Early timing of our update this month as our website guru Neil of Progress Concepts asked me if I could jot something down, sooner rather than later as he is taking a well earned break for the seasonal holidays.
They do say time goes quicker as you become older and this year in particular seems to have flown by for me at least. As we went into summer we turned the hull of our jet hydroplane Longbow the right way up with the help of so many friends after I had struggled through the freezing temperatures of winter with every electric heater I could muster to get her painted on the underside. Following that there was sanding and cleaning the inside of her hull to remove waste epoxy, then I was sidetracked as only dads can be into helping two of my kids and their respective partners sort out their gardens and houses that each of them had just bought. Back with the boat they returned the favour to help dad erect the steelwork in the driveway that would allow us to lift the jet engines for Longbow in and out of her hull, all of which my good lady Gill is over the moon about looking at RSJ’s towering above her every time she opens the curtains or front door.
However the thing that really ate into the project time wise as we went into autumn, has been this steel cradle for supporting the twin jet engines within the hull that I never envisaged would take so long to sort. Initially I had drawn the cradle up specifying BS4 T45 thin wall high strength square tubing where I could have cut all the tube lengths and joints by hand here in my cottage workshop in a weekend.
There are few suppliers for the high strength tubing and it quickly transpired that those who would normally carry square section BS4 T45 tube were out of stock and would only source it as a special order if I was after enough to build the whole boat out of it. Stumped at the first hurdle we made the decision to alter the drawings and go for off the shelf available round tubing. The connections for that can be done by hand but as one pipe has to saddle around another and there were various angles involved a much better job is having them cut by laser or plasma. That turned out to be a right headache with pipes going walkabout around the UK with the courier, a pipe going missing and then having to dress the plasma pipe ends up in preparation for fabrication but eventually we got them over to our welder Steve Charlesworth in Huddersfield at the end of last month.
At time of writing the engine cradle is still a work in progress so it is going to be in the New Year before it is ready for collection and trial fitting in the hull. That being especially so since Steve has had more pressing issues to sort with livestock, snow and ice on the moors at his farmhouse and then like everyone else it’s Christmas holidays with his family.
In the meantime whilst we were waiting for the steel cradle to be fabricated it was time to get back into doing some epoxy laminating with the task of forming the timber sections at the bottom of the hull that the engine cradle will have to bolt into.
Colin Fletcher, Area Sales Manager for our sponsor Wessex Resins & Adhesives Ltd very kindly re-stocked us with a selection of their WEST SYSTEM products such as new pumps, mixing tubs / sticks and spreaders.

As mentioned previously the UK descended into temperatures well below freezing which we are just not geared up for dealing with on a regular basis. Whilst the WEST SYSTEM can still cure at temperatures down as low as 4ºC using their 205 Fast Hardener it made more sense to form the laminates in the warmth of our cottage than swallow the electric costs of heating up the workshop for a small job.
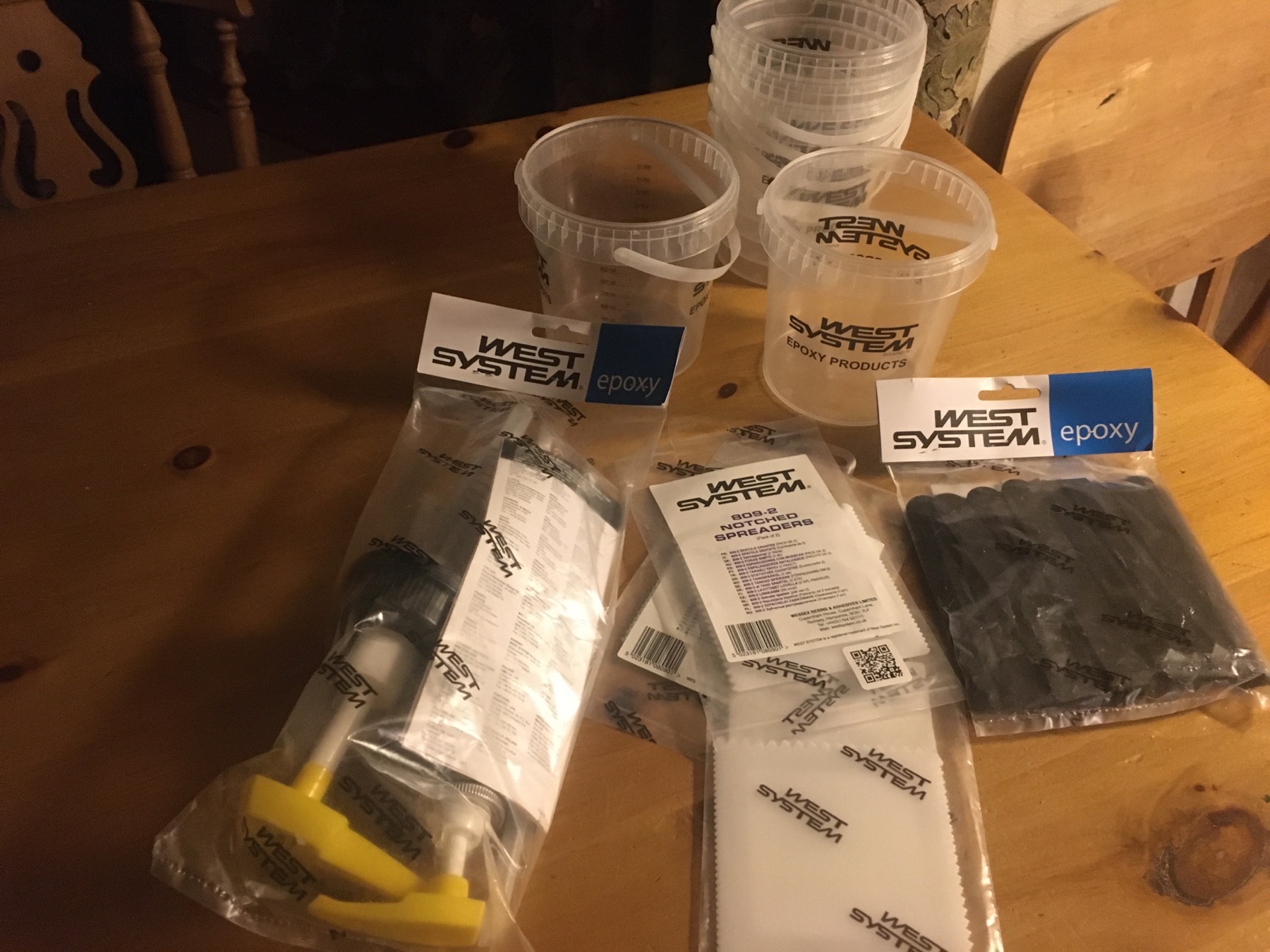
I am not so sure my long suffering wife Gill was too happy about me using the dining table for doing the laminations over a few days as she glared at me eating meals off our knees but I sure enjoyed being able to work on the boat whilst watching a film, having a brew and biscuit. I did say to Gill it was a pity the main hull wouldn’t fit in the cottage as it was so much cosier to work on to which she just shook her head in silent disbelief.
