To kick off this month’s update, our good friend Dave Warby reports exclusively back to us as follows, on the development of his jet hydroplane Spirit of Australia II where Dave and his Team travelled to Blowering Dam, New South Wales, Australia a couple of weeks ago:
“After our testing at Taree in April we identified a slight twisting of the vertical aero stabilizer which we feel may have been caused by heat. This misalignment affected the boats handling so a new vertical stabilizer was built and fitted the to boat before our May test at Blowering Dam. We knew prior to arrival at the Dam that the amount of water was going to be low as a good deal had been let out for farming during our very hot summer in Australia but when we arrived it was down to only about 25% of its normal volume.
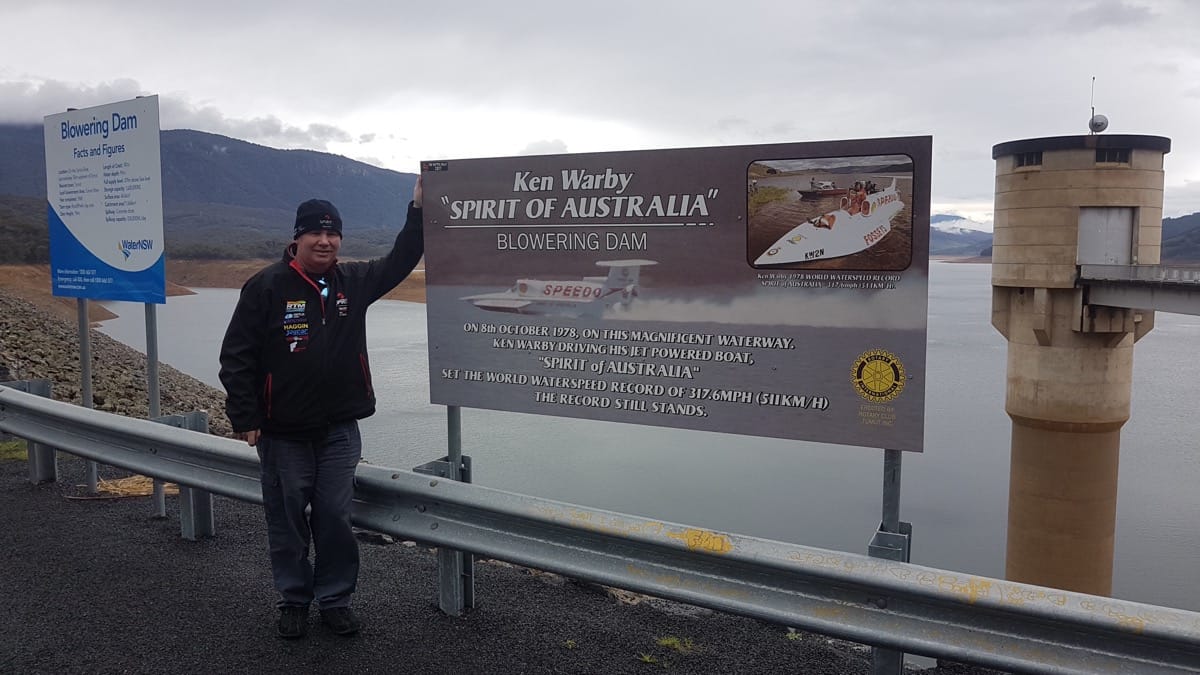
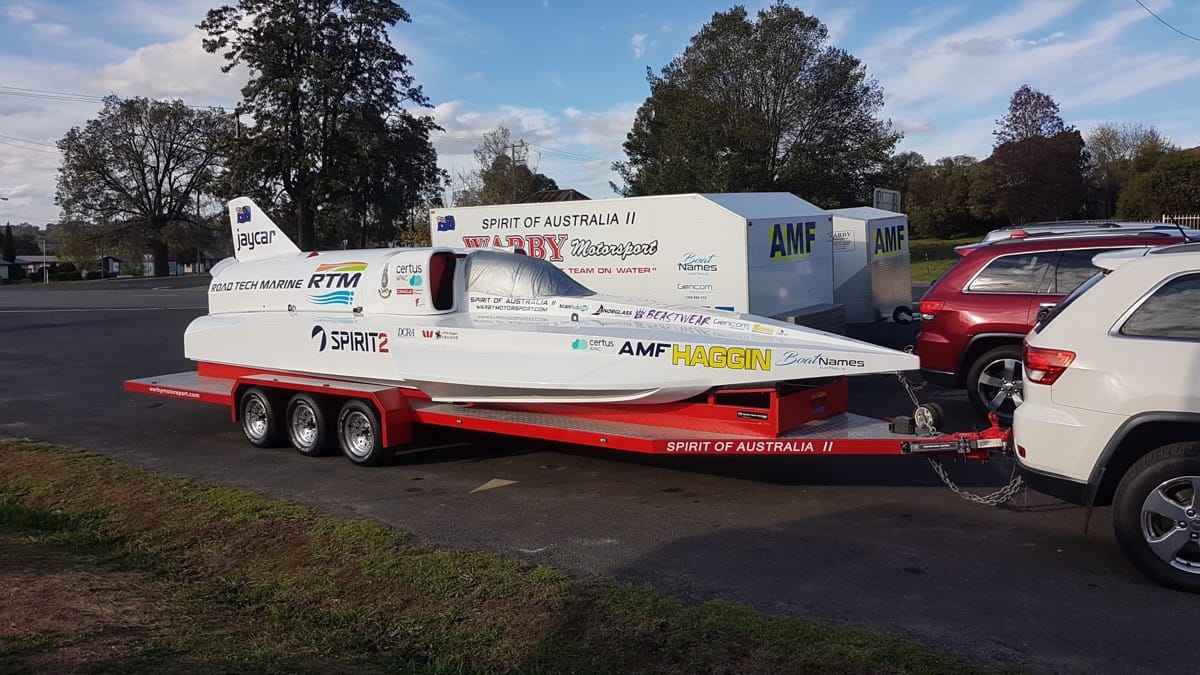

As the water level at the Dam was so low, we couldn’t use the area of the Dam we would normally use, which is more sheltered from the wind between the mountains. Instead we had to use around 4 to 5 km stretch of water from the Dam wall itself to our base camp at The Pines boat ramp. This is a more exposed part of the Dam so more readily affected by the weather and in particular the winds, compared to that which we would normally run on… but good enough to get some test runs in.
