Merry Christmas to everyone and thank you for tuning in to our monthly update during the festivities. To begin with Dave Warby reports back as follows from latest testing of his jet hydroplane Spirit of Australia II at Blowering Dam in Australia at the beginning of December:
“After the last series of testing the cockpit had been modified with the seat lowered a couple of inches, new steering shaft, steering wheel an inch wider diameter and revised radio for communication.
Great news is that the Royal Australian Navy Fleet Air Arm 808 Squadron have now joined Warby Motorsport to assist with our venture of breaking the Outright World Water Speed Record.
We had permission for exclusive use of the Dam over the weekend so trying a new rudder on the Saturday for this series of testing (which had only just been manufactured for the boat the day before), I found the boat veering to the right as a result of this rudder’s alignment proving to be slightly out.
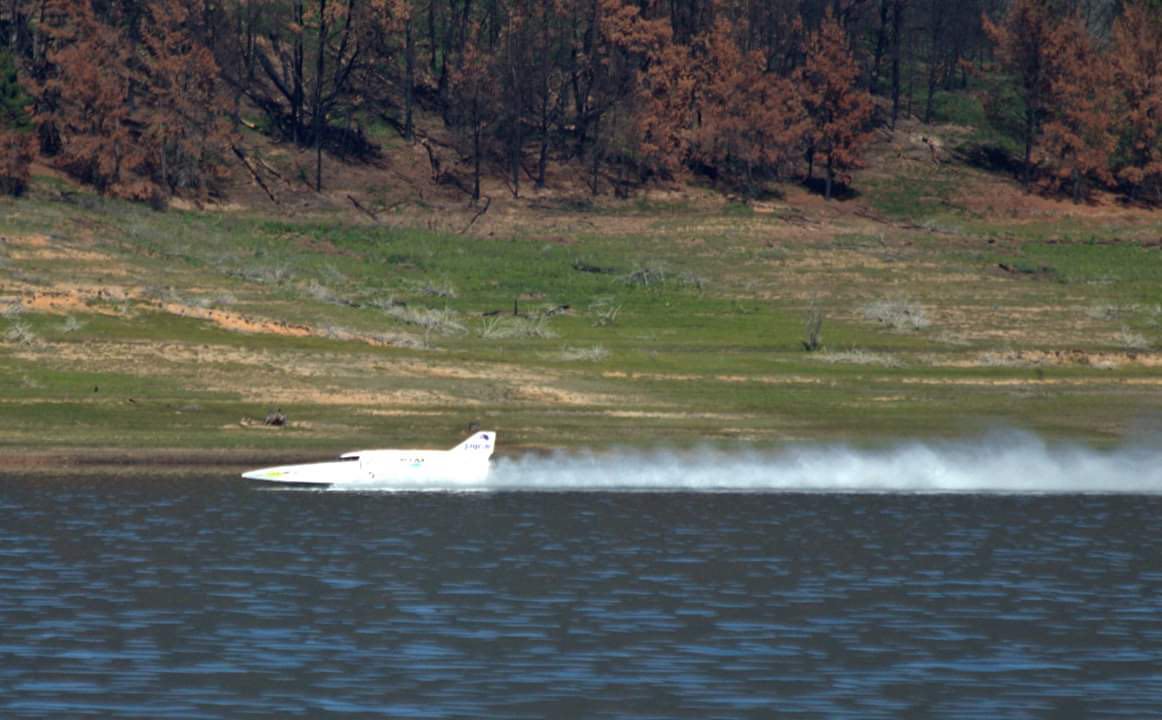
My dad (Ed. current Outright World Water Speed Record holder Ken Warby MBE) and myself then made some adjustments to the rudder in the workshop and it ran much better second time out but still not quite right.
After making further adjustments we put the boat back in the water but this time the Orpheus jet engine was slow to spool up with the electric starter motor and as a result we suffered a ‘hot start’ and recognising this for what it was straight away, I shut the engine down to prevent damaging it.
For those of you who are not familiar with the term ‘hot start’ it refers to a situation where upon starting the turbojet and the fuel being ignited, there is insufficient air being sucked through the engine to keep the temperature of its components under the manufacturer’s limits.
