Here is one for your local pub quiz, what is the second most common natural polymer in the world? If that has you stumped (no pun intended), the answer is a component of wood, called lignin. So what is lignin and what on earth has it got to do with the building of our jet hydroplane Longbow?
Lignin is water resistant and reinforces the cell walls of all land based plants including trees and stops them from collapsing. This is important because without the lignin the hollow cells within trees responsible for transferring water would collapse and the tree would die. It is this lignin that gives the tree and consequentially wood cut from it, resistance to bending but in our case there are certain timbers within the hull of Longbow that we want to intentionally bend in order to form certain shapes whilst importantly retaining the strength of the material.
Think of a curved chair leg as shown in the following sketch. If that leg was simply cut out of a large section of timber wide enough to accommodate the shape, it may well collapse when somebody sat upon it because the grain of the wood over the curved length would in some areas only be relatively short and therefore weak. In order to resolve this problem what we need to do is bend the wood so the grain remains continuous over the full length of the curve with little loss of strength whilst also reducing wastage of wood from our sponsor of the project Robbins Timber.
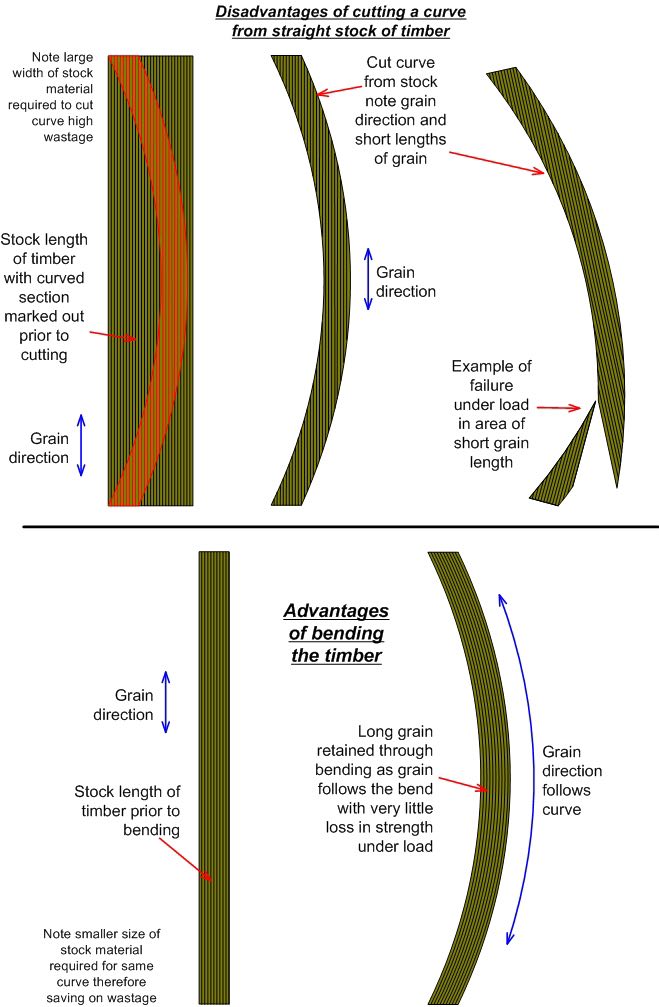
Fortunately lignin can be temporarily softened by subjecting it to unpressurised steam at 100ºC for a period of time, typically an hour per inch thickness of the wood you wish to bend, irrespective of width and in this pliable state we are able to bend it to the shapes we require.
Timber from some trees inherently steam bends better than others, with exotic hardwoods and softwoods not being particularly easy to curve by this process. This is especially so if they have been kiln dried in order to remove much of the moisture they contained when the tree was initially cut down to accelerate natural seasoning of wood before use. This being the case we need to re-wet the wood we want to bend for a period of time, in order to aid heat transfer through the full section of timber and thereby reach all of that lignin inside and soften it. Typically for the sections of wood we wish to bend, we want to pre-wet that wood for at least 24 hours.
Given the timber we wanted to bend in this instance was over 20 feet long, it wasn’t going to fit in the bath of the cottage to soak it in there, which is probably just as well as my wife Gill as you may imagine would not have been too pleased (although I must confess engine parts in the past have been put in the dishwasher for cleaning). Thinking about the problem, we hit upon the idea of dropping a tennis ball in the eaves gutter outlet of the cottage in order to block it, filling the gutter with water from a hosepipe and putting the lengths of timber in there to soak as shown in the following photo.