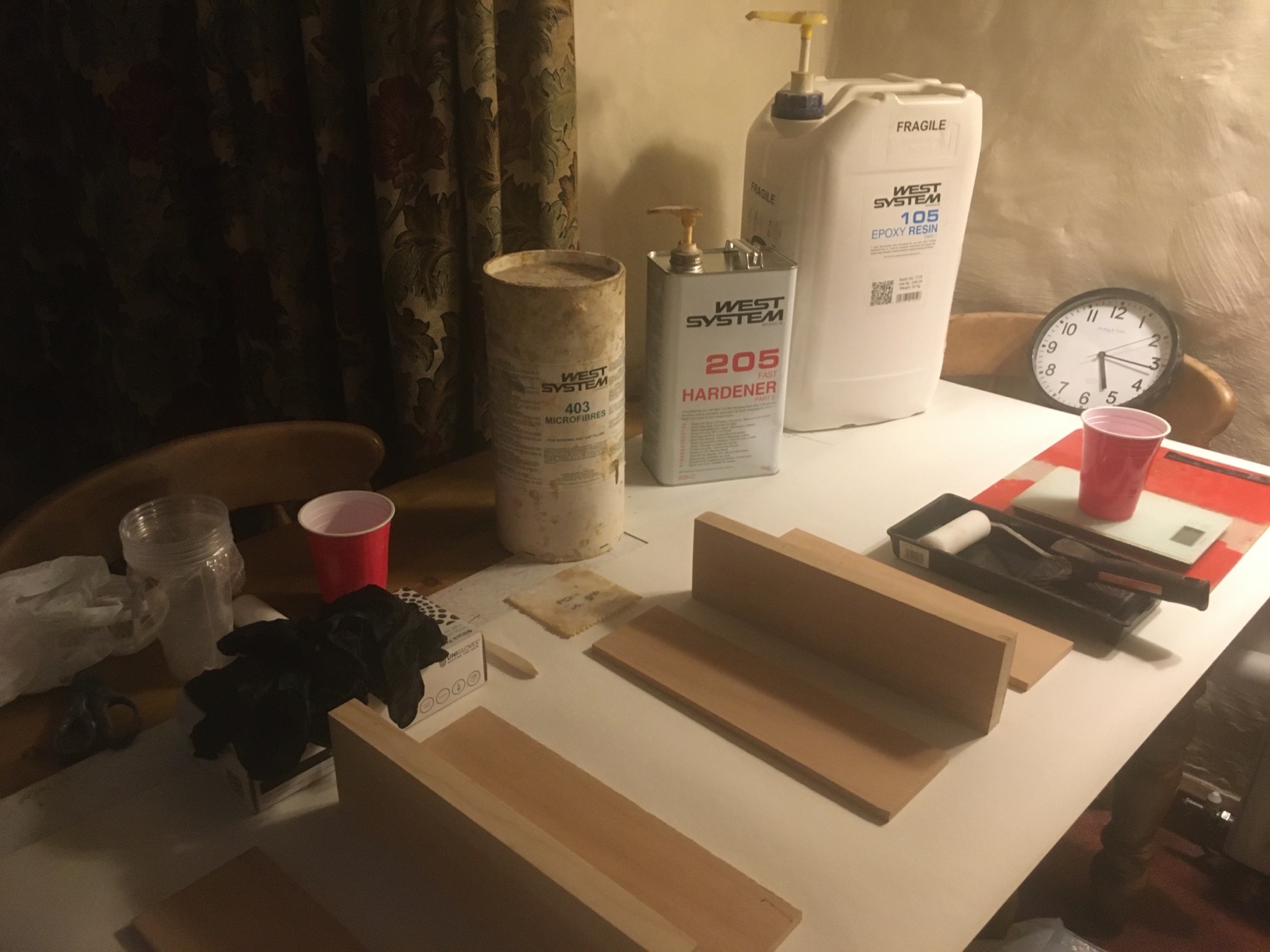
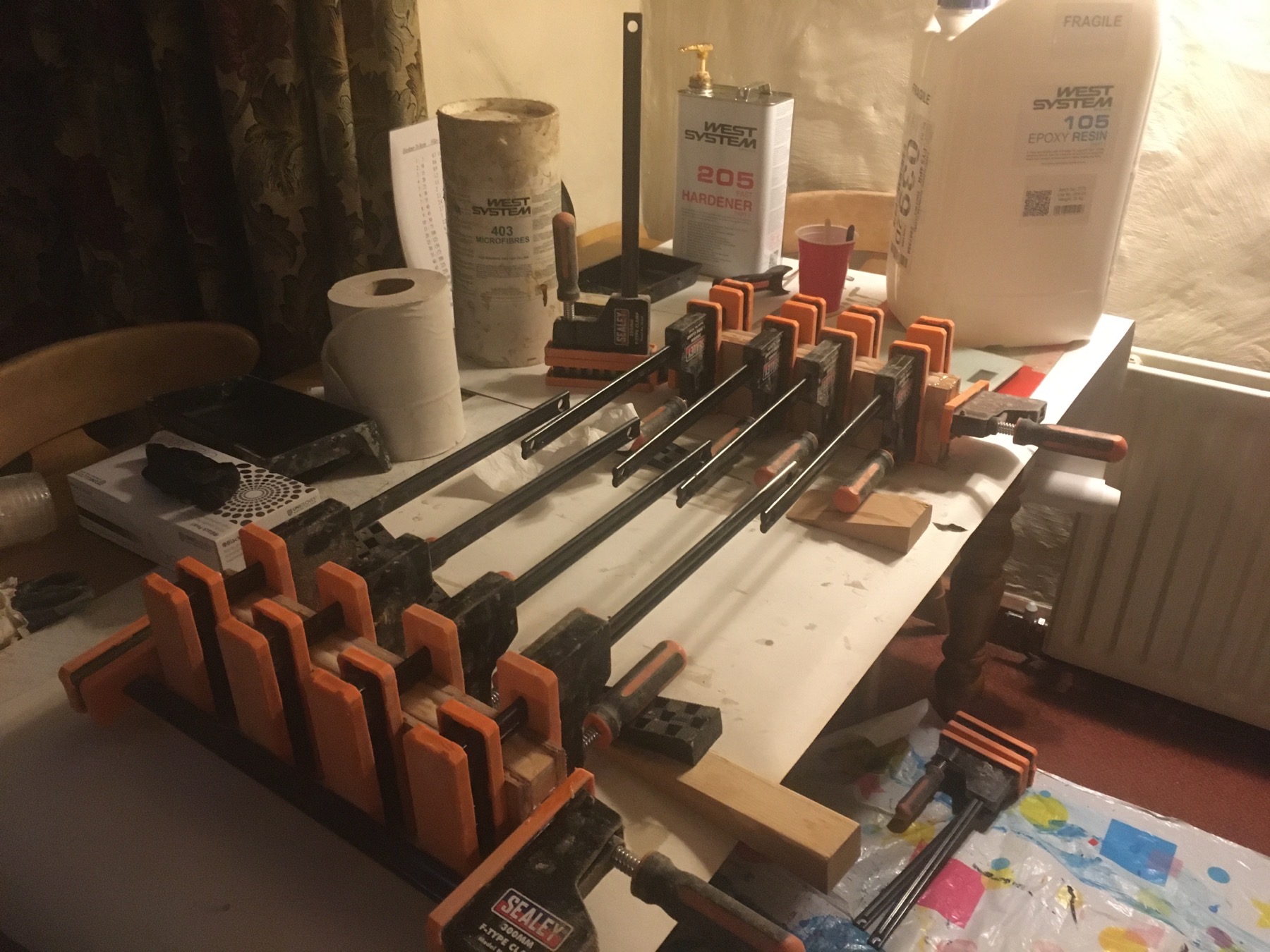
Anyway with the laminates formed without a drop of epoxy being spilled on to the carpet I can pop them into the bottom of the hull once the temperatures pick back up in the workshop.
In other news one of our sponsors WEC Group, whose headquarters are at Darwen, Lancashire have entered into partnership with the Ruskin Museum, having the full support of the Campbell Family Heritage Trust to be the Museum’s engineering partner for the jet hydroplane Bluebird K7. Steve Hartley the MD of WEC Group has a passion for speed as discussed below, is highly patriotic and was aware that Bluebird K7 was originally built from scratch in around a year just a few miles down the road from his factory at Samlesbury.
