An early update for December folks as Neil of Progress Concepts, who very kindly manages our website for this little venture, quite rightly wanted to clear his desk of tasks before settling down with his family for the seasonal festivities.
Our driver for Longbow, the jet hydroplane that we are building, is Flt Lt David-John Gibbs (DJ) of the RAF and for those who have not had the pleasure of meeting DJ, here is a little video (one of three if you do an associated search) as he explains about the Grob 115E Tutor aircraft of the RAF, with which as part of his military service, he performs aerobatic displays at airshows around the U.K.
Here also are a couple of photos of DJ in action performing a different aerobatic display, this time not with a propeller driven aircraft but the BAC Jet Provost that has a top speed of 440mph as he puts it through its paces.
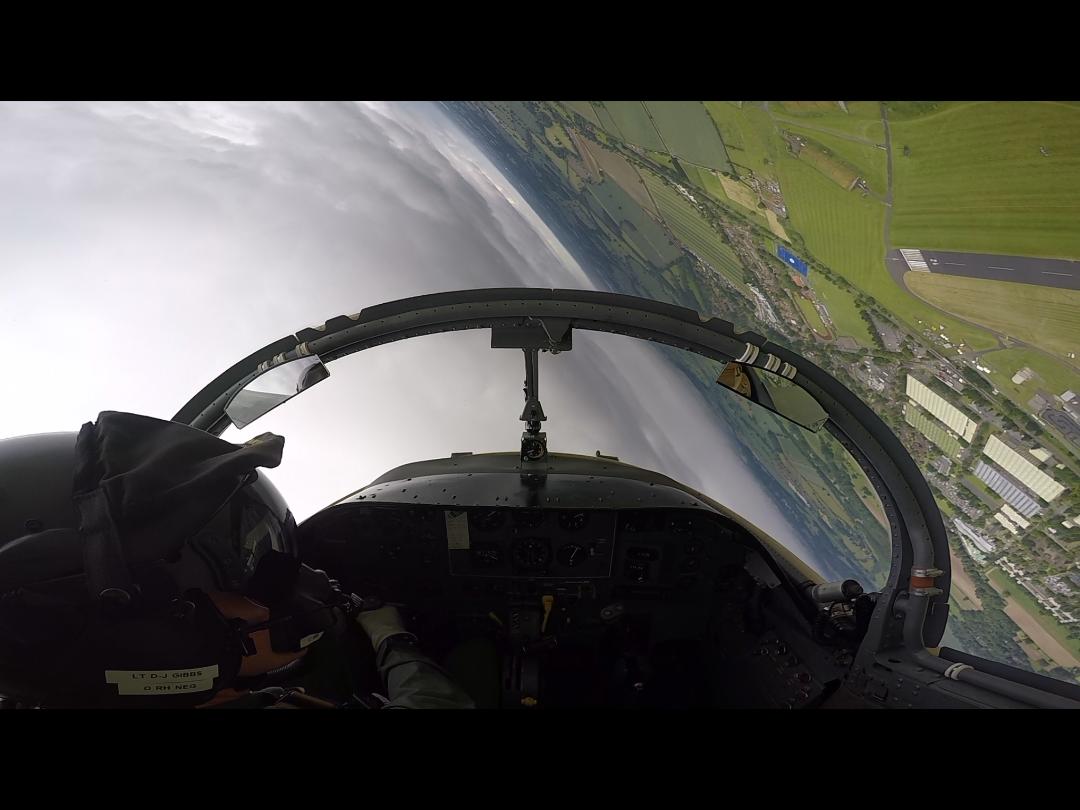
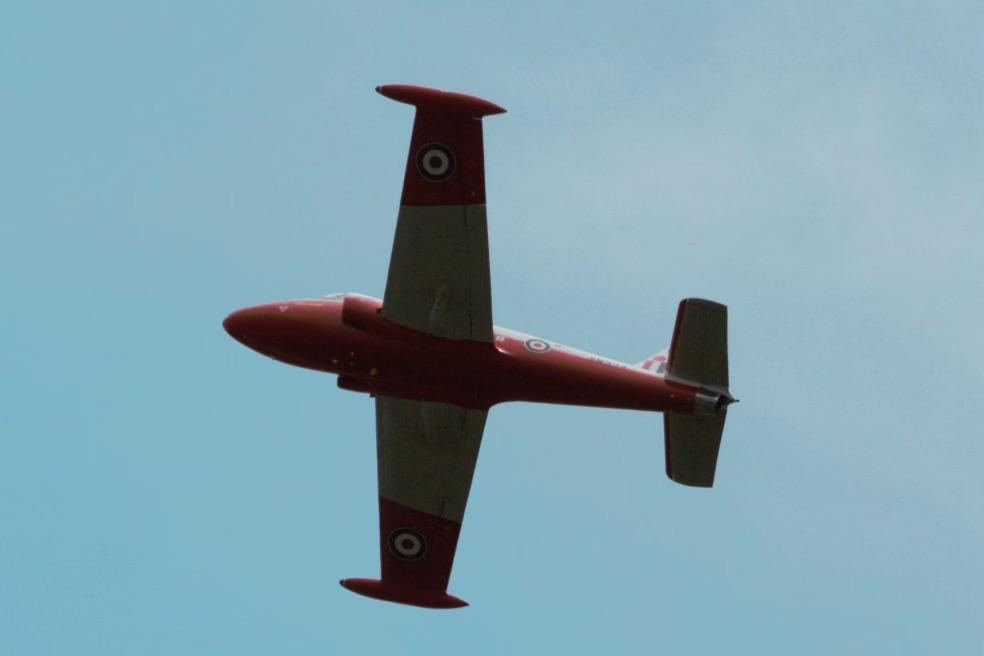
The Jet Provost is powered by a single Viper of the 200 series jet engine developing 2,500 lbs of thrust, whereas our jet hydroplane Longbow is powered by twin Vipers of the more powerful 500 Viper series, developing around an additional 1,000 lbs of thrust each, so a combined static thrust of approximately 7,000 lbs !
