Thank you for tuning in to this month’s update as summer looks like it has finally arrived here in the UK, or should I say at least it hasn’t rained in the last few days and the heating has stopped coming on.
So what have we been up to over the last few weeks? Well as we continue with the building of the hull for our jet hydroplane Longbow, of which more of that later in the update, we also turned our attention a little to her jet engines. Just because you have managed to source and purchase the engines, it doesn’t mean you can just stick them in the boat and away you go. In order to get them to work at all, you need a whole bunch of other stuff and much of that is not unfortunately what you can just pop down to Halfords for.
The Viper turbojet engines we are using in Longbow are no longer made by Rolls Royce, which means there is a limited number of support parts around to get those engines to work just how we want them to for our specific application. To complicate things even more there were a few different models of Viper engine made for different applications. Our particular model of Viper, the 535 version, is used within the Strikemaster aircraft where the front of the engine sits against a bulkhead, so for that it didn’t need a pointy cone, or bullet shaped bit of aluminium in the middle to smooth the airflow out as it is sucked into the engine. In our application there won’t be such a bulkhead directly in front of the engines so in order to get the best performance out of the engine that we can, we needed bullet noses for the engines that are used for other models of the Viper as shown in the photo below looking more like a Viking helmet.
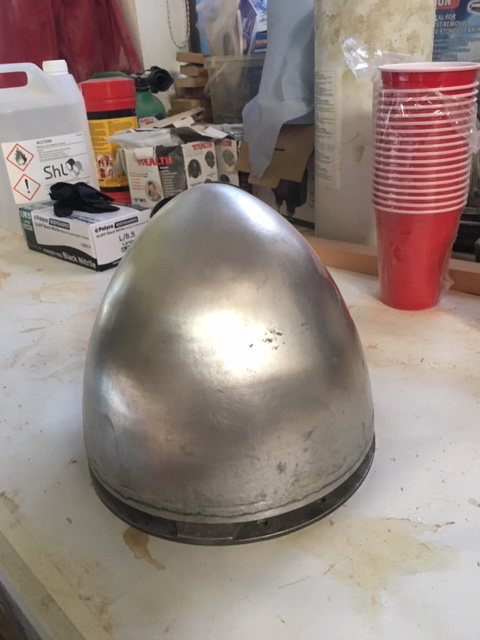
James Everett of Everett Aero in the UK managed to source us one such bullet nose but we were struggling to find another, especially as those that do have them tend to hold on to them. Karl Olleranshaw at Dukinfield Metal Spinning in Manchester asked to have a look at the one we had and determined it was spun in multiple sections that we would need patterns making for. Additionally it is reinforced internally and then welded to an intricate aluminium base that we would require a five axis CNC machine to reproduce. The photo below shows Karl measuring the thickness of the nose cone metal as Fred watches on:
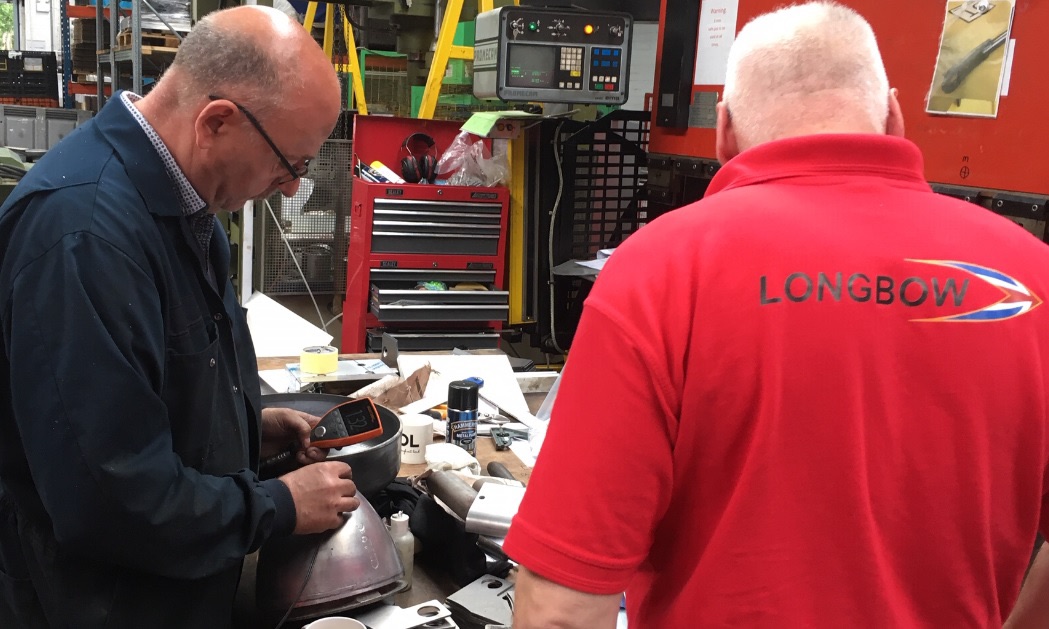
Blackpool & Fylde College who are assisting us have such a 5 axis CNC machine but just as we were pondering about doing the design work, Olie Eriksen in the USA contacted us and said he had a nose cone on the front of his Viper engine that he would be prepared to sell us, which solved that little puzzle, notwithstanding the eye watering amount of import duty one has to pay for such a relatively small item.
