This month it was great to see our good friend Dave Warby and his team back at Talbingo Reservoir in New South Wales, Australia for a weekend of development runs with his jet hydroplane Spirit of Australia II. As we move into our summer season here in the U.K. those on the other side of the world are in the midst of their winter and Dave said it was the coldest temperature he has ever driven the boat with temperatures around 12ºC in the day dropping to 7ºC at night. Although they did manage to get a few runs with the boat over the weekend and gather some useful information from them, frustratingly they had to call it a day and head back to the workshop due to high winds whipping up the lake surface. They will be back at Talbingo in a few weeks for a three day trial so hopefully the weather will be kinder on their next visit.
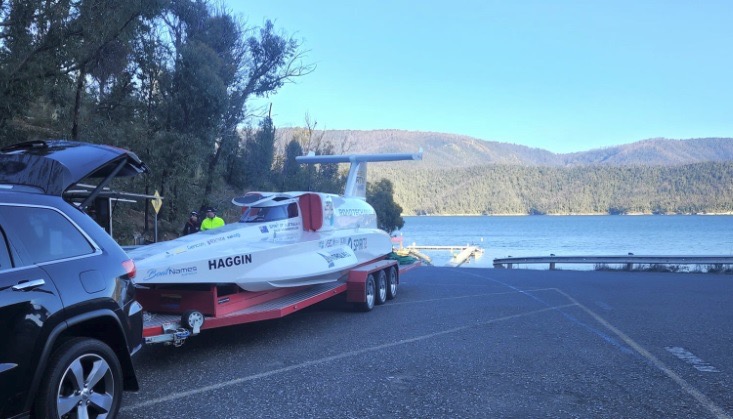
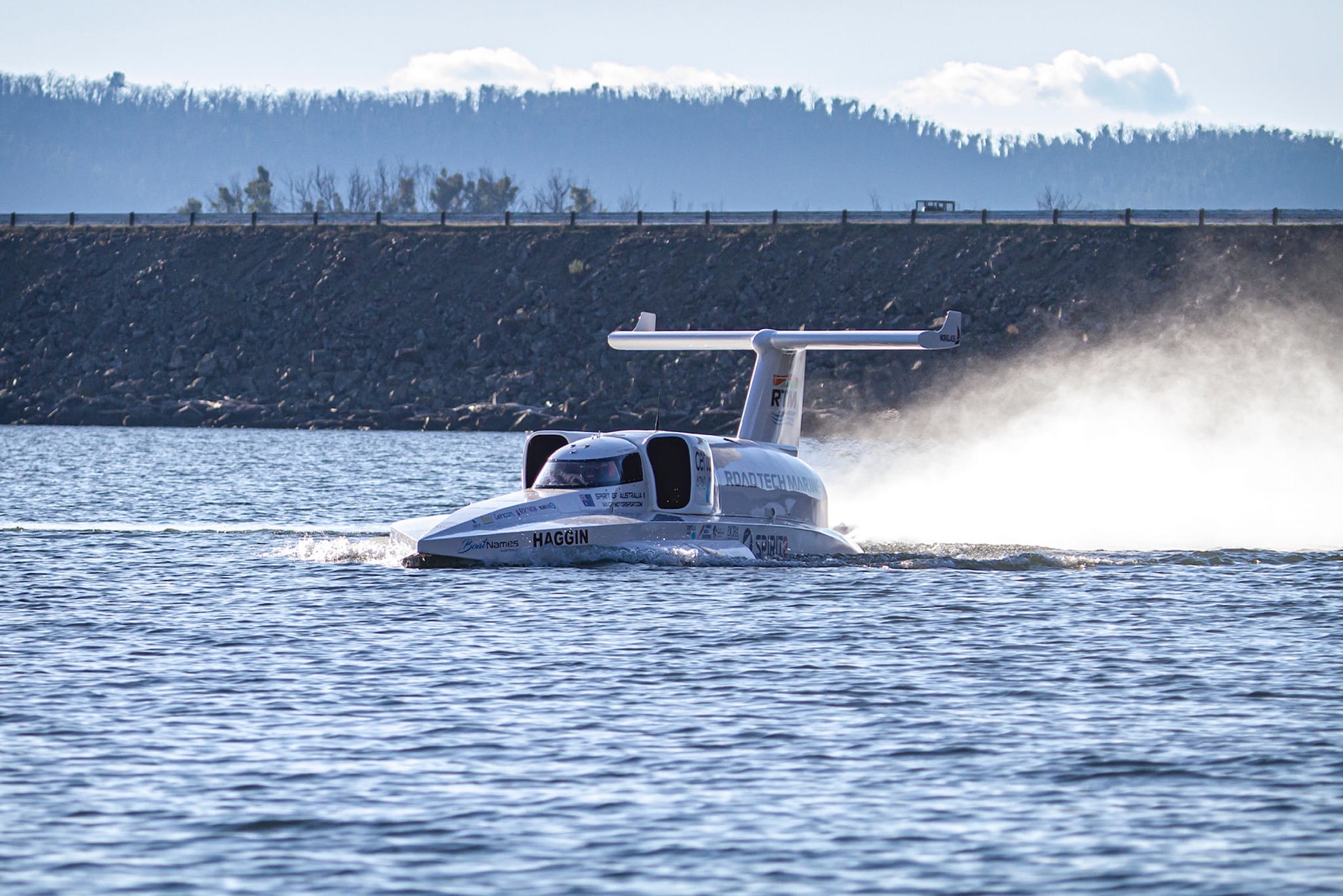
Back here in the U.K. with the warm weather now upon us I had to put off working on our jet hydroplane Longbow to help my youngest son Robert and his partner Caitlyn sort out their rear garden of their first home together. When they bought the property the lawn dropped down