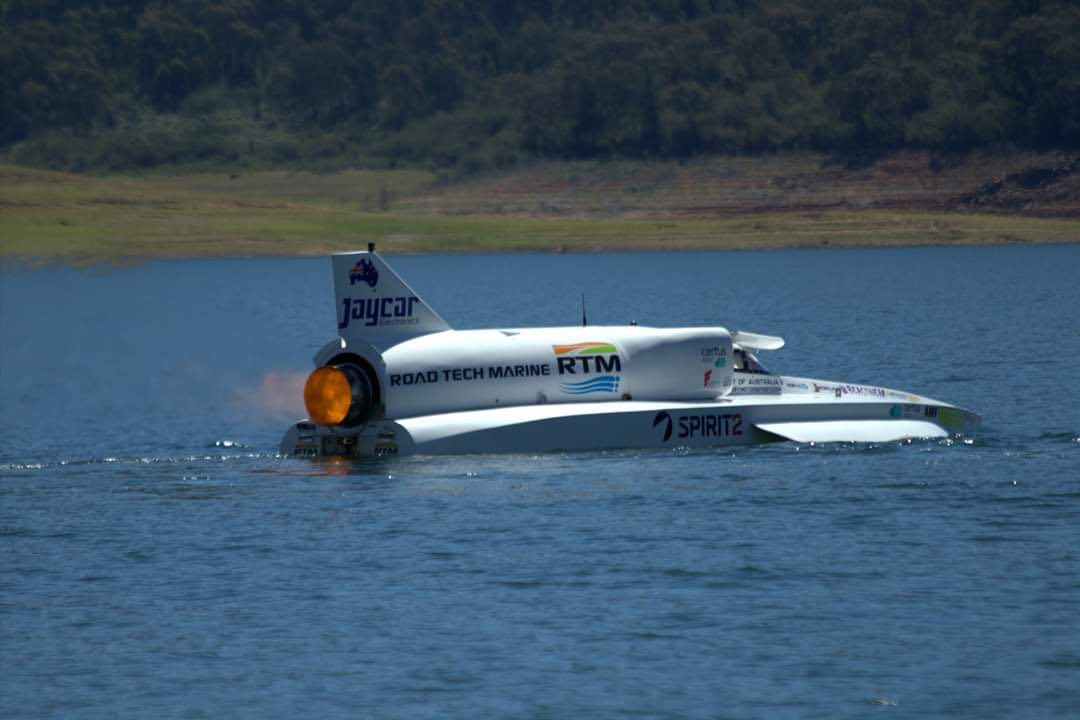
That night the team working until 1am replacing the electric starter motor with a spare second hand unit that we had brought along; only to find this other starter motor had dropped a segment and could not spool the jet engine up quick enough so there was no point in risking another hot start.
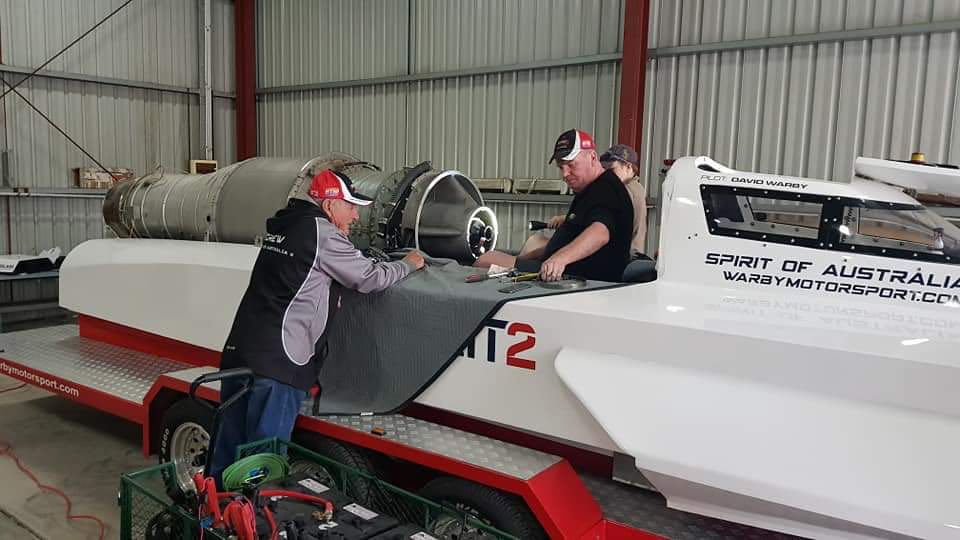
Sunday morning a storm blew in with thunder and lightning along with high winds which meant we could not run even if we had sourced another starter motor. The Team, our support divers, emergency services and rescue boats all stood down.
Just when we were feeling rather dejected one of our sponsors ceo of RTM and Jaycar who had flown down from Sydney to watch us and seen our struggle first hand, offered to buy us two new starter motors and increase their financial support to us. You will appreciate that the Team, dad and myself were overjoyed at this news as it will allow us to go forward with our next round of testing.
On the Monday on the way back with the boat we called in at HMS Albatross to meet up with the rest of the 808 Squadron and cannot thank them enough for coming on board with our venture.