We have started to buy the aircraft gauges we will need that will tell us what the engines are doing when they are being run, such as how fast it is turning (RPM) and how hot the temperature of the exhaust gases are (EGT). We may at some point consider going to digital gauges, not least because they would be considerably lighter and consequentially present less of a danger to the pilot if they detached in a cockpit should the worst happen in a crash situation. An aircraft gauge weighs around the same as a small rock and with two of everything for the twin engines that is quite a collection of rubble to go for a high speed tumble with in a confined space. However at the moment the main aim is to get the engines up and working so keeping things simple, the traditional aircraft gauges that are meant for the Viper engines will certainly do for now.
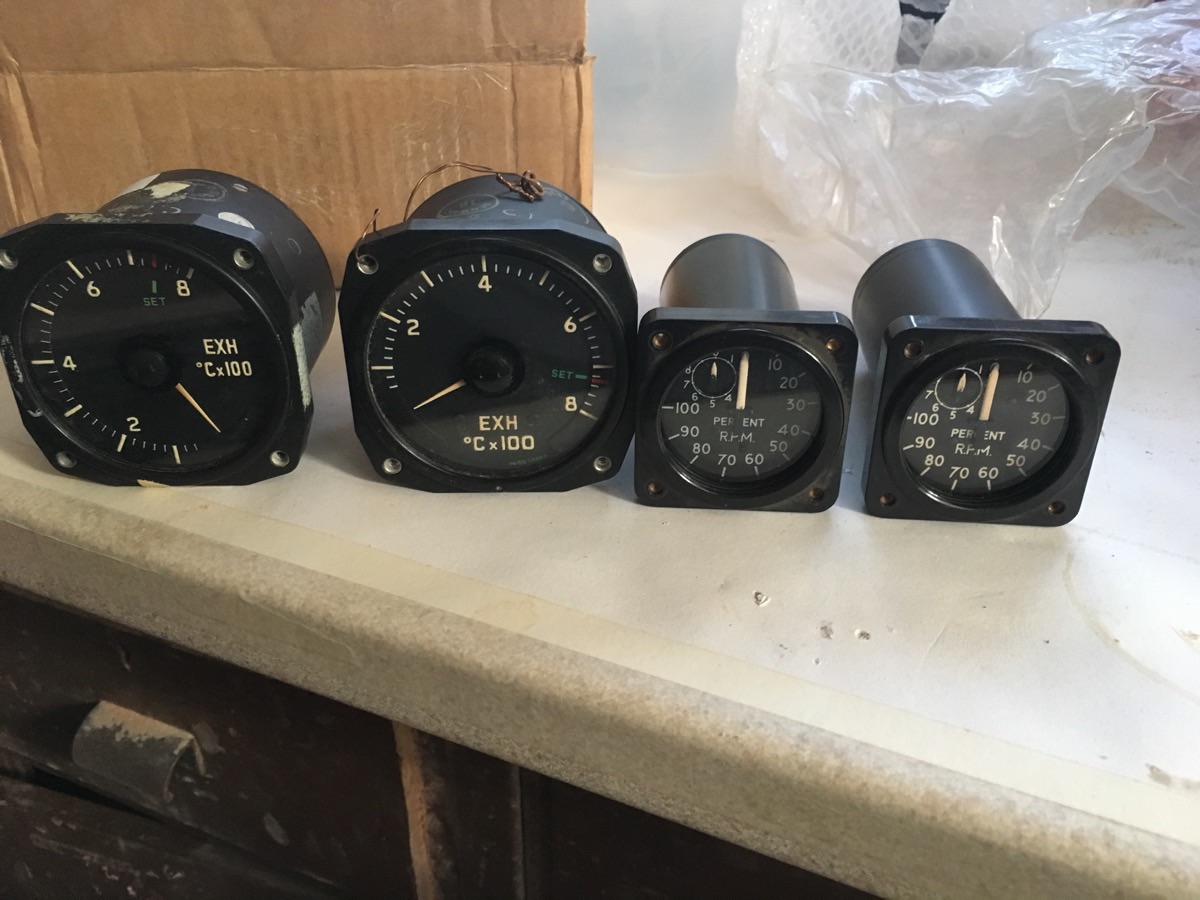
There is no point having the EGT gauge without the set of four thermocouples to drive them, specific for the jet pipes of that particular engine in order for the gauge to get a reading from. Again running twin engines that meant eight thermocouples are required with the gauge calibrated to see the correct number of thermocouples down each jet pipe. Were eight such thermocouples specific to that aircraft easy to find? No of course not, it is like an international treasure hunt but eventually we did manage to track some new old stock (NOS) down and buy them too.