With DJ in the media spotlight last month being announced for the role of reserve driver when the Ruskin Museum run Bluebird K7 in 2026, we were contacted this month by our local BBC Radio Lancashire twinned with BBC Radio Cumbria. Their enquiry was to ask if I would mind coming into their Blackburn studio to chat with the lovely Nishma Hindocha about building Longbow and the background to the project. It is the first time that I have spoken publicly about the venture so please forgive my nerves in the following audio link of the interview kindly captured by my good pal Tony Stuchbury. It is I suppose just something the team and I are going to have to get used to as the build and development of Longbow progresses and with that inherently and in thanks to our sponsors, becomes exposed to a wider audience.
Away from the media our design engineer for Longbow Paul Martin has been spending all of his time and really do mean all his time, getting into the finer details of the driver cockpit design. For example ensuring the loadings on the pilot harness mounts in that cockpit are within limits in the event of a crash. For the capsule itself it is impossible to predict where the peak loadings will be in all the permutations of any and all crash scenarios one might think could occur. Accordingly Paul has had to design the cockpit to withstand those peak loadings not just in specific areas but everywhere.
We are in communication with the governing body for Outright World Water Speed Record attempts, the UIM, through the British Powerboat Association (BPBA), currently to discuss procedures for sample panel testing of the composite outer shell to the cockpit. Fortunately Paul has undertaken many such load tests in his long career as a composite design engineer so in that regard, this requirement is thankfully far from his first rodeo.
The stage that we are now currently at is whilst Paul concentrates on the outer composite shell analysis, he has meanwhile provided us with a provisional layout for the tubular steel cage that he has designed for the driver to sit within.
From that design we have taken off tube sizes and approximate lengths to allow us to make a cutting list for initial enquires to stockists of BS4 T45 steel tube that the steel cage for within the cockpit will be fabricated from. This high performance carbon based steel has been used within the aerospace industry of the U.K. dating back to being part of the legendary Spitfire and Hurricane airframes and was selected by Paul to be used for the twin jet engine cradle within Longbow. The material for that engine cradle being previously kindly sponsored and supplied through Mark Sugden of John. W. Laycock steel services in Keighley.
The next job with the steel cage for the cockpit will be to draw up each of the tube joints and bends as these will be required by the software of the machines that will laser cut and bend where appropriate the tube to the required joint shapes / angles. Once those drawings are completed Paul will review and amend them as necessary to sign them off before we proceed to cut metal and fabricate.
As we approach the end of the year I must thank our sponsors, partners and followers for hanging on in there whilst I paused writing the monthly updates I know many of you follow but trust you will appreciate that with competing teams attempting this record, I have been very limited with what I could publicly disclose in respect of Paul’s design of Longbow’s cockpit and striving to make it BPBA / UIM compliant if able to do so.
I for one knew from the outset it would be a mammoth task to try and have a cockpit that would be BPBA / UIM compliant and a very big ask of Paul’s time, knowledge and effort to attempt to do so given the huge speeds involved. However looking at the work that Paul has undertaken to date and continues to do so on this I am absolutely flabbergasted at just how complex such analysis actually needed to be. If ever there was a case for the statement ‘we would be lost without you’ it applies to Paul and his dedication to getting Longbow built and on the water doing what she is designed to do.
I showed just a small section of Paul’s work on the driver cockpit capsule to Neil our website manager and whilst Neil is obviously no structures expert he is a very bright software engineer and upon reading and digesting this sample of Paul’s work he shook his head in disbelief at just how involved Paul’s analysis to date has been.