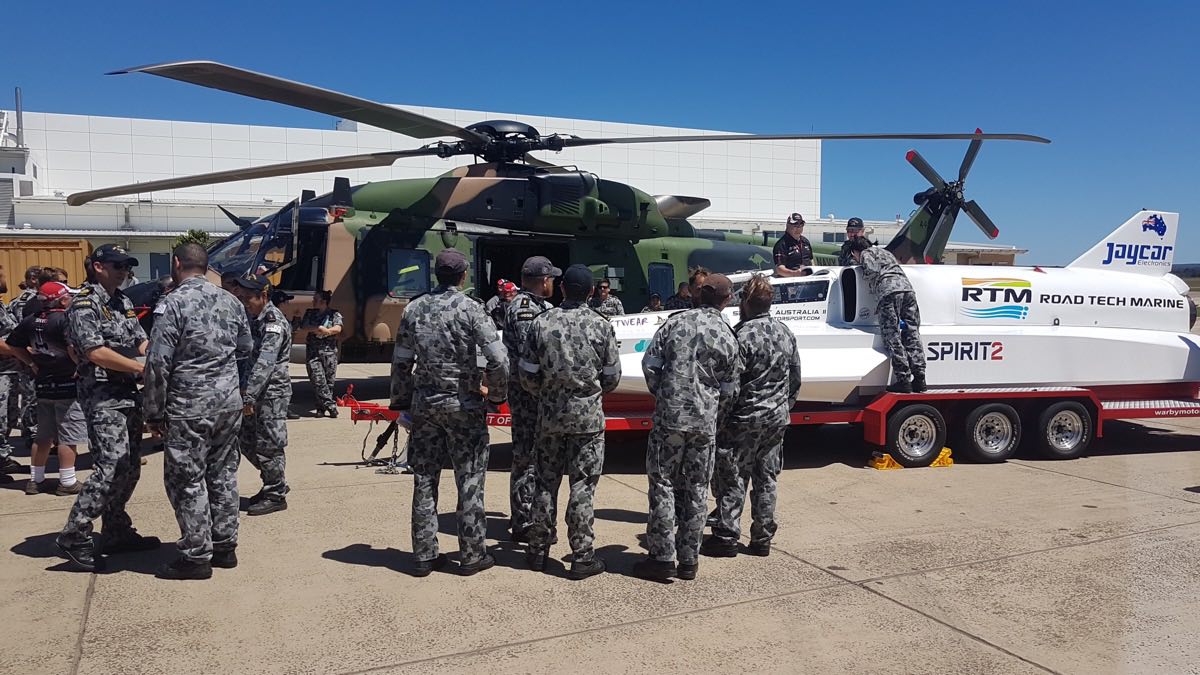
On returning to our base we will pull the engine out to check for any damage to both it and the hull with the intention to test local to us in Taree, NSW early February and then return back to Blowering Dam in March. We stay away from the Dam in what is for us now summer, to let the local boat users have their enjoyment of the facility.”
We will report back on Dave’s further testing and progress in the New Year and wish him and his team every success for 2019.
Back with our own venture the driver for our jet hydroplane Longbow, serving military pilot David-John Gibbs (DJ), has written the following section for some of our readers, especially those within schools, who are new to the venture and have asked why we are using a pair of Viper jet engines within the boat. Some of this is repeated and expanded upon in more detail within our October 2017 diary entry written before we started building the boat but hope you will find the following helpful as a more brief and light hearted explanation:
‘Speed is a need but thrust is a must’.
You would be forgiven for thinking that I had just pulled the above phrase out of a Christmas cracker but it serves as an introduction as to why we decided to use twin Viper jet engines for Longbow. So if thrust is a must why not just use the much larger and more powerful Avon, or even an Olympus engine as used in Concorde? There are a number of considerations to be taken into account when selecting an engine, so in no particular order:
Thrust. This one is easy. More thrust = more speed. Actually it isn’t a straightforward, linear relationship. In simple terms to double the speed you need 4 times the thrust.
Size, weight and rotating mass. Let us take the extreme example of using a jet engine out of the retired supersonic passenger aircraft Concorde that you might see when visiting an aircraft museum. Certainly ample thrust available here at a rated 38,000lbs dry (i.e. without reheat – see later comments on this), however this engine is physically massive – Over 4m long, 1.2m diameter and weighing over 3 tonnes. A hull that could accommodate an engine of this size and weight and also remain buoyant would be similarly massive, and therefore entirely impractical. Not only that but you have to consider that within the relatively narrow beam hull of a delicately balanced jet hydroplane, large diameter engines have a considerable amount of rotational mass that would cause us headaches with stability as that engine accelerates and decelerates. So whilst thrust is a must, size really does matter.