When Steve kindly offered for his apprentices to fabricate our trailer for Longbow he not surprisingly had a scan through our website and with that mentioning the history of Bluebird K7 amongst the jet hydroplanes it prompted him to reach out in private to Gina Campbell QSO, her partner Brian and the Trustees of the Ruskin Museum. That partnership may well have been formed some time ago with reference to unnamed engineering support having been secured within previous public statements by the Museum. As to the timing of the announcement formerly naming Steve and the WEC Group, as the Museum’s partner, one might imagine it being deemed appropriate by the parties to do so now, for what might be expected to follow shortly in the New Year but we will just have to wait and see.
Steve founded the WEC Group company which has grown to employ around 900 people and you could not wish to meet a more helpful genuine chap. I can remember sitting down at a meeting with him in his boardroom and he looked at me across the table and said if I want to I can put all of my staff onto a job I am passionate about. If I need to employ various people with certain skill sets outside of the company then I will. If I need to buy in specialist machinery then again I will. In other words whatever it takes to make it happen, he is wealthy enough, experienced enough as a tough businessman and driven enough to get it done. It’s as simple as that and it is a recipe that has seen the WEC Group under Steve’s leadership become very successful indeed, winning the Best Large Company Award in the north west for the last six years on the trot.
I have met Steve on a number of occasions in and out of his work and he has amongst his many toys that he owns, a couple of helicopters, an ex military Aero L-39 Albatros high performance jet trainer (that flew a display in this year’s Blackpool Air Show), in addition to one of his companies currently overhauling a BAE Systems Hawk T1 jet aircraft trainer similar to that used by the Red Arrows air display team that he has bought to run alongside his L-39.
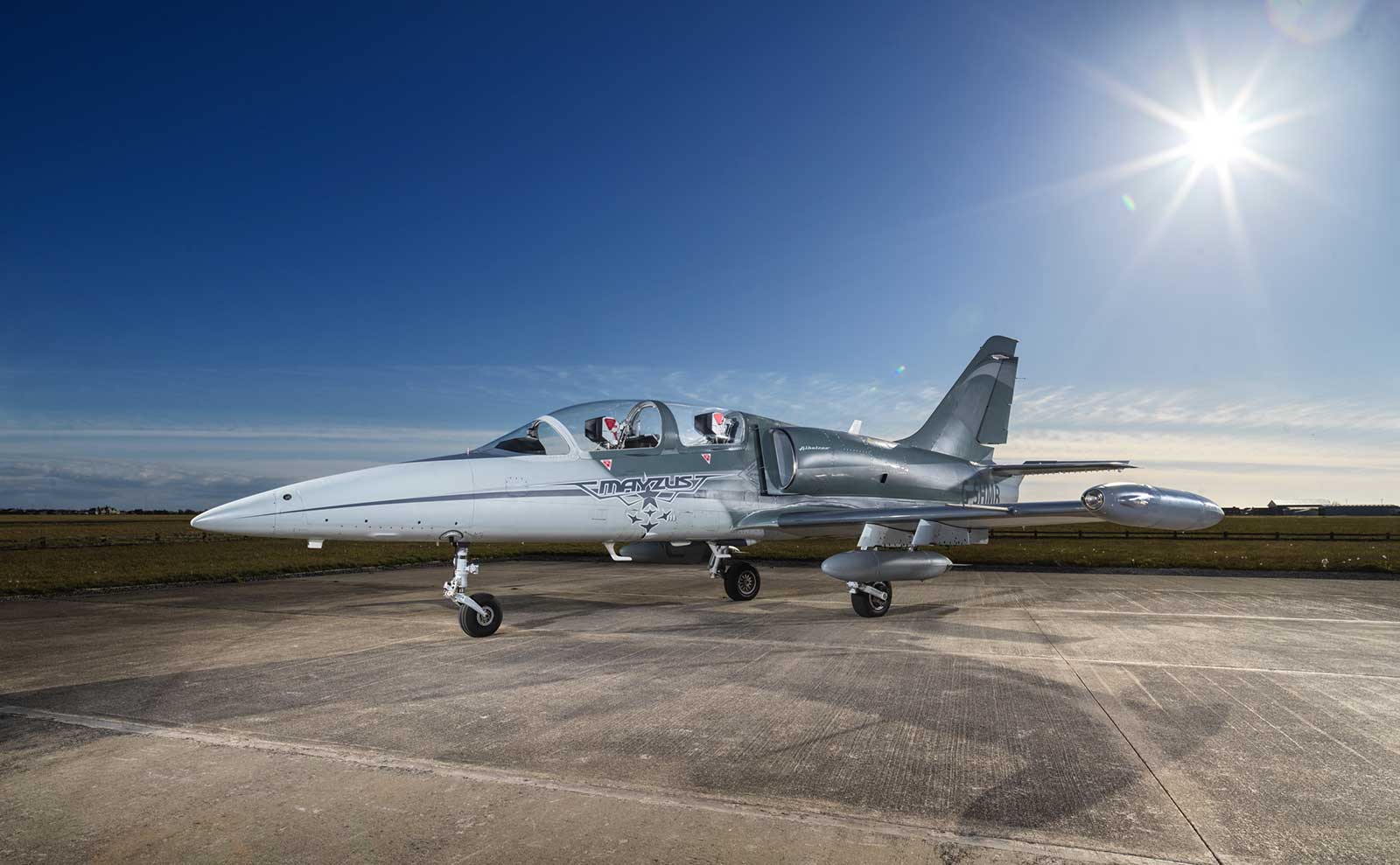
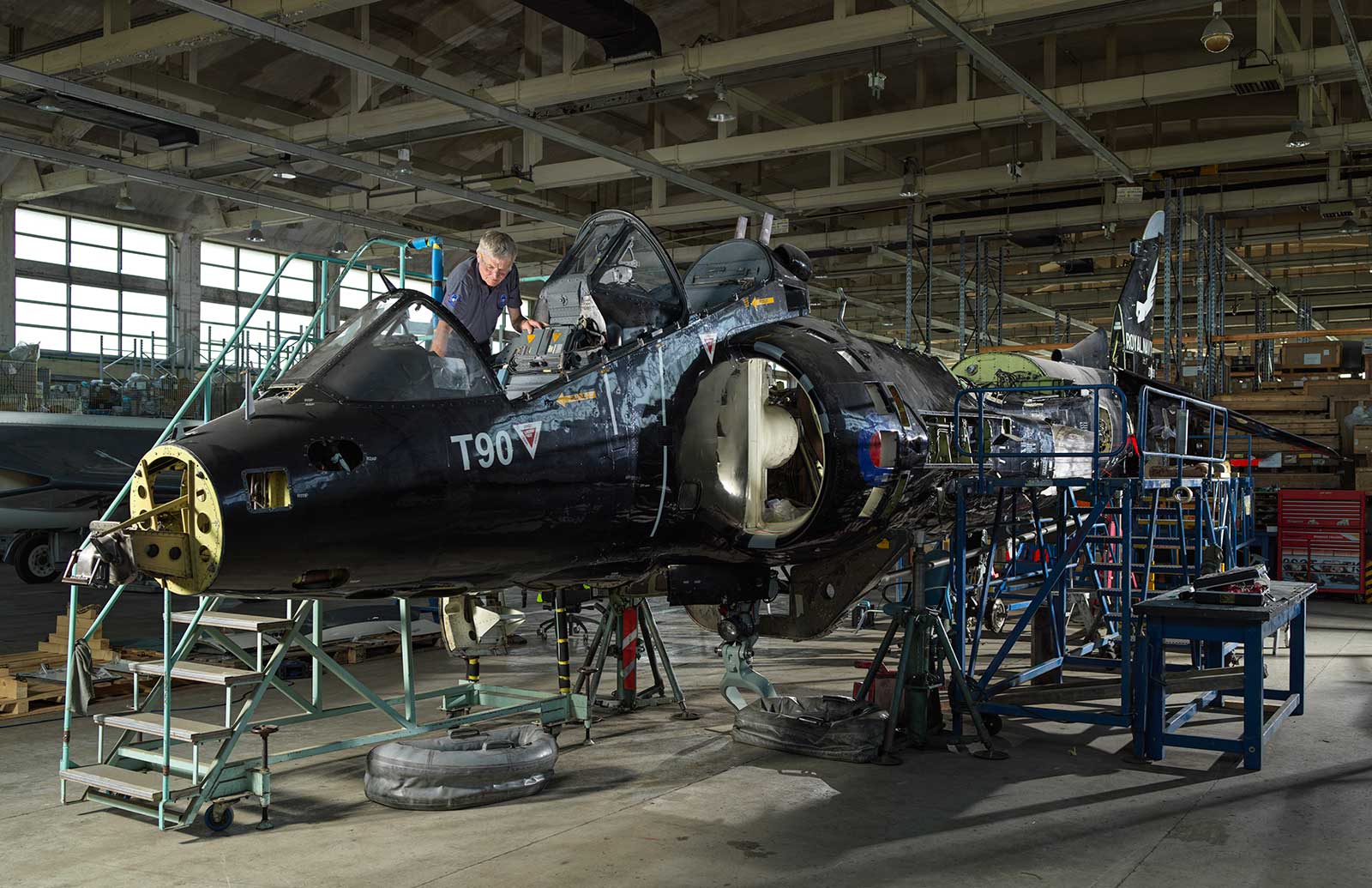
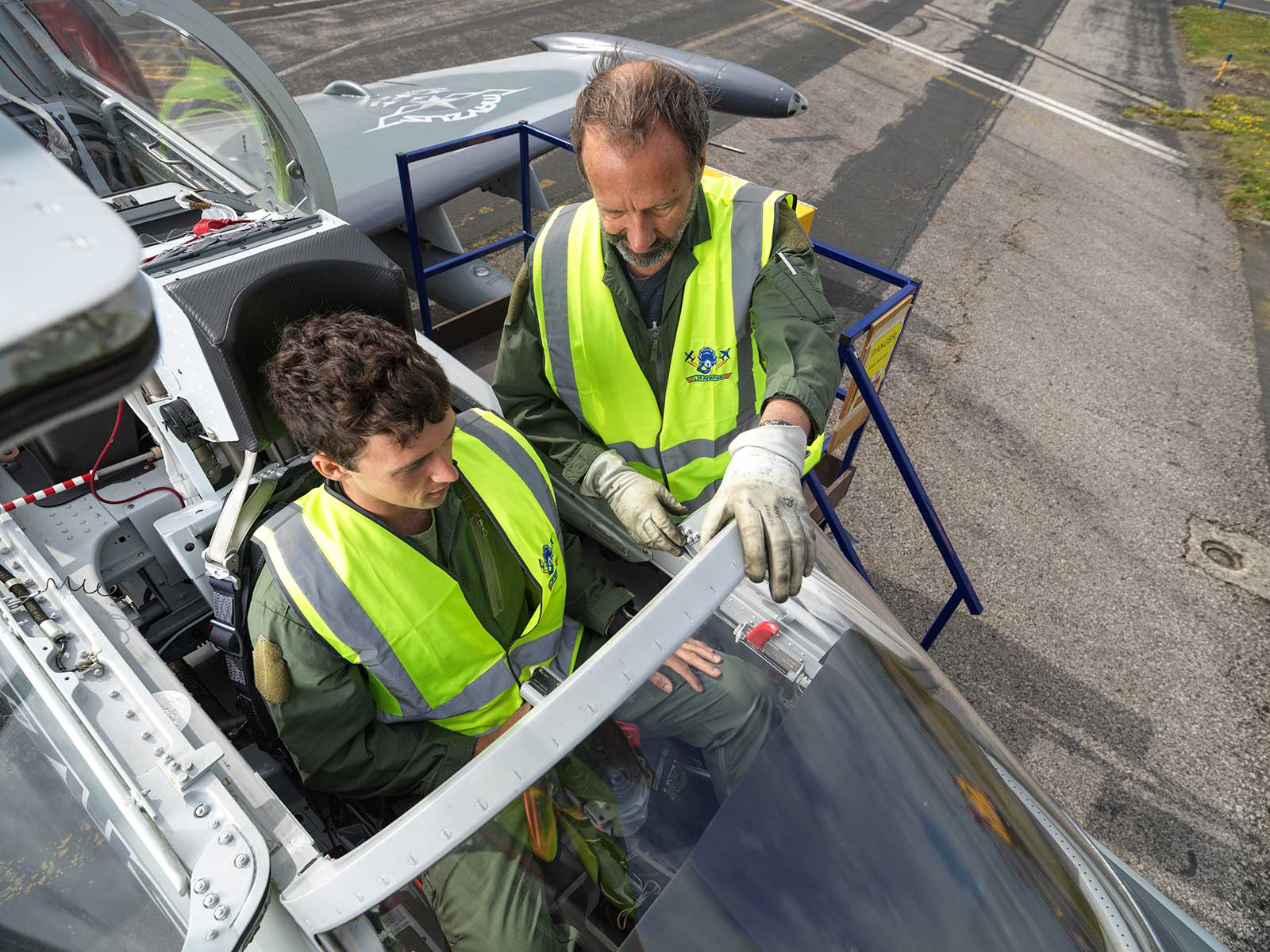
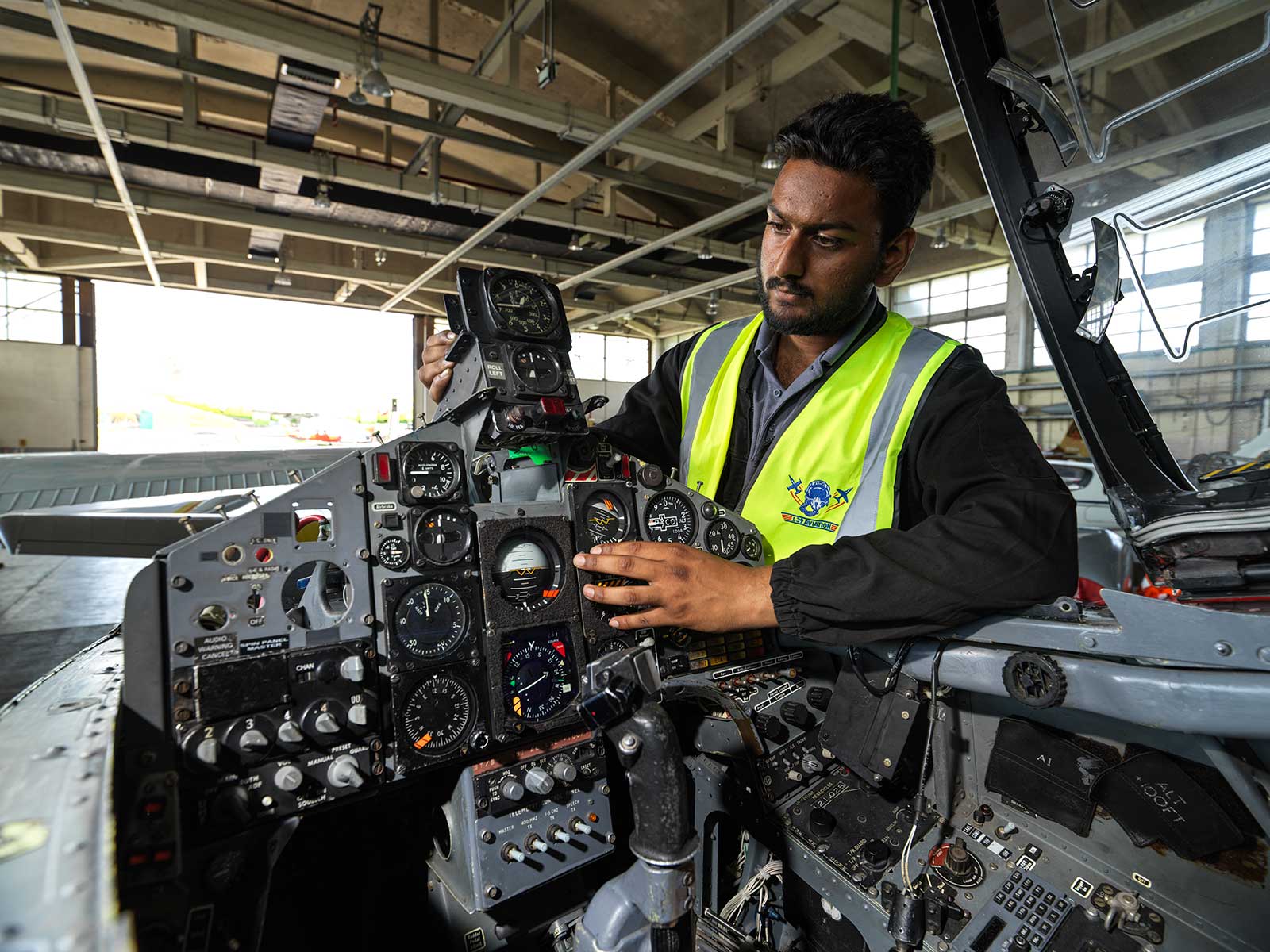
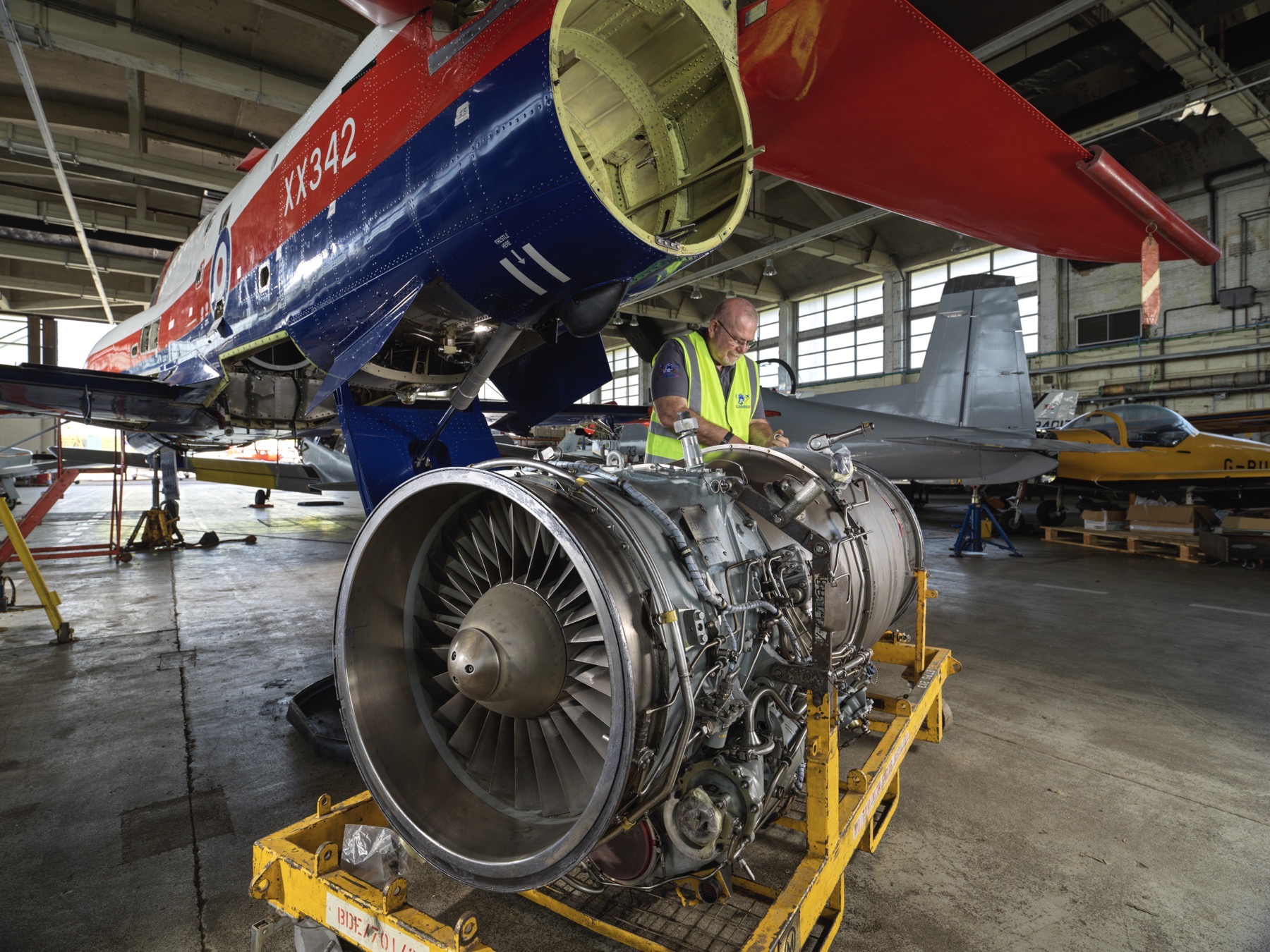
