Thank you for tuning into our latest update for the project of building our jet hydroplane Longbow. The beginning of this month was spent with me finalising the drawings for the twin jet engine cradle and sending them off for our design engineer Paul Martin to cast his eye over them. Whilst my wife Gill and myself had made a good recovery from COVID that we had fallen ill to last month, unfortunately Paul, who had also got hit with the virus then had a bout of shingles. Understandably that put something of a delay into getting the engine cradle drawings signed off but once Paul was recovered and was able to do that I could then proceed with a further series of drawings. These additional drawings being required to quantify and order material from, along with them being used as an aid with the fabrication stages to follow.
The engine cradle height determines the height of the jet pipe coming out of the back of the engine in relation to the vertical distance it is up from the bottom of the hull and the bottom of the rear planing shoe.
As a nautical term the distance from the lake surface to the deck or the upper edge of a small boat where if the water reached and would then run into the hull is called the amount of ‘freeboard’. So for us really the distance from the lake surface to the bottom of the open ended rear of the jet pipe at the back of the boat is our equivalent ‘freeboard’ distance. Sketch 1 below may be helpful with the discussion.
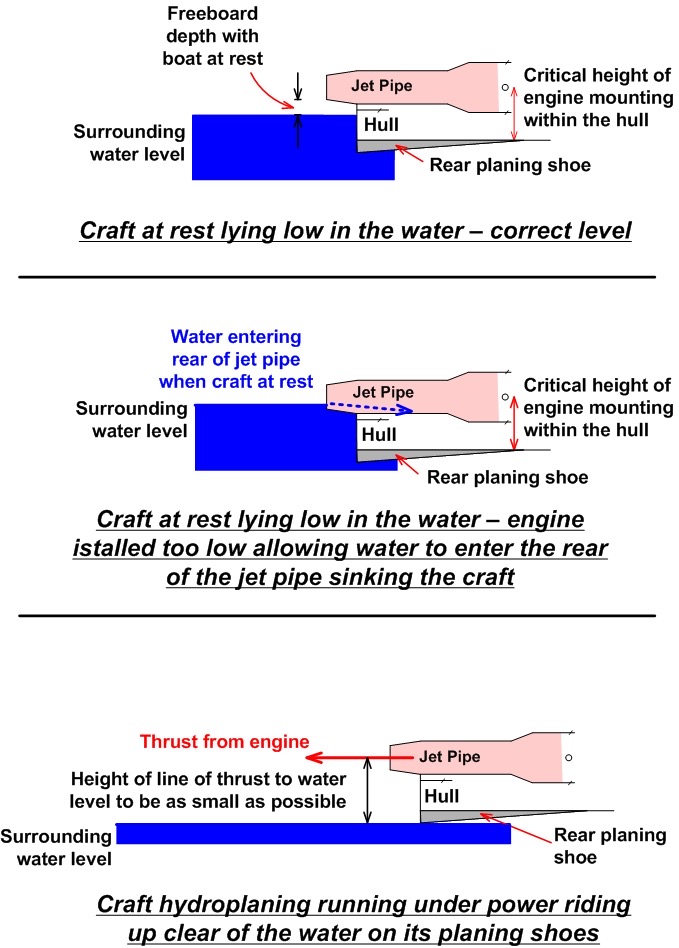
From a stability point of view when the craft is running under power on her three planing shoes we want the thrust coming out of the back of that jet pipe to be as close to the surface of the water as can get it. However when the craft is at rest she is no longer sitting upon these three points of her planing shoes, the whole underside of her hull is now within the water so she is floating much lower down and we can call this the level of her static buoyancy. Now the trick is to have enough static buoyancy with the craft full of fuel and the pilot on board, that the rear of the jet pipe is nothing more than a few inches above the level of the surrounding water. Get it wrong and the water will enter the rear of the jet pipe and sink the boat. The following photos compare the rear of the Crusader hydroplane and Bluebird K7 at rest where you can see the difference in the level of the jet pipe above the water.