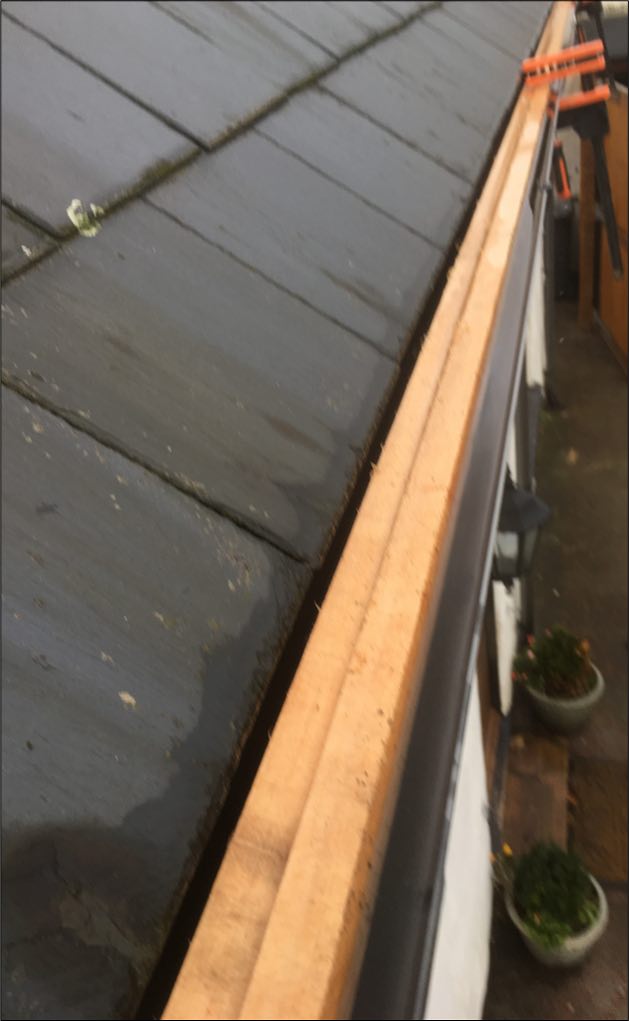
This worked reasonably well other than for the fact that believe it or not, wood floats (which helps when building a boat), such that the top surface of the timber we wanted to soak was not being wetted as much as we would have liked and considering we have quite a lot to do, a better solution was required.
We did try polythene ‘lay flat tubing’ which you can buy in various widths and thicknesses and comes on a roll. It is meant for packaging where you heat seal the ends of whatever you are putting inside but filling that with water over twenty feet proved to be too much pressure for the elongated bag to contain and leakage at the seams would inevitably occur as shown in the following photo where the timber packers allow for the slope of the driveway.
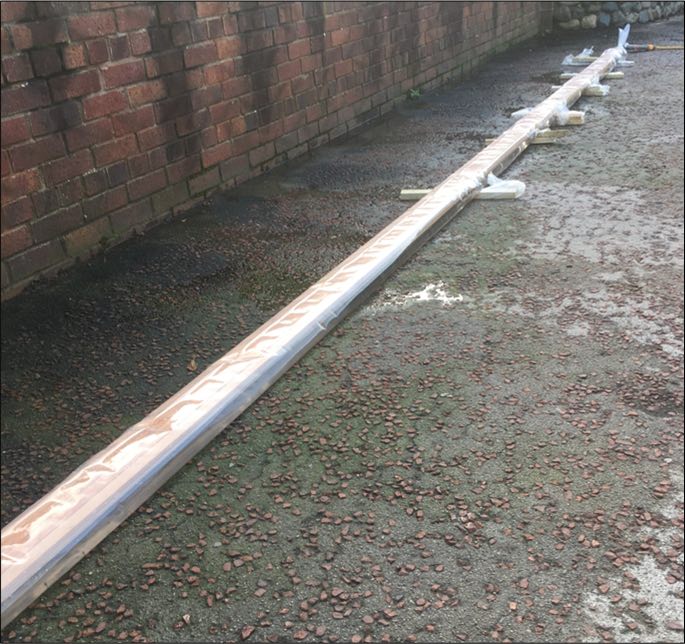
The solution came along in the form of using rigid plastic soil pipe, large enough in diameter to accommodate the widths of timber we want to bend, a screwed sealing cap at one end, a bend at the other end along with another screwed sealing cap. Sliding the long lengths of wood into the straight end of the pipe, then fitting the sealing cap shut behind them followed by filling with water from a hosepipe from the other end of the soil pipe, until the water comes up that bend as a tell tale sign so we know the soil pipe is fully flooded all along its length before fitting the top sealing cap. The result works very well with lengths of timber fully immersed in water on all surfaces and left to soak.
