Welcome to this month’s update as the clocks roll back here in the UK, bringing with it the shorter daylight, colder seasons, spooky Halloween and the heaters along with dehumidifier are switched back on in our little cottage workshop.
So other than meeting up for a brew and eating too many biscuits, what has been happening this month in the Longbow camp?
Well first off the blocks was Stephen Woods who has an aircraft breakage business down in Devon kindly supplied us with some aircraft toggle switches and a multi lever throttle box that some of you may recognise as being from the retired military twin engine Westland Lynx helicopter. This unit will not be going into our jet hydroplane Longbow that is being powered by twin Viper pure thrust gas turbines but will instead be used for the static rig engine tests we want to perform prior to the engines being installed into the hull. The rig will also serve for any later testing of engines we may want to undertake outside of the boat.
This Lynx throttle box was recommended for us to use by our gas turbine engineer friend Rene Redmond over in New Zealand. Rene uses this throttle box for his Viper engine tests and I have to say it is a lovely piece of engineering complete vernier adjustment for the throttle, a series of micro switches and associated lights within the levers.
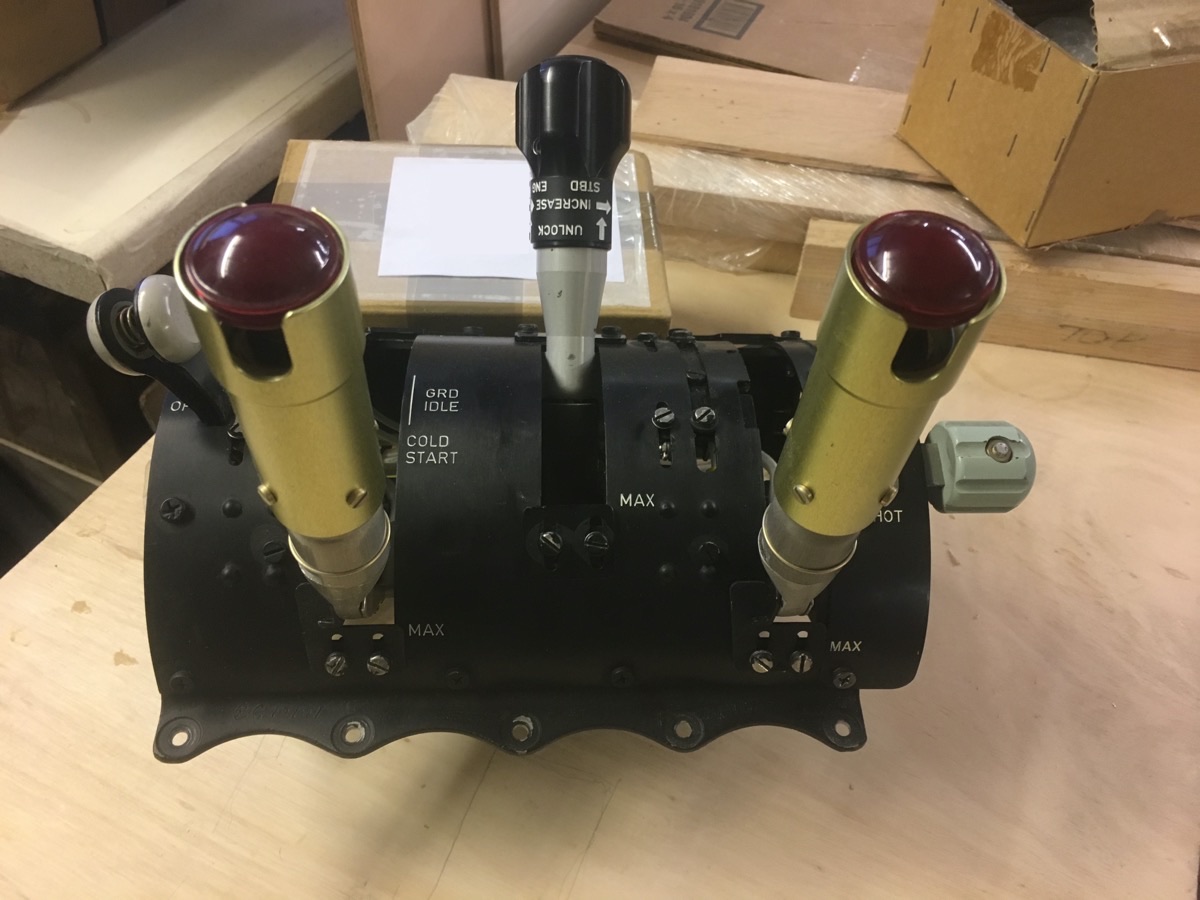
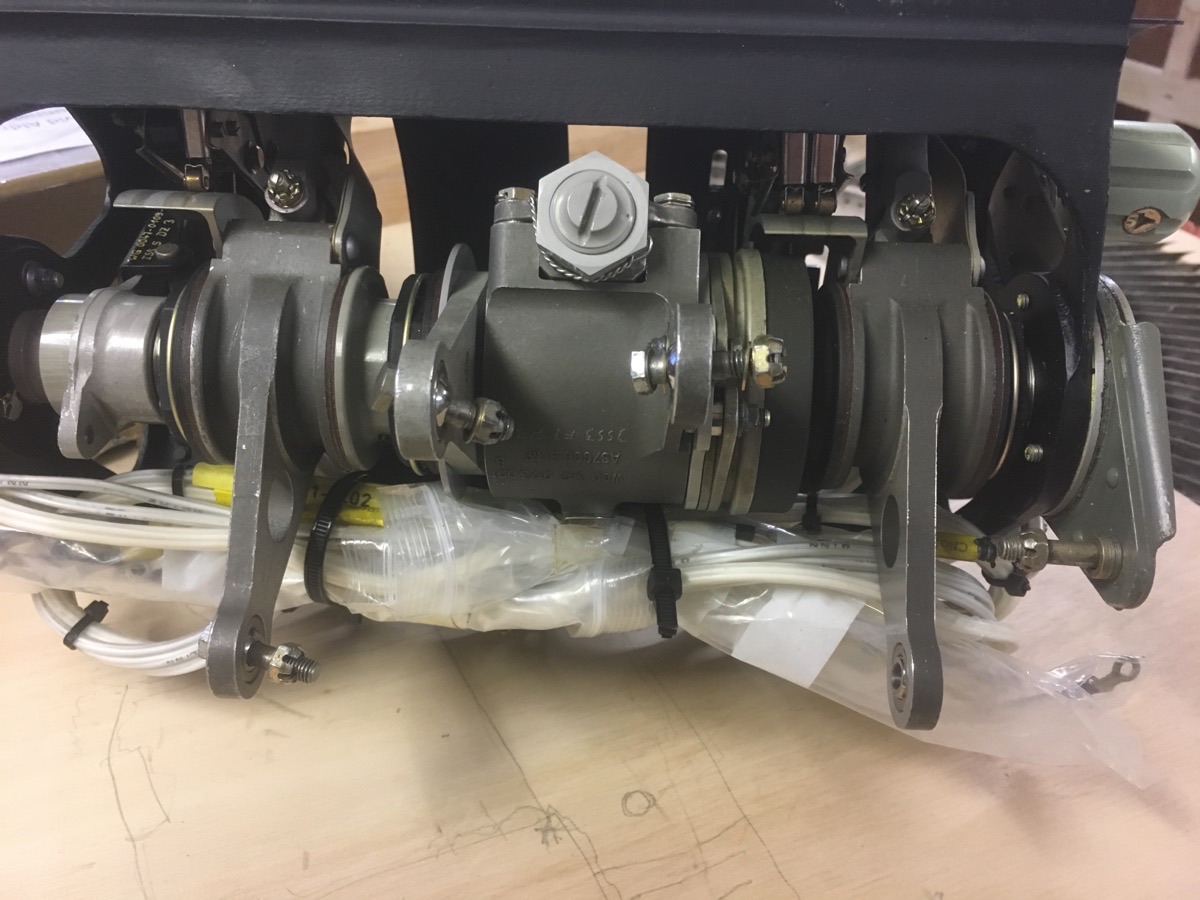
You may remember within previous updates design engineer, Steve (Dawber) coming to us through one of our education partners, Blackpool & The Fylde College. Steve having taken pity on us and decided to help us out has very much become part of the Team and one of the items he has designed for us is a lifting frame for the Viper jet engines. His design has been very kindly fabricated and certified by one of our product sponsors Britlift who have a policy of employing ex British Forces personnel, which fitted very nicely with our patriotic project where the driver of Longbow is to be serving Royal Navy pilot David-John Gibbs. The result was we could not be more pleased with how the engine lift has turned out and very well done to all involved.
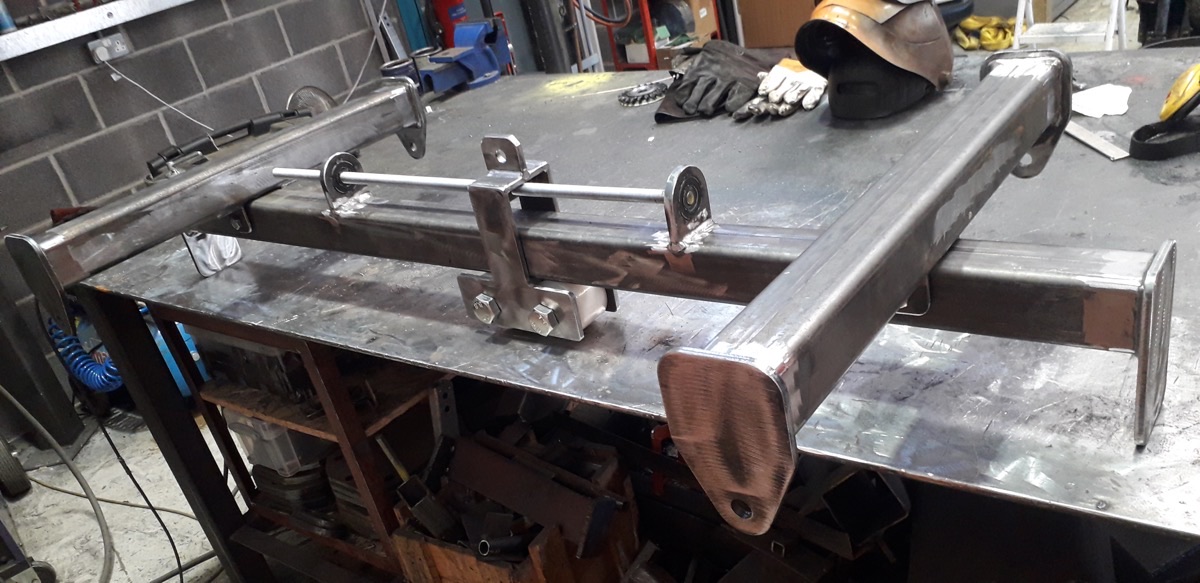
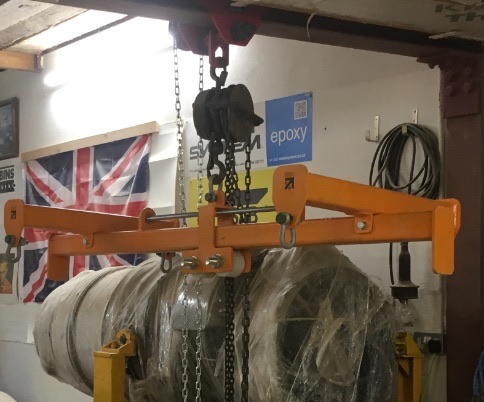
In order to connect this engine lift to the engine itself, appropriate certified rigging was kindly supplied by another of our sponsors Will Dunn of Lifting Equipment Store who jumped at the chance of being involved with our little project.