Location within the hull. Some gas turbines have afterburners (often called reheat) to increase their performance and where that afterburner is an integral part of the engine itself such as the Tornado aircraft’s RB199 engine, or the Eurofighter aircraft’s EJ200 engine, there is no jet pipe downstream of that reheat module due to the very high temperatures associated with afterburning. An example of the RB199 engine is shown below when we went to look at some being released by the Ministry of Defence:
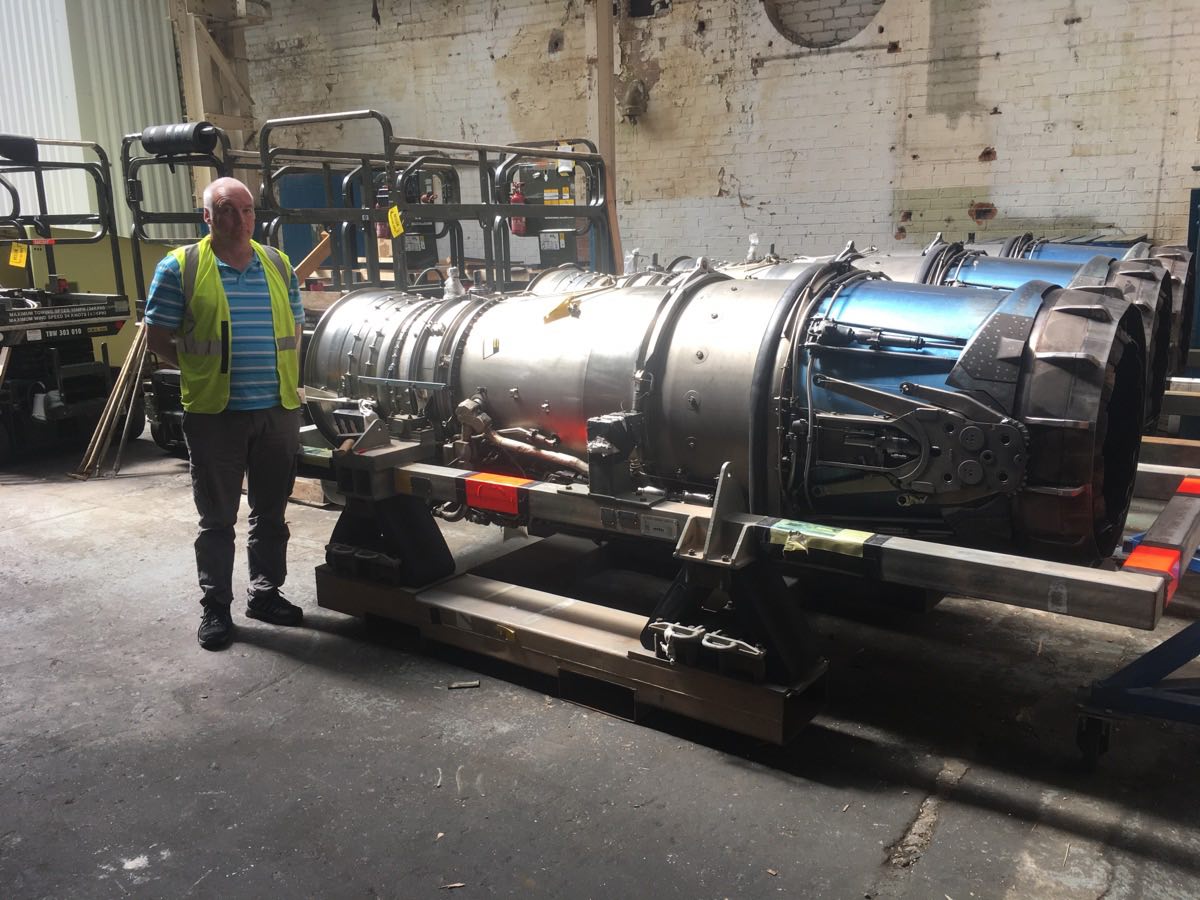
This inherently means that these types of engine are located at the rear of the aircraft. For our application however of using a jet engine in a boat, we need the engine as far forward in the hull as we can get it otherwise with all that weight at the back, unless it were countered by adding weight up front, rather like a seesaw, the jet hydroplane would be far more likely to lift up off the water at the bow as it ran at speed and consequentially blow over.