If that wasn’t enough Steve races a number of high performance vehicles internationally, an example of which is his ex John Watson McLaren MP4/1 which some of you who are race enthusiasts may recall was the first Formula 1 car with carbon fibre monocoque as detailed within the following article. Steve won the Masters Racing Legends Championship for 1966-85 Formula 1 cars this year.
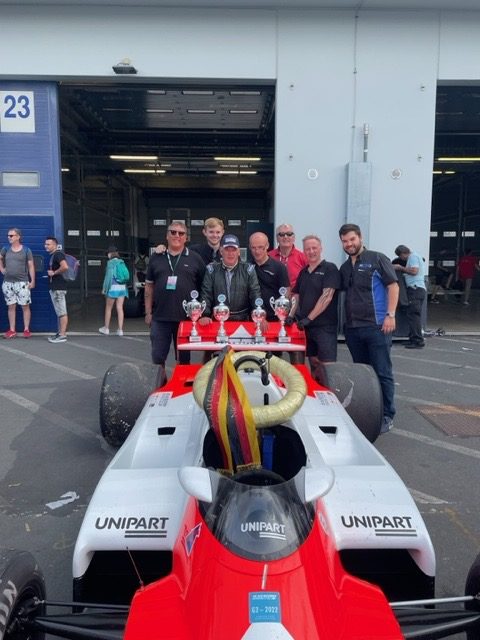
The following video show Steve racing his McLaren F1 car at Brands Hatch:
If you want to know what it is like to go up in an L-39 jet aircraft the following video of one flying in Australia will give you a flavour of what a thrill they are:
Steve’s aircraft and the company he formed to look after them, amongst providing other specialist aircraft services, are in part located just down the road from our project at Squires Gate Airport, Blackpool, which obviously will be helpful with our little venture in the times ahead.
Some time ago Steve wanted to commemorate that Darwen was the smallest town in the UK to finance through public donation a Spitfire during World War II. After some consideration and at a cost to themselves of £175K, WEC Group designed, fabricated and donated to the town a beautifully impressive stainless steel monument of the fighter aircraft that you can readily see as you drive through the town centre.