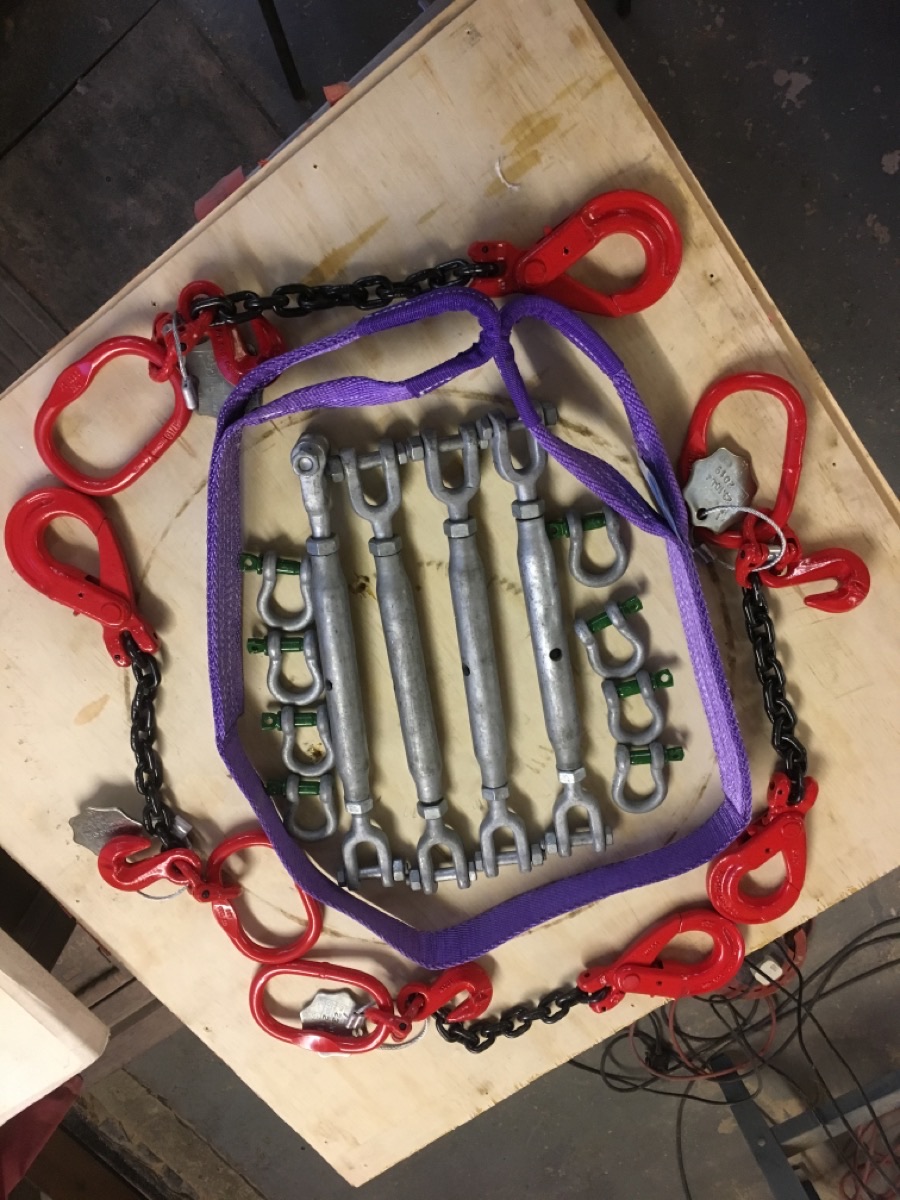
This month we managed to set aside some time to take the tired turbine disk of our good friend Dave Warby up to Hartlepool College. For those who have been following the venture this relates to one of the Orpheus jet engines that are powering Dave’s jet hydroplane Spirit of Australia 2 as he continues with his bid to better his father Ken’s Record of the fastest boat in the world. Dave sent this used turbine disk over to us from Australia in exchange for one in perfect order that was in a display engine at Hartlepool College Aerospace faculty and it was our pleasure to handle the exchange here in the UK on Dave’s behalf.
Lesa, Dave’s partner had kindly sent us over some of their superb SOA2 team shirts for us to proudly wear as a thank you for helping them out. As we were stopping over in the Lake District on the journey up to Hartlepool, my wife Gill & I thought it would be a nice touch to take a couple of photos showing their turbine wheel as a bit of SOA2 and their team shirts at Pier