and away from the house in addition to being lower than adjacent properties so at best it was unacceptably boggy and at worst partially flooded during periods of heavy rainfall. A bit of time and effort working together makes the whole area a more usable space as the following photos show. However I have told the kids that is it for a while given that last month saw me kitchen fitting at two of their houses, then this month sorting out one of their gardens. The boat isn’t going to build itself and I have missed working upon it so I need to get back on it:
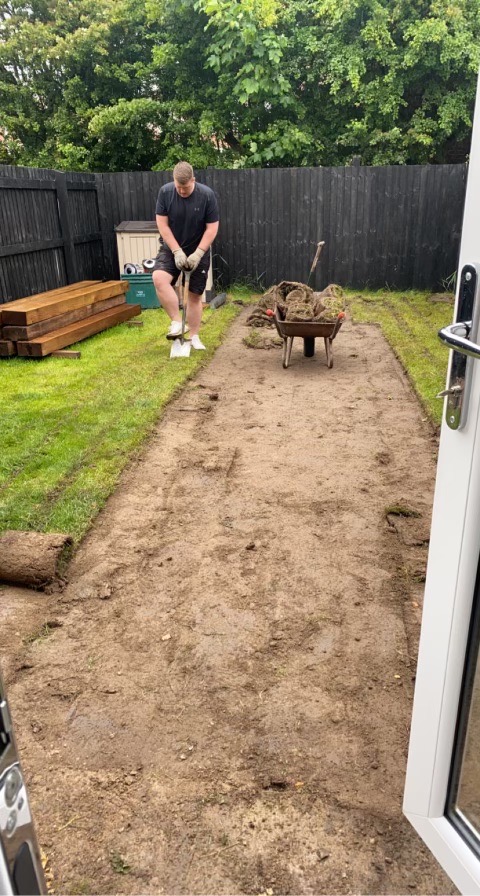
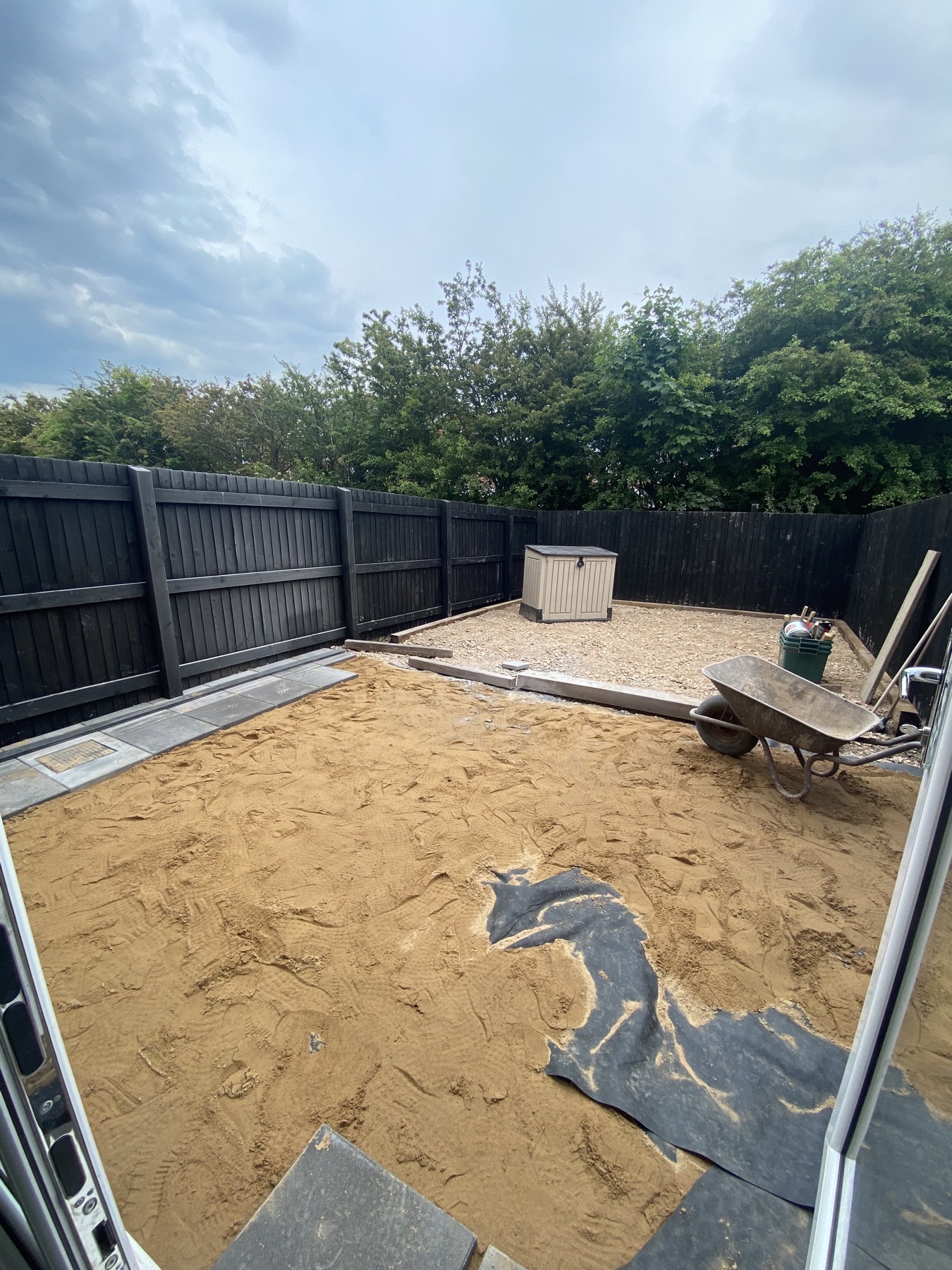

Last month you may recall that we built a gantry on the driveway of our cottage so can lift the jet engines in and out of the boat. With one of these engines out of its transport stand I was able to make some measurements of both the engine and stand framework along with also taking ‘as built’ dimensions from inside of the hull of Longbow now she is the right way up on her trailer. The purpose of all of that being to set about drawing up the cradle to accommodate the boat’s twin Rolls Royce Viper 535 engines side by side within the craft.
However before the I could draw the design for the cradle I had to make a decision about what metal to fabricate it from which, in turn was a bit of a headache as explained below.
With things like this it certainly doesn’t do any harm to look at how other people have mounted jet engines within their cars, trucks, boats planes, etc. When you look at what materials were used for engine cradles within previously built jet hydroplanes there is quite a variety of how people did it in each case. The American Hustler jet hydroplane used aluminium angles largely bolted together, Bluebird K7 had used high grade steel, the loose replica of that craft the K777 had used welded aluminium plate, whilst others had used plain steel and even some stainless steel.
Generally speaking the cheapest least problematic material to weld either in the workshop or by the side of the lake with what may be limited resources is in my view plain steel. You may also hear of people using what is commonly referred to as Chromoly steel for high performance vehicle chassis and driver roll cages. Chromoly gets its name from the chromium and molybdenum within it and more technically goes by the designation number 4130.