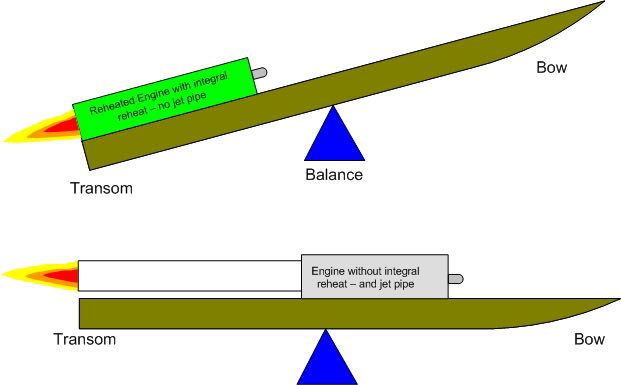
If you add weight up front to counter the issue, you need a bigger hull to carry that extra weight and then you get into a case of diminishing returns for that more powerful engine.
Ease of operation. On paper a powerful RB199 jet engine from the Tornado military aircraft looks like a good prospect however you only need to scratch the surface to see that is an extremely complex engine to operate. If you open a gas turbine throttle too quickly a number of undesirable things can happen: the temperature limit for the turbine can be exceeded, the delicate balance of pressure, temperature and airflow within the engine can break down causing the compressor blades to aerodynamically stall and hot gases to be spat out of the intake (This is known as surge, and is usually quite damaging), or the flame can simply blow out.
Early gas turbine engines overcame this with a large operating margin away from surge and temperature limit conditions, at the expense of output and efficiency. Slightly more modern engines used mechanical governing devices that schedule the correct fuel supply to the engine burners based upon the speed the engine is rotating (revolutions per minute or RPM) but modern, highly efficient engines such as the RB199 use electronics by way of a digital engine control unit (DECU) to operate the fuel valve.