Cottage, where the steam yacht Gondola is berthed at Coniston Water with kind permission of Fay Lakin whose family own the house, pier and attached caravan site. This being the location where Donald Campbell’s Bluebird K7 jet hydroplane had been based for many of his World Water Speed Record attempts so many years ago and Fay’s mother Janet remembers having Donald and his team as their guests back then.
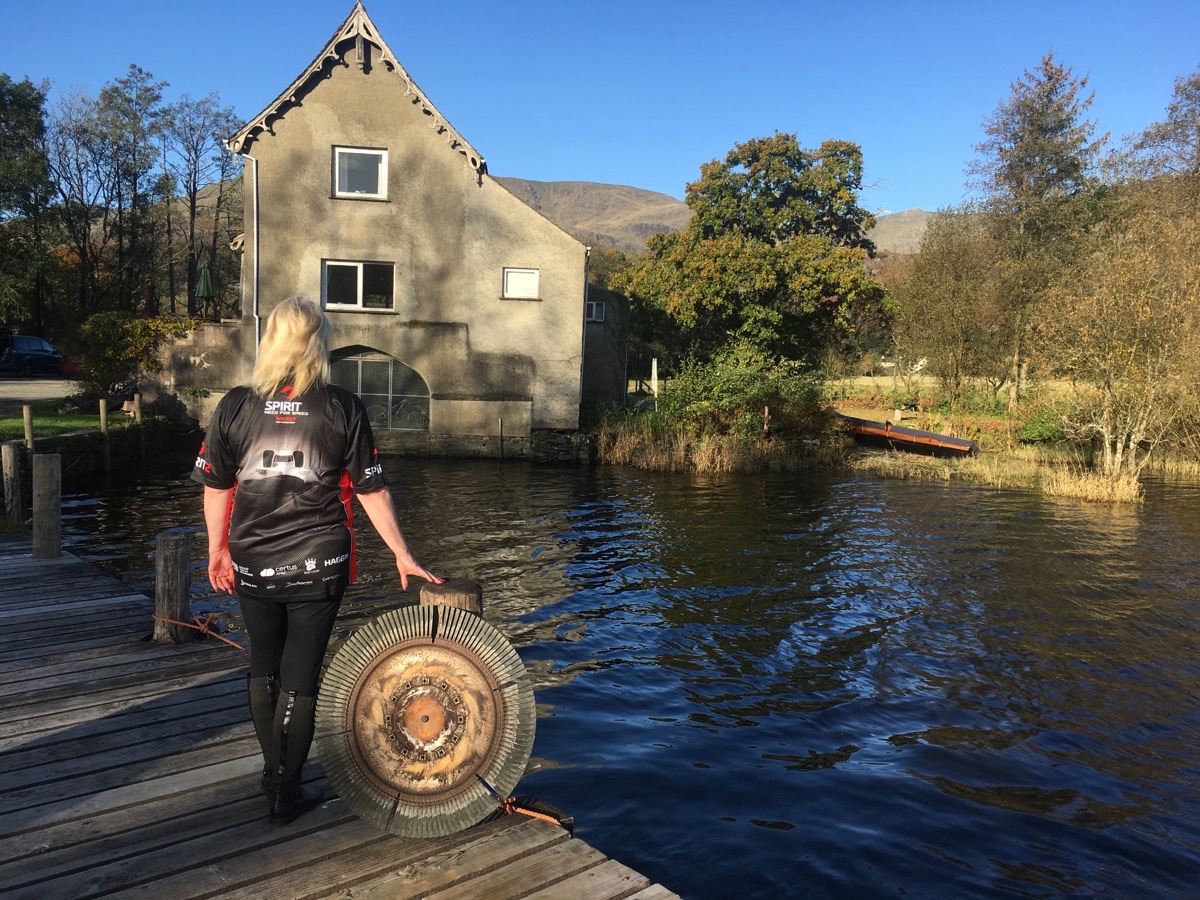
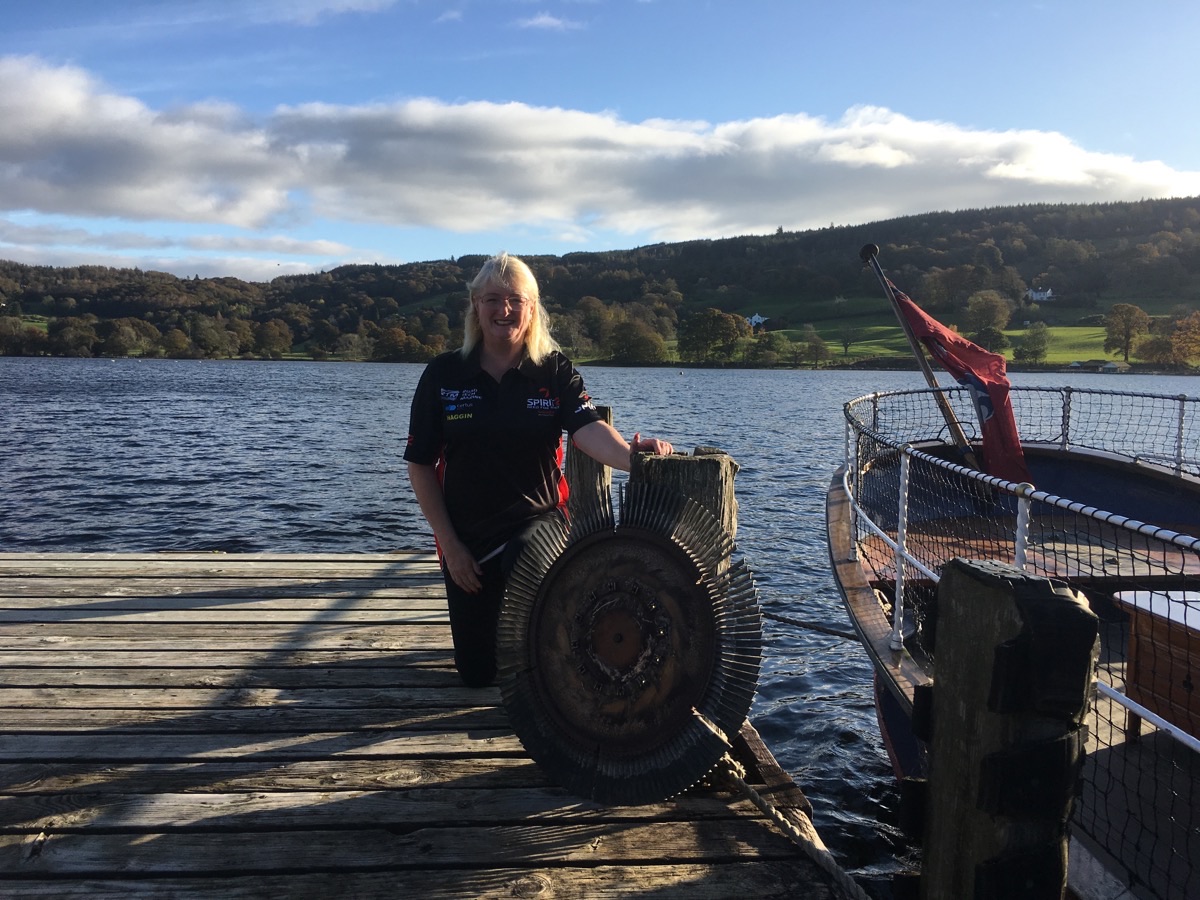
Dave has had further corrective surgery on his hand this month and is under strict instructions from Lesa and the team to let that fully heal before he is allowed back in the boat. This being the case development tests which were planned for this November have been put on a short hold. We will report back on the next round of tests with SOA2 in due course and in the meantime wish him a speedy recovery.
Back with Longbow, Blackpool & Fylde presented us with a lovely sign for our workshop wall in recognition of their educational partnership with the Project.