It is a misconception that Chromoly 4130 is lighter than plain steel but what it allows you to do is use a thinner section of it compared to plain steel for the same loads it is intended to carry. Hence if you can use a thinner material to do the same job as a thicker alternative you end up saving weight. In some situations saving weight is important for example with race cars designer Colin Chapman he was well aware his Lotus cars would win races if they were lighter than his competitors whilst being of similar engine performance.
The following photos perhaps illustrate the point where you can see the thickness of plain steel tubing used in the jet engine transport stand compared to the thickness of a high grade steel square tube similar to that used in the chassis of Bluebird K7.
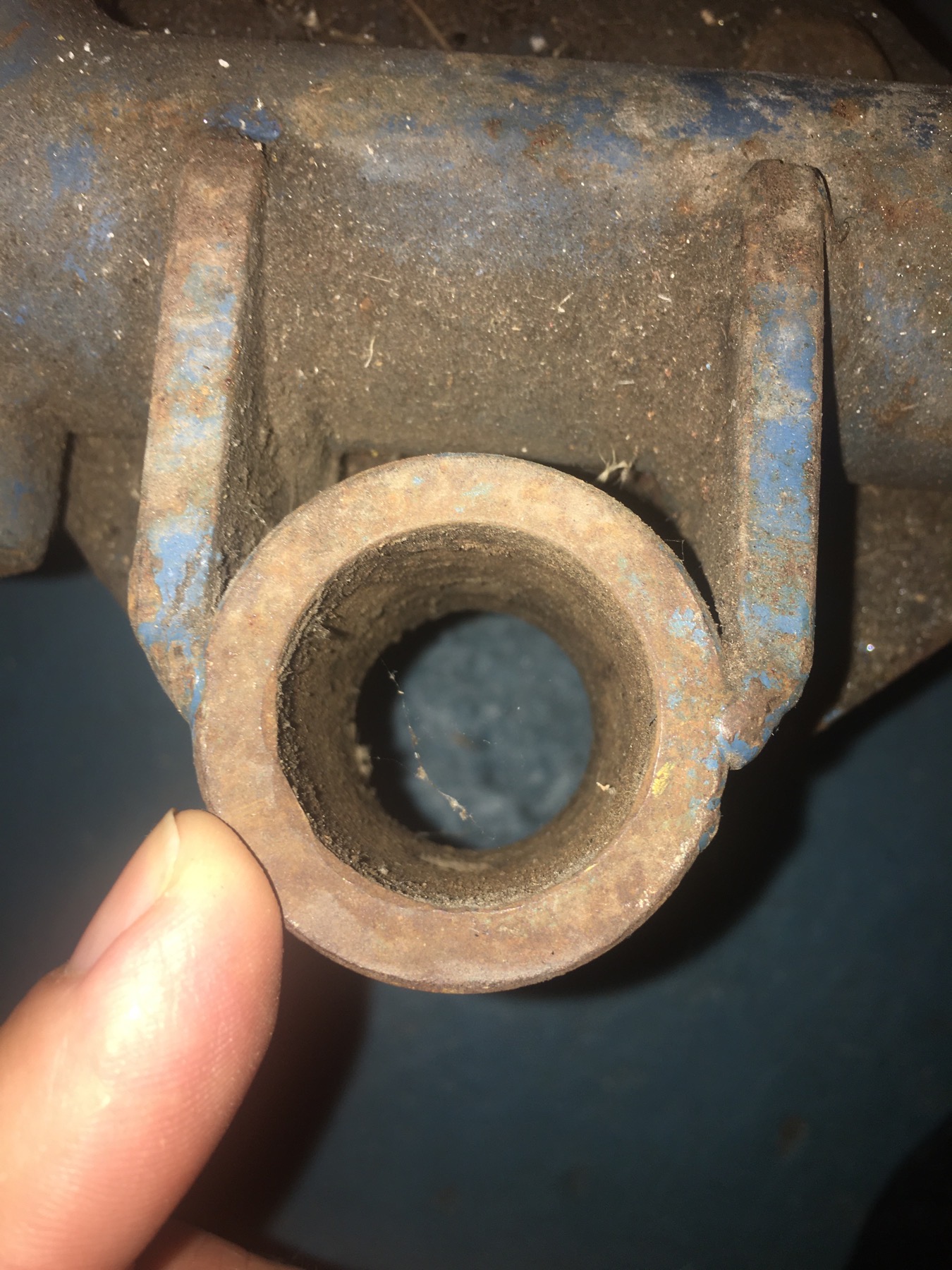
