As we work towards making a credible British attempt upon the World Water Speed Record (fastest boat in the world) of 317mph held by Australian Ken Warby MBE; a big thank you goes out to our sponsor Wessex Resins & Adhesives for their ongoing support of our Project.
This month they kindly sent us a range of their superb WEST SYSTEM EPOXY products that included 207 Special Clear Hardener to go with their 105 Epoxy Resin along with mixing pumps specific for this combination.
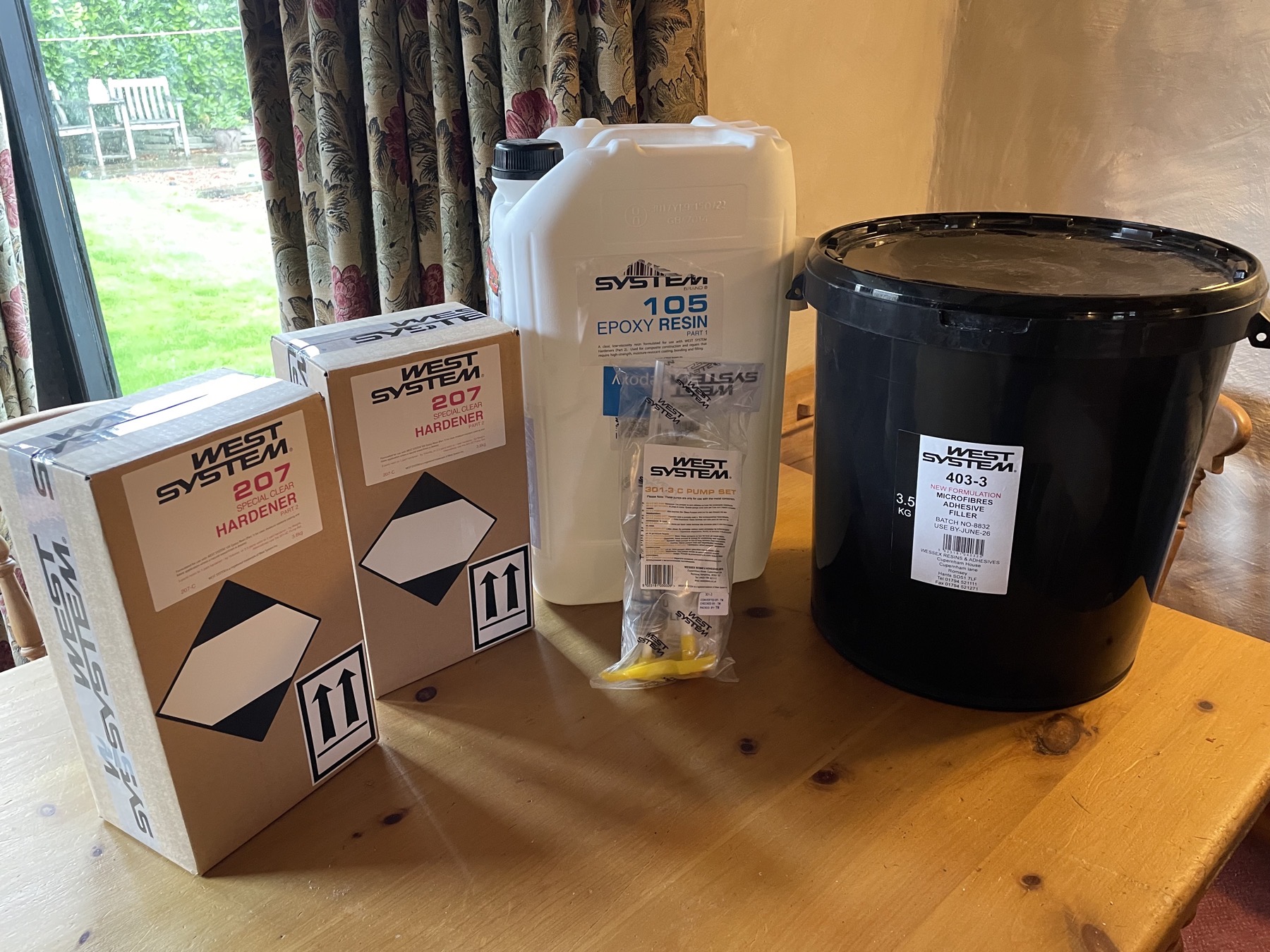
The reason that we requested this product now was to apply it to the interior of the hull before the metal framework for the engines is permanently fixed into place. Whilst one obviously builds a boat with the intention that water should stay on the outside during its operation, they are not fitted with bilge pumps for nothing because all boats inevitably take on some degree of water during running out on the lake.