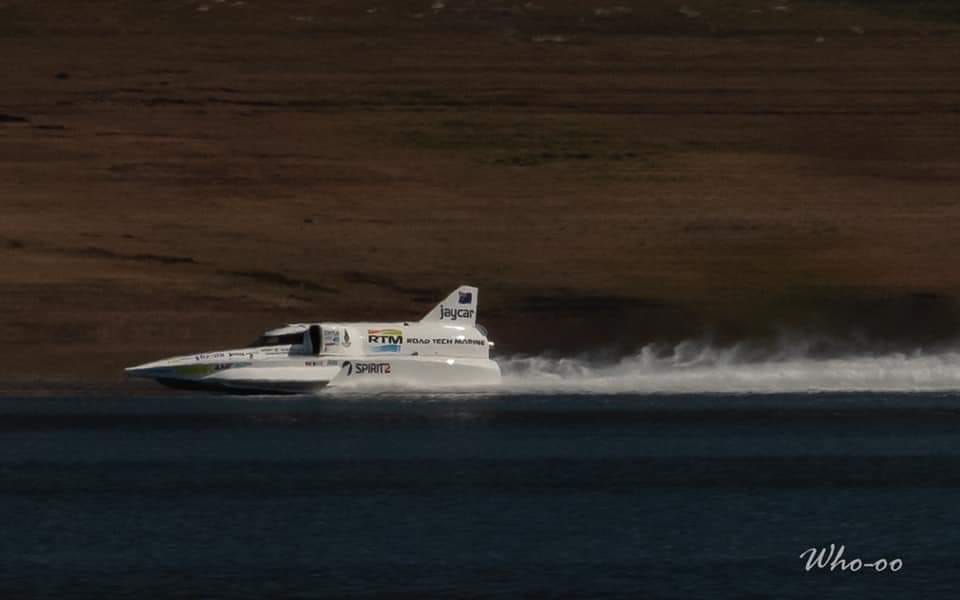
Our first few runs on Saturday were in the 180mph region, to get familiar with the landmarks we were using for this area of the Dam being different to that which we would normally use. I found the top end near the Dam wall quite rough, but it settled down around halfway along our course.
On Sunday we made 3 runs at sustained speeds: 210mph, 221mph and 235mph. The new vertical stabilizer worked really well and the boat handling was the best to date. Our 235mph run was done using only 80% thrust (where jet engines start to make their serious power) and we held 230mph for 1.5kms. However the top end of the course was so rough, we cracked the centre fuel tank mounts on our 235mph run.
https://youtu.be/JFx7S6gANAs
We tried for a 4th run but unfortunately we had engine starter battery issues, which caused a hung start, or hot start as it is sometimes called, so we called it a day.
We are extremely encouraged by our May tests. The boat is handling well. We know the boat has more than enough power for the Record. Our safety team did an ‘on water’ practice emergency rescue, and our ‘start & on water servicing’ team have had more training and on water experience, which is just as important as testing the boat.
We will now look towards late August for our next test at Blowering, the Dam is currently filling up nicely, which will allow us to return to the world record course with more room and better water. The period between now and then will give us time to do some repairs and check over the boat”.
You can find out more about Spirit of Australia II here warbymotorsport.com.
Returning to our own jet hydroplane Longbow, working on the principle that it is better to have and not need, than to need and not have, we managed to source and purchase another Viper jet engine of the same model to our other engines for the craft. This jet engine, just like our others, comes with the important flight hours remaining and complete set of paperwork. The intention is to have all of the jet engines we have, proven within a test rig and the students under the guidance of their lecturers, at our local educational sponsor, Blackpool & Fylde College are very kindly assisting us with this task.