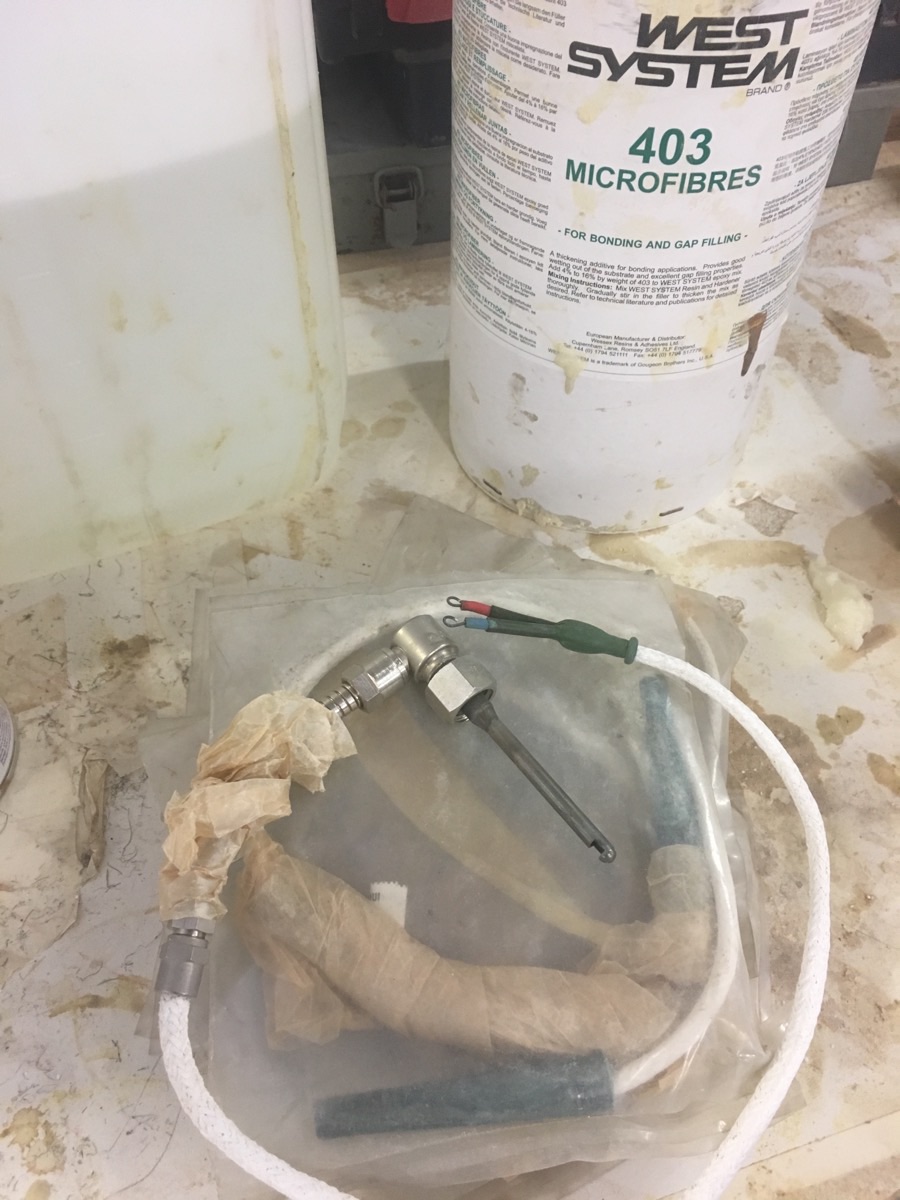
Next on the shopping list was the mechanism for lighting the jet fuel. The Viper like many gas turbines has two igniter plugs, one directly opposite the other on each side of the engine that act like your spark plugs in a petrol car to ignite the fuel. Only in this case once you have lit the fire in the jet engine you can turn the spark off because like a gas cooker it should then stay lit until you turn the fuel off / run out of fuel.
In the case of the jet engine it is a very hefty spark that is required and it fills the area around the spark plug tip with a burst of hot plasma (ionised air) that when it fires makes a loud bang as shown in this short video of the spark occurring at the igniter plug which is in slow motion courtesy of Tony Rycroft of Heinzmann, one of Longbow’s sponsors:
https://youtu.be/XtwpU7rq_cQ
In order to provide that spark it requires a lot more electricity than your car spark plugs, in fact a highly lethal dose that you don’t want to get in the way of ramped up to kilovolts from a humble 24vDC supply and care with a healthy respect for safety is definitely needed when handling the igniter unit (Heinzman unit shown) supplying the spark.
