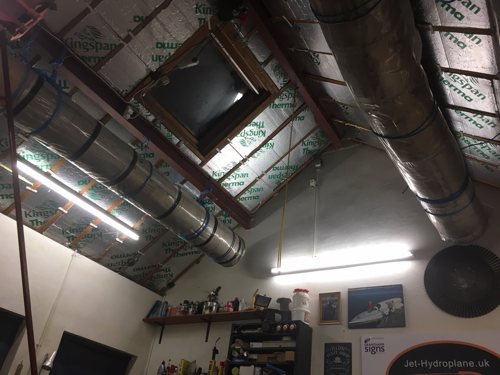
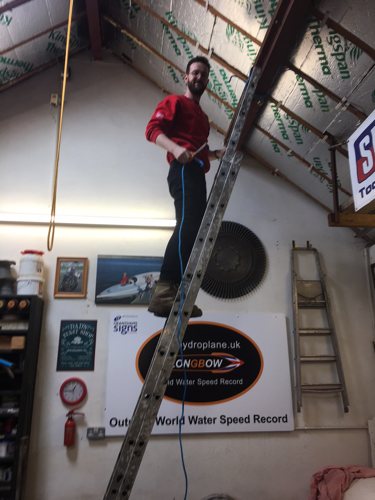
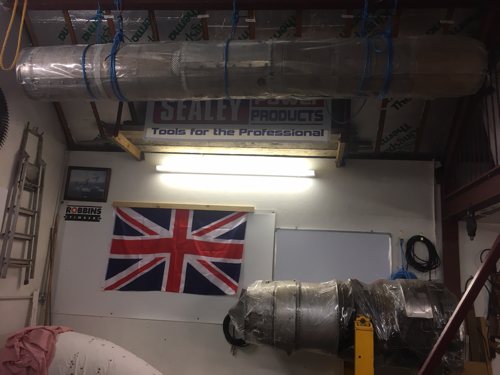
Meanwhile Steve has been working every night of the week and all his weekends getting his rear extension completed, new kitchen fitted, full house re-wire, plastered not only the extension but also the entire bungalow and fitted new fireplaces, new feature slate tiling to lounge walls, new boiler and central heating system throughout, new en-suite and new main bathroom.
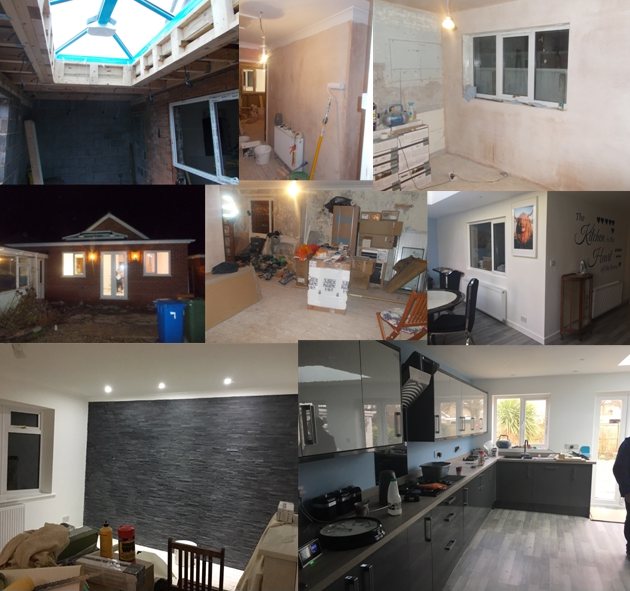
Not bad for one very highly skilled lad working in his spare time mostly on his own in only a few months. This is why him and Dave who designed / built his own cottage and workshop / garage make such a good team when it comes to seeing a job through. As these two set about building the hull for Longbow under my design authority after their work on the Bluebird replica K777 and Bluebird K7, you can be confident that Longbow is actually going to come to fruition.
It was only fair that we let Steve get the majority of his mammoth home renovation project completed rather than drag it out any longer than necessary by taking him off it to commence building the hull. In addition as stated in our last update we have had to wait for our special order of high grade timber being shipped from the USA to our timber sponsor Robbins. That shipment arrived at the end of January and we are now ready to commence with the build. Sealey another one of our product sponsors are kindly lending us electric heaters for the workshop that provide a ‘dry’ heat which is essential if the epoxy is to cure appropriately and without contamination from wet heaters such as LPG or paraffin.
I have just completed this years annual dunk test for my Formula 4 powerboat and it has also just passed the revised UIM / RYA cockpit ruling with regards to head clearance, which increased to 10cm this year to take greater allowance for stretching of the seat harness in the event of a tumble.
Our next update should come along relatively quickly to report upon arrival of the timber for the main stringers so please keep tuned folks, as this is where the interesting and fun bit really starts !