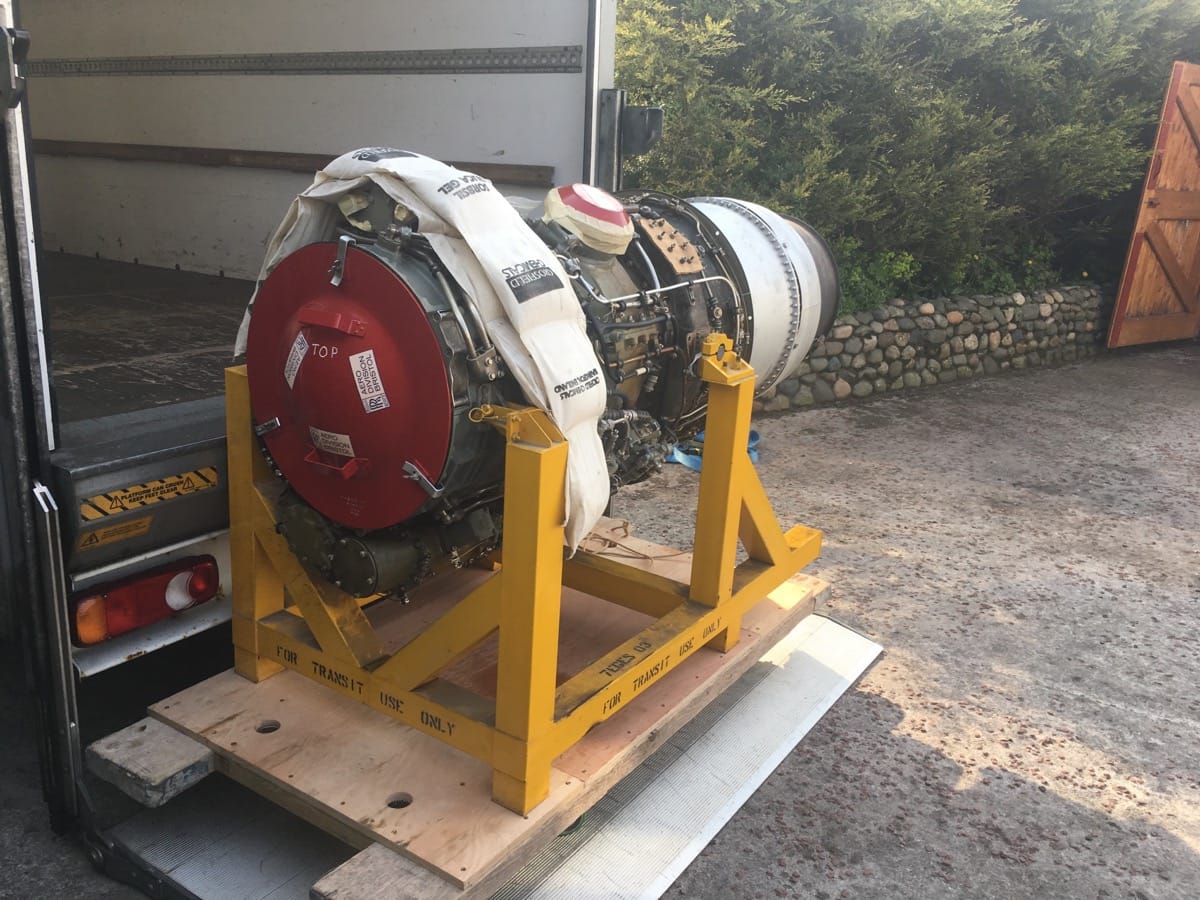
On the continuing build of the hull for Longbow, the next job was to make the glue blocks to the underside of the hull that will provide the necessary support and bond area where one section of the underside, as yet to be fitted will eventually meet another. These blocks are shaped on one face so as to provide the continuous joint area to the underside of the hull whilst on the opposing face as seen from within the hull, craftily allowing a means by which any water that finds its way into the hull, can be drained towards the transom. They were fitted into place using West System Epoxy supplied by our sponsor Wessex Resins and also mechanically attached with stainless screws by our sponsor Avon Stainless Steel Fasteners:
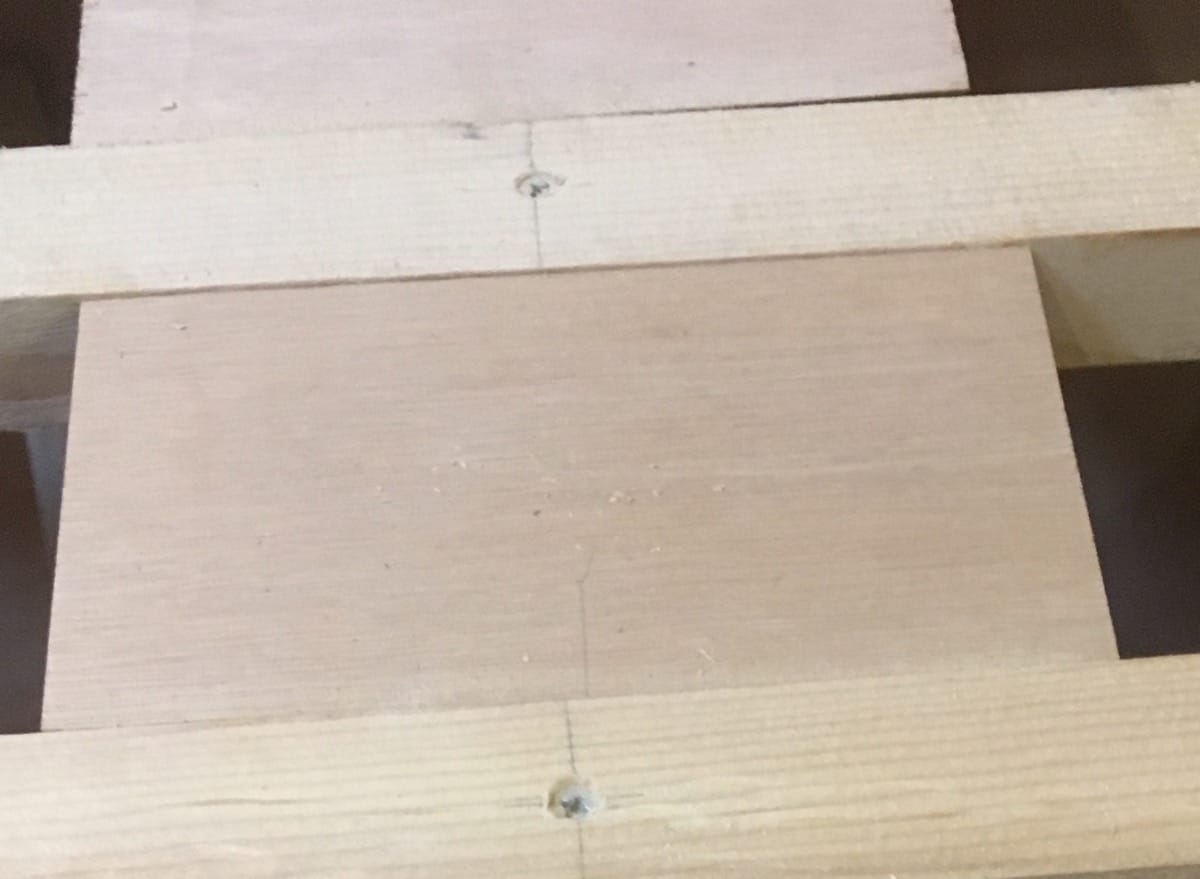
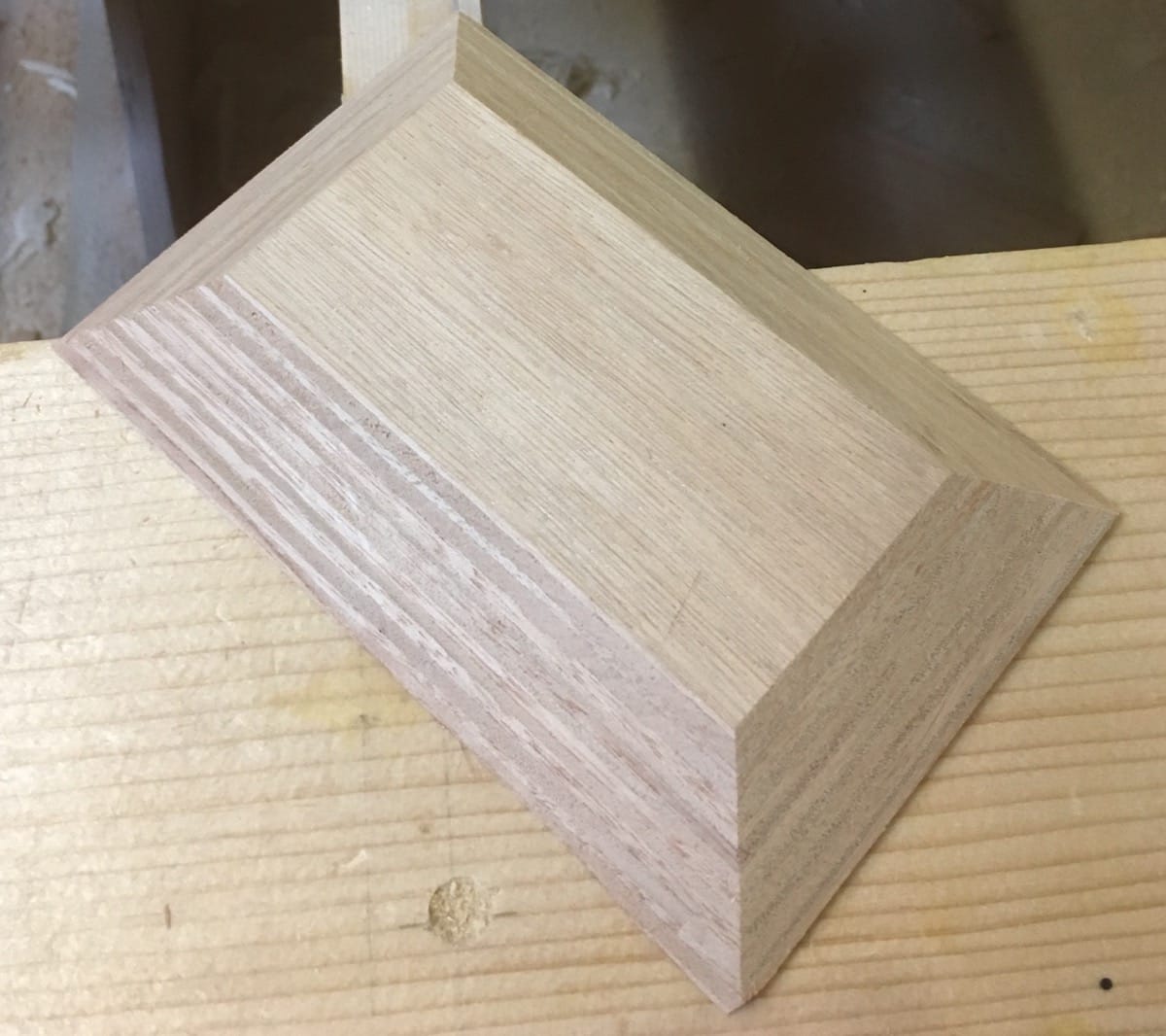
Once all these glue blocks were in place we could then move on to cutting the rebates into the side frames along the length of the hull and fitting the timber mid rails supplied by another of our sponsors Robbins timber. Again the attachment was done using West System Epoxy and screws. Of note and as shown in the photos below we are using pull saws for many of the hand cut joints and if you have never used them before on your woodworking projects, may we suggest you give them a try. If you can get used to the cut being made on the pull stroke then you should find that for detailed work, they cut more efficiently and provide a narrower cut (termed kerf) than saws which cut on the push stroke. Also as the cut is made with the blade in tension we find this tends to give a straighter cut than a saw cutting on the push stroke / in compression.
