I know it is only three weeks after the last diary entry but my good friend Neil of Progress Concepts, who very kindly does all the IT work for the Project is going away on holiday at month end so I didn’t want to leave doing this update until his return in the midst of March.
Having made a good start to February with sanding the underside of Longbow’s hull for the final coat of our sponsor International’s superb gloss Perfection Pro paint, things have somewhat ground to a halt when COVID came calling at our cottage along with crazy storms and unusually for us a day of snow at time of writing!
The paint accelerator that I wanted to try in order to reduce the timeframe for dust contamination to settle on the paint has now arrived from the USA. However under the circumstances I trust you will appreciate it is just a case of waiting a week or two for the weather to improve as any to attempt to put paint on the hull under the stormy freezing weather at the moment would be just asking for trouble.
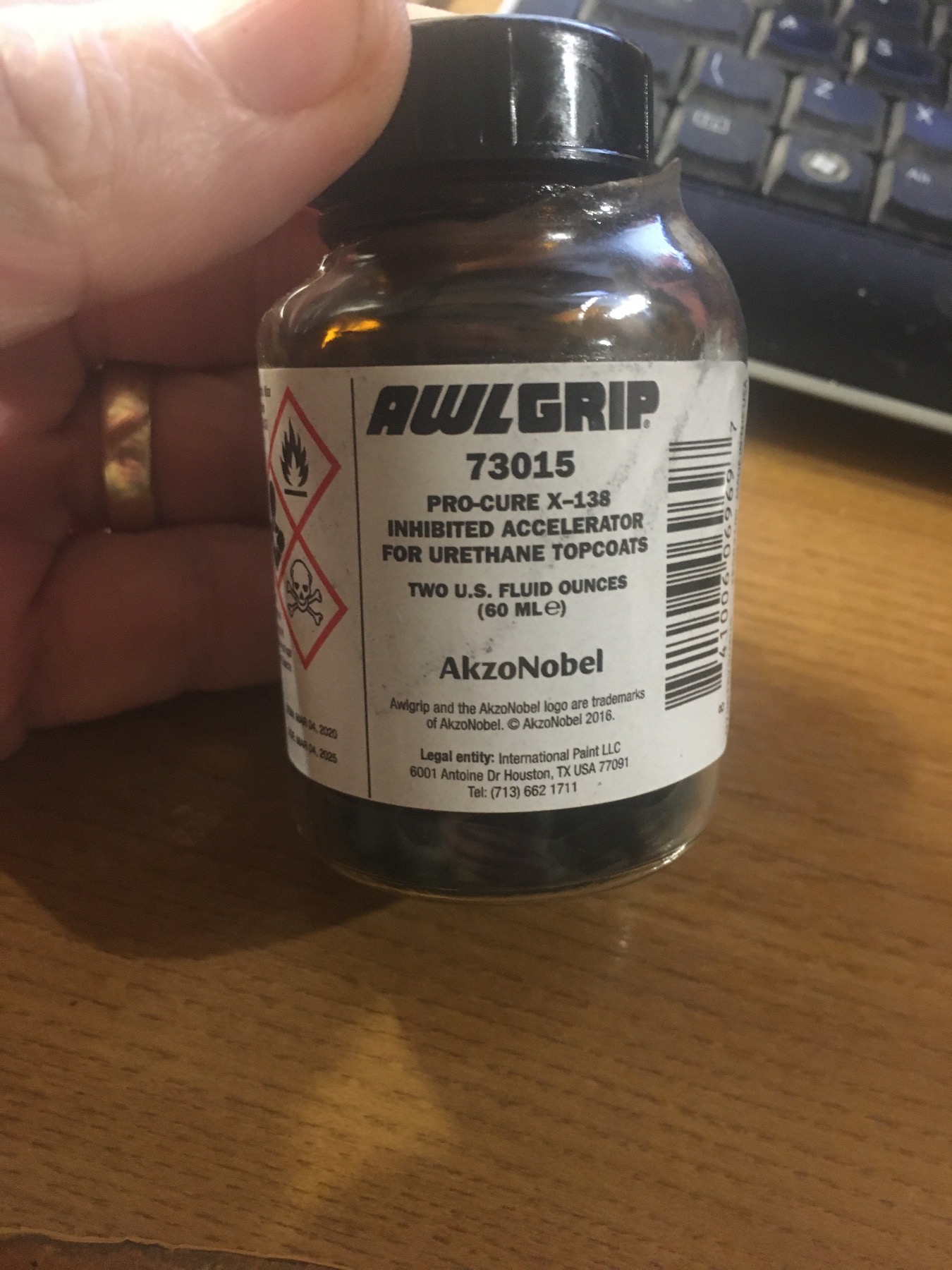
So putting the above to one side it has allowed me to write a little about a subject I have been asked to explain in hopefully easy terms for folk to get their heads around and that is ‘thrust augmentation’. Or in other words for a short period of time getting more thrust out of a jet engine than it would normally deliver. Now I know there will be the gas turbine engineers, mathematicians and those who play around with jet engines who will criticise me for the simplistic way that I have written the following but let’s try and keep this at a level that doesn’t bore people to death and is simply helpful to those with a passing interest in going quick with jet engines.
We have already discussed in previous diary updates about how a gas turbine jet engine works so if you are new to the website and want to learn about that, then may I suggest you have a trawl back through the previous diary updates and have a read. What we are interested in here is how do we make greater thrust come out the back of a jet engine for a short period of time.
Well if you want more thrust out of your jet engine why not just spin the turbine quicker especially if you are only going down a quarter mile length of track for several seconds where is the harm in that? Well funnily enough manufacturers of jet engines don’t put limits on how fast you can spin that engine for nothing. If you alter the manufacturer’s maximum fuel settings on the engine to allow the turbine to revolve faster than the they have put a safe limit on the engine, as things spin faster than they were designed to, they tend to stretch more than they were supposed to.
Given there is a minimal gap between the blades of the turbine wheel and the metal tube within which they spin it doesn’t take much over-speed for the outer tips of those blades to start rubbing against the inside of that tube and before you know it, at best the whole lot comes to a very expensive grinding halt. An even worse day out for anyone stood behind would be blades breaking off and coming out the back of the engine as shrapnel mixed with jet thrust, or for somebody at the side of the engine saying hello to a blade at its root, coming at them as it broke out of the engine casing with all the kinetic energy of an artillery round.