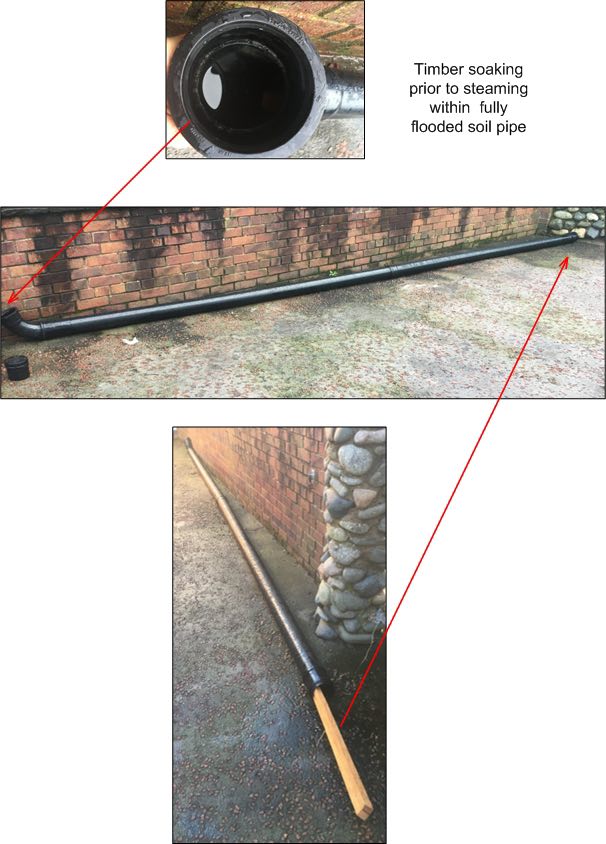
Our next job was to make a container that we could put the soaked lengths of timber into and then introduce the steam to soften the lignin. You might ask why we just didn’t use the soil pipe that we had previously filled with water to also steam the timber but the plastic of the pipe melts at the temperature of the steam, so that was not going to be the answer. What we decided to build was a traditional steam box over twenty feet long that would suffice for repeated usage, yet able to be taken apart into manageable lengths for storage when not in use. In the following photos you can see Steve and Fred forming the steam box from plywood which we coated internally as a protective barrier and inserting timber dowels across it in two levels to act as periodic supports for the timber we want to steam, whilst still allowing the steam to circulate all around the wood.
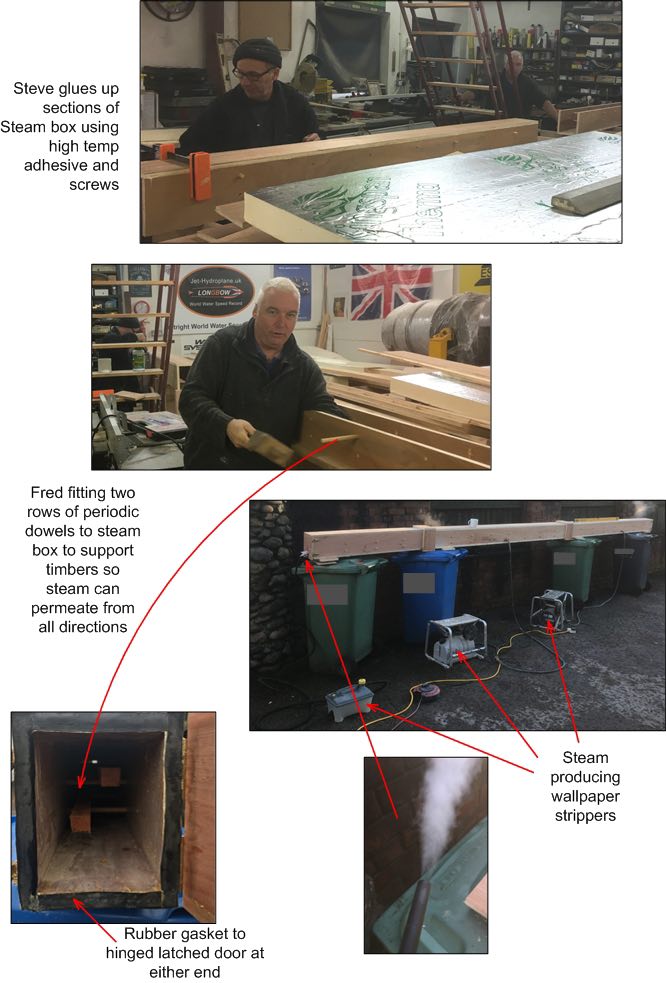
One important feature of the steam box is that you actually want some degree of leakage of the steam constantly being introduced into it to occur, otherwise it would start to pressurise with dangerous explosive results and to ensure this leakage is maintained a drain hole is provided at one end that also allows the condensing steam to drain out when the box is set at a slight angle down to this end. The following photo shows the steam emerging with condensate at this drain point.