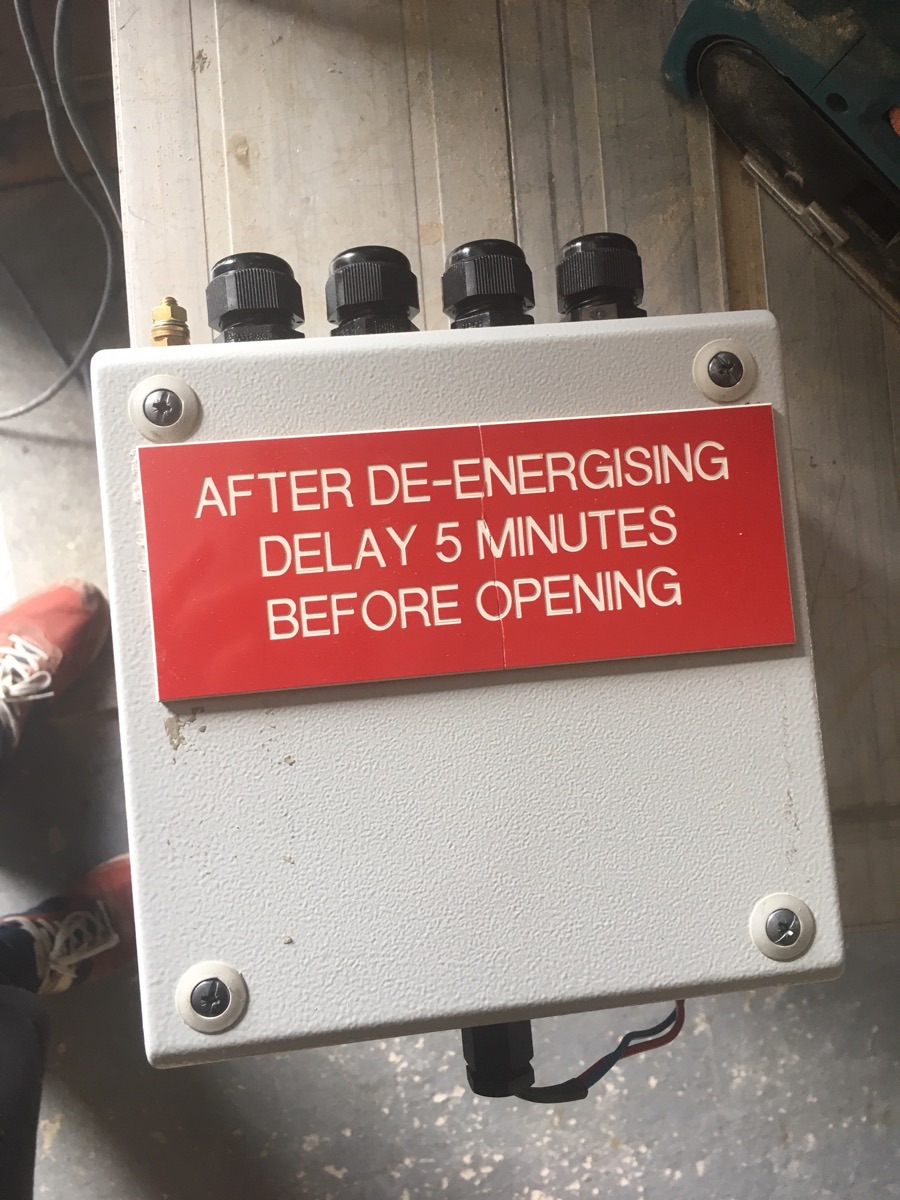
We are currently working on provision of the igniter leads and will report back on this within future diary updates.
Sealey (Jack Sealey Ltd) one of the UK’s leading suppliers of workshop tools and equipment continues to do us proud as another of our sponsors and their marketing Director Steve Buckle kindly supplied us this month with one of their 50mm diameter mini disc air orbital sanders. This is perfect for getting into all the awkward spots on the hull. They also have kindly supplied this month a geared beam trolley which we will need for support of a lifting rig we are having made for the jet engines to take them from their stands and into the hull of Longbow for a trial fit.
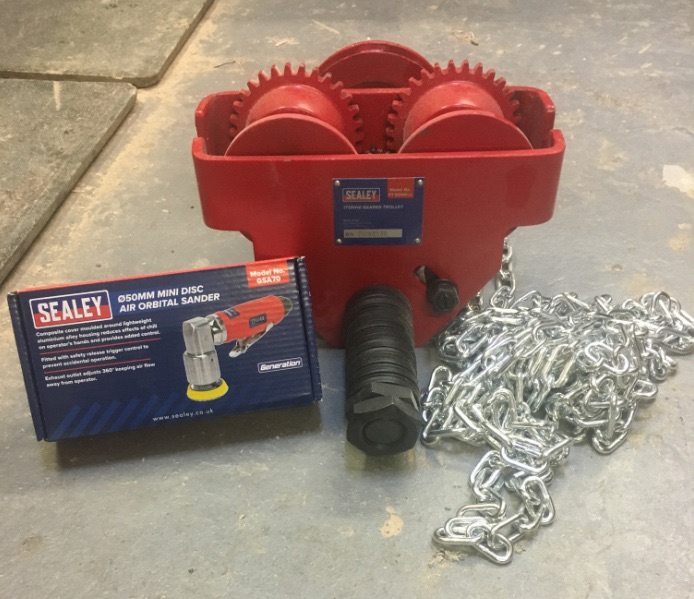
As regards continuing the build of the hull for Longbow you will recall that last month we had just turned her over for the first time, in order to form the curving top outer rails. However before we could go on to form those rails there was a considerable amount of profiling and sanding to do, cleaning up epoxy that had weeped slightly from joints as they were formed but which had been difficult to access when the hull was inverted.