The 207 Hardener when mixed with the 105 Epoxy Resin not only gives a superb clear finish that allows the beauty of the wood to be seen, it also protects the timbers inside the hull against moisture ingress, strengthens all the joints inside the hull whilst also providing some degree of protection to the mix against sunlight by having an ultraviolet (UV) inhibitor within it.
Given the amount of sanding dust in the workshop at present it will be preferable to undertake this coating the inside of the hull with epoxy out on the driveway of the cottage in order to reduce dust contamination of the finish. As the inside of the hull is quite an extensive and intricate area to cover in epoxy and we need to apply the coats of epoxy ‘wet on wet’ it will require getting a few folk to assist as well as doing it on a dry warm day with little wind. I am therefore currently waiting for a window of opportunity to pull the boat out of the workshop to do that given the weather is currently very unsettled. To add to the mix one of my daughters Jenny is getting married in four weeks, so you will appreciate the family are currently focussed upon that big day at the weekends running up to it rather than dad pleading to spend the day coating the inside of the hull with epoxy!
Fortunately there have been lots of other jobs on the boat that I was able to get on with in the sanctuary of the workshop away from all the wedding craziness but more about that later in the update. First we must resume where we left last month upon the task of fabricating the two jet pipes for Longbow’s twin jet engines.
I gave our good friend and expert welder Steve Charlesworth a call to let him know that our welding sponsor ESAB was struggling to source appropriate TIG rods for welding the specific grade of Nimonic alloy our jet pipes were made of. In order to move the job along without unnecessary delays Steve’s solution to that was to make his own welding rods from surplus pieces of the original jet pipe so he could at least have confidence that the material he was introducing as a filler matched that of the parent metal.
The next thing Steve had to do was cut the front connecting flanges off the rest of the jet pipes as they were currently welded on at an angle of three degrees, whilst for our application in the boat we needed them to be straight. You can see in the following photo the difference in height from one side of the jet pipe flange to the other once Steve had it on his machine table that is a level datum and then with it removed.
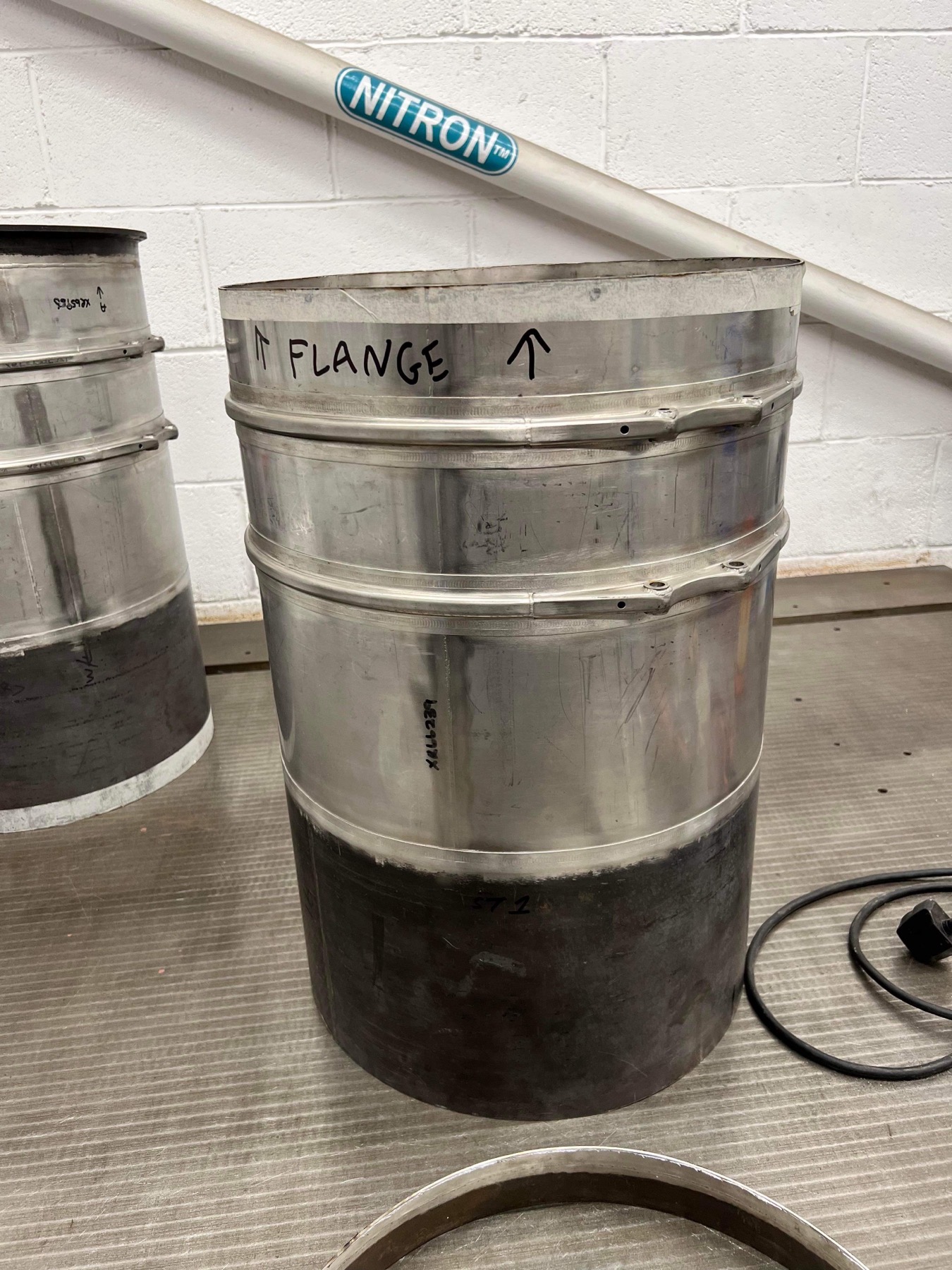
The next little headache was the minimal thickness of only around 1mm the jet pipes are made of which means the material wants to buckle and distort the moment you introduce heat as you weld it. In order to combat that Steve asked me to draw up and have laser cut two sheets of aluminium that when bolted together would act to keep the jet pipe circular during the welding process. The aluminium the ring was formed from would act as something of a heat sink whilst also having a hole in the middle rather like a big polo mint to allow Steve to reach inside the pipe at the same time. The following photos show the aluminium former we had laser cut at our sponsor WEC in Darwen and it being used inside a section of the jet pipe by Steve.