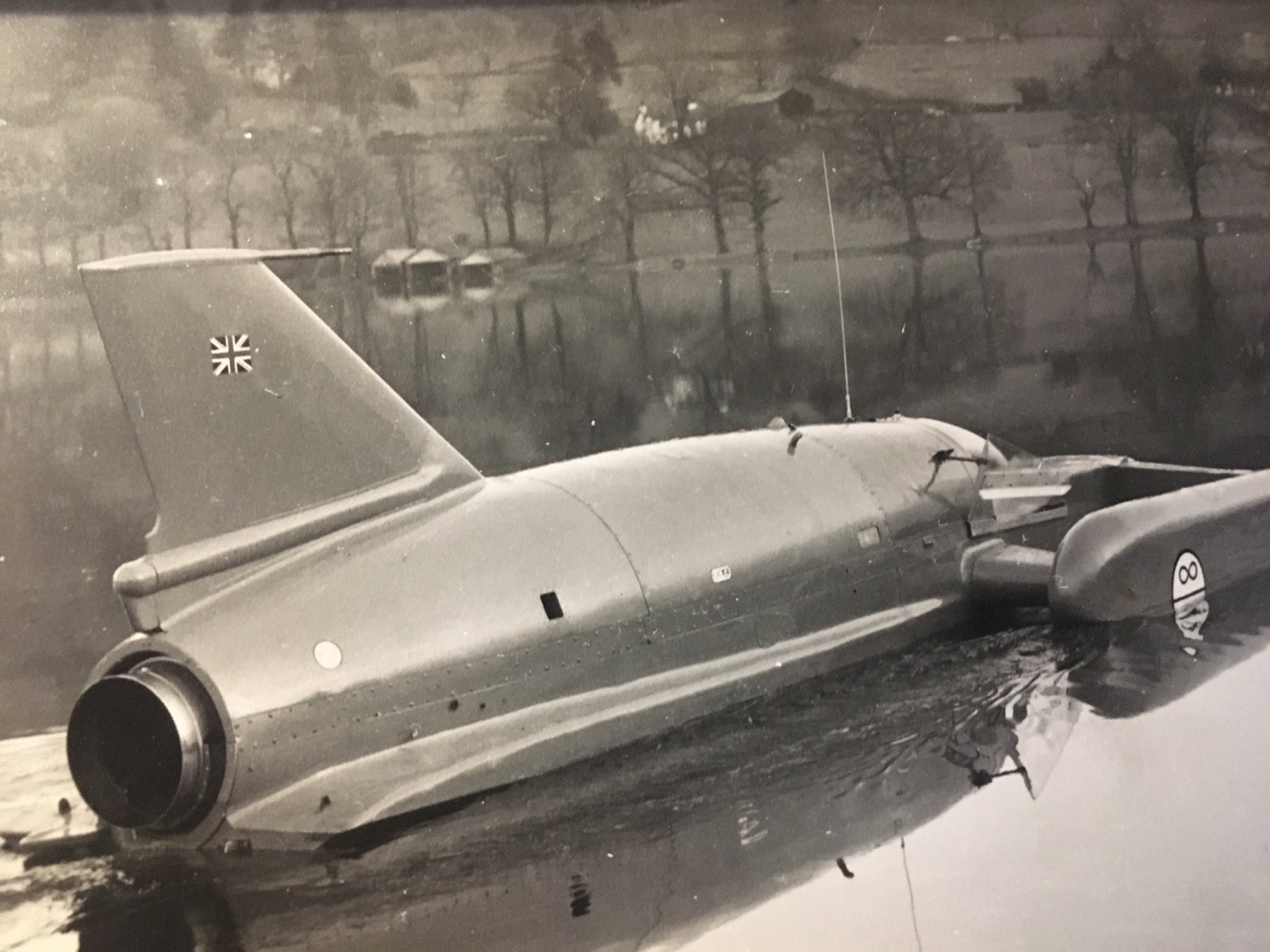
Bluebird courtesy of Paul Allonby
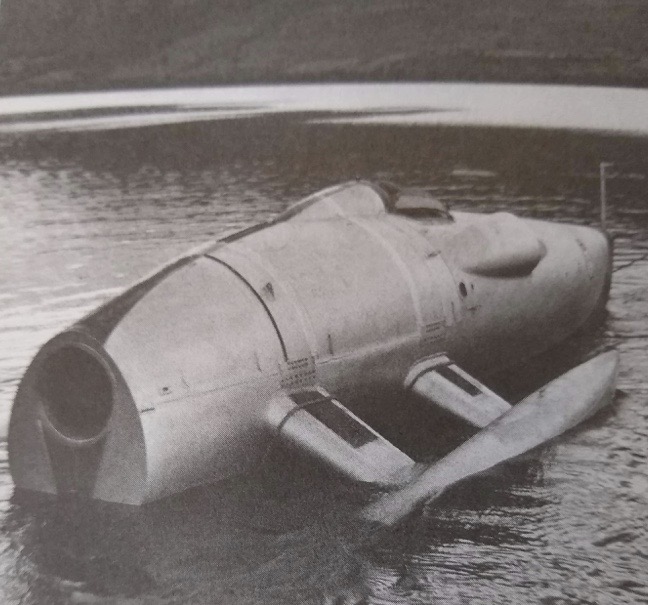
Crusader courtesy of Steve Holter
To a certain degree you can alter the distance between the bottom of the end of the jet pipe and the surrounding lake surface by shifting the weight about within the hull of the boat. However there is a limit with how much you can do this because you are also altering the balance of the boat when running at speed, which may in turn adversely alter her stability. That is to say making her more prone to taking off from the water altogether, or pitching down into the lake, neither of which would be a good day out, especially for the driver.
Also if you move the weight too far forwards in the hull to give a decent amount of freeboard distance, this might result in the attitude of the hull at rest being nose (or bow) down and therefore when the jet engines are powered up the craft just ploughing nose down into the lake surface, instead of rising up onto her three planing shoes.
You may imagine that engineers for a jet hydroplane would have no problem getting this freeboard distance spot on at their first attempt. However even with the iconic hydroplane Bluebird K7 designed by Chartered Engineers the Norris Brothers, they were unfortunately a mile out with the trim of the boat when first trialled in the Lake District. The front of the boat was awash with lake water running over it and the rear of the craft high out of the water.
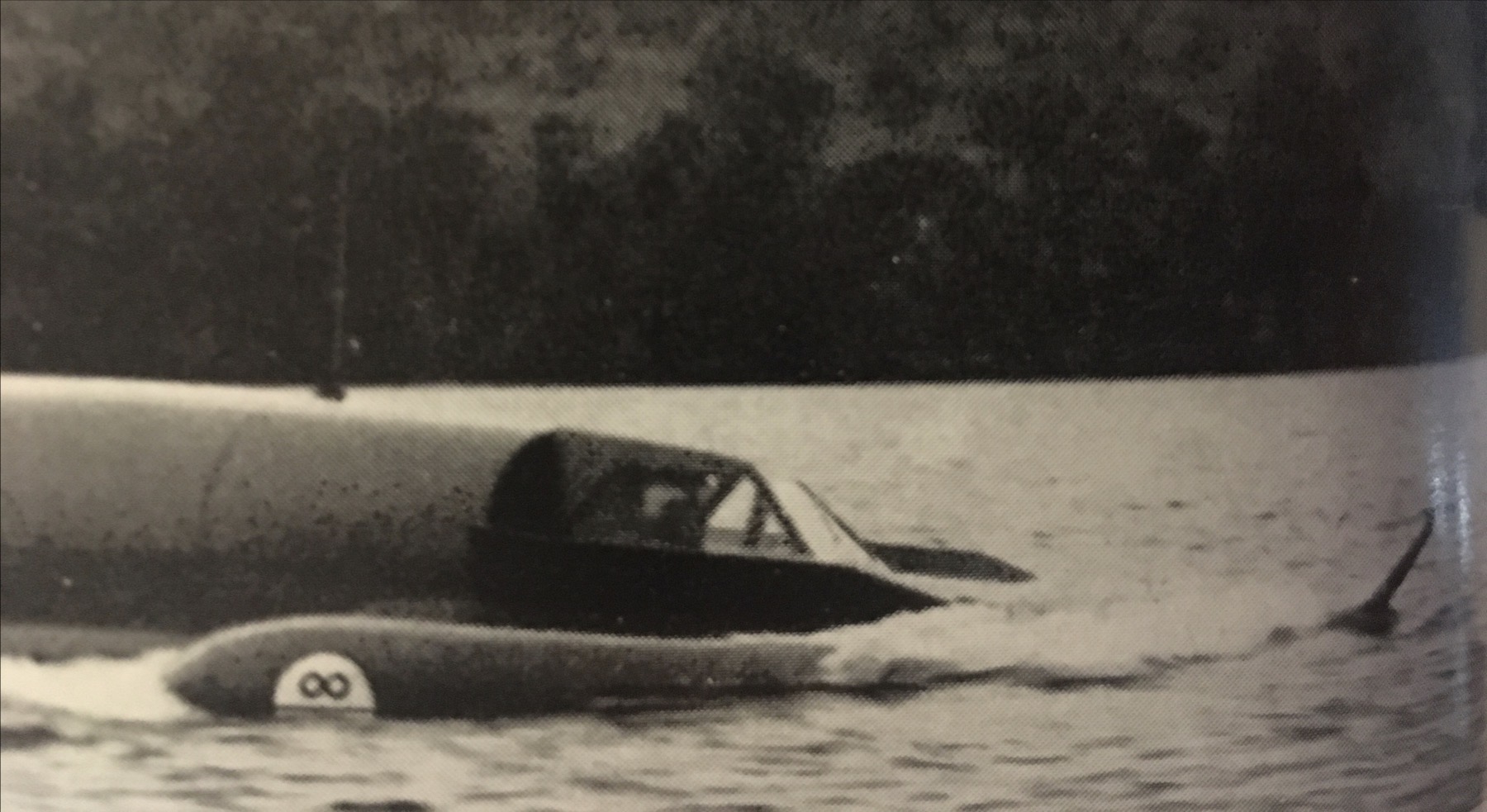
Indeed they were so far out with their calculations that they had to chop away a considerable amount of the rear sides along with rear of the hull and take one of the two spars located at the front of the boat out of the hull sides and lay it on top of the hull in order to just get her to work as intended.