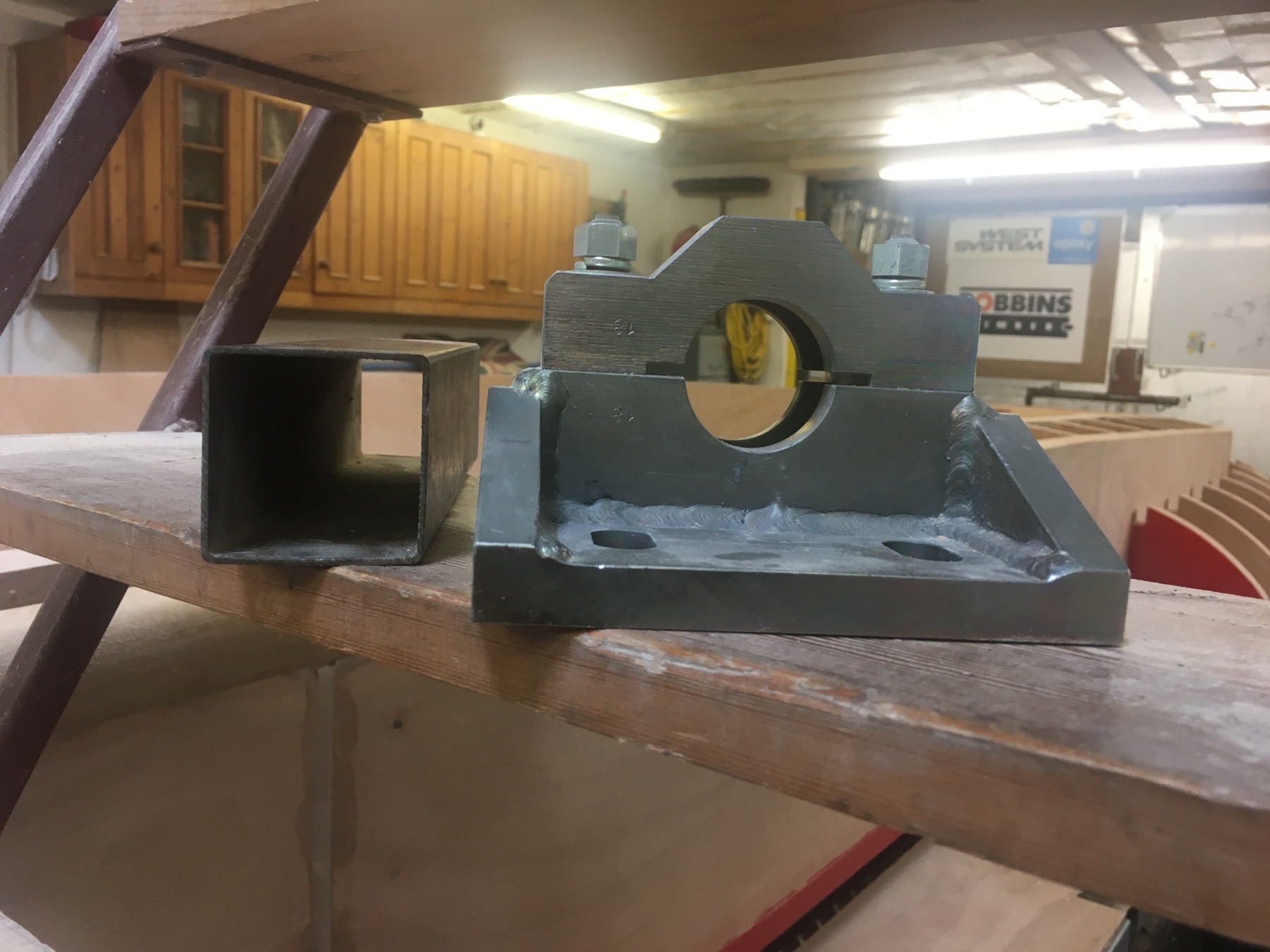
If we were using just one jet engine within the hull of Longbow then the amount of metalwork required to carry that single engine within the hull would be relatively small and consequentially the difference in weight between using a thin walled high grade steel and a much thicker walled plain steel to do the same job would be relatively small compared to the weight of the entire craft. However since in the case of Longbow we require a metal framework that will carry two jet engines side by side within her hull then the amount of metalwork to achieve that design function is significant and hence the total weight of that metalwork is in our case worth keeping to a minimum. I can always add weight if needed but taking weight out of the boat once built might not be so easy.