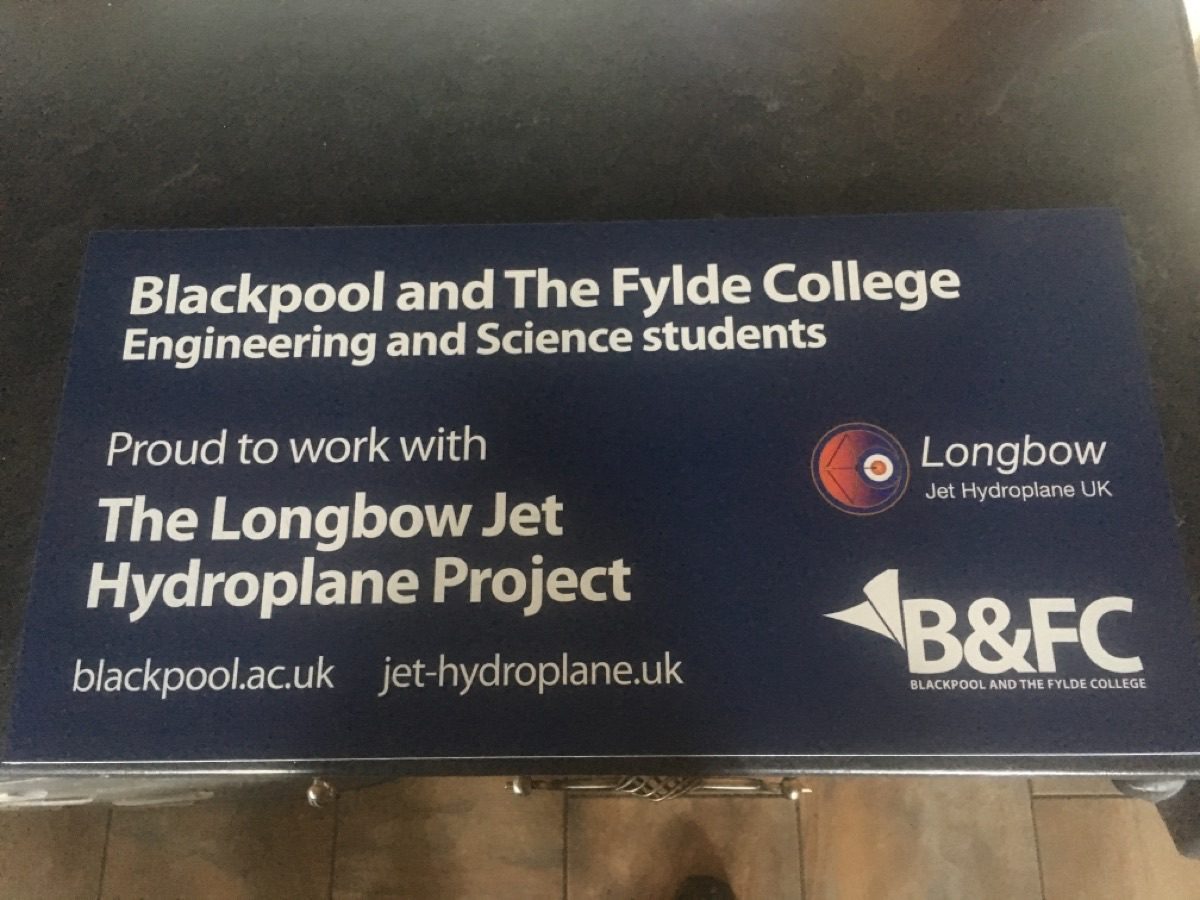
We also had a very productive meeting with Tracey Taylor, Darren Fernandez and later Adam Pridmore of RS Components who are sponsoring the venture, about them doing a series of promotional videos regarding the building, testing and running of Longbow for publication on YouTube that hopefully will commence next year.
I make no apologies for the following praise and thanks to our sponsors mentioned below this month, even though it may sound something of a trade list, because without them and all the other sponsors who have come on board, this little venture of ours simply would not happen and it is only right that we feature them to say thank you during the monthly updates as and when they supply product to help build Longbow.
In the first instance we are extremely grateful to Hamish Cook, along with David Johnson of Wessex Resins & Adhesives Ltd, as this month they very kindly sent us WEST SYSTEM resins and hardeners to keep us in stock of one of the best marine grade epoxies in the world, as we move on to the next phase of construction.
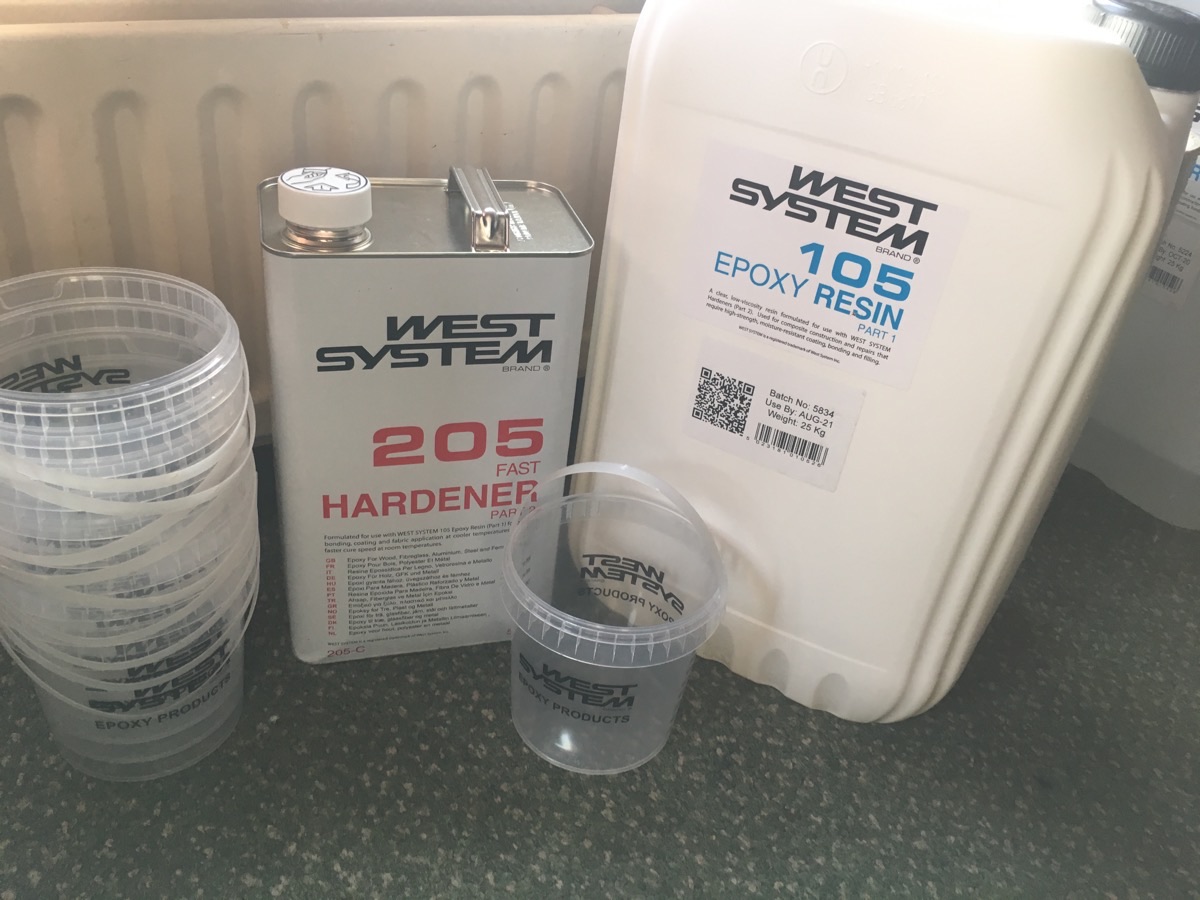
Another major sponsor of the Project, Sealey this month sent us their excellent soldering workstation along with a reel of solder, so that my good friend and electrical engineer John Fielding can get to work on forming the electrical connections for the jet engines