Jet engines hoover up an awful lot of air per second and to perform at their best they want that air to flow directly at them so when you look at a jet engine on a test bed you will see the front of it having a bellmouth attachment, rather like the end of a trumpet. Again on an aircraft the jet engine intakes are unobstructed to take that air in as smoothly and directly as possible. In the case of Bluebird these major alterations to the design of the craft to get her static buoyancy / trim to an acceptable level and be able to rise up on her planing shoes with engine thrust applied meant that the airflow to the front of her jet engine was no longer a straight entry but had to pass over and down that raised front spar which was far from ideal given the disturbance to that airflow it then caused.
With all this in mind I thought it would be prudent to measure the amount of freeboard on Bluebird K7, the loose replica of that craft K777, the jet hydroplane Hustler that broke the world record after Bluebird and my good friend Dave Warby’s Spirit of Australia II in order to compare it to what I was proposing for Longbow. It is interesting because the twin Viper jet engines for Longbow are smaller than the Orpheus and J46 engine in the other jet hydroplanes I investigated so in one respect you might think the thrust line could be close to the water on Longbow than the other craft. However you also have to take into account the twin viper jet engines in Longbow add up to be heavier than a single Orpheus (but not as heavy as the J46 in Hustler). In the case of Hustler I had drawings of the hull and consequentially the freeboard distance and as for Bluebird I had drawings of the hull frame that I had done years ago when helping with the restoration of the craft and designing a rollover jig for it within the workshop.
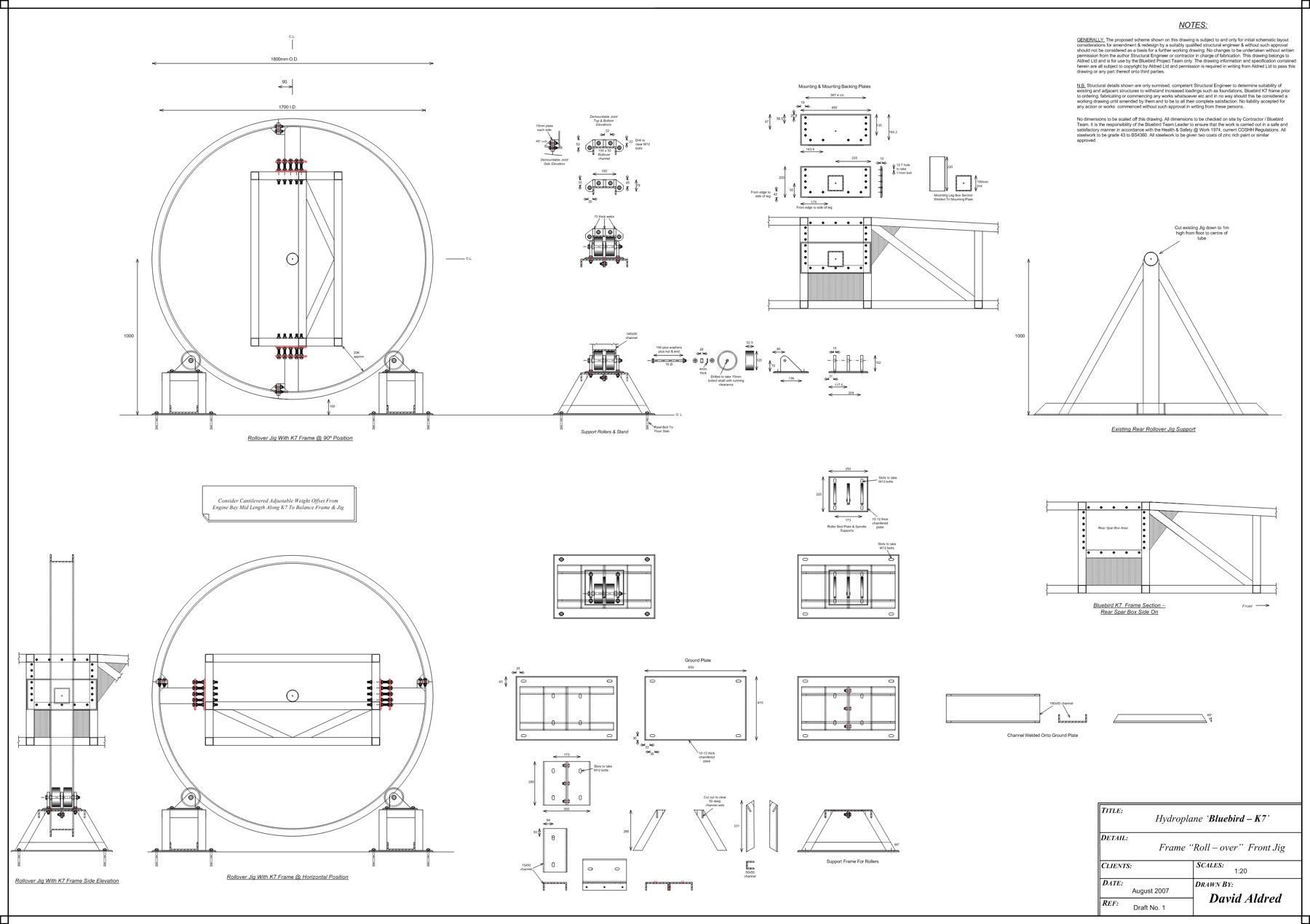

I then paid a visit just down the road to Lytham to see my good friend Charles Morris at Helical Technology to measure one of the Orpheus engines I had sold to him years ago when building the K777 there and it was good to have a catch up and nice that Charles offered to assist with some aspects of Longbow if I should need it.