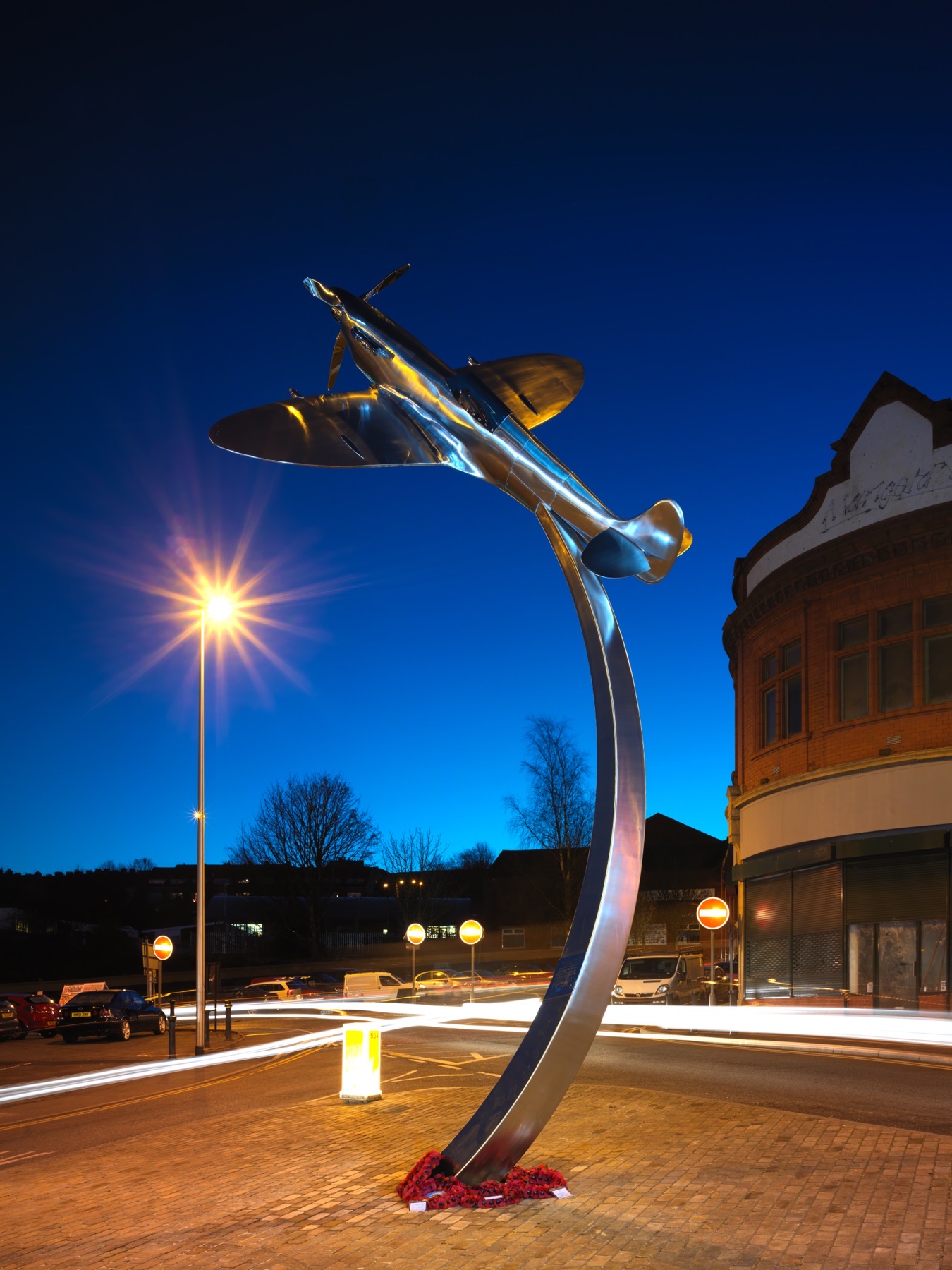
In the Lake District over which Steve flies his various aircraft he can look down upon the UK’s first stainless steel road bridge that his company built at a cost of £5 million pounds that replaced the previous one which had collapsed during stormy weather at Pooley Bridge, at the top of Ullswater.
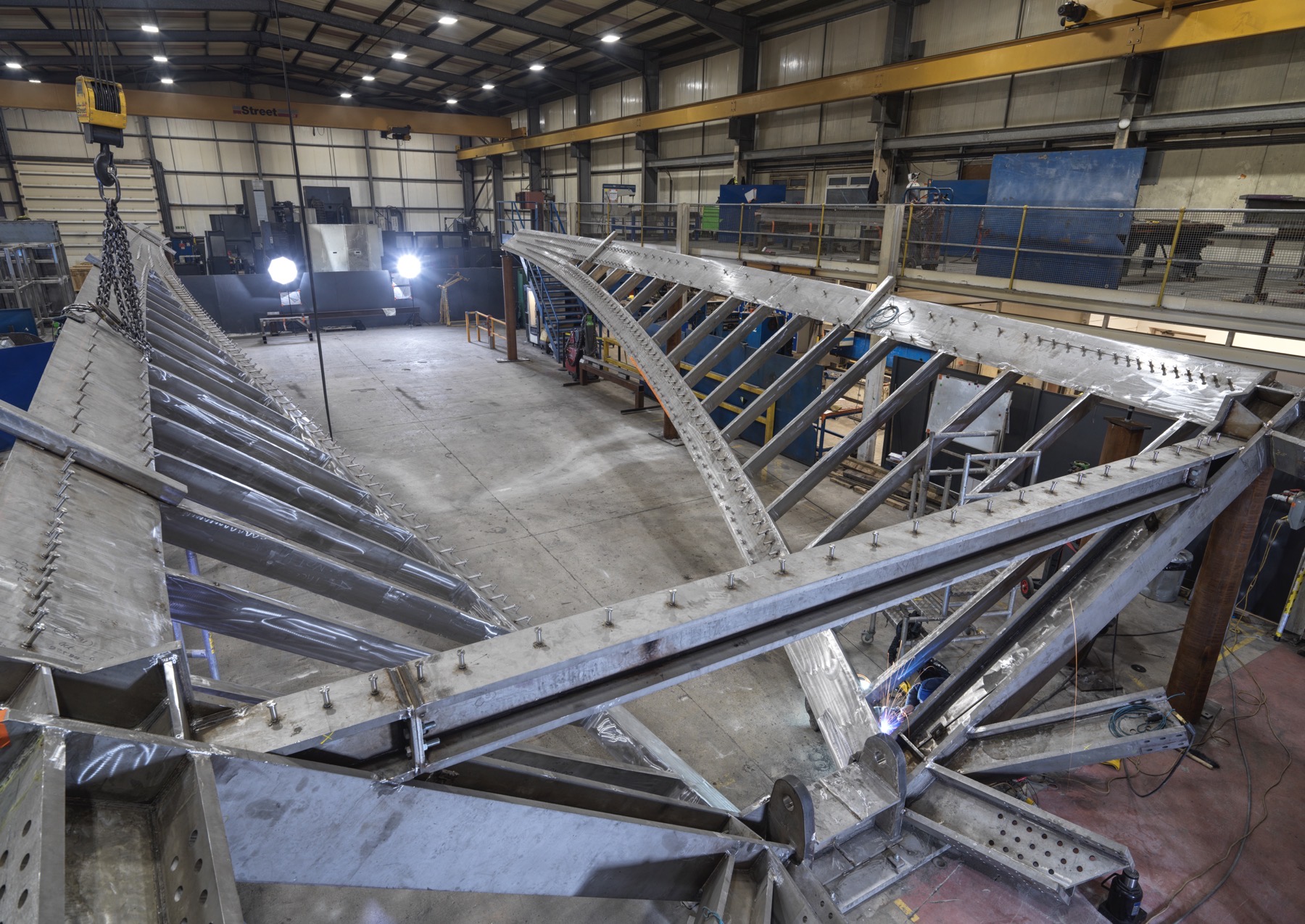
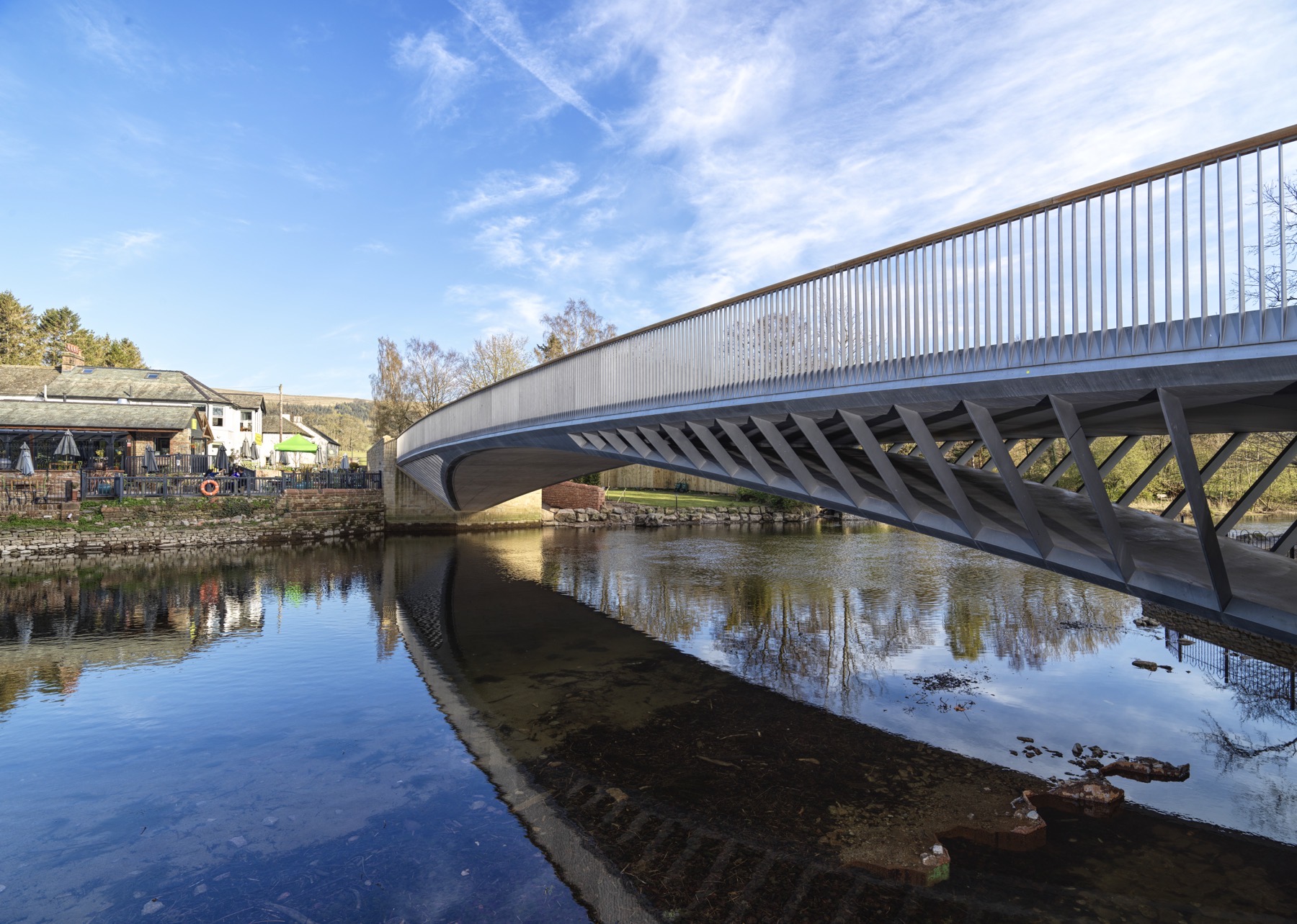
This of course is just an example of their work as you will appreciate just how many jobs are required from a bit of machining and