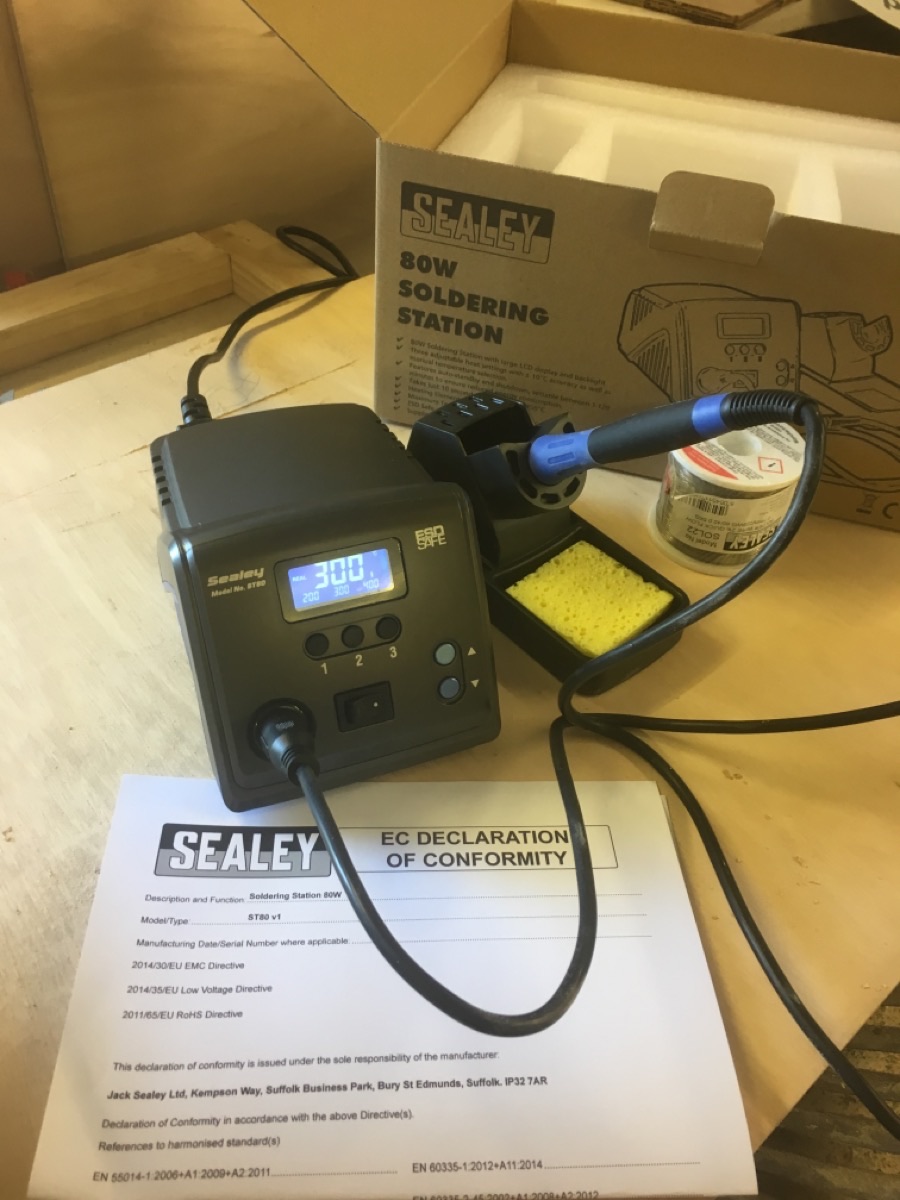
As with so much of forming the hull there is a never ending task of cutting shaping and sanding to be undertaken. As part of ensuring that we keep ourselves well protected from that hazard we are very grateful to Trend Machinery & Cutting Tools Ltd for this month sending us both their excellent Air Stealth half mask and their Airstealth Lite Pro masks for us to use.
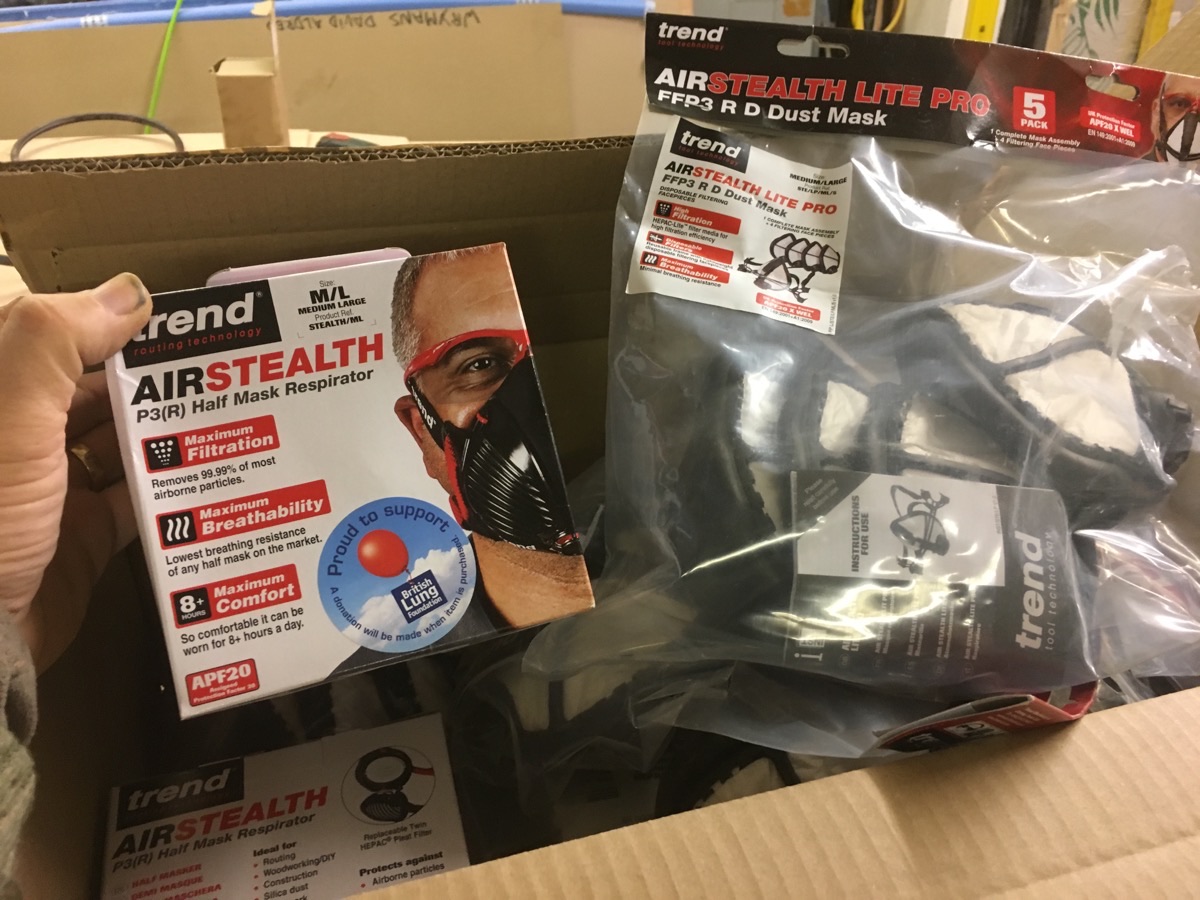
It is no use having the product if we don’t pull our finger out and get on with the build itself. At the end of last month you may recall that Steve (Hanson), Keith (Cowie) and I had all worked together to prepare the panels, timber framework and start to put the sides of the hull onto Longbow using Raptor composite nails and Sealey clamps to hold the panels in place; whilst the WEST SYSTEM epoxy used to attach the panels, cured. This month Steve, Keith and myself managed to continue that task successfully to the point that both sides of Longbow using the marine grade plywood, kindly supplied by our fantastic sponsor Robbins Timber, have been permanently fixed into place over the substructure.