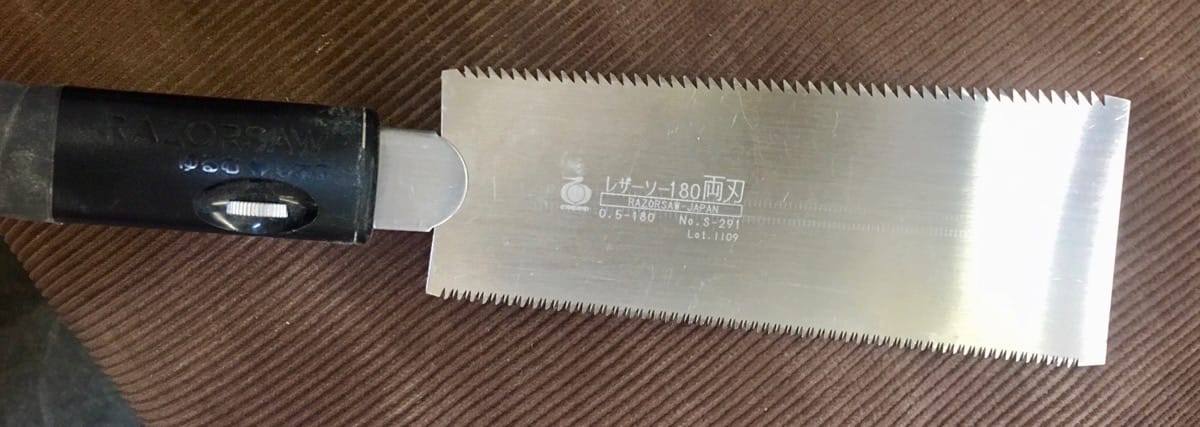
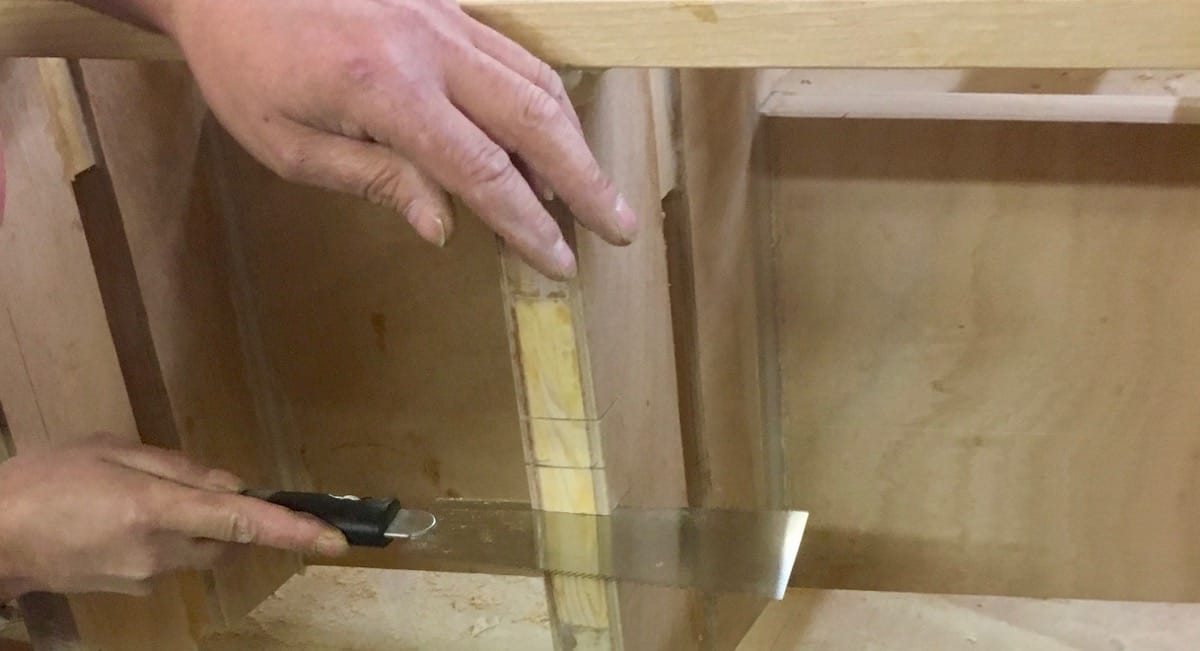
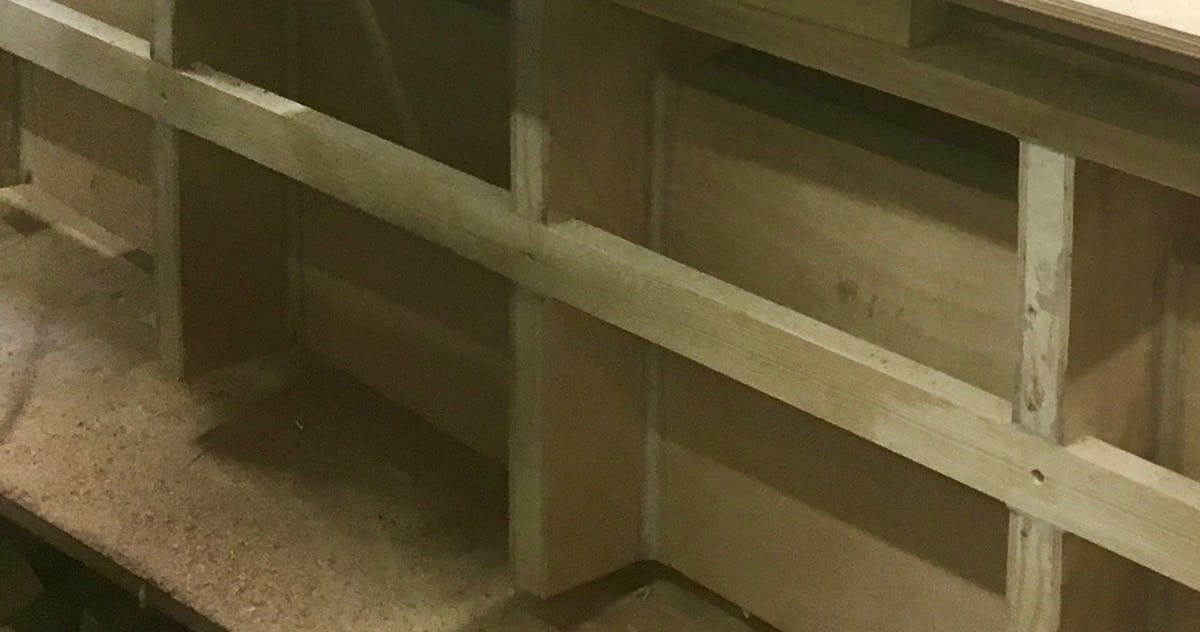
As you will recall from previous diary updates we had to date built Longbow upside down in order to provide access to form the underside rails, keel etc. However once the mid rails on the sides of the hull were in place, the next job would be to form the top outer rails of the hull. Whilst we could have continued to do this with the hull upside down, we decided that, at least for us, it would probably be easier to do this with the hull the right way up, which obviously meant turning her over.
We knew that there was not enough height in the forward section of the workshop with the build table in place, to allow spinning her over in-situ, so the only option was picking the hull of Longbow up and walking her outside to turn her the right way up. I had a quick chat with Dave (Warby) about this and he reckoned about 10 Aussies would be needed so obviously I had to recalculate this to the Pommy equivalent!