If you think things could not get any worse than that then you would be mistaken as the heavy metal discs those blades are attached to at their root can also fracture and explode like slices of pizza. Whilst a turbine disc failure is thankfully a rare occurrence they do still happen, for example an aircraft sat on the ground during an engine test in 2006 let go a section of turbine disc that went out the side of the engine for a distance of half a mile. I will just repeat that in case you missed it – yes half a mile as it went across aircraft taxi ways, then across two runways that were in use and then it took investigators two days to find it.
So if we don’t fancy over-speeding the jet engine how else can we get more thrust out of it?
Well if you can think back to your school days and your physics class then Newton’s second law says the force (thrust) needed to accelerate an object increases with the object’s mass. So the thrust of a jet engine is dependent upon the density of what is being blown out through the turbine which generally you would expect to be air and mostly combusted jet fuel.
However what if we were to add water to the air being ingested by our engine? Well since water is more dense than air, the total density of what is being blown out through our engine would go up and as a consequence so would the thrust. Now we can inject that water into the engine in three different places. We can ingest it in the front of the engine, we can squirt it into the combustion chamber of the engine, or we can inject it just before or just after the hot wheel (power turbine). The last option is the simplest as it doesn’t have all the hassle of possibly damaging the compressor blades or messing with the combustion mixture of the air and fuel.
Of note the Harrier jump jet used distilled water injection into the Pegasus jet engine with the water supplied from a tank that gave it around 90 seconds of additional thrust for certain situations. Other examples of aircraft to use water injection for additional thrust were early versions of the Boeing 747, 707 and B52 bombers.
As you might imagine water is a heck of a lot cheaper than jet fuel but the same would apply if we injected unlit jet fuel into jet pipe of the engine rather than water before it emerged out the jet pipe. That is to say we would through density alone likewise increase the thrust of the engine the same as we did by injecting water in the previous example. However what if we then set fire to that fuel because who doesn’t love flames coming out the back of a jet engine?
As luck would have it even though air has been previously mixed with jet fuel and set on fire inside the depths of the jet engine itself that process does not use up all the oxygen in that air. In fact it only typically consumes about 25% of the available oxygen so there is still a heap of oxygen (75%) coming out the back of the engine itself before it then carries on its journey out the end of the jet pipe. If we squirt in more jet fuel at this point and set fire to it then the temperature of that air is going to go up massively. This what is what is known as afterburning or reheat.
Other terms that are worth mentioning at this stage before going any further are a jet engine running without an afterburner is often said to be running in ‘dry’ thrust and when the afterburner is lit running in ‘wet’ thrust. At maximum ‘dry’ thrust without engaging the afterburner this is sometimes also referred to as ‘military power’.
Now going back to our afterburner if the temperature of that air goes up massively due to the additional fire you have just ignited in the jet pipe then, that air wants to also expand massively. If you cannot get your head around that think about how they unpack a hot air balloon on the ground, light a fire beneath its open end and the hot gases expand to fill the balloon ready for take off.
In our case these much hotter gases are contained by the jet pipe so they act to increase the velocity (and consequentially thrust) of the air coming out the back of that jet pipe. Getting increased thrust by injecting fuel into the jet pipe and then setting fire to it so as to create more heat in the heat jet pipe and thereby greater velocity of the air is what afterburning or reheat of a jet engine is all about.
Unfortunately the efficiency by way of how much fuel you have to throw into an afterburner for the amount of thrust you get back out is not brilliant even when the system is designed by the original engine manufacturer. For example the afterburning version of the J79 engine that was used in the F104 Starfighter aircraft increased overall fuel consumption by 400% for only a 50% increase in thrust. Better efficiency figures are reached using more modern low bypass engines compared with older turbojets but it still results in a massive of fuel consumption increase for the amount of additional thrust provided. For this reason afterburners are generally used for short duration such as military aircraft that need to take off and accelerate to altitude as fast as possible, or combat manoeuvres.
Part of this eye watering amount of afterburner / reheat fuel inefficiency is explained by the flames themselves seen coming out of the back of the afterburner when it is functioning. It should be obvious that you have fire still occurring in the jet stream and for that to happen you must have fuel in the jet stream still being combusted outside of the vehicle / aircraft when ideally it should have all been used up as part of the combustion process inside the afterburner section of the jet pipe.
A feature of the flame coming out of the vehicle / aircraft often seen particularly when an afterburner is in use is what are known as ‘shock diamonds / discs’ or ‘mach diamonds / discs’ which are a series of bright spots at regular intervals of diminishing intensity the further the jet stream is from the engine. The name mach funnily enough does not come from the classic song ‘Mack the knife’ but from an Austrian physicist Ernst Mach who studied the phenomena and whom the speed of sound is name after. So what causes these shock or mach diamonds to occur?
Well with an afterburner lit and running at maximum flow, the air (and to some degree jet fuel) coming out the back of the jet pipe is typically doing so at a velocity that is supersonic and as a result of that a series of oblique shock waves form about the centre of the this stream of air as it emerges.