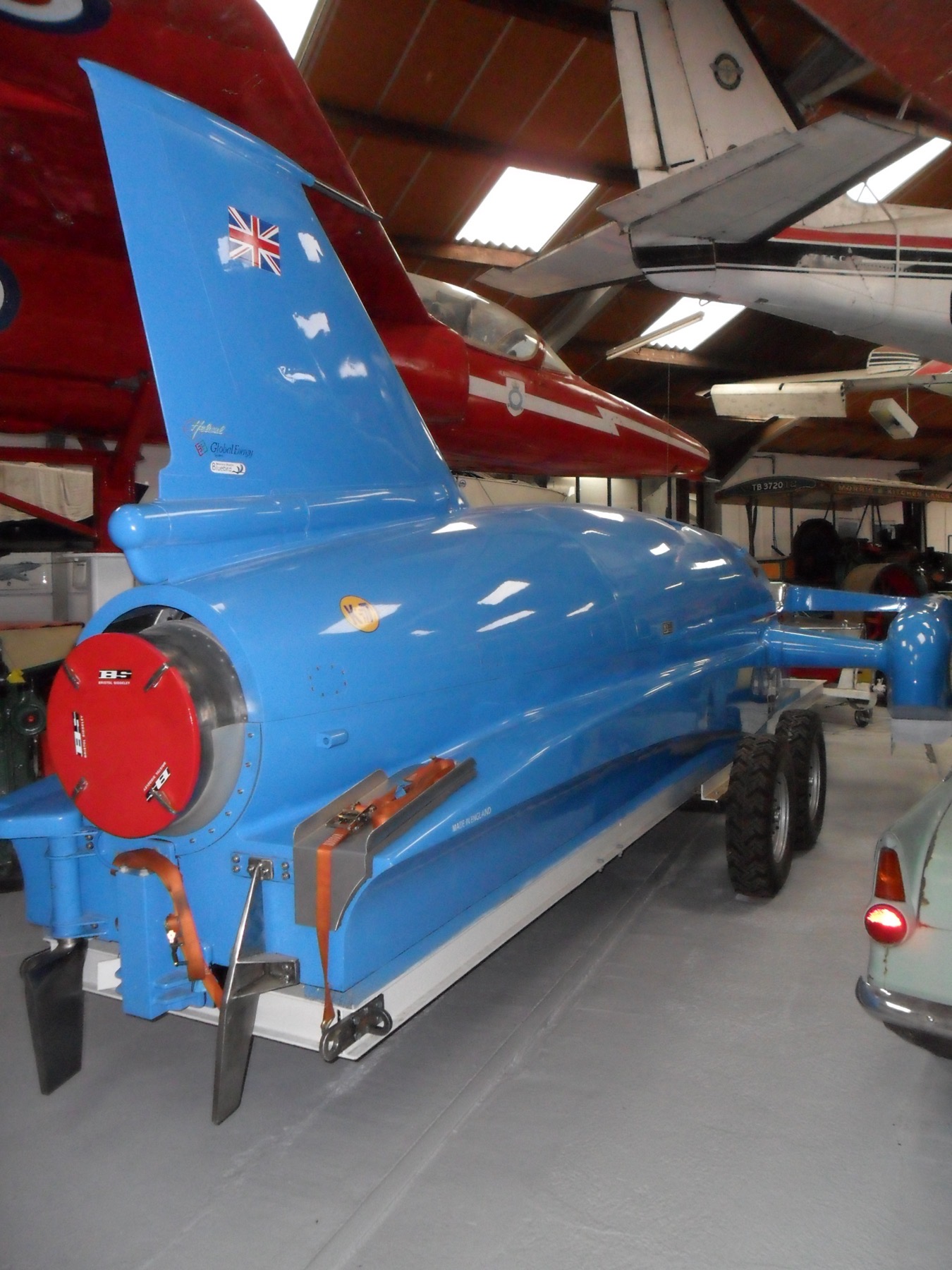
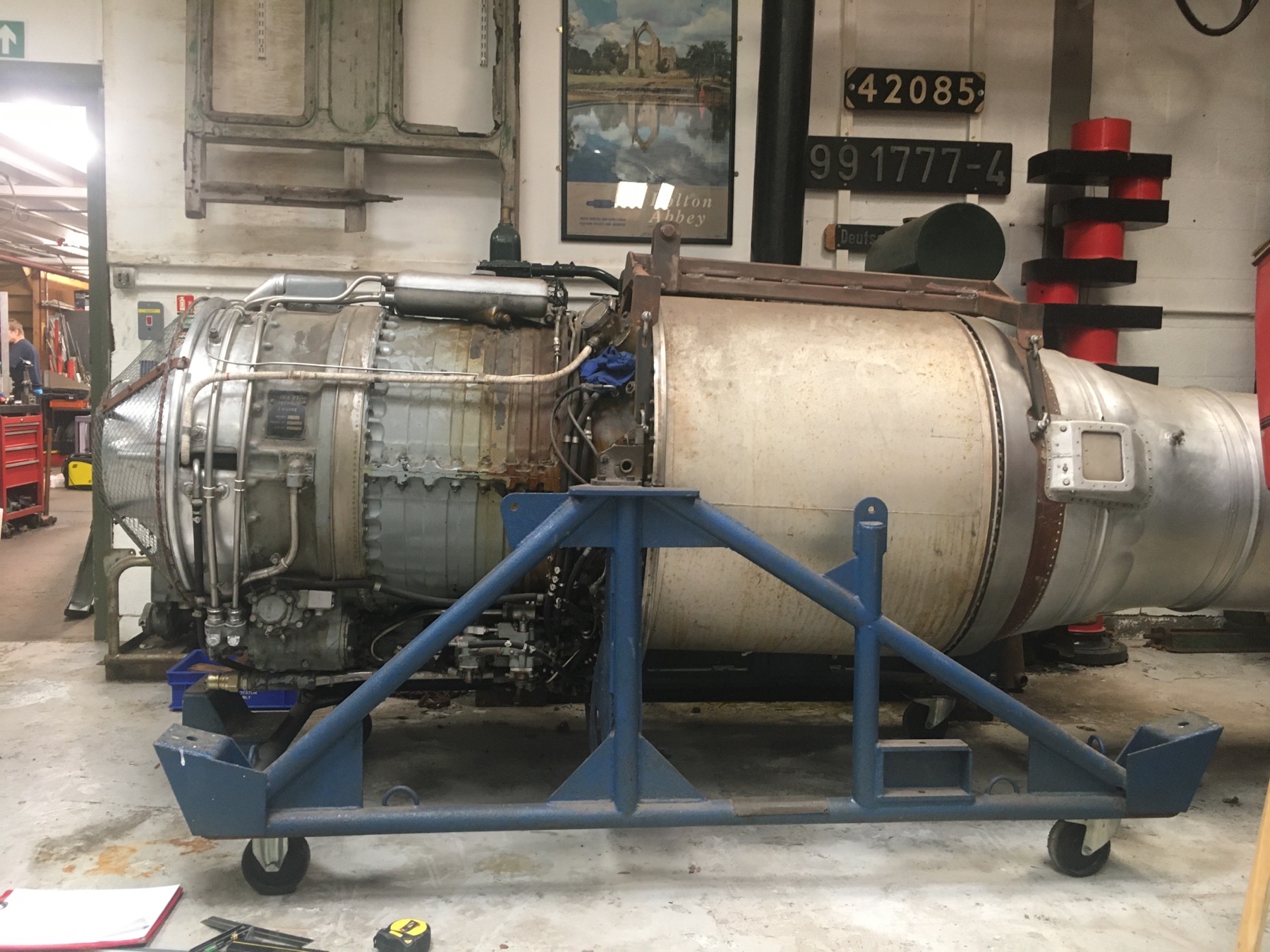
With the measurement of the Orpheus I could then put this into the hull drawing for K7 and compare that with the freeboard distance of K777, Hustler and also my good friend Dave Warby’s Spirit of Australia II. Of note Dave’s thrust line on SOAII appears from my calculations to be lower than K7’s but with greater freeboard distance reflecting the weight difference between the two craft which is excellent for Dave on both fronts.
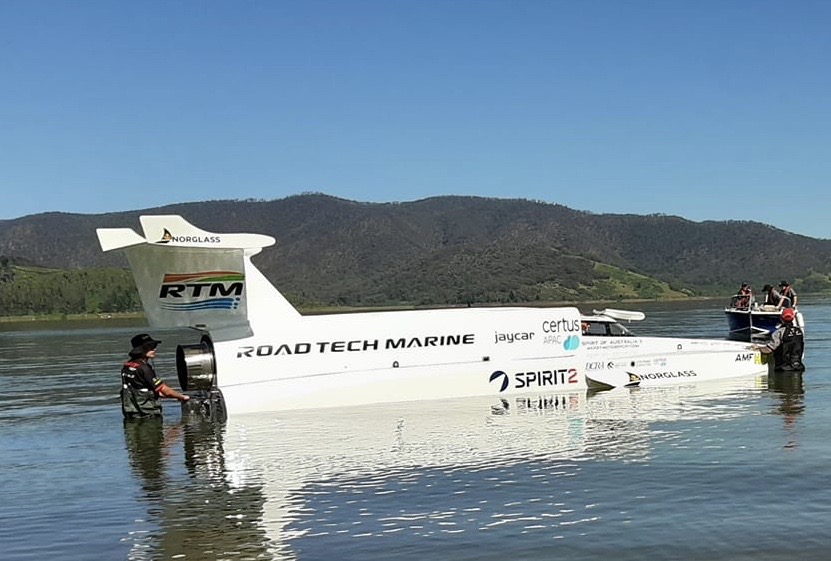
All of this is not an exact science by any means as there are so many variables that come into play between the five jet hydroplanes but it was a helpful exercise in comparative number crunching in relation to Longbow. However