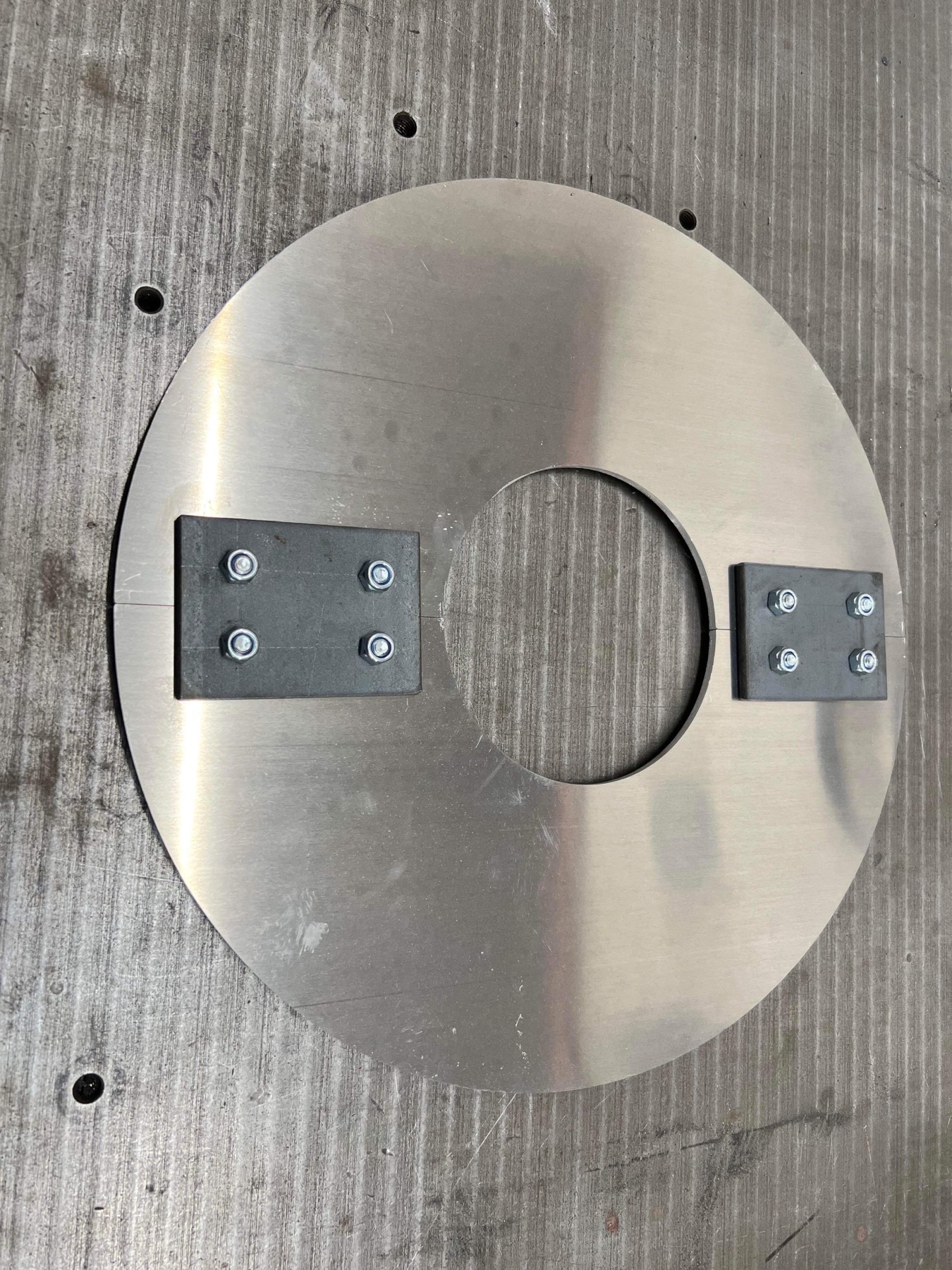
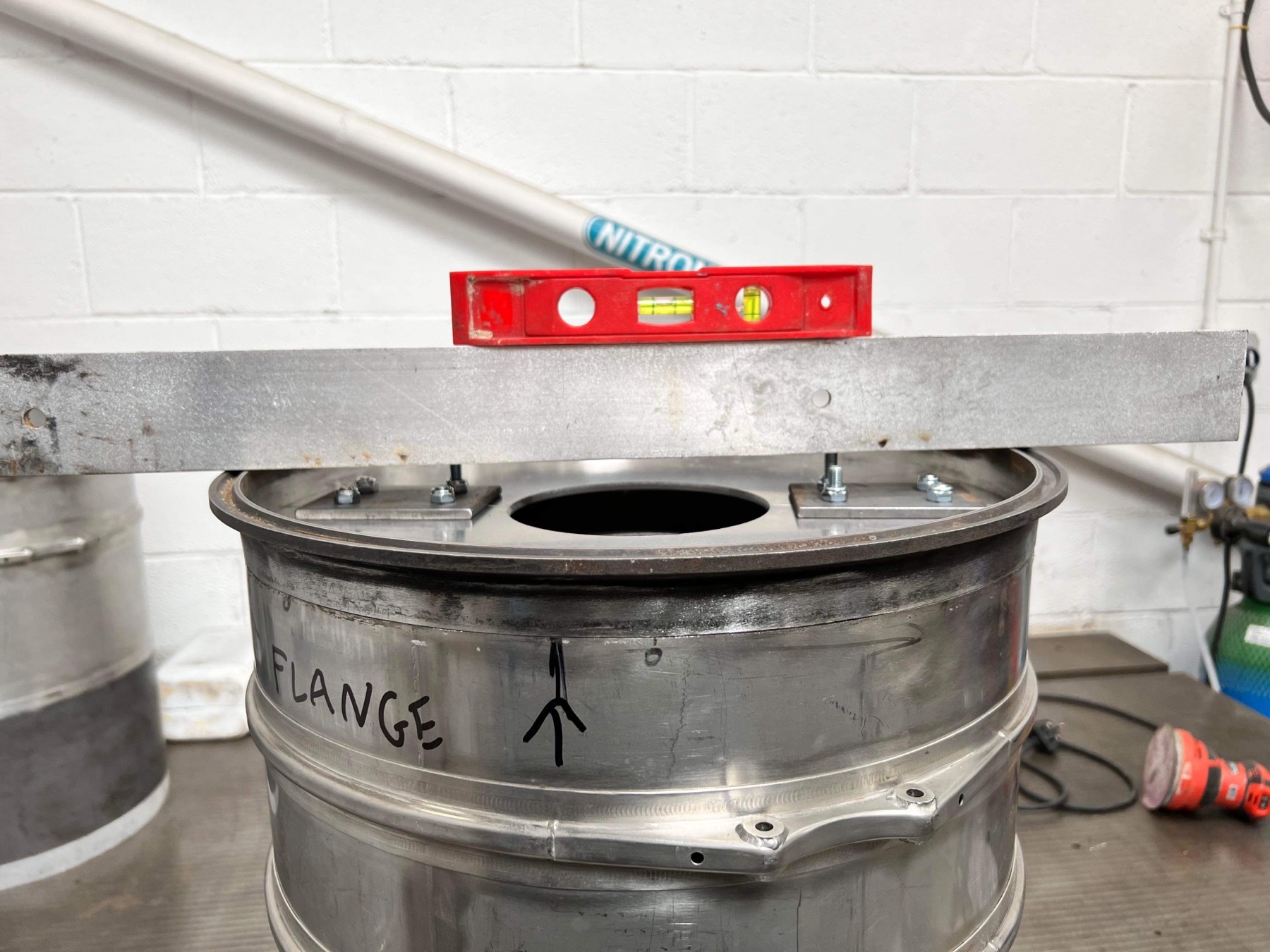
The original long length of jet pipe had been originally fabricated by welding several short sections of jet pipe together with one section sleeved inside another and the next section sleeved inside that then so on over the length of the pipe for the aircraft. Imagine it rather like a long telescope where each section is 2mm smaller diameter than the next but where we now only wanted each end of the telescope. You will appreciate that you are then faced with trying to weld together bits of tube that are definitely not the same diameter which meant Steve had to then shrink the larger sections down to meet the smaller ones before he could weld them together.
Now he had managed to do all of that Steve’s next problem was the threaded entry points for the jet pipe thermocouples that are welded into the original jet pipes.