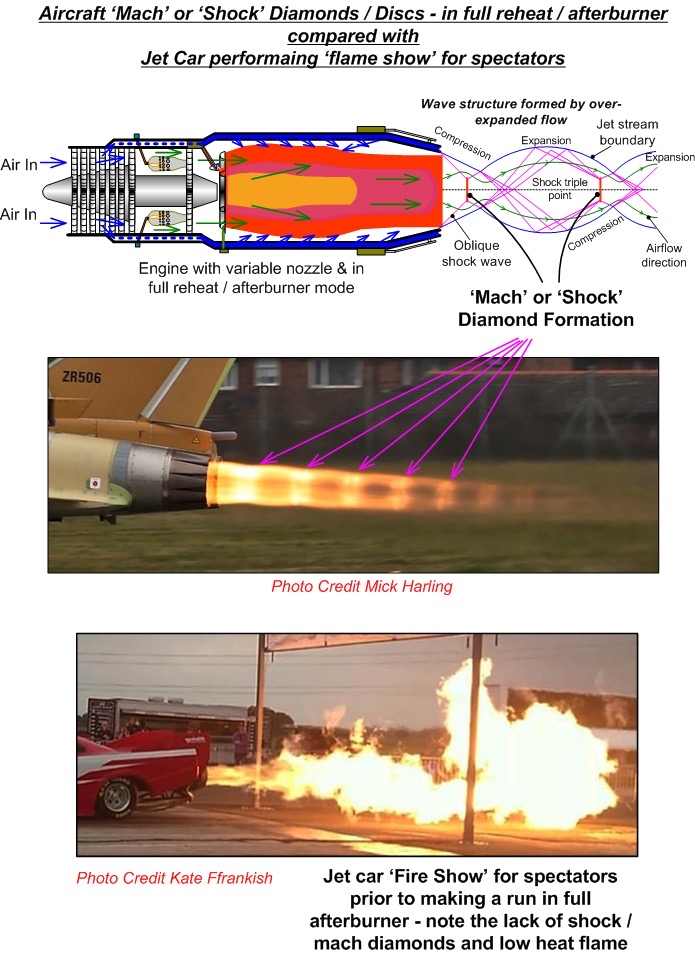
Particularly at or relatively close to the ground the air pressure around us is higher than the air pressure coming out the back of the jet pipe and so this surrounding air squeezes the supersonic air as it emerges and in doing so slows it down. This in turn causes the temperature of that supersonic air to go up to such an extent that it spontaneously ignites a certain amount of the unused jet fuel within that air previously referred to that didn’t get combusted within the afterburner.
The result of this spontaneous ignition of unburnt fuel in the jet stream is the glow of the first mach / shock diamond or disc being formed that can be distinctly seen in amongst the jet stream. The situation then simply repeats at regular intervals bounded by the shear of the airflow relative to the surrounding relatively still air and this shearing of air at this interface takes energy out of this airflow diminishing the phenomena with distance.
Going back to what is going on inside the afterburner you cannot simply squirt fuel into this section and throw in a match and expect it to light. You might expect the fuel to spontaneously ignite if you threw it in there but it would take around 800 deg C at sea level to do that and the air coming out the back of the engine isn’t hot enough to do that reliably.
The air coming out the back of the engine itself before it reaches the afterburner rig is typically moving at about 750-1200 feet per second or 500-800mph which is rather gusty to hold your match up and expect it to stay lit so we need a better system than a match and crossing our fingers.
I can think of three common and one special case to ignite jet fuel within an afterburner and referring to the sketch as follows:
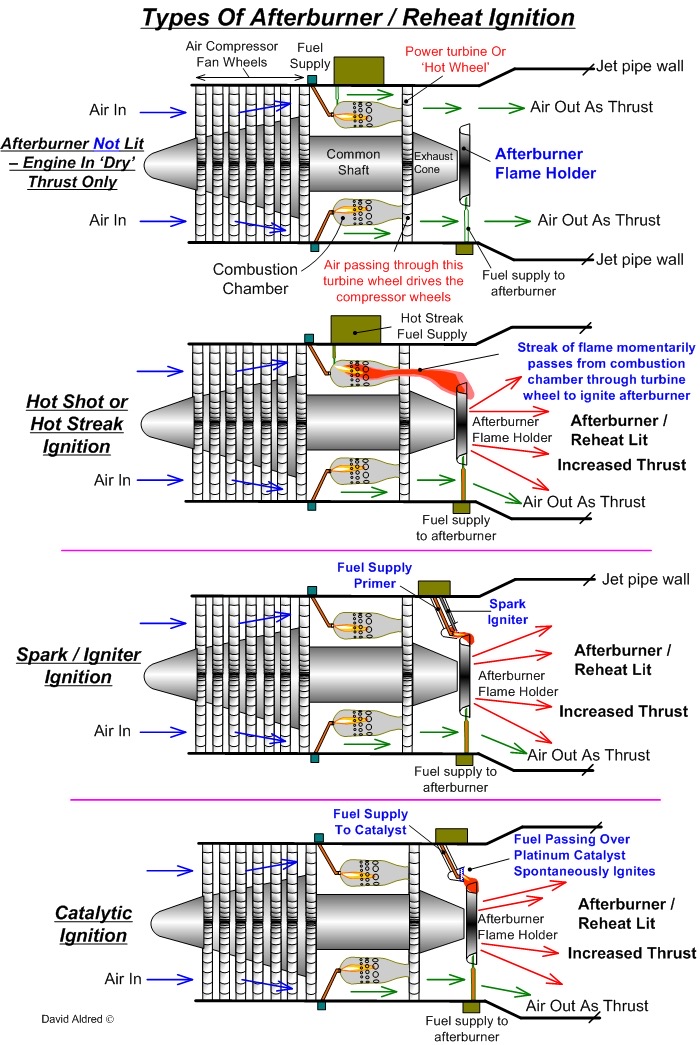
In the first method of afterburner ignition (and one which is often used on jet cars) you can inject an additional amount of fuel into the combustion chamber of the gas turbine itself for a short period of time. This additional fuel causes an elongated flame to shoot out of the combustion chamber and pass right through the turbine wheel blades to set fire to the fuel being introduced into the jet pipe as part of the afterburner rig on the other side of that turbine wheel. This system is called a ‘hot shot’ or ‘hot streak’ type of afterburner ignition. When it works right the turbine blades are not damaged by this system but get it wrong and it has been known to cut through those turbine blades like a hot knife in butter destroying your engine.
A different system of afterburner ignition is to have a spark / igniter plug and a supply of fuel housed side by side in the jet pipe and shielded from the airflow by a metal shroud. This supply of fuel is ignited by the spark / igniter plug and once lit the flame then propagates to the rest of the main fuel supply rig of the afterburner.
Thirdly is the use of platinum / Rhodium catalysts that when heated by the jet stream already coming out the back of the main engine will cause standard jet fuel introduced onto that catalyst to spontaneously combust. Platinum has an affinity with hydrogen atoms and this relationship was even used with a rather unusual handheld lighter or hand warmer that anyone could buy which did not require a traditional flint spark to provide ignition as shown in the following video:
Another afterburner ignition system used specifically on the SR71 Blackbird aircraft was to light the afterburner and indeed the engines themselves by the reaction of Triethylborane (TEB) which spontaneously ignited when brought into contact with the air at a temperature above -5degC.