This DECU housed separately within the aircraft calculates the optimum fuel flow based on RPM, temperature, pressure and pilot demand and itself receives instructions from further electronic controls within the cockpit including a potentiometer throttle. Whilst all of this allows a much more precise throttle response – ideal for a jet fighter – it adds a whole new level of electronic complexity and cost. To get an RB199 engine operating properly within our jet hydroplane would be an immense technological challenge and the cost of the necessary additional components to get that engine to run safely within the craft would far exceed the purchase price of the basic engine itself. Which brings us nicely on to…
Cost. With an unlimited budget we could make a case to purchase any engine we wanted, with a full spares and support package. Unfortunately pockets that deep only belong to the Government and the airlines, so our choice is somewhat constrained.
Availability. Dismissing the cost element for the moment, the above could almost form the basis of a wish-list. Unfortunately getting a jet engine isn’t just a case of writing to Lapland and seeing what arrives on Christmas morning; There is only a very limited range of serviceable engines on the market. Buying an engine from a museum or a scrap man isn’t sensible. The engine may be incomplete, internally damaged or otherwise turn out to be just a very expensive, non-working ornament.
The supply of engines is a very fluid thing. Wait for ages and an Adour engine from a Hawk aircraft may turn up. This would be our ideal engine, however currently there simply aren’t any available to us. This left us with only one realistic choice to buy and use within the UK – The Viper.
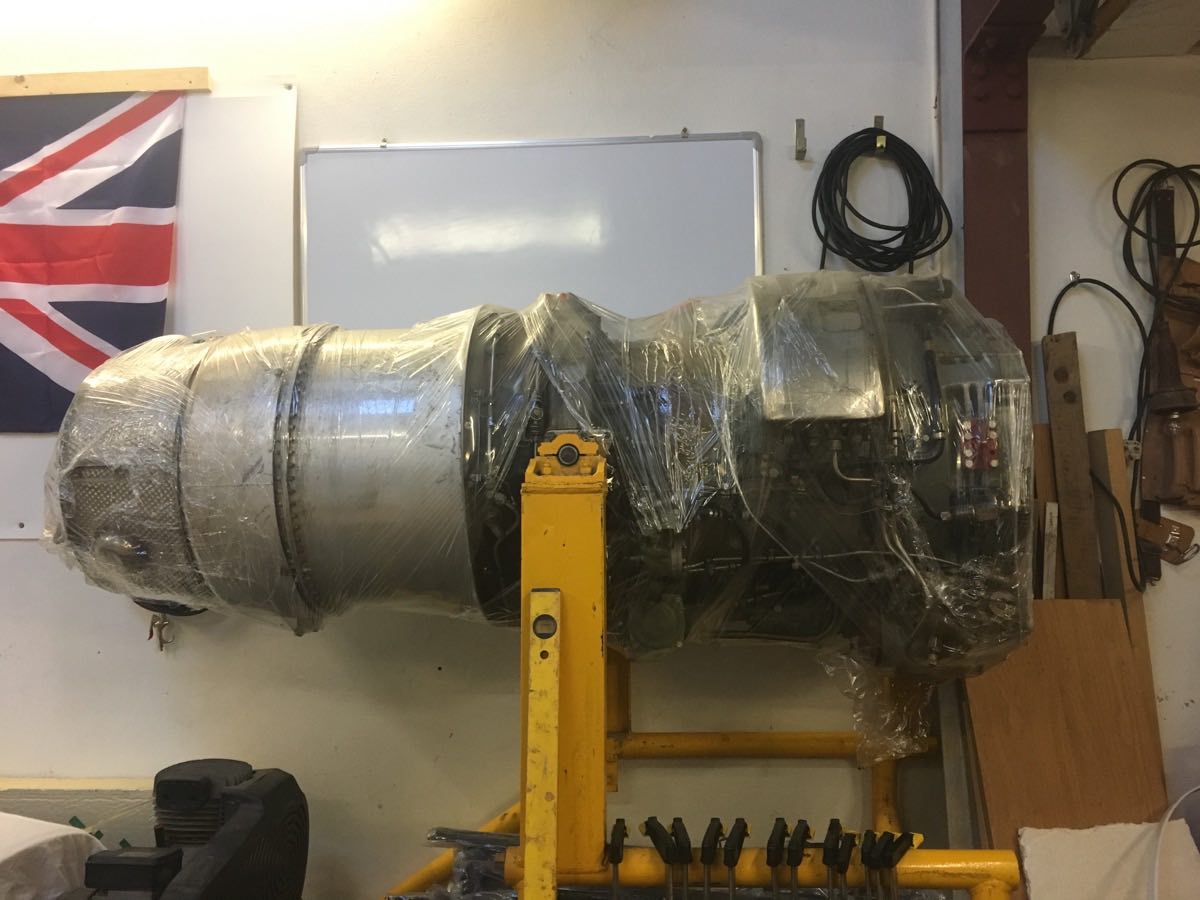
It is simple to operate with its mechanical fuel control system and electric start, is affordable and spares are available. Unfortunately a single Viper is only equal to the maximum thrust of the existing Outright World Water Speed Record craft and obviously we need a format which exceeds that, given we have also said ‘thrust is a must’.
Whilst using a single, larger engine has some advantages, using twin Vipers provides the necessary thrust in a British package that is available, easy to operate, can be brought well forward in the hull to provide good balance and for our limited means is affordable. The further advantage of the Viper is that spare parts, and even spare engines are available. This last consideration is very important to prevent the project grinding to a halt due to engine issues that cannot be resolved.
Thanking DJ for the above and returning to the ongoing build of Longbow’s hull, the next task for Fred, Steve, Keith and myself, after setting the vertical timber frames that separate the main timber bearers from the sides