‘It’s all in the preparation’ I can hear my elders and betters say and whilst absolutely true, sanding down is very time consuming with little to show for it, other than being covered in dust and no doubt we will have to do this many more times as the build progresses. Sanding is just one of those tasks that you just have to put your appropriate protection equipment on, don’t rush and methodically get on with.
In the end we got where we needed to be and then could cut out for, bend, shape and add the outer upper frames. These being secured in place with West System Epoxy from our sponsor Wessex Resins and screws from another of our sponsors Avon Stainless Fasteners.
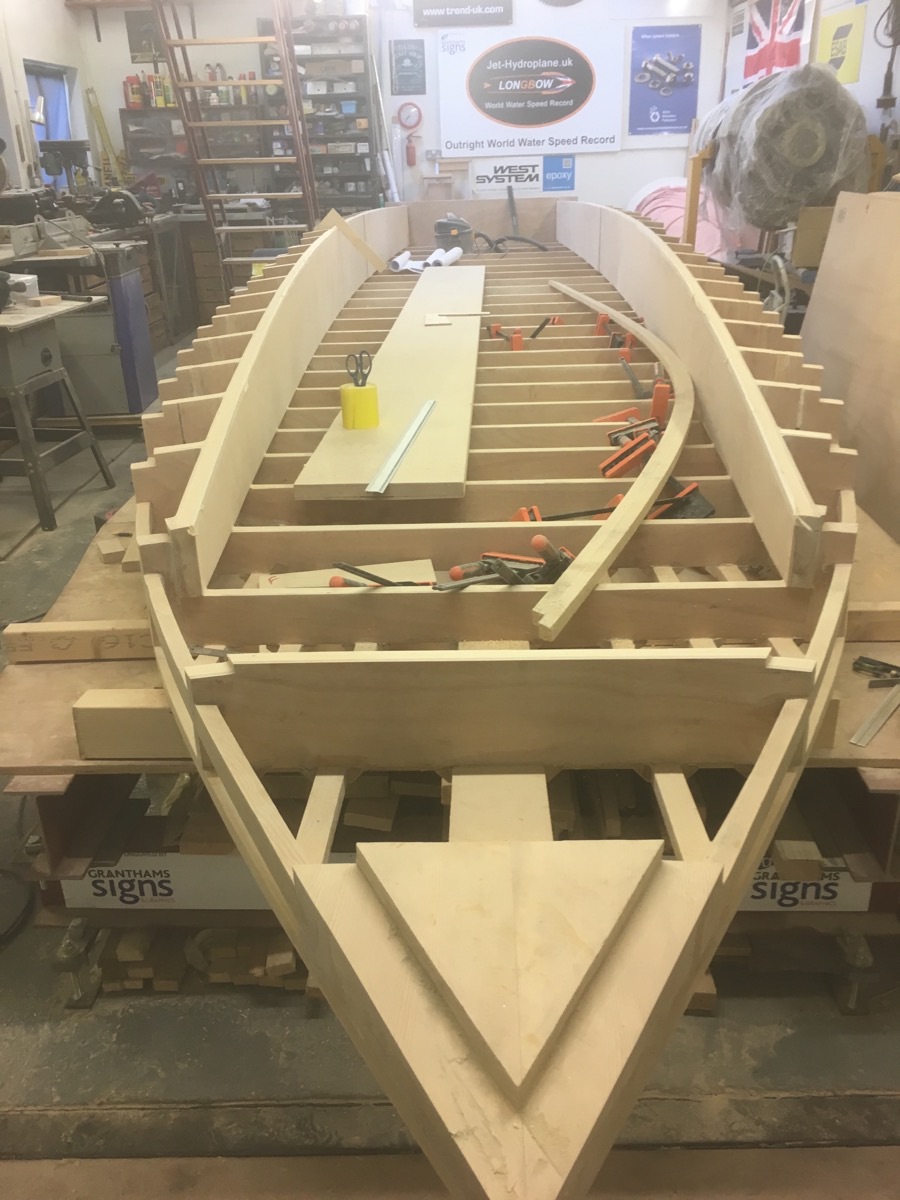
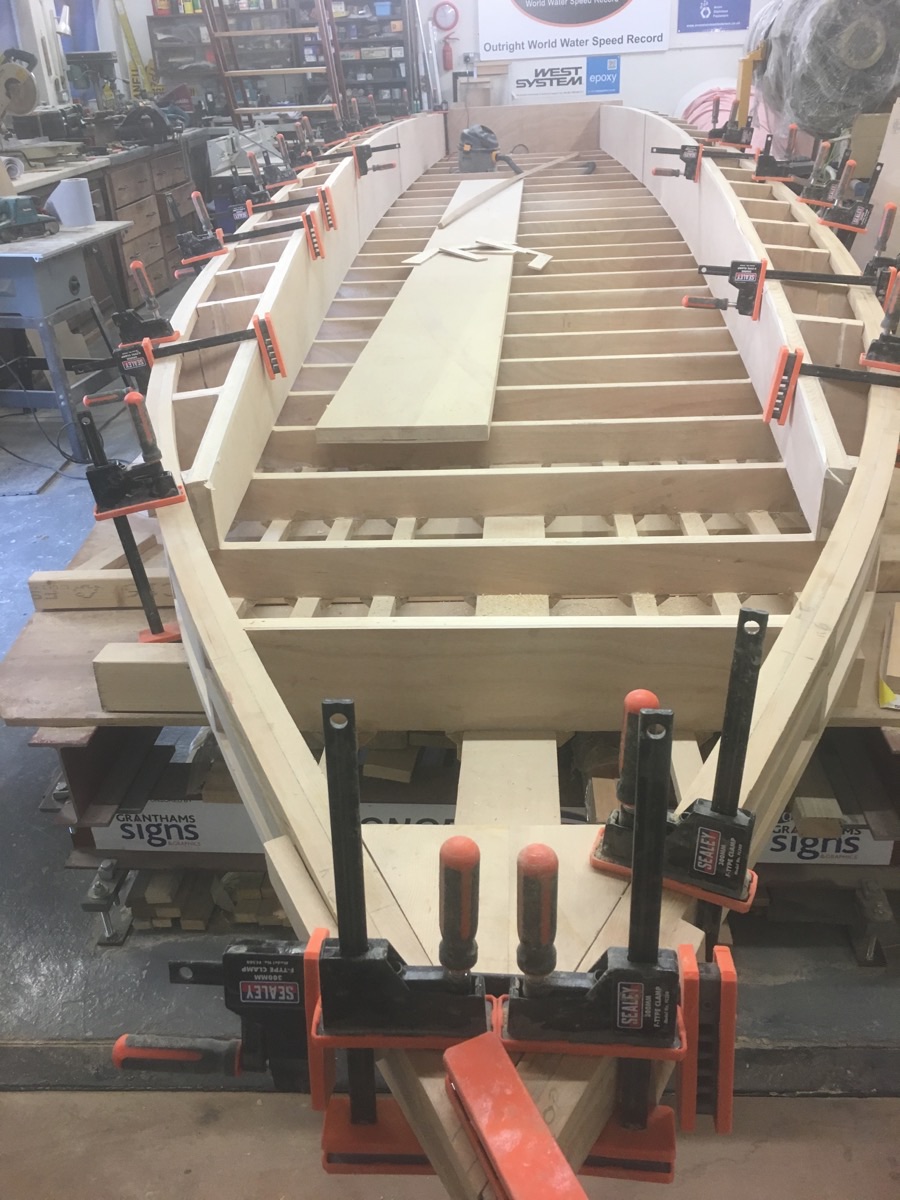
Dr. Margarita Georgiva, Programme Leader for Engineering and Mark Stephens Program Leader for Aero Engineering from our education partners at Blackpool & Fylde College (B&FC), have compiled a list of tasks that their students have kindly offered to assist us with, as well as using the venture for their studies and dissertations. Head of Machining lecturer Robert Lewis for example is arranging for his students to machine some compressor casing blanks for the jet engines.