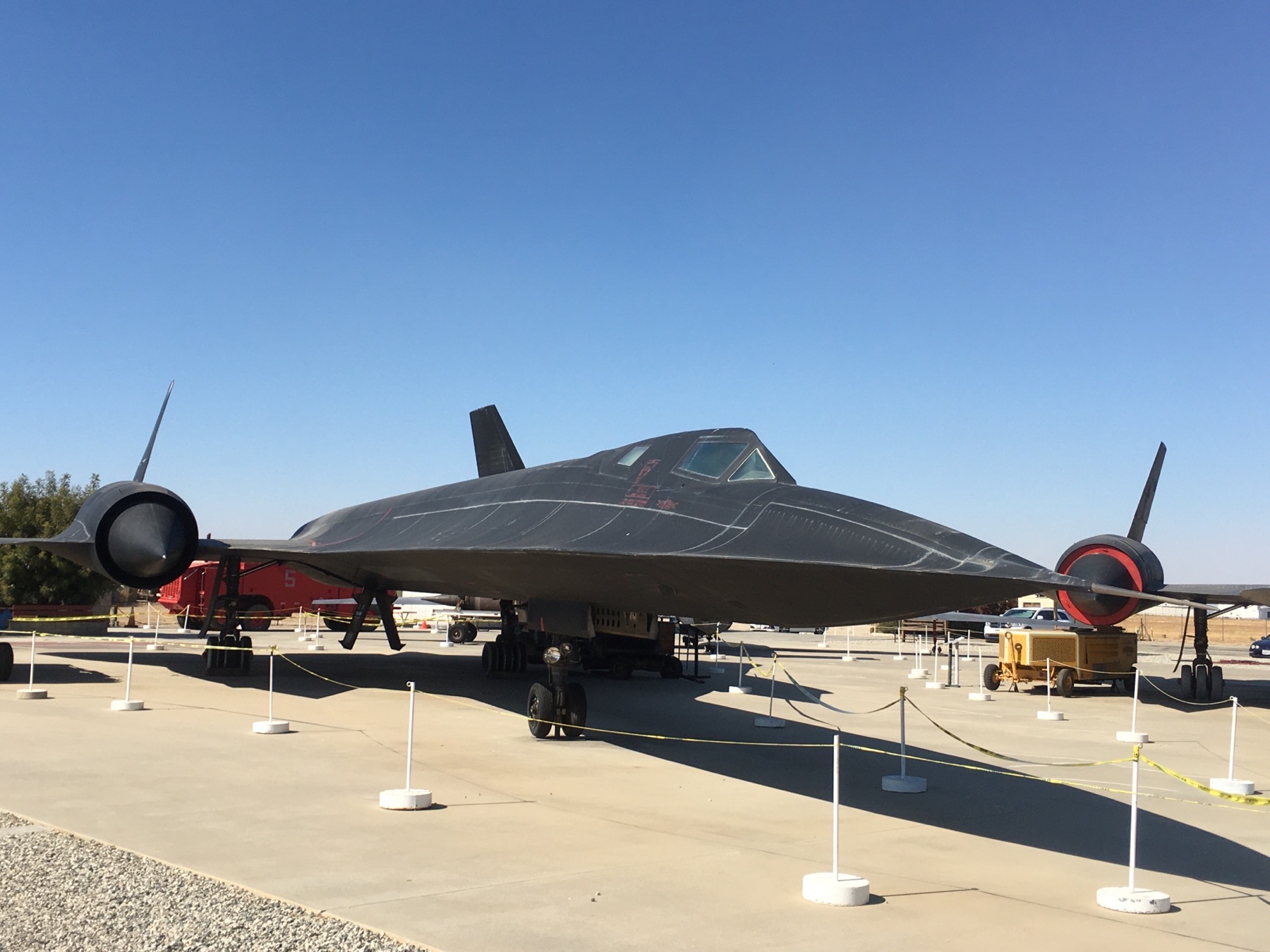
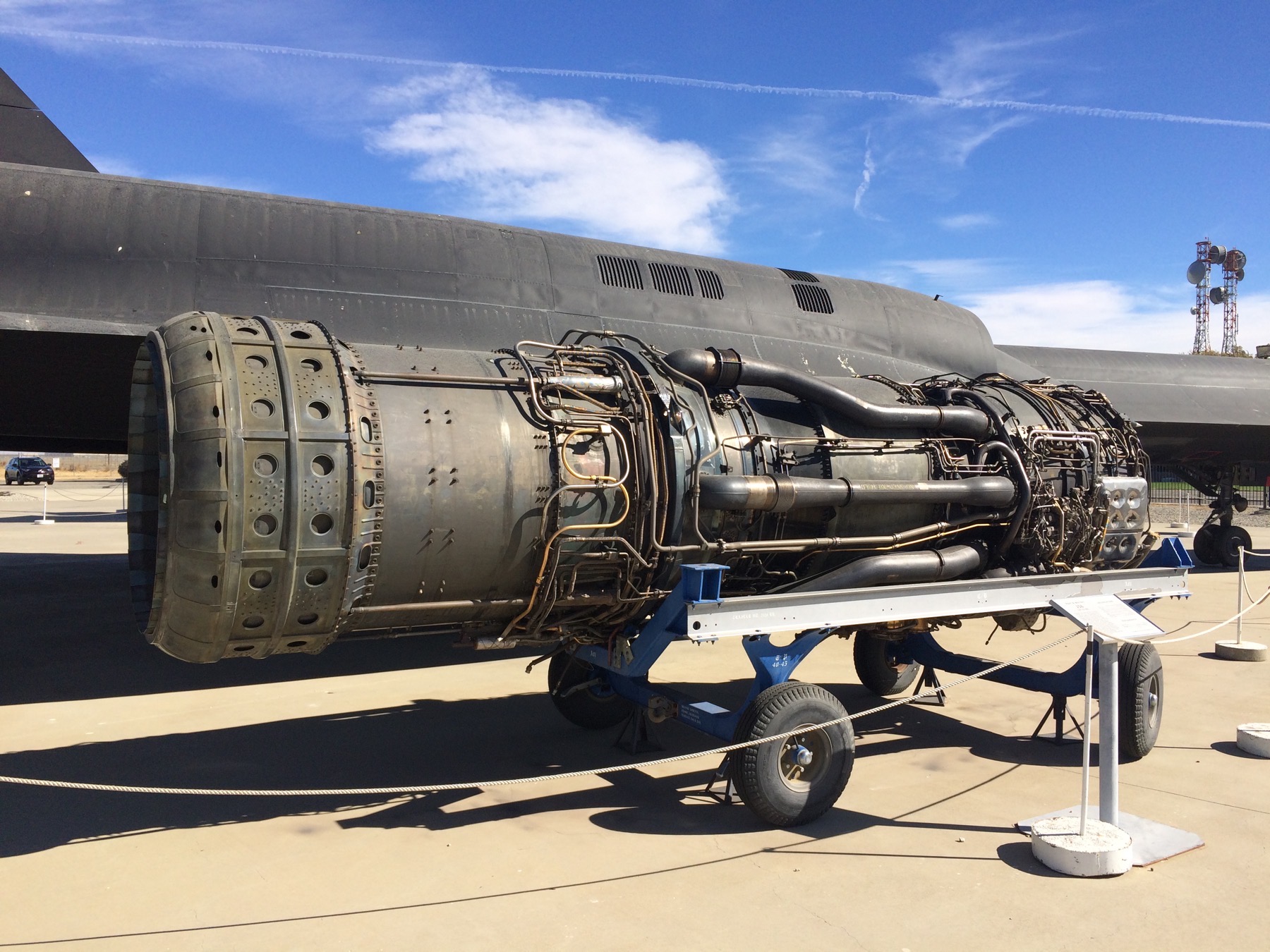
This TEB system was used alongside catalyst igniters in the aircraft due to it having a special type of fuel (JP7) that was made purposely difficult to ignite by other means but consequentially limited the number of restarts the afterburners could make in flight to the reservoir of TEB available in the aircraft. JP7 fuel was developed so as to reduce the risk of standard jet fuel igniting from the heat caused to the airframe flying at such incredibly high speeds (officially stated as Mach 3.2 but probably faster).
So now you know how to light your afterburner we then need a means by which when we spray fuel into the jet pipe it will hold a flame steady in the high speed air coming out the back of the engine and under varying conditions of mixture, distribution of gas flow and in the case of aircraft varying attitude. The result is a series of concentric metal fuel manifold gutter rings each in the cross sectional profile of a ‘V’ or ‘U’ shape sometimes with perforations to allow some degree of airflow and yet be aerodynamic into which jet fuel is supplied via a manifold with a number of outlets to spray fuel from that gutter and then ignited by one of the means previously described. The afterburner remaining lit for as long as the pilot / driver holds the throttle in the afterburner position supplying fuel to the system.
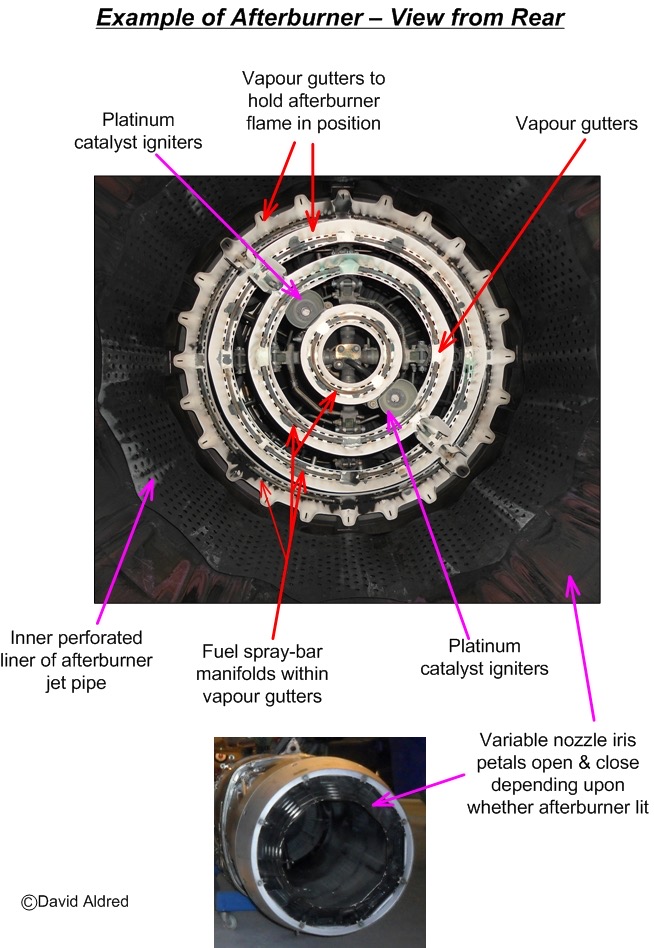