and as was readily apparent with Bluebird K7 I remain sceptical of the numbers until I see how Longbow sits (or sinks) in the water when the build is complete and the trials can begin. The aim really is to get the engines as low in the hull as we can at the outset as it is a lot easier to raise them up in the hull than it is to lower them.
On the build itself it was nice to get back into the workshop after what has felt like a very long lay off with helping my kids out with their new houses and then being ill with COVID. I am just starting to get my head around forming the upper framework and tops of the sponsons so more on that to follow next month.
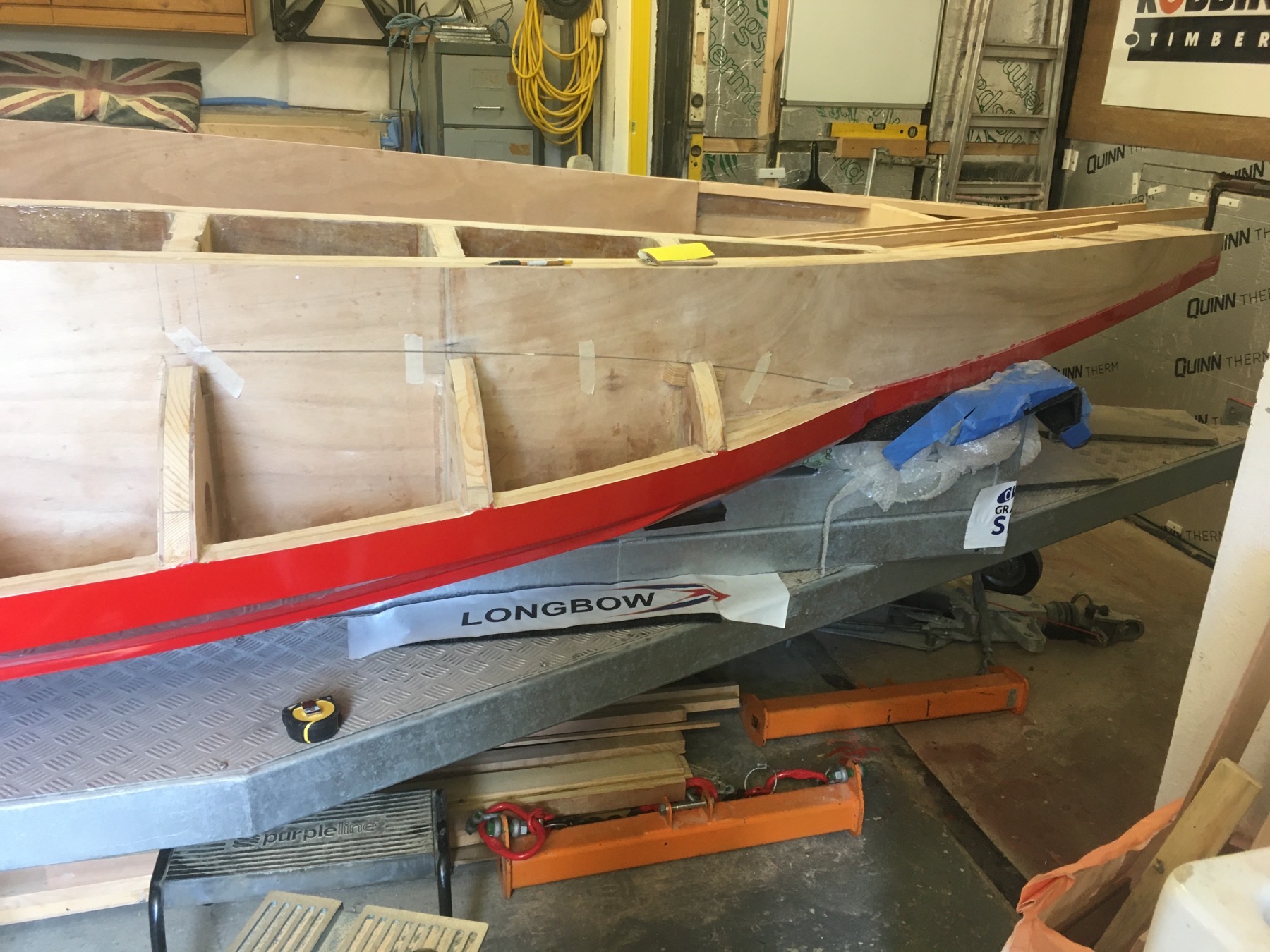