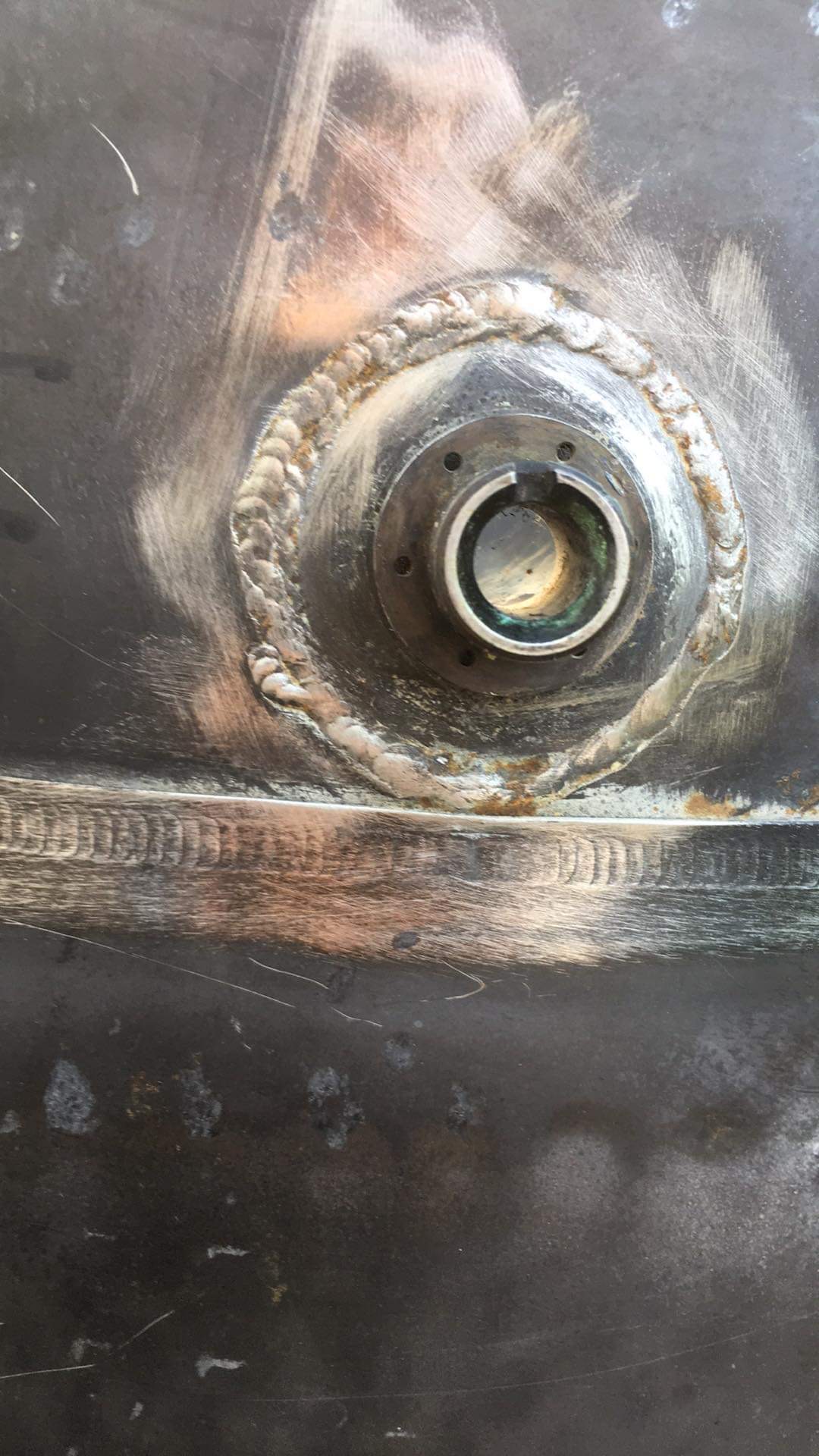
Where they were originally located was close to a bend in the jet pipe and as stated previously we could not retain any bends we needed the jet pipe to be straight and shorter than the original pipe. There are four thermocouple entry points into each jet pipe and Steve had to cut them all out then cut four new holes in each jet pipe to re-weld them into place.