As one can see from the photographs these concentric afterburning fuel gutter / manifold rings combine to partially obstruct the airflow coming out of the back of the engine and as a result, rather like standing in front of a fan, the thrust of the engine without the afterburner lit is somewhat reduced compared to the same engine without an afterburner rig fitted.
Because of the increased volume of gas during reheat when the afterburner is lit, the jet pipe has to be a larger diameter than a standard jet pipe fitted to an engine without afterburner, otherwise there would be a risk of this rapidly expanding extremely hot air pushing back through the engine in a complete reversal of airflow. Since the engine is not designed to cope with air going the wrong direction through it, nor the massive heat of the afterburner spilling out the front of it, such a situation would wreck the main jet engine in no time at all.
It is also for this reason that afterburners are not usually lit at throttle settings less than 80% because the less air coming through the engine the greater the risk of lighting the afterburner causing that rapidly expanding air to blow back the wrong way into the engine.
The hassle with just having a large fixed diameter jet pipe that is only suitable for when the afterburner is lit, is that when it is not lit that jet pipe is simply too large in diameter to get the best amount of thrust normally coming out the back of the engine. How much can this screw the up the normal performance of the engine? You might be surprised that a complete loss of half an engine’s normal thrust would be typical in that situation, or think of it like how much performance you would lose pulling half the number of spark plugs out of your car engine.