As far as the build timeline goes, yes of course it would have been far quicker and easier to have built a cockpit that was not BPBA / UIM compliant and had that fitted into the boat this year. However in our particular case, for running a jet hydroplane at speed safely here in the U.K. such an approach I have little doubt would have only come back to bite us further down the line.
That is to say when it comes to ensuring we are doing our utmost to keep the driver of Longbow, the team supporting the craft out on the lake and the public watching on the shoreline, all as safe as we can, the documentation we will have to submit to gain permissions to run Longbow upon lochs / lakes here within this densely populated country, to obtaining insurance, etc then to attempt to run Longbow outside of the BPBA / UIM governance of British power-boating would present us with considerable challenges to say the least.
For the Longbow team we must endeavour to take what we consider to be the safest, path to getting this jet hydroplane on the water and developed in order to make a credible attempt upon the Outright World Water Speed Record for Britain. So just as the British Longbow archers did at Agincourt, it’s two fingers up to anyone who would suggest we approach this venture in any other way.
Wishing you all a very happy Christmas and all the very best for 2025 !
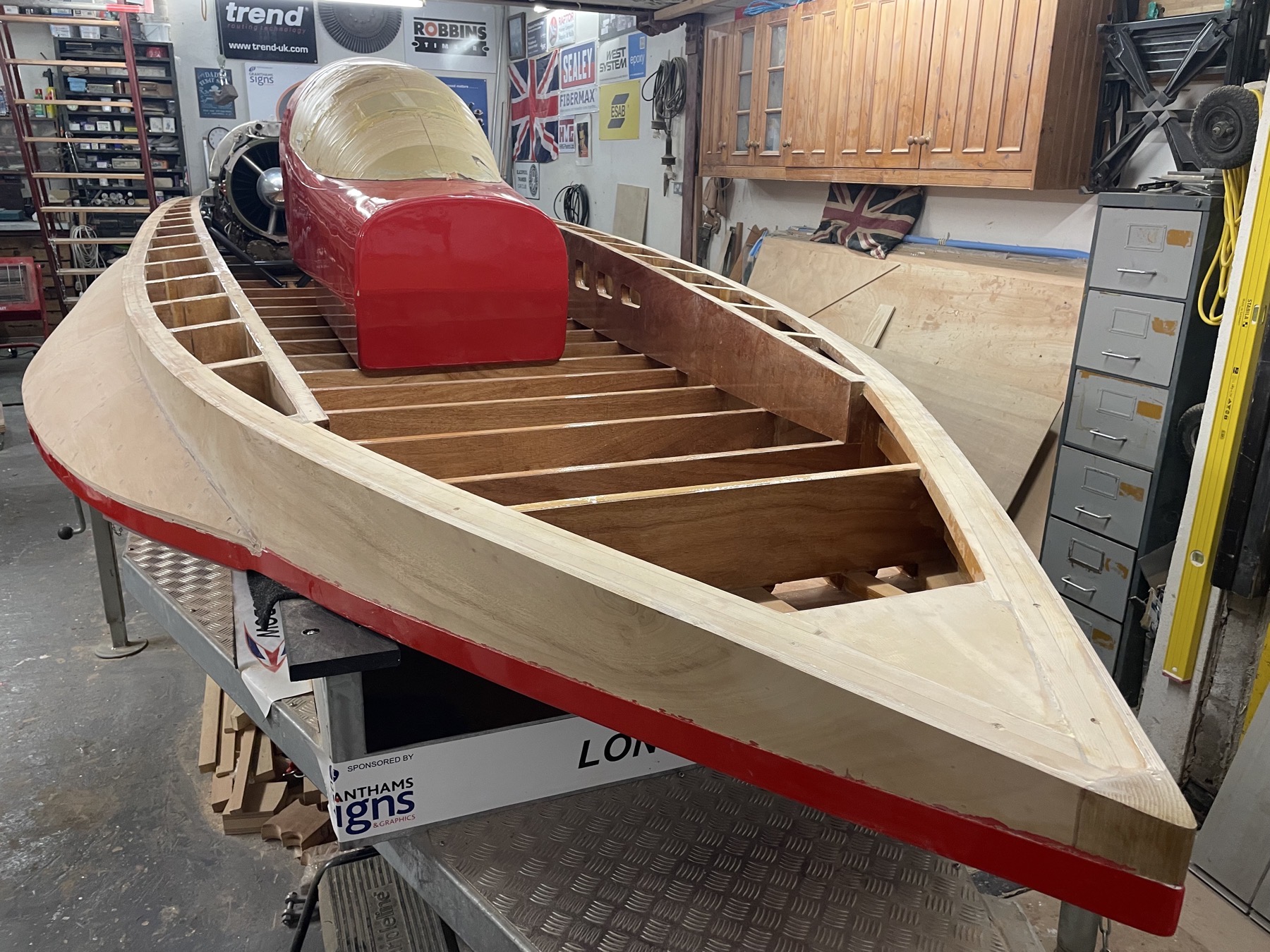