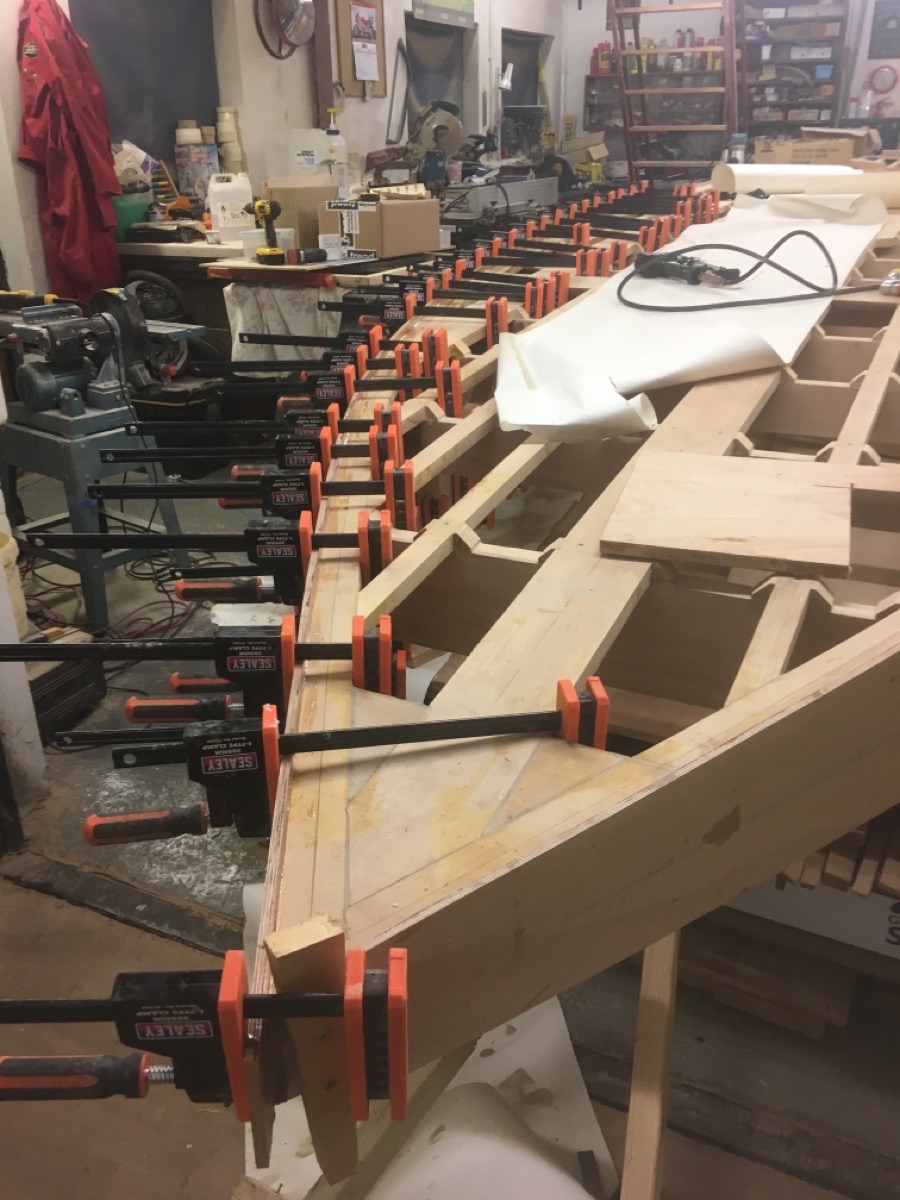
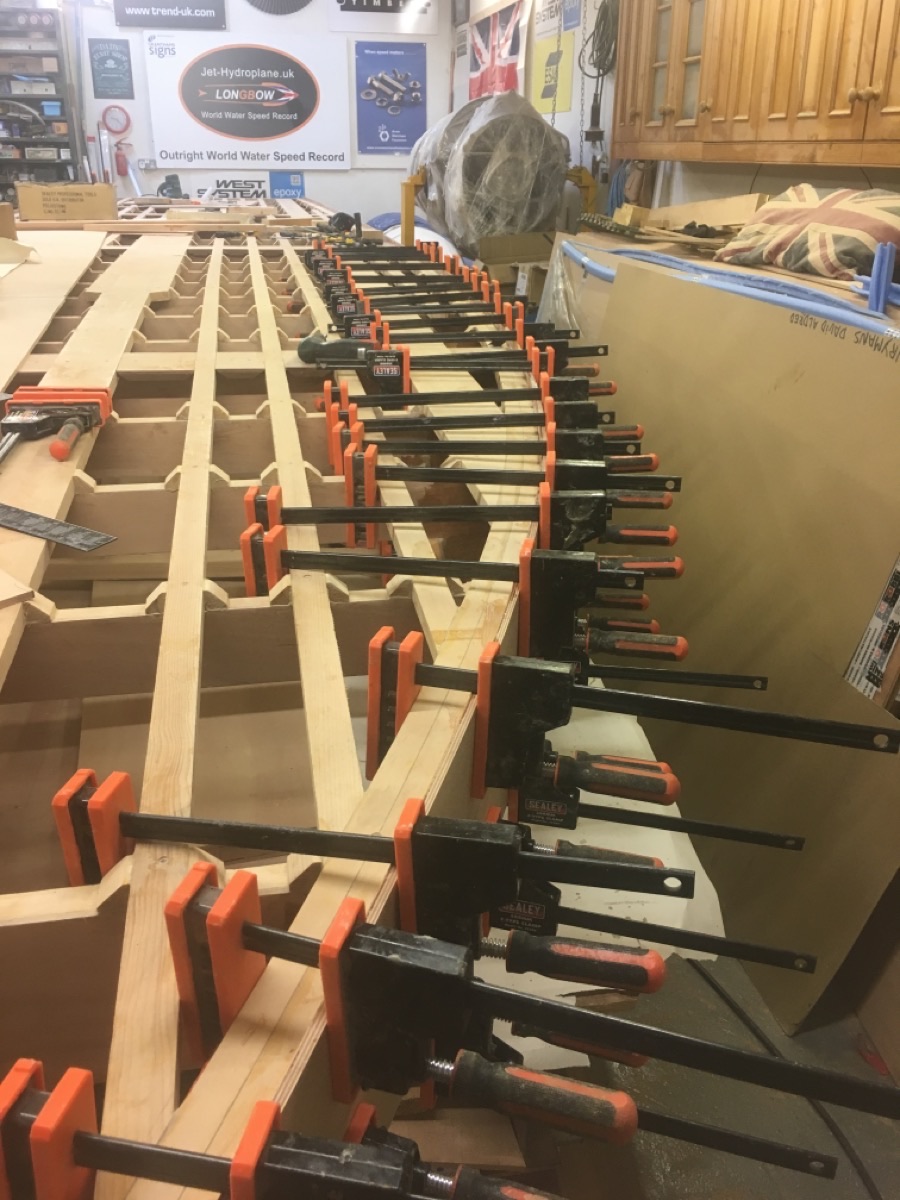
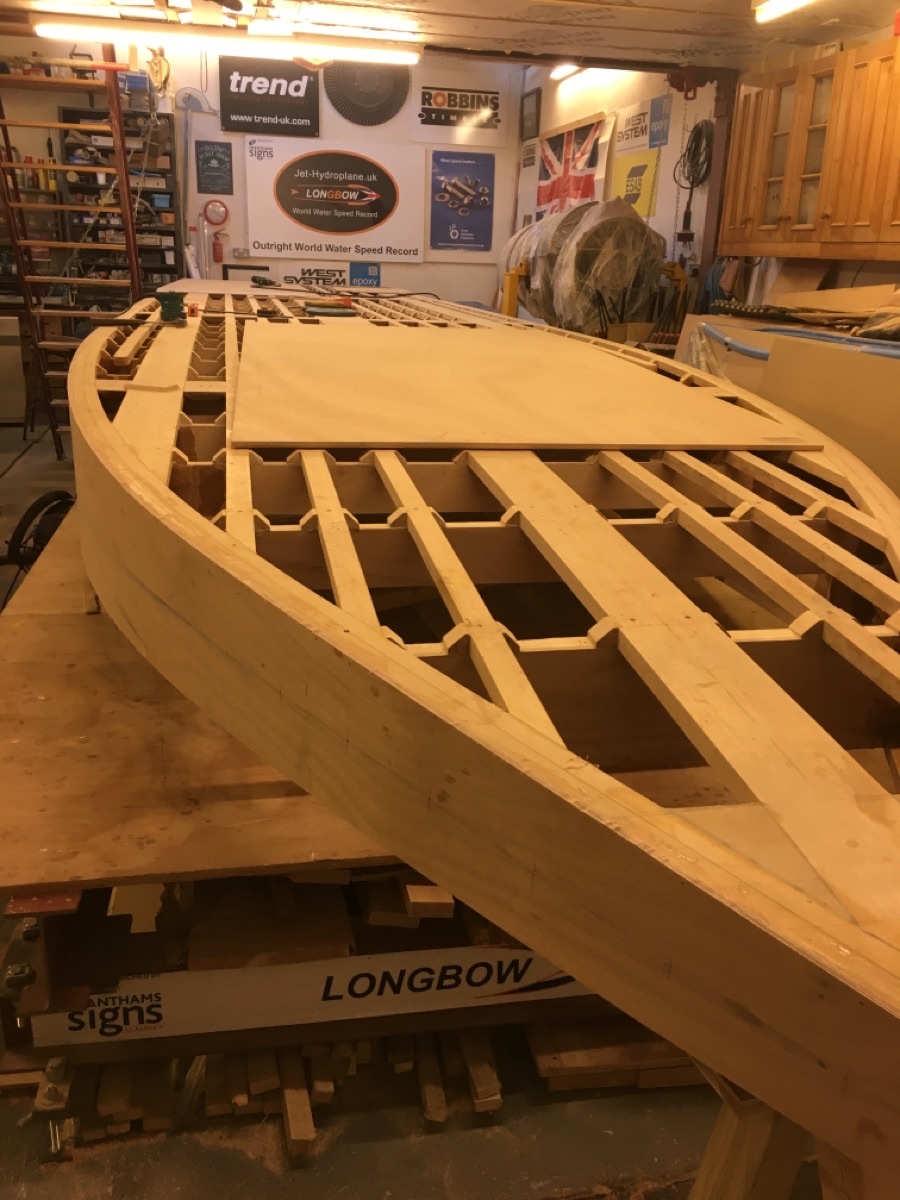
Now that the sides of the main hull are fixed into place we could then move on to the underside of the hull to tackle that in a similar manner. That is to say forming more scarf joints, cutting and shaping the panels, followed by lots of fixings and WEST SYSTEM epoxy. That is not going to be an easy task for the person who draws the short straw of having to crawl on their back inside the full length of the boat between the work table that Longbow is being built upon and the underside of the hull which is less than a couple of feet deep, to scrape off any epoxy oozing out from the joints. Not a place for anyone who is claustrophobic for sure.
On that joyful thought, that is it for this month’s update folks. As always thank you so very much for tuning in, if you have not done so already, please take a moment to like our Facebook page and we hope to see you again towards the end of November for the next instalment of building our jet hydroplane Longbow that with good fortune will hopefully lead to a British attempt upon the Outright World Water Speed Record.