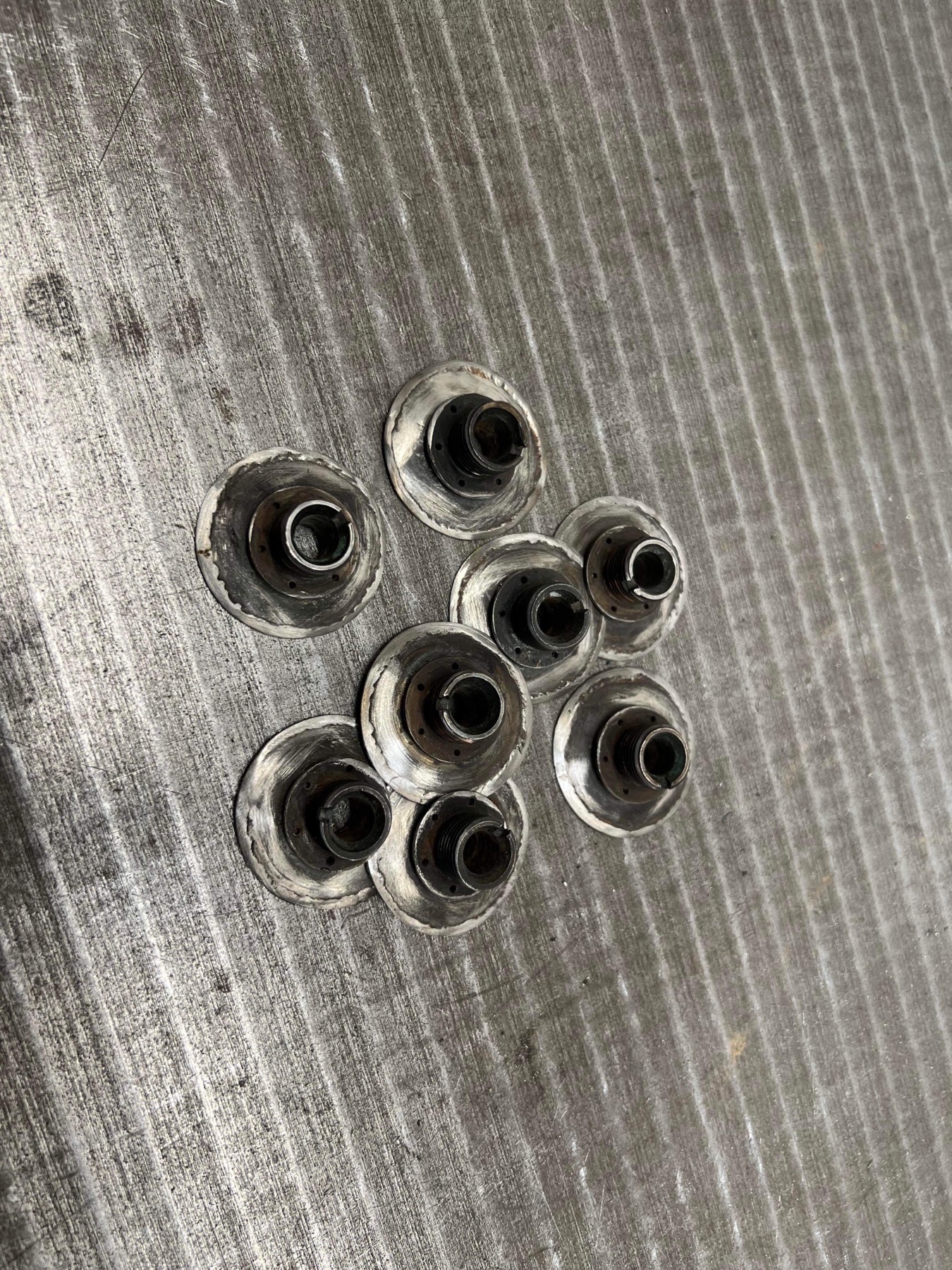