Ask the guys on the team to turn up on their weekend off to pick something heavy up and it is amazing how busy everyone is. However it transpired that offering free beer to turn up, ensured we were not short of folk on the day. In any case everyone who had been in the workshop to date was rather excited about how easy she would be to come off the build table, in case we had stuck her to it with epoxy by mistake. We wondered about how heavy she would be in this stage of the build and how stable the structure would be for picking up and turning over in only this partially completed state. Other than that we all wanted to see her outside on the driveway where her size and shape could be fully appreciated.
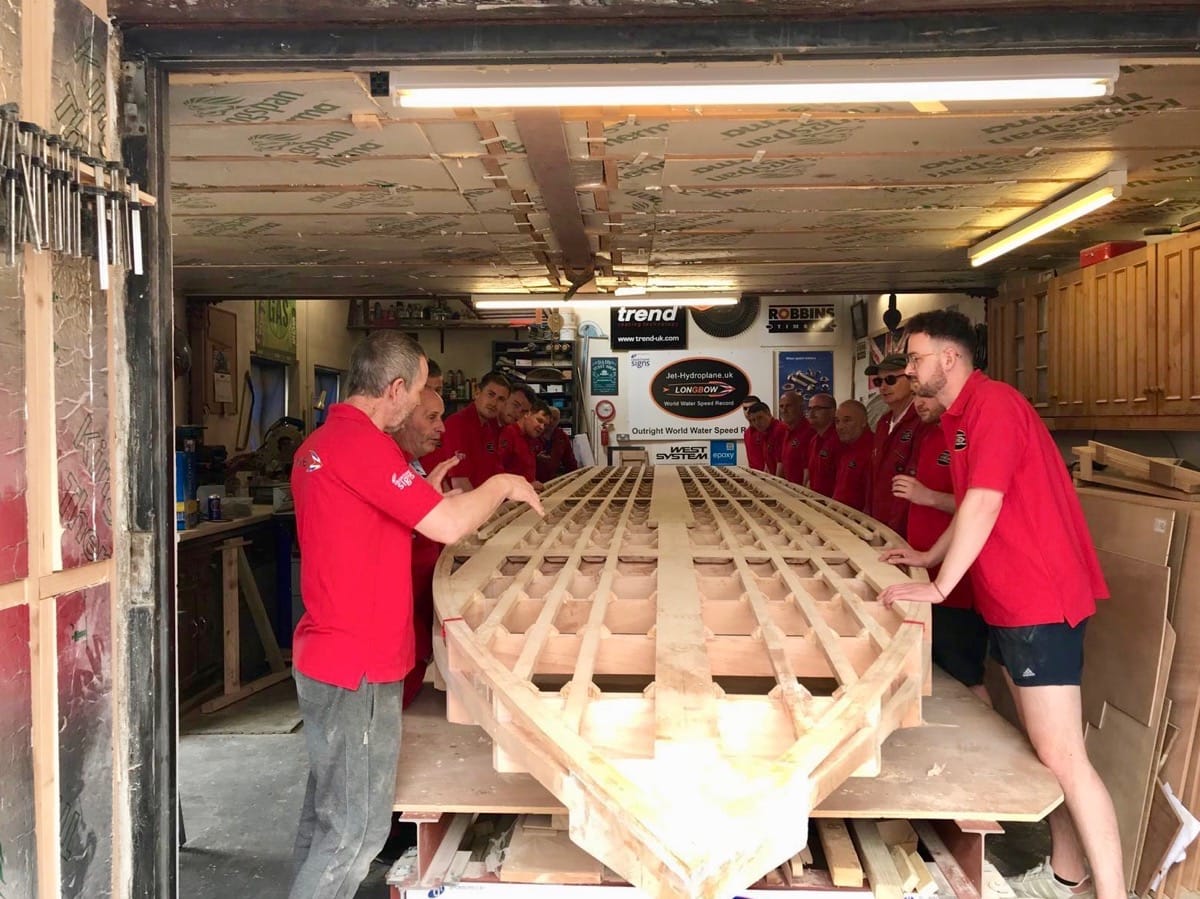
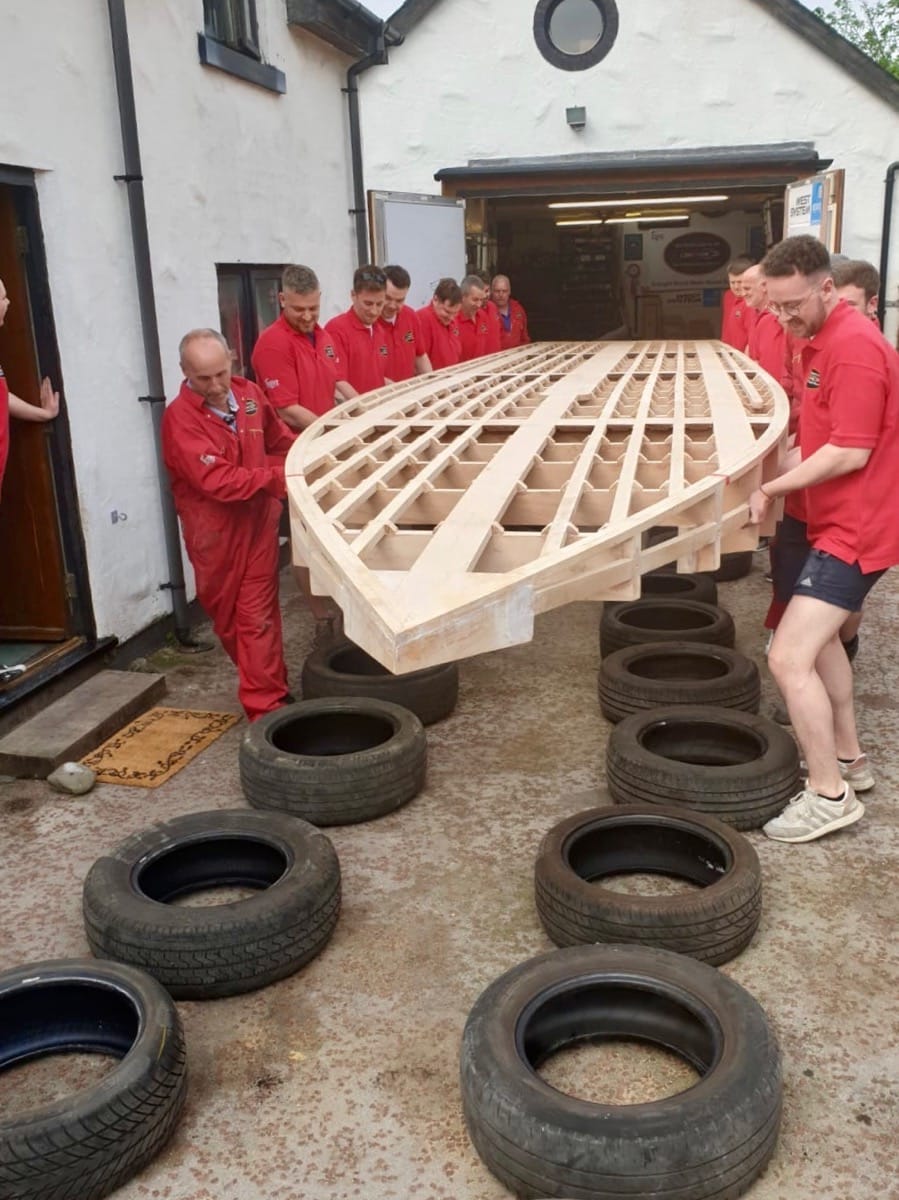
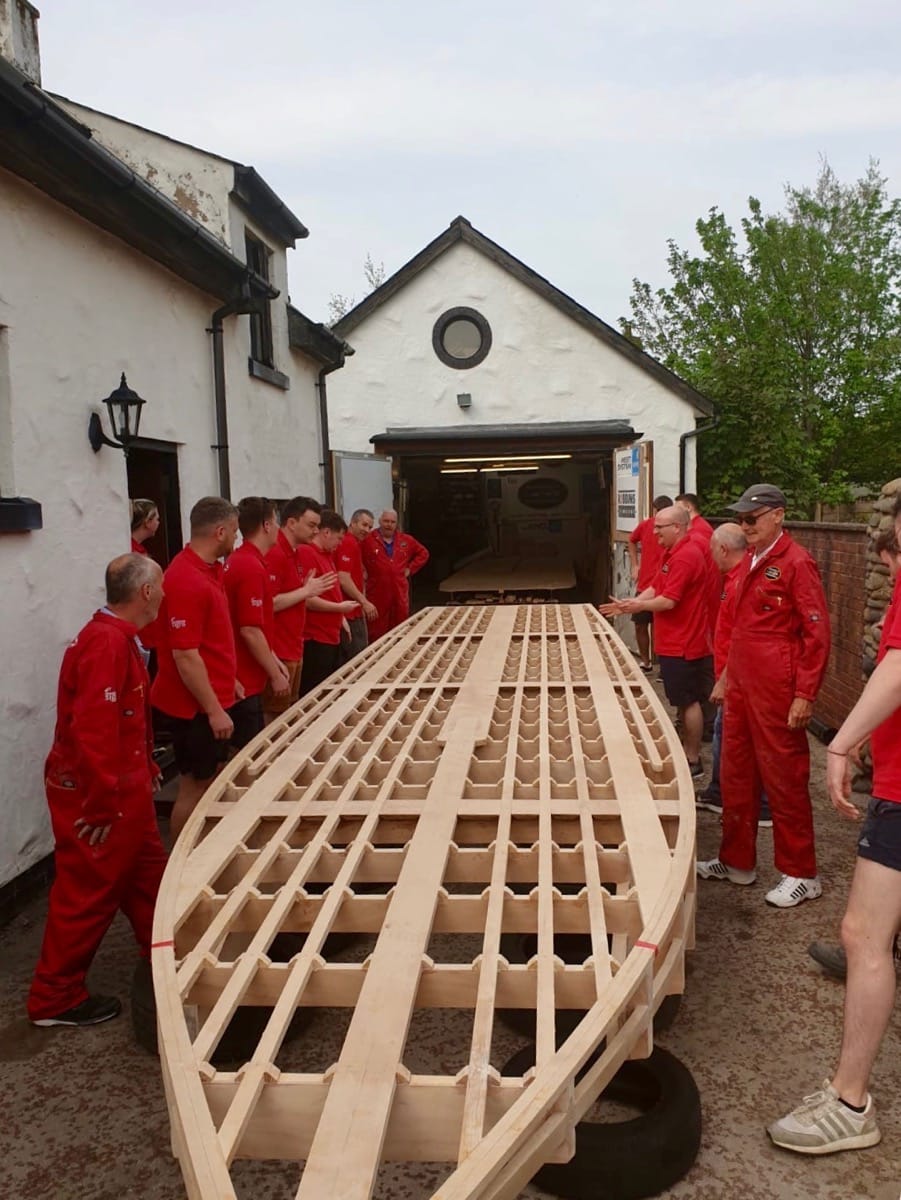