Sourcing and supply of the metalwork for the twin jet engine cradle for Longbow including the high grade BS4 T45 steel tubing is in the very capable hands of our metalwork sponsor Mark Sugden of John W. Laycock ( www.johnwlaycock.co.uk ) who you may recall supplied all the metalwork for our purpose built trailer.
When sponsors so very generously come on board with the project of building our jet hydroplane Longbow it is so nice that they are in return able to use the venture as a marketing platform for their own businesses and the following links are just some of the articles our sponsor Britlift who fabricated the purpose made engine lift have been able to benefit from:
https://britlift.com/britlift-backs-world-water-speed-record/
https://www.hoistmagazine.com/blog/britlift-backs-world-water-speed-record-attempt
https://www.cranestodaymagazine.com/news/britlift-backs-world-water-speed-record-attempt-9958070/
Going back to the trailer for Longbow this was welded by the apprentices of WEC at Darwen whose Managing Director owns an Aero L-39 Albatros fighter / trainer jet and an ex RAF Hawk T1 the same as the Red Arrows fly based at my local Blackpool Airport. It was therefore great to see the L39 feature this month at the Blackpool Air Show along with a Strikemaster powered by a single Viper engine (two of which will power Longbow), the RAF Eurofighter, Red Arrows and the Battle of Britain Memorial Flight amongst others.
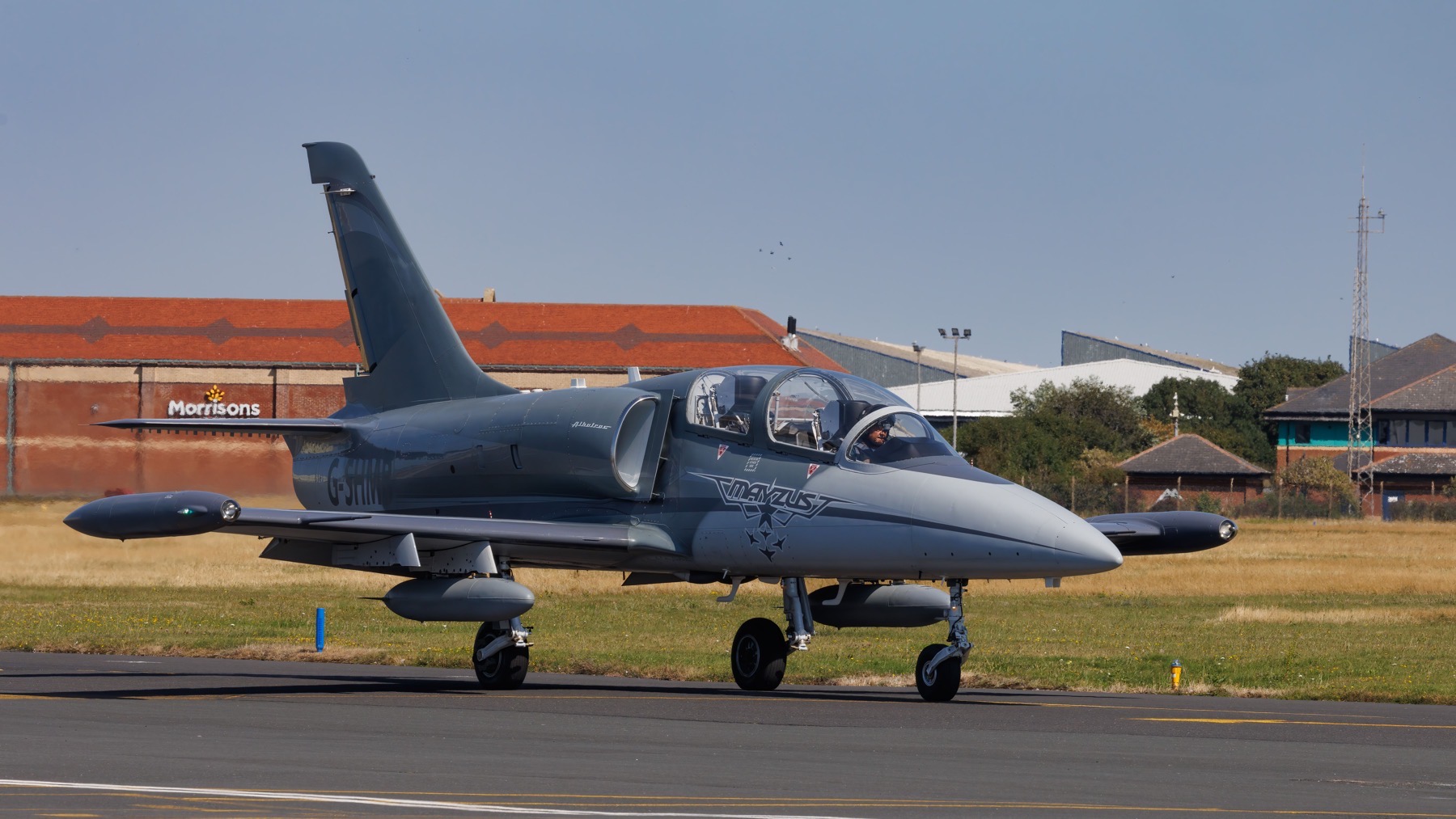
With kind permission of Neil Draper
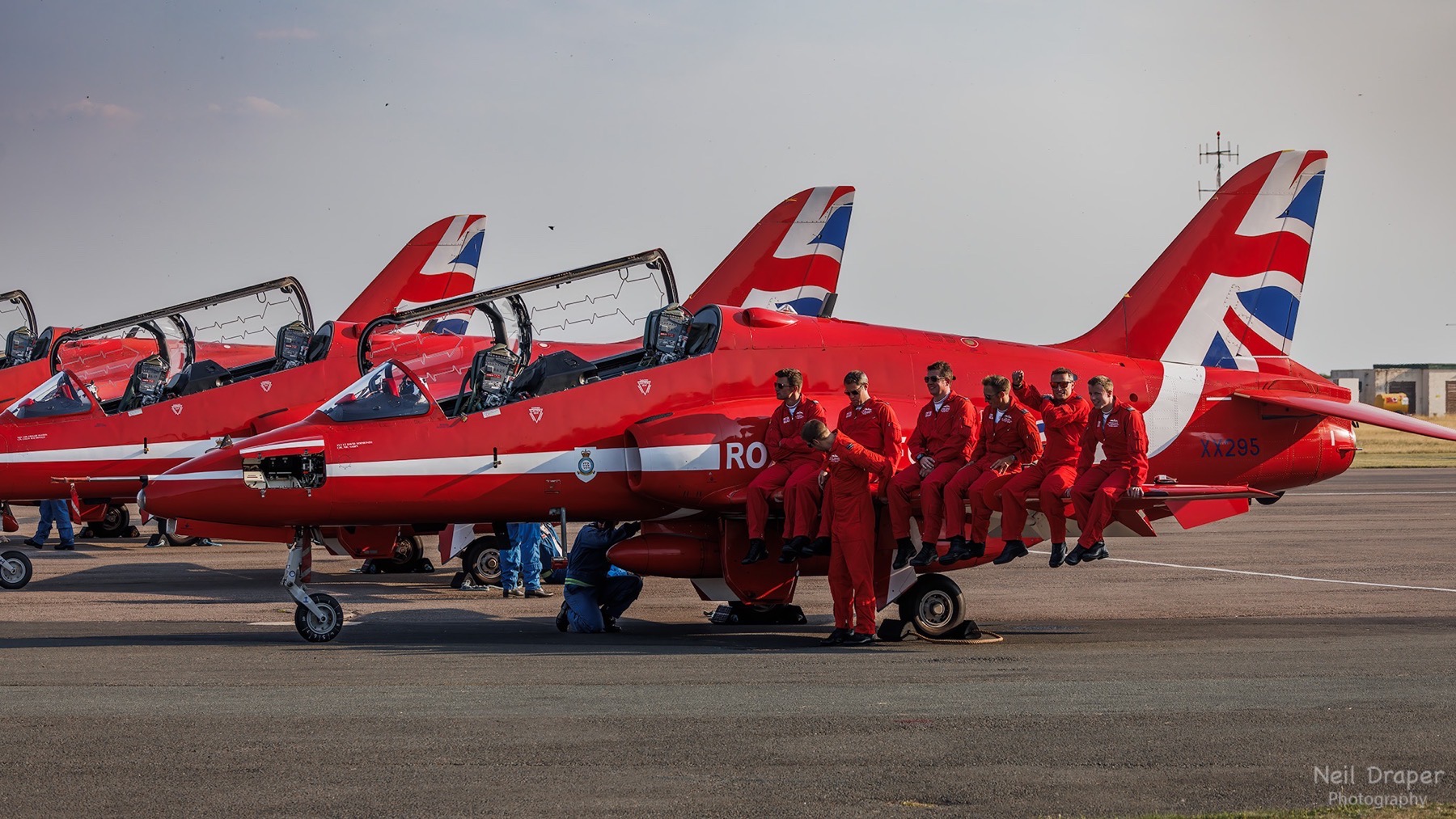
With kind permission of Neil Draper
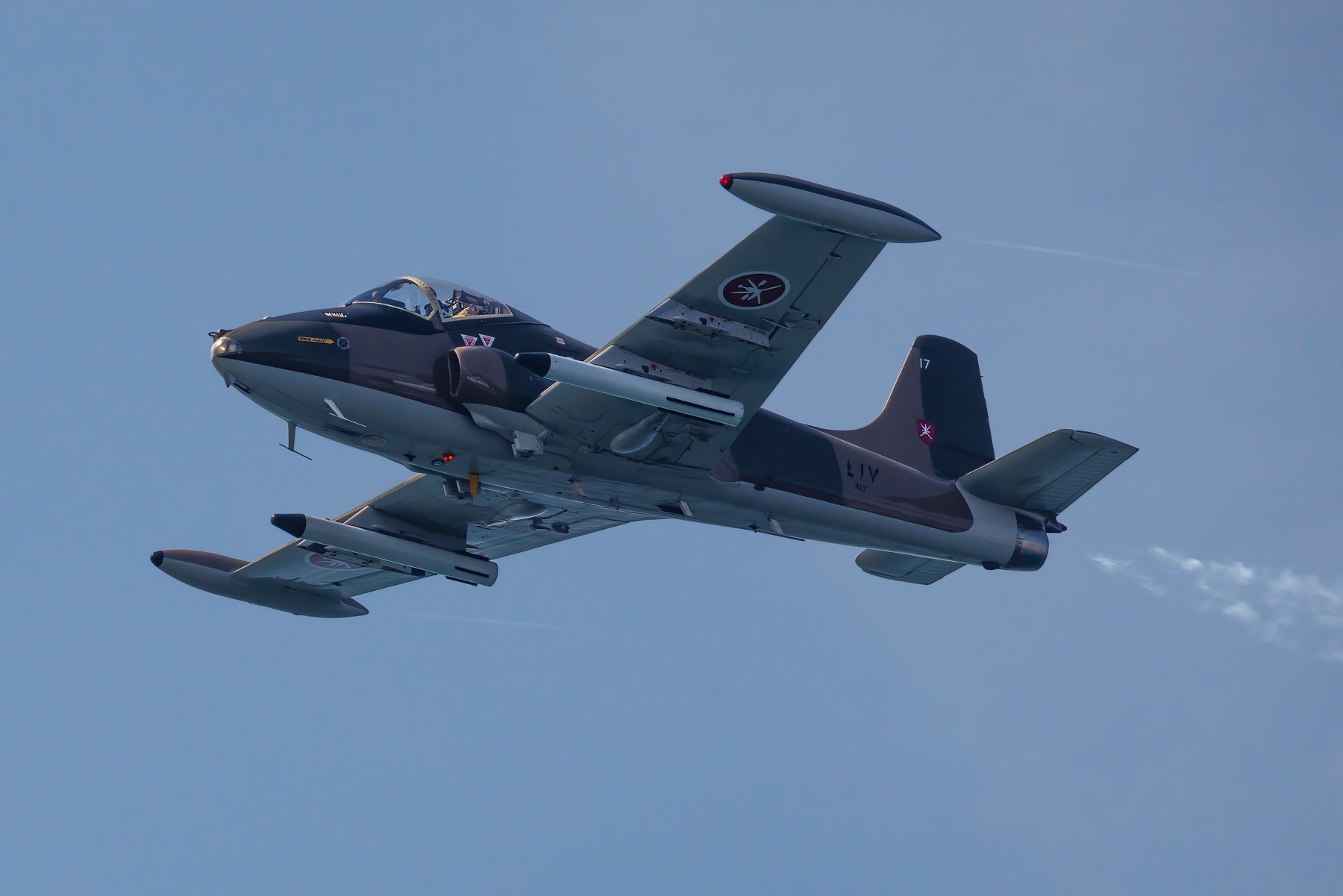