Following a talk that we were asked to give at B&FC to the lecturers of various departments, a group of students and staff from the college made a visit to our humble little workshop, in order to see Longbow under construction and her jet engines.
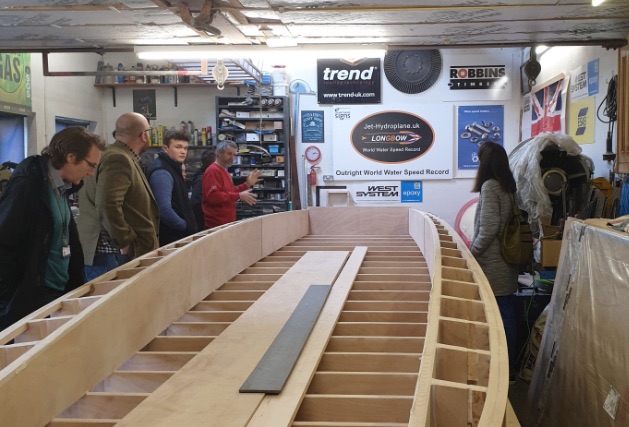
A nice coincidence and just to show what a small world we live in, was the discovery by chance that Tracey Eastham Senior Tutor of the Creative Arts Faculty at the College, who’s students are assisting us is, like ourselves, good friends with Gina Campbell QSO, who held the Women’s Outright World Water Speed Record and daughter of Donald Campbell CBE.
We have also adopted Steve Dawber who is doing a BE (Hons) in Mechatronics Engineering at Blackpool & Fylde College whilst working as a design engineer up at Morecambe. Steve is apparently a whiz at 3D CAD drawings which should be a great help for various components on Longbow as an interface between ourselves, Kevin Hardcastle design engineer at Aximo and freelance design engineer Paul Martin. Steve who’s mug shot is captured below for the benefit of his wife who was suspicious of him disappearing on certain evenings to help us out, doesn’t drink tea or coffee when he comes to help but that won’t excuse him from buying the biscuits.