laser cutting, to mammoth projects continually passing in and out of their doors each and every week, to run a profitable business employing getting on for a thousand staff.
However for me one of the prime examples of Steve’s good intentions is him building his new engineering apprenticeship academy, that he privately funded to the tune of £3 million in order to train our engineers of tomorrow.
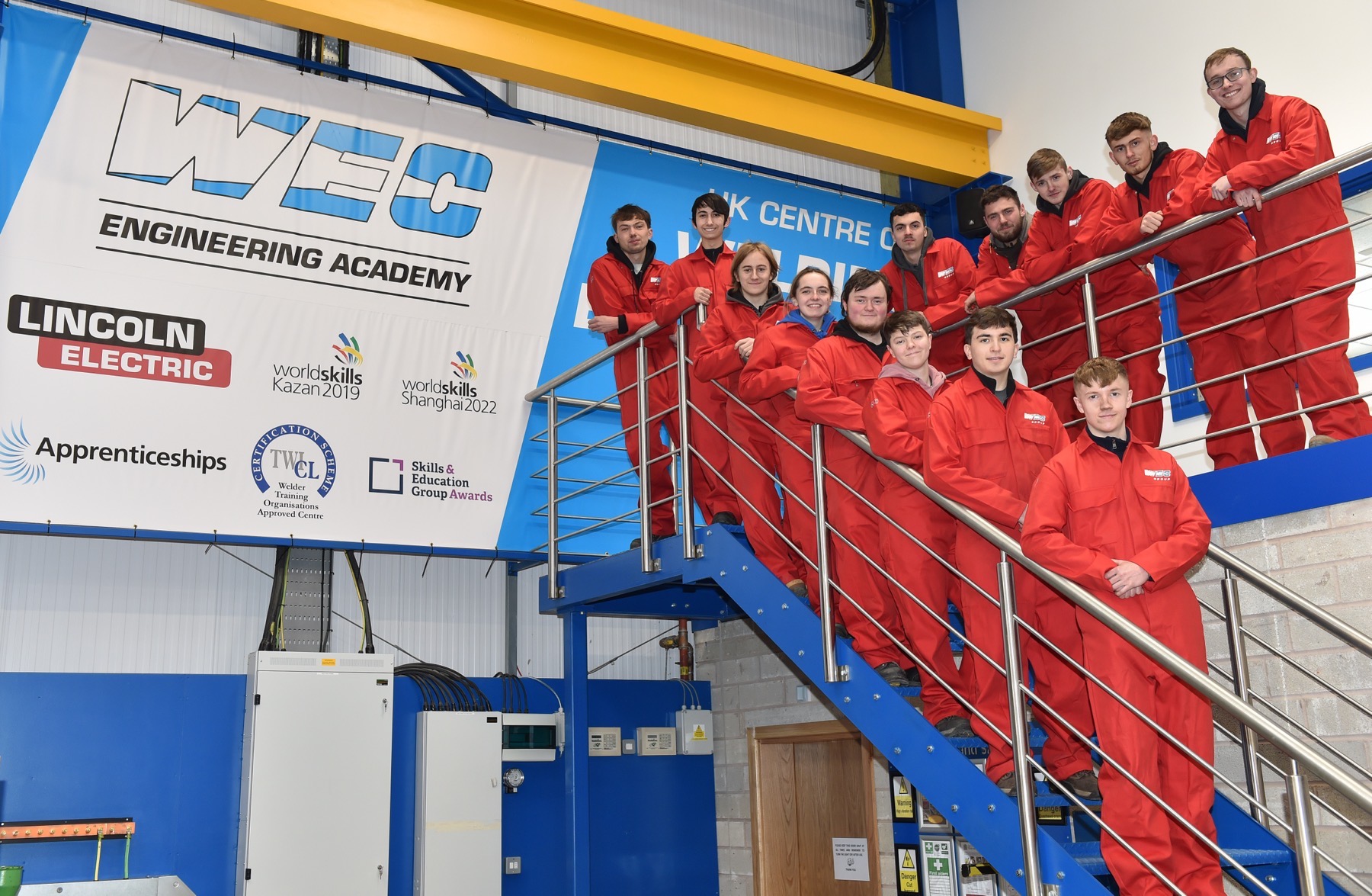
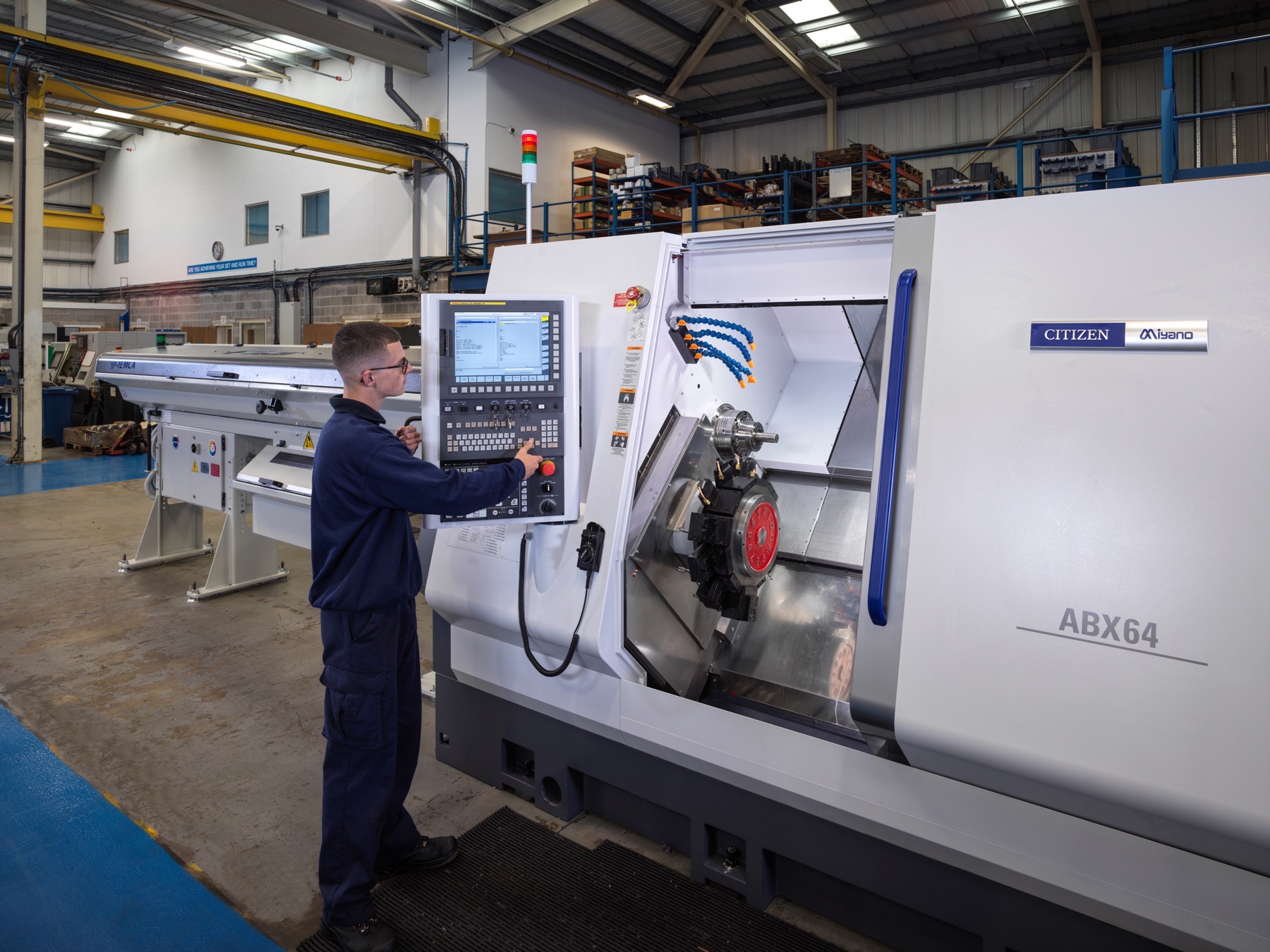
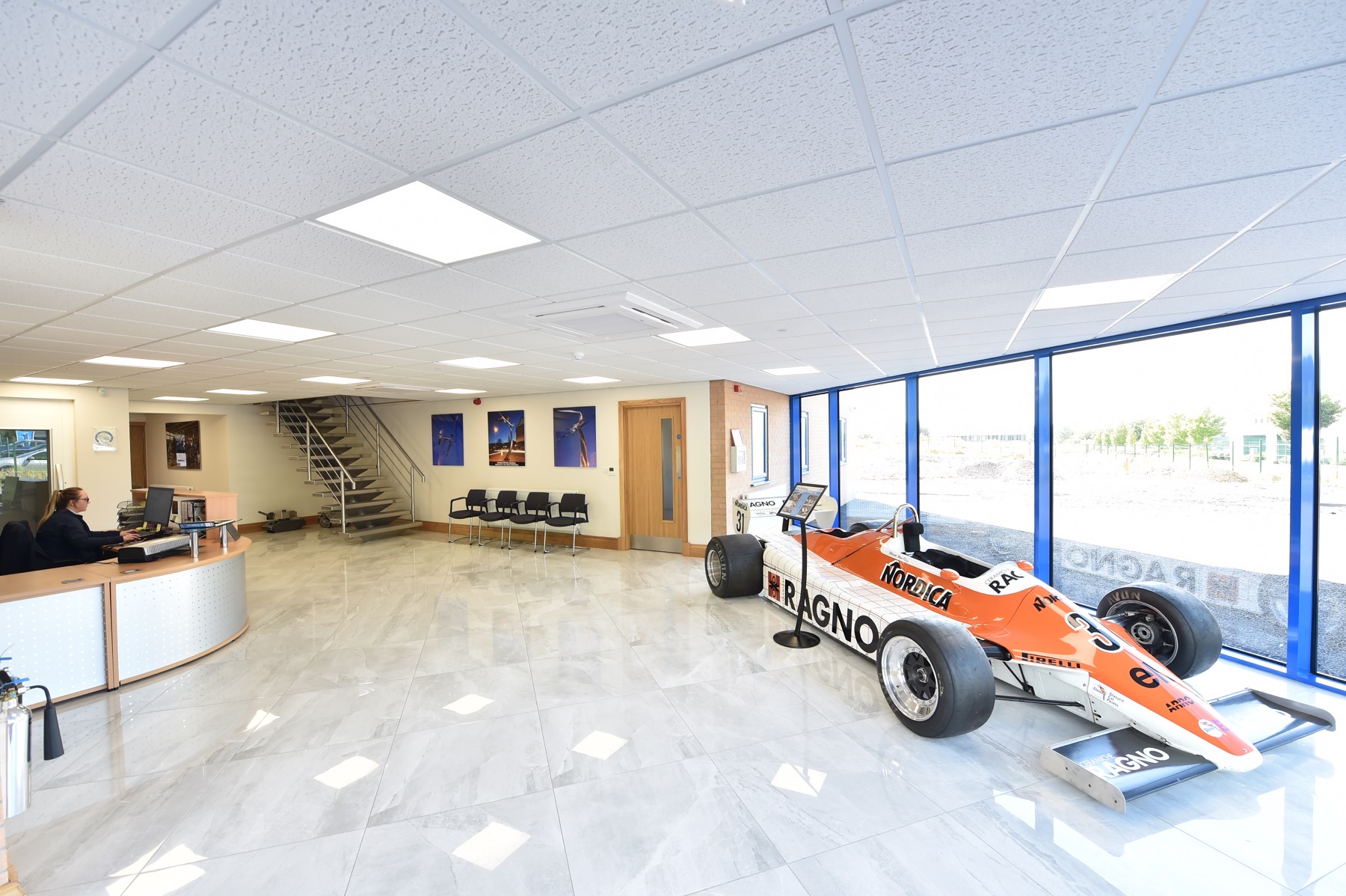
How good is that apprenticeship? Well an apprentice of theirs has been ranked within an international competition representing the UK as one of the top 10 welders in the world, which I trust you will agree speaks for itself with regards the calibre of their training.
All of us involved with Longbow are so very grateful to Steve and his umbrella of companies for their ongoing support of our little project as and when necessary.
So that is our round up for this year folks and all that is left to do is wish you all a very Merry Christmas and all the best for a successful & Happy New Year.