With kind permission of Neil Draper
Prior to Blackpool Airport being located at Squires Gate it was sited where the Zoo is now built adjacent to Stanley Park and some of the original aerodrome buildings are still there where it was the first Municipal Airport in the country.
On a final note our red Toy Poodle Ruby has just had a litter of gorgeous pups, three girls and a boy so if you would like one when they are ready to go then please let us know.
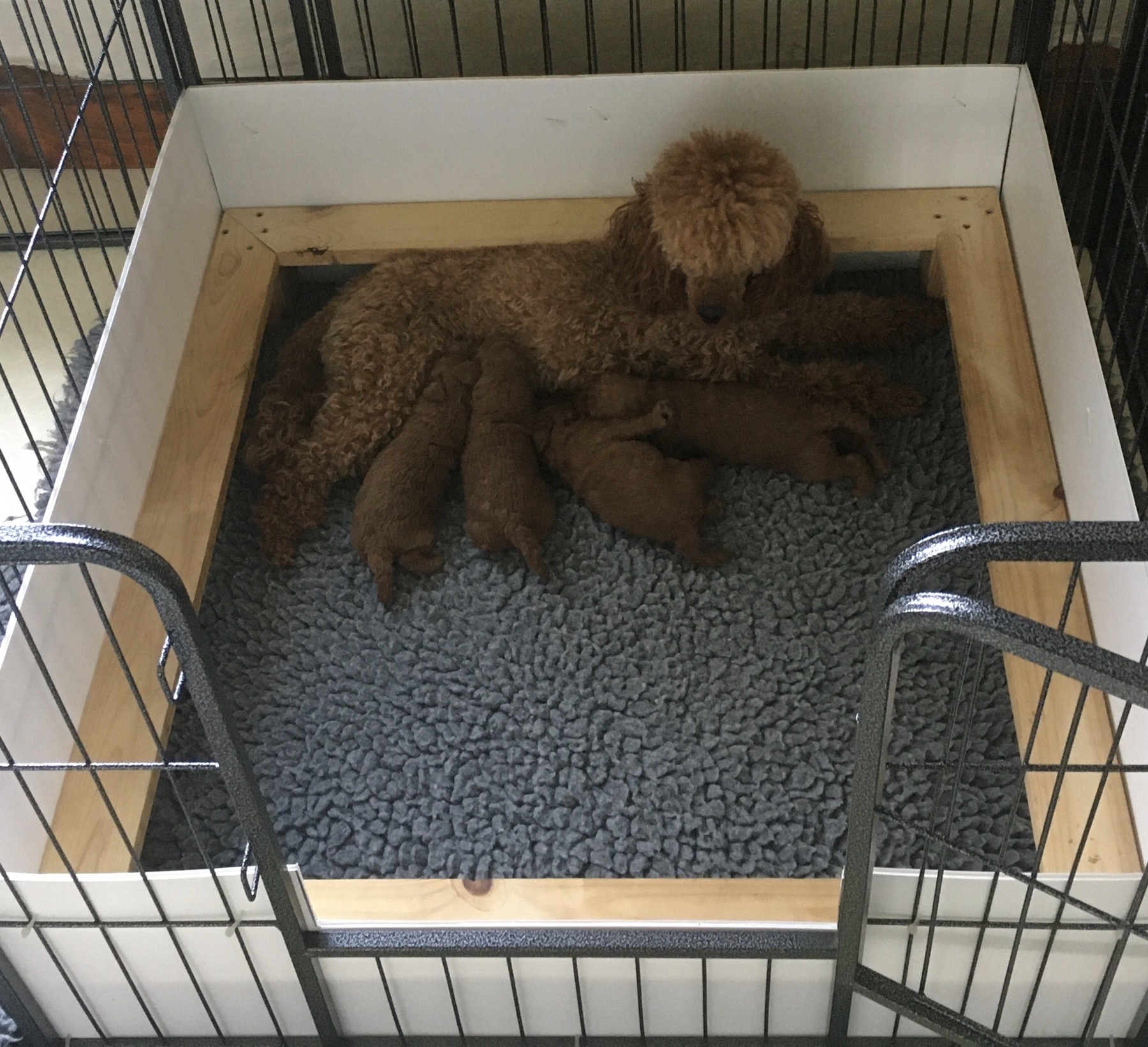
Well that is it for this month folks. Please drop by again at the end of September for the next instalment of our little venture of building and running our jet hydroplane Longbow and in the meantime if you have not done so already and are into social media, take a moment to like our Facebook page.