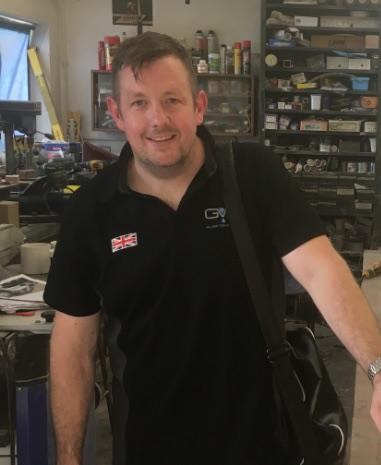
In all seriousness it is great to see the students from different faculties wanting to become involved with building and the running of Longbow. To be inspired by the venture, as it snowballs into so much more than a few friends daring to have a go at building a jet hydroplane from nothing more than a cottage workshop. Though maybe that is part of the appeal becoming part of something you don’t see everyday but which, like so much in life, anybody can do if they set their mind to it.
Casting our eyes ahead we have also been mindful of being asked whether we would wish to run Longbow when she is complete, at Coniston Water in the Lake District National Park, in addition to other venues such as Ireland and the lochs of Scotland. Although the wooden hull of Longbow is obviously not effected by corrosion, in the same way an all metal hull would be, her jet engines and any metalwork that forms part of the craft certainly would corrode and her jet engine performance severely compromised if subjected to salt water ingress, or say water high in other mineral content. Accordingly inland freshwater venues are only where we will allow Longbow to be run.
The Lake District, is relatively local to us, having once been part of Lancashire where Longbow is being built and as many following our venture are aware, is historically the venue of previous World Water Speed Records attempts in the UK. As such it provides our closest reasonable length of inland freshwater, where if permission were hopefully granted and with a little good fortune we could develop the craft for a British attempt upon the Outright World Water Speed Record.