One of the downsides to using Chromoly 4130 is that the thicker amount of it you want to weld, the greater the requirement to heat treat the material both prior to and after welding, if failure of the joint in service is to be avoided. Another downside is that you have to be very careful indeed about the welding of any plain steel brackets, plates, etc to Chromoly 4130 tubing as failure of the joint in service to these dissimilar metals can readily occur.
Chromoly 4130 steel was initially developed in Ohio, USA for the American aircraft industry, being in use as far back as 1926 and an alternative high grade steel was similarly developed for the British aircraft industry designated by the British Standard BS T45. The Spitfire and Hurricane aircraft use BS T45 steel tubes as have some of the land speed record cars and many other high performance vehicles. A couple of advantages of T45 tubing over 4130 are that you can weld T45 without having to undertake the heat treatment referred to previously and you can also readily weld plain steel brackets and plates to it without fear of joint failure.
With the jet engine cradle for Longbow there was then the decision of whether to make it from square or round section metal tubing. Round tubing is the strongest shape by weight being more resistant to bending and torsion (twisting) especially where load paths may be variable. It is not therefore surprising that round tube is by far the most popular shape of both 4130 and T45 tubing. So given we need to accommodate both jet engines within a very limited space, then for the combination of strength, lightness of the structure being fabricated, ease of welded joints including attaching brackets, plates, etc, in addition to availability of material here in the U.K. BS T45 tubing is our preferred choice for our twin jet engine cradle.
Now with all of that in mind it was time to start doing some schematic drawings and I needed to be very careful with the layout as the space in the hull to accommodate the twin Vipers side by side is very limited. I also have to bear in mind that the engines may need to be moved forwards or backwards within the hull from their original design position once we get around to seeing how Longbow sits at rest on the surface of the water and her balance when running. There are also parts of the engines that stick out and get in the way of what would otherwise be the most compact and direct routing of some steel tube pathways but the following development concept sketch will perhaps give you a flavour for the layout.
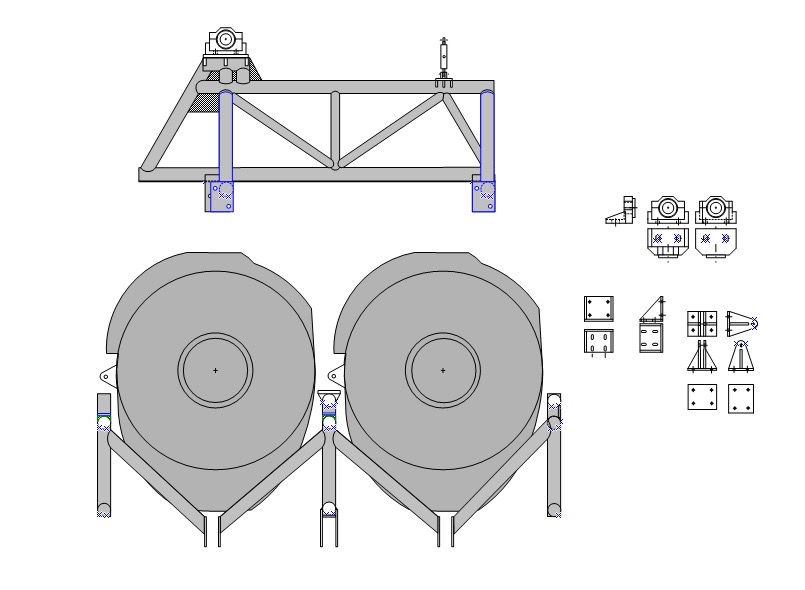
Once everyone is in agreement over the final design for our engine cradle we can then place an order for the material through our metalwork sponsor, John W. Laycock based in Keighley, West Yorkshire, whose MD Mark Sugden has so very kindly supported us throughout the build of Longbow including supply of all the metalwork for Longbow’s trailer.
That is all for now folks and see you at the end of July for the next instalment with hopefully more physical progress on our jet hydroplane Longbow now that I have sorted my children’s jobs out!