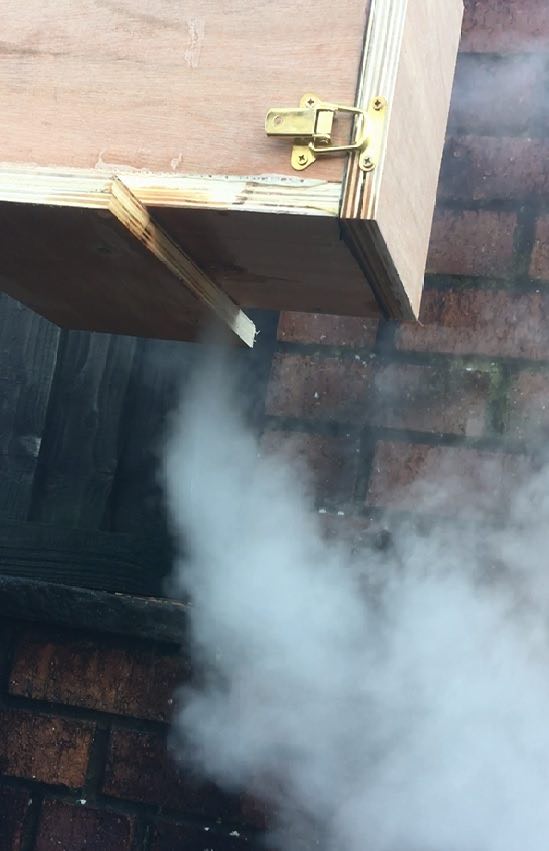
As regards producing the steam itself there are various methods of doing so but we found the easiest, for our use to be electric wallpaper stripping steam producers, which act rather like a large kettle and are easily topped up with water during the process. For the considerable length of the steam box we found that we needed three such units to ensure sufficient steam was being produced whilst also allowing for shutting one down at a time to top up water levels as necessary over time whilst maintaining steam production with the other two. The following short video shows the whole steam box in action with the three electric steam producers feeding it.
https://youtu.be/VtisE71Avv0
We steam the wood in its box outside as we do not want all that moisture laden air being produced from the process within the workshop, where it would otherwise be absorbed by the timber hull of Longbow under construction. The reason being as you may recall from previous diary updates, how important it is to maintain a relatively dry moisture content of the wood for correct bonding with Wessex Resins and their West System products who are sponsoring the entire build.
After steaming for the required length of time for the sections of wood we want to bend, once you open the steam box and withdraw the wood with the lignin in its pliable state, you literally only have a few seconds to put it into place and clamp it down into the required shape before the lignin cools and solidifies once more. This rapid cooling down is especially so where we are undertaking the process in the freezing temperatures of winter here in the UK.
If you are not quick enough with taking the wood from the steam box and clamping it into position before the lignin sets hard again, it is simply a waste of time resulting in either the wood breaking as you attempt to bend it, or springing back to its original shape once you remove the clamps. The following video perhaps illustrates just how quick you have to be and the rush involved to get the material out of the steam box and clamped into place, noting the use of thin sacrificial secondary battens between the clamps and steamed wood to prevent crushing of the timber fibres.
https://youtu.be/M28fZqca9dU
Once clamped into position allowing for a small degree of spring back, the bent timbers are held like that for at least 24 hours. However the process is far from complete, as we then have to allow considerably more time for the moisture content of the wood to naturally dry back down to a level that is appropriate for bonding with the West System products. For testing and monitoring of the wood moisture content during this process we use an industry standard Protimeter MMS, that provides both moisture levels of the wood but also relative humidity readings.
We hope that you have enjoyed reading this month’s update of how we are progressing with building the hull of our jet hydroplane Longbow and perhaps you may remember a little about the process of softening lignin in wood in order to bend it, when you are taking time out to relax in a steaming hot bath.
In next month’s update we intend to report back on our good friend Dave Warby and his team in Australia, with how they progress with their latest round of tests of their jet hydroplane Spirit of Australia II, for which as always, we wish them every success.
Stay tuned, tell your friends about us and please take a moment to like our Facebook page, Jet Hydroplane UK. See you next month for the next instalment of this exciting adventure to attempt the Outright World Water Speed Record (WWSR), from all on the Longbow team.