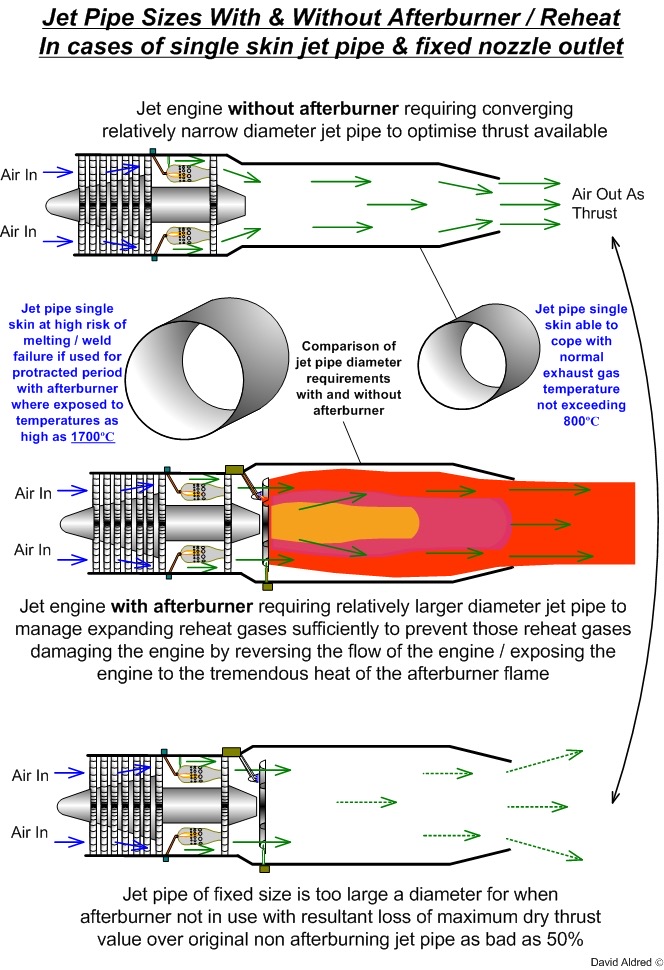
If you are running a jet car where the afterburner is lit from the start line and only operating for say less than 10 seconds over a quarter mile, then this situation of having a jet pipe that is only suitable for afterburner use might be acceptable. However if you are running a jet engine where you want to run some of the time from idle, to maximum dry thrust without reheat, then this is not a very good situation at all.
Manufacturers of reheated / afterburning engines are obviously well aware of this issue and because of that they have developed jet pipes that give the best of both worlds. That is to say small diameter at their ends for when the afterburner is not lit to give great performance of the engine within its dry thrust range and then change to a large diameter jet pipe outlet for when the afterburner is lit. In the early days of developing afterburning engines this variable diameter nozzle to the end of a jet pipe was done with a pair of in effect metal eyelids that could be moved from fully open to part way closed depending upon the throttle / reheat selection of the pilot.
In later years and as seen in modern afterburning engines from manufacturers we have the development of iris nozzles where a series of movable petals open and close to form a constant fully circular nozzle of varying diameter at the end of the jet pipe. These petals being moved by typically a series of hydro-mechanical rams close to the end of the jet pipe varied in position by the pilot / engine fuel and temperature sensors to match the throttle setting selected by the pilot all the way from idle through to full afterburner.
Whilst a standard jet for a non afterburning engine is able to cope with temperatures up to around 800ºC and typically more in the region of 550-650ºC, the temperature inside the afterburner will readily be more in the region of 1500-1700ºC which is too high for the standard jet pipe to cope with for a protracted period.
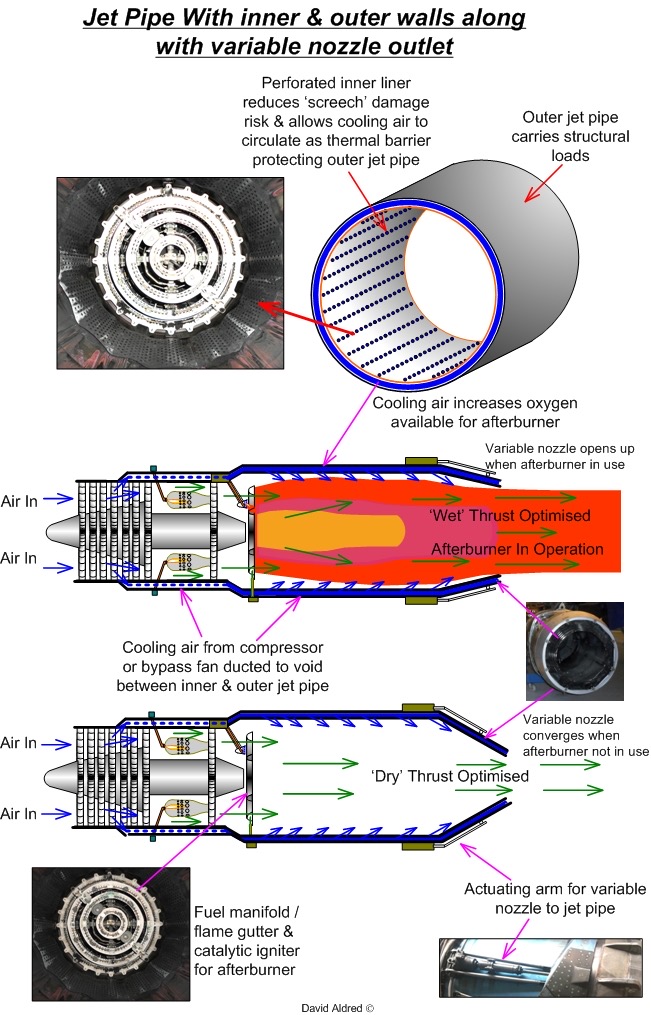
In order to deal with this problem the jet pipe for an afterburning engine as manufactured by the engine supplier is typically of sandwich construction with an outer metal tube that carries the structural loads and an inner jet pipe liner perforated with many small holes or slots over its entire surface so that air can pass readily through all of these holes and slots. What this sandwich design of jet pipe allows for is relatively cool air from the front of the engine be that taken via pipe-work from the compressor section or a bypass inlet, into the void between the inner perforated jet pipe and outer structural jet pipe tubes. In so doing this cool air permeating into the jet pipe acts to provide a thermal shield to the very high temperatures inside the afterburner and hence prevent both inner and outer jet pipes from otherwise suffering weld failures and generally melting.