of the hull, was to laminate the individual frames and vertical sections using the West System epoxy in order to provide additional strength and bonding. For those reading our diary for the first time please note that at this stage the hull is being built upside down:
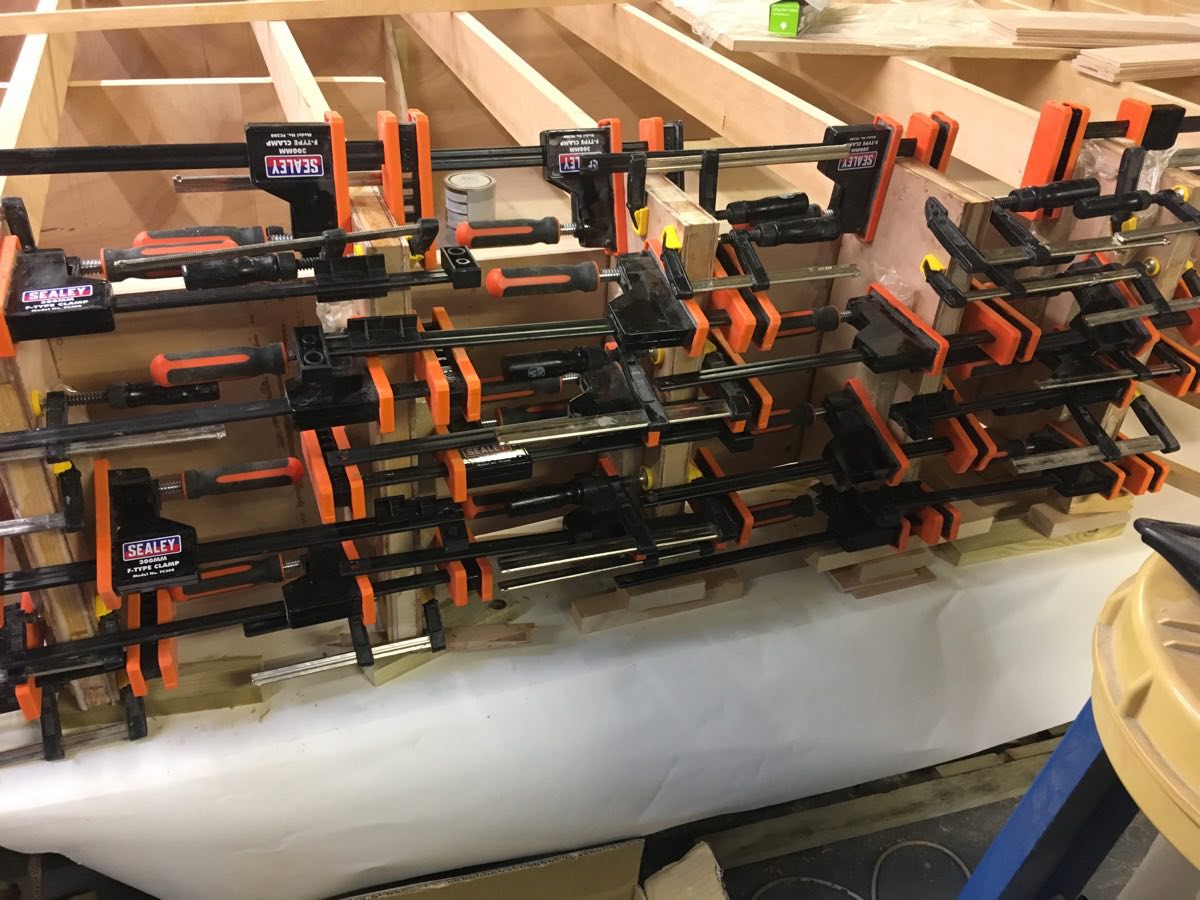
You can never have enough clamps with this build:
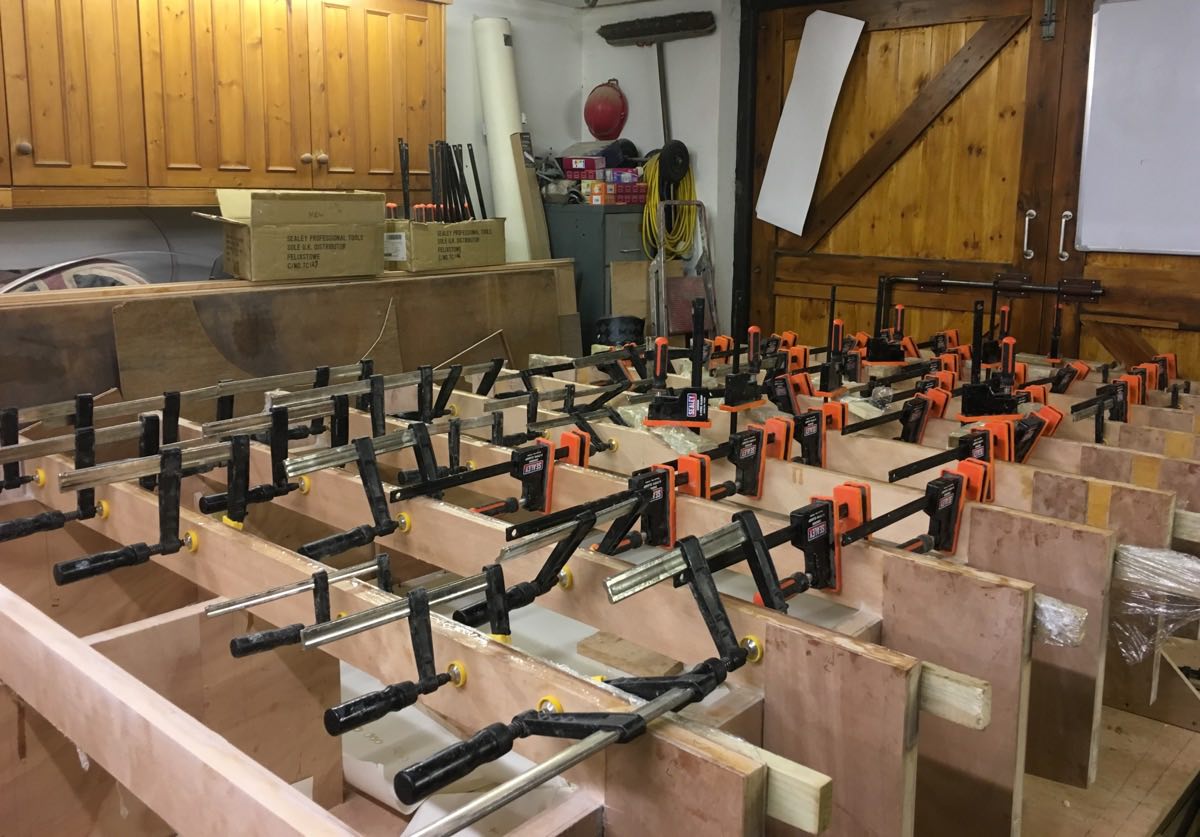
Given the considerable number of individual frames this series of laminations took a lot longer to actually do than it took to write herein but we got there in the end:
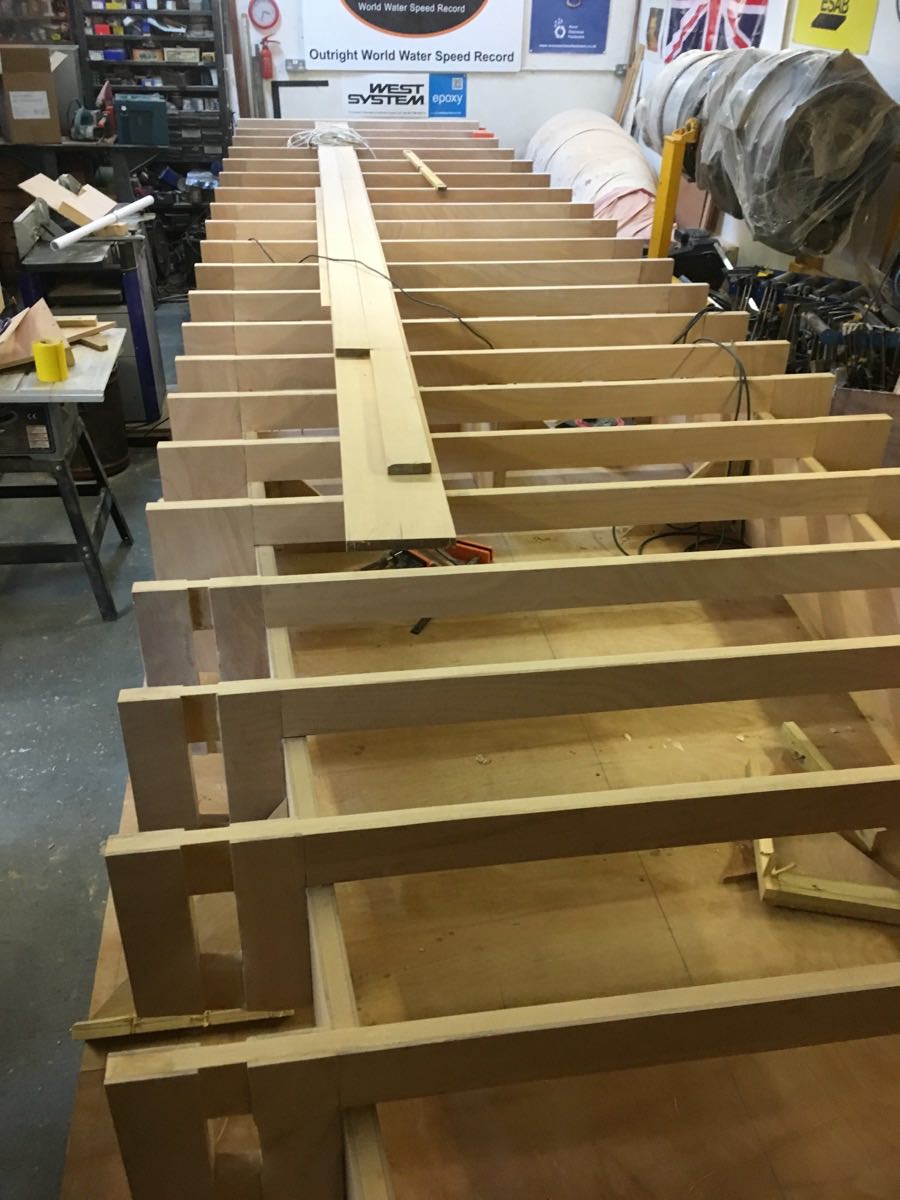
Next month we will show you setting out the keel of the hull to Longbow but in the meantime spare a thought for our composite design engineer Paul Martin who is working with his Finite Element Analysis (FEA) computer model of the driver capsule for Longbow and having to adjust 24,000 elements of this model by hand! Paul clearly has the patience of a Saint and along with Neil Morton, our website guru from Progress Concepts, we would be lost without you guys and cannot thank you enough for coming on board with the Project.
As we close for this update we wish you a very successful and Happy New Year from the Longbow Team. Please spread the word of this exciting venture of our jet hydroplane being built on the Fylde Coast, Lancashire, UK and see you next month for our next instalment.