As it transpired it all went surprisingly well compared to previous events where beer had been involved. She felt a lot lighter than we had envisaged as Longbow came up off the build table and we walked her out into the driveway without anyone falling over or putting their back out, to be gently rested on a number of tyres that provided a cushioned stable temporary surface that would not damage the timber framing. These tyres were kindly loaned to us by Adam Wilson at Wyre Tyres and proved ideal for the job. It was only when we had the hull of Longbow lifted on to her side that somebody remembered it might be a good idea for the website, to video the occasion but hope you enjoy the following short clip of us finishing turning her over and walking her back in and safely placing her once more upon the build table:
https://youtu.be/twigAPvybS0
I guess that is about enough news for this month folks. We hope you enjoyed this month’s update of our venture, along with that of our good friend Dave Warby. As you can see these pure thrust jet hydroplanes are like nothing else and the professional, methodical approach of the way Dave is working his boat up to speed with safety paramount, is an inspiration of how to do it right and in turn for us to follow.
If you want to keep in touch as the progress continues, then please like / follow our Facebook page, or follow us on Twitter but in any case the diary updates are usually issued towards the end of each month. Projects of this nature to become the fastest boat in the world, do not come along very often but when you can see them actually happening, with a ‘can do approach’ from a small home workshop, that folk can actually relate to, in order for the job to get done, then they present an excellent marketing platform.
If you are interested in working with us and our local college, as an inspirational project in education, or want to become involved with support, for this British attempt upon the Outright World Water Speed Record, then please contact us.
Take care and see you in June, from all at the Longbow Project.