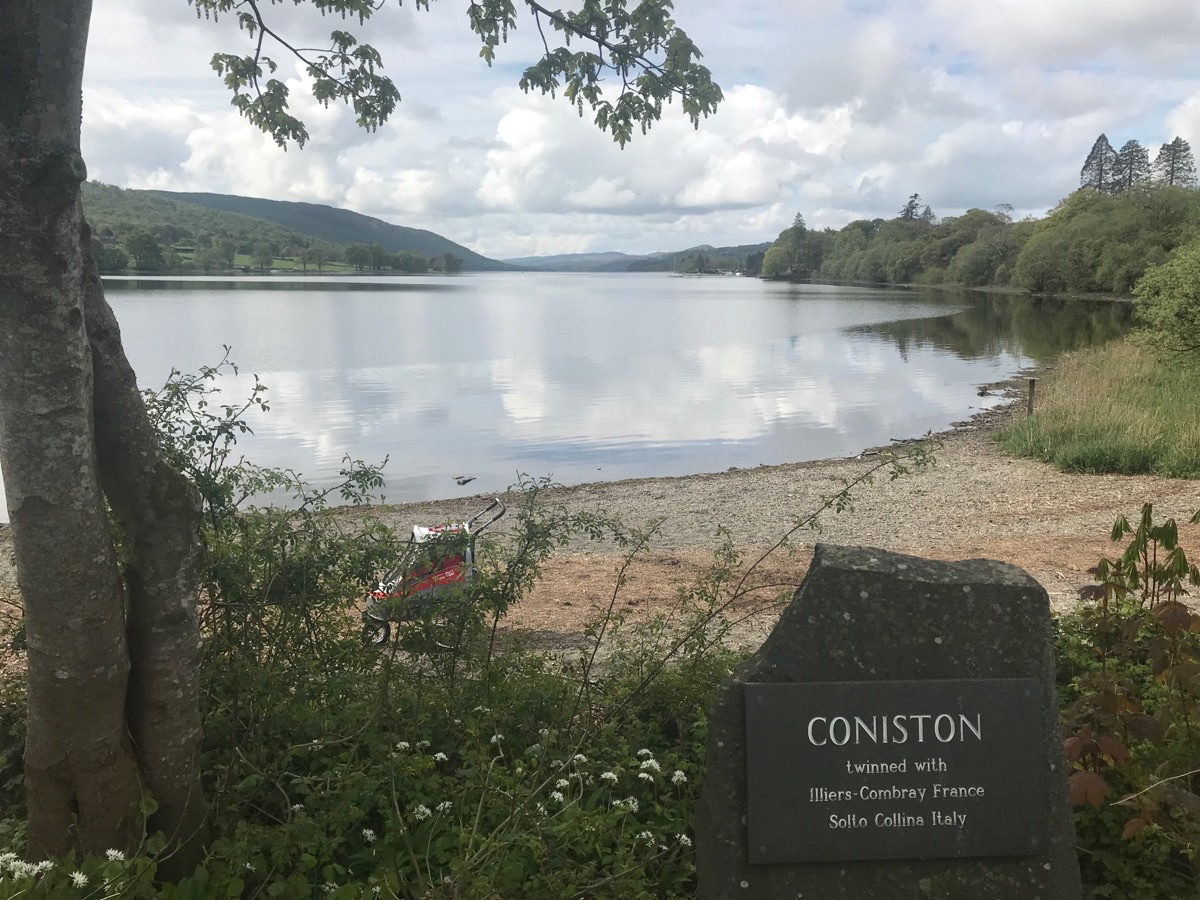
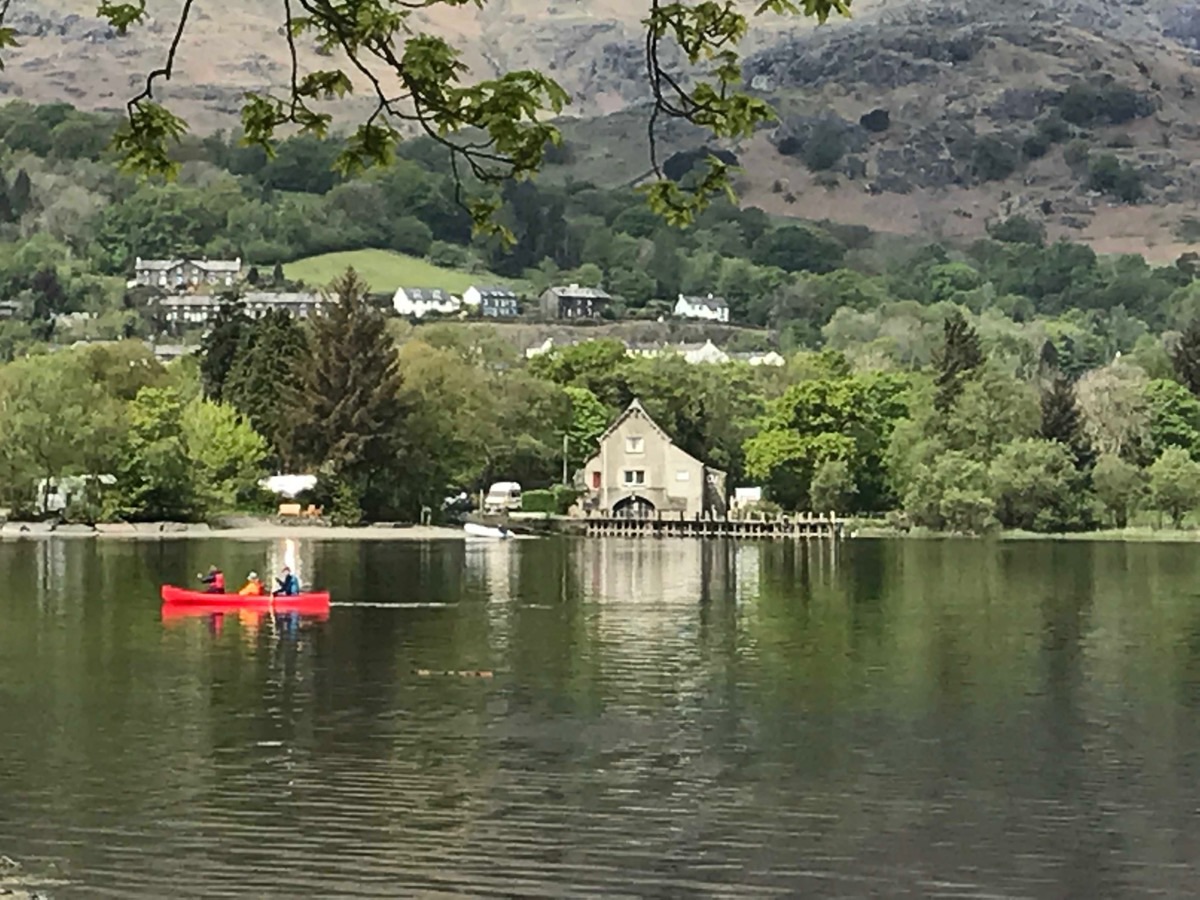
This being the case we have recently been in communication with the Lake District National Park Authority (LDNPA) and some of the people of Coniston, in order to begin courteously working with them, on satisfying their requirements of us as their respectful future guest. That is to say how we may be able to run Longbow safely in consideration of the many other users of this most beautiful location, in addition to ensuring our responsibilities in relation to environmental protection are fully met. We must therefore take this opportunity to thank all the LDNPA staff, especially solicitor Julie Wood, Steve Tatlock and Stephen Ratcliffe for being so very kind and helpful as we begin to feel our way through this process and to ensure we consult and have the agreement of all concerned, well in advance of Longbow being completed.
If you are interested in working with us and our local college, as an inspirational project in education, or want to become involved with support, for this British attempt upon the Outright World Water Speed Record, then please contact us.
That is all for now folks, thanks for taking the time out of your busy lives to read this month’s little update, take care and see you at the end of July for the next instalment, from all here at the Longbow Project.