Some of the undesirable effects of using an afterburner are both ‘screech’ and ‘rumble’ which are pressure oscillations at both high and low frequencies respectively, caused by combustion instability within the afterburner, particularly more noticeable at sea level. Left unchecked both afterburner ‘screech’ and ‘rumble’ will cause the engine to oscillate to such an extent it will completely break apart and is obviously something the manufacturers of afterburners try to design out of occurring. The perforations to the inner liner of the afterburner jet pipe previously referred to go some way to reducing the undesirable screech and rumble as does the design of the iris petals of the nozzle to the jet pipe.
In many cases the jet engines fitted with afterburners in aircraft, the throttle can be moved from idle through to maximum rpm 100% dry thrust (termed military power) without afterburner; then on to lighting the afterburner with minimum reheat thrust right the way through to maximum afterburner all as one seamless progression of thrust. However in some older jet engines there was either a significant time lag or a very noticeable step difference in thrust between maximum dry thrust and lighting the afterburner. For this reason Part Throttle Reheat (PTR) was developed for some engines like the Rolls Royce Adour where the afterburner could be initially engaged as low as 80% normal dry thrust. this gave a more seamless delivery of power which was further improved when engines were fitted with fully digitally electrically controlled units (DECU) to manage the engine rather than by solely hydro-mechanical systems.
When looking at the jet cars used for drag racing whilst some use engines that were manufactured with afterburners having jet pipes with inner liners and variable nozzles for the reasons previously described, there are also some jet cars that run with afterburners that have been built specifically for that jet car which may or may not have jet pipe liners and may or may not have variable jet pipe nozzles.
Sometimes with the turbine running these jet cars can be rigged to blow a huge amount of either smoke or low heat yellow flames out of the back of the jet pipe as a crowd pleaser. These shows are sometimes generated by spraying oil or fuel from a supply tank on the car into the hot jet pipe sometimes ignited by lighting up the true afterburner or having its own ignition. Obviously such smoke and flame shows should not be confused with a well designed afterburner lit on full reheat with mach diamonds coming out of the back of the engine. Shown below two very famous jet cars Firestorm & Vampire.
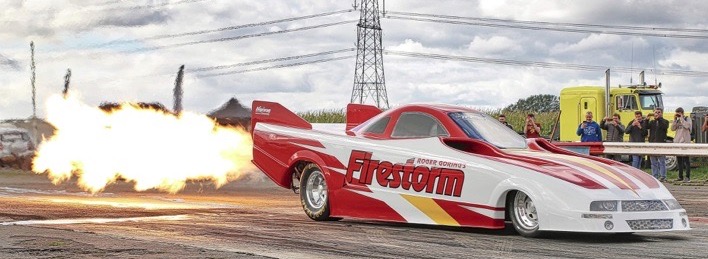
Credit Phil Evans
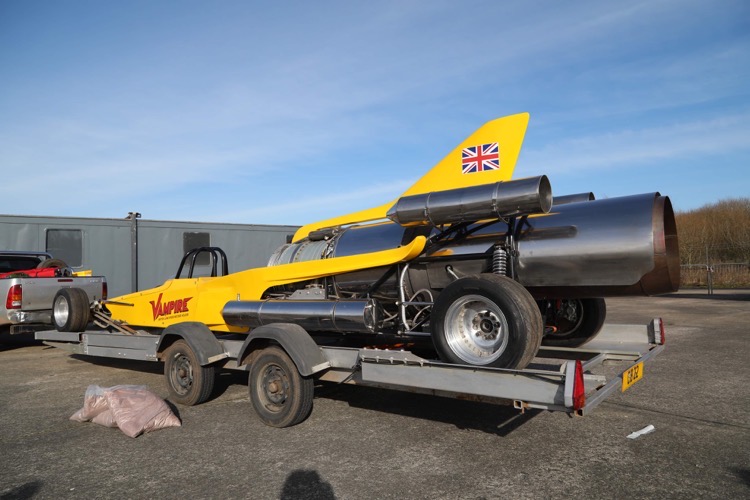
Credit Phil Evans
One hopefully can see from all of the above that an engine manufacturer spends a huge amount of time, money and effort in the development of their thrust augmentation systems, be that water injection or afterburner and with purpose made reheat to a modern low bypass military gas turbine engine, a thrust increase getting on for 70% may be achieved.
However equally with the best will in the world making your own afterburner with a fixed nozzle can be a very hit and miss affair and even folk with a lot of experience are doing well to get much more than a 20% increase in thrust which is a long way short of the 70% referred to above but a significant increase nevertheless. Shown below is New Zealand’s Dean Hart and his record breaking afterburning viper jet car which he is now selling if you want something different parked in your garage. If you look carefully at the rear of the car you can see down the jet pipe the afterburner gutters and fuel manifold:
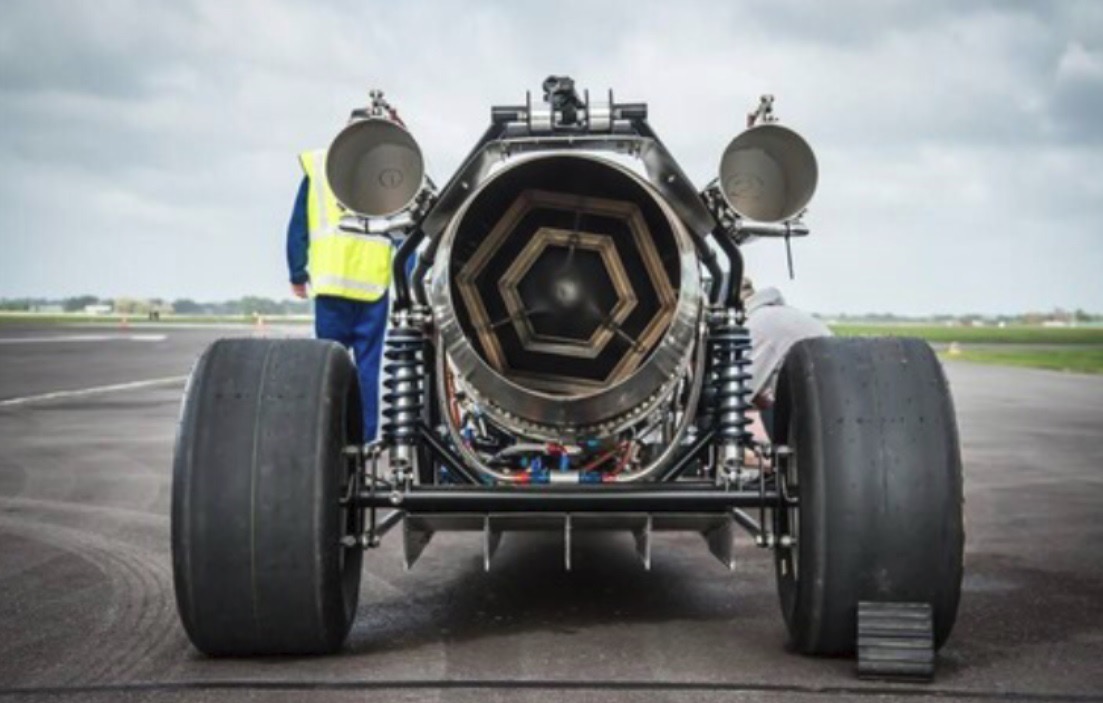
Credit Dean Hart
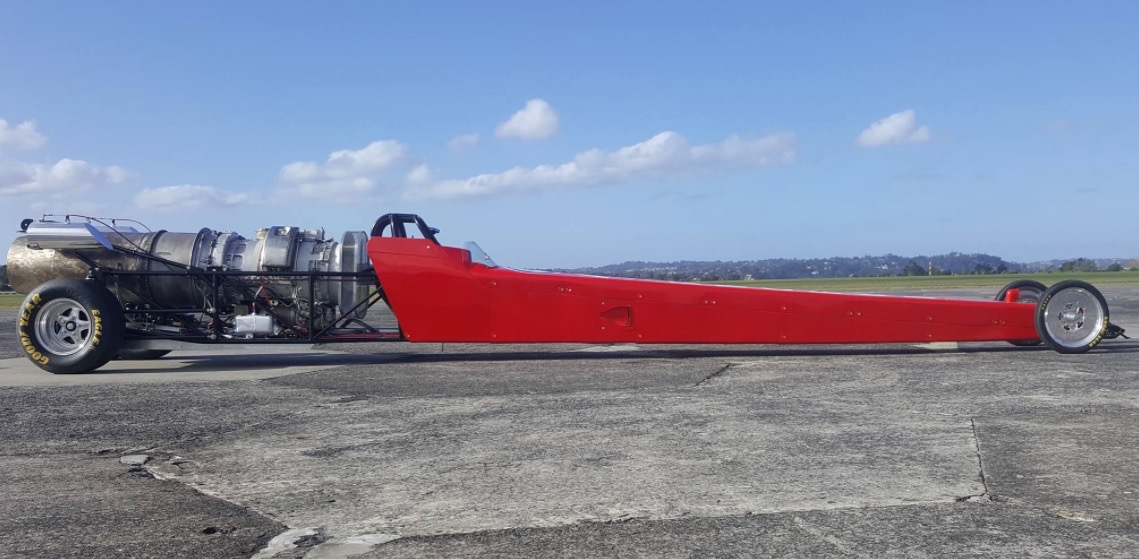
Credit Dean Hart
Having a go yourself at building an afterburner and bolting it onto your stock jet engine that was quite happy without an afterburner is something you really have to weigh up the pros and cons of doing so for your particular application.
Compared with an engine manufacturer’s reheated engine, a home built one is more likely give you headaches with whether or not that afterburner is going to light when you are counting on it to do so, concern over how stable the reheat flame is and whether the design will suffer serious engine damaging screech or rumble, how vicious for the stability the vehicle the afterburner will be in both the manner in which it comes in and goes off when extinguished.
Add to that the fact that you have probably halved the engine’s maximum dry thrust performance if you run with a large diameter fixed nozzle afterburner jet pipe and the afterburner is drinking fuel at a stupidly high rate so that is a much larger fuel load to carry if you are travelling over a significant distance.
Your single skin jet pipe without a liner running for more than a short distance / minimal period of time is going to be prone to heat failure and unless you really know what you are doing the chances of wrecking the rest of your rare and expensive jet engine downstream of your home made afterburner have probably gone up considerably.
I say all of this because people will ask me why I don’t fancy making an afterburner for the Viper jet engines of Longbow like they do with the jet cars running over a quarter mile. In our case the likely problems that would come with a home built afterburner whilst not insurmountable do not marry too well with our jet hydroplane running over several miles and then back again within the hour. It is difficult enough keeping the craft stable and trimmed as fuel is used on an ever changing surface, without adding more headaches a home made afterburner with massive fuel consumption over that distance would bring to the situation.
I hope I have not bored you too much with the above in layman’s terms and perhaps you will have a bit more insight into what all those flames coming out the back of a jet engine, hopefully for the right reason mean.
For those who like formulas and physics fed up as to why I did not go into the maths side of things with the above here is a little bit to keep you happy:
So the amount of thrust (T) of the gas turbine itself depends as we have said previously upon the mass of the airflow passing through the engine.
The product of mass and velocity is called momentum.
Therefore mass (m) x velocity (v) = momentum and having units of kilograms per metre second (kg x m/sec).
Divide by time we get kg x m/(sec x sec) =kg x m/sec^2 = Newtons.
The quantity “mass divided by time” is the airflow passing through the engine in a given time and is termed ‘mass flow rate’ (units being kg/sec)
Multiply by the exhaust velocity (metres / sec)
we get kg/sec x m/sec = kgm/sec^2 = N
However this calculation does not take into account of the forward motion of the vehicle, aircraft, boat, etc when net velocity, which is exhaust velocity (vj) minus the vehicle velocity (va) applies.
Thus T = kg/sec x ( vj-va).
Most engine specifications give the static thrust for an engine but to be able to use the information correctly you also need to know either the values for ‘vj’, or mass flow rate, or both because the net thrust of the engine will typically decline with forward velocity.
However the other important factor with all of this is how good the engine air intake efficiency is as this is highly influential upon the actual performance of the engine within that particular aircraft / vehicle / boat, etc.
Mind boggling isn’t it but then again that’s half the fun of making it happen. So that is all for the February update folks and I hope by the next diary update at the end of March the storms will be over and I will have made more progress with the build of Longbow. Thank you for dropping by and if you have not done so already please like our Facebook page to be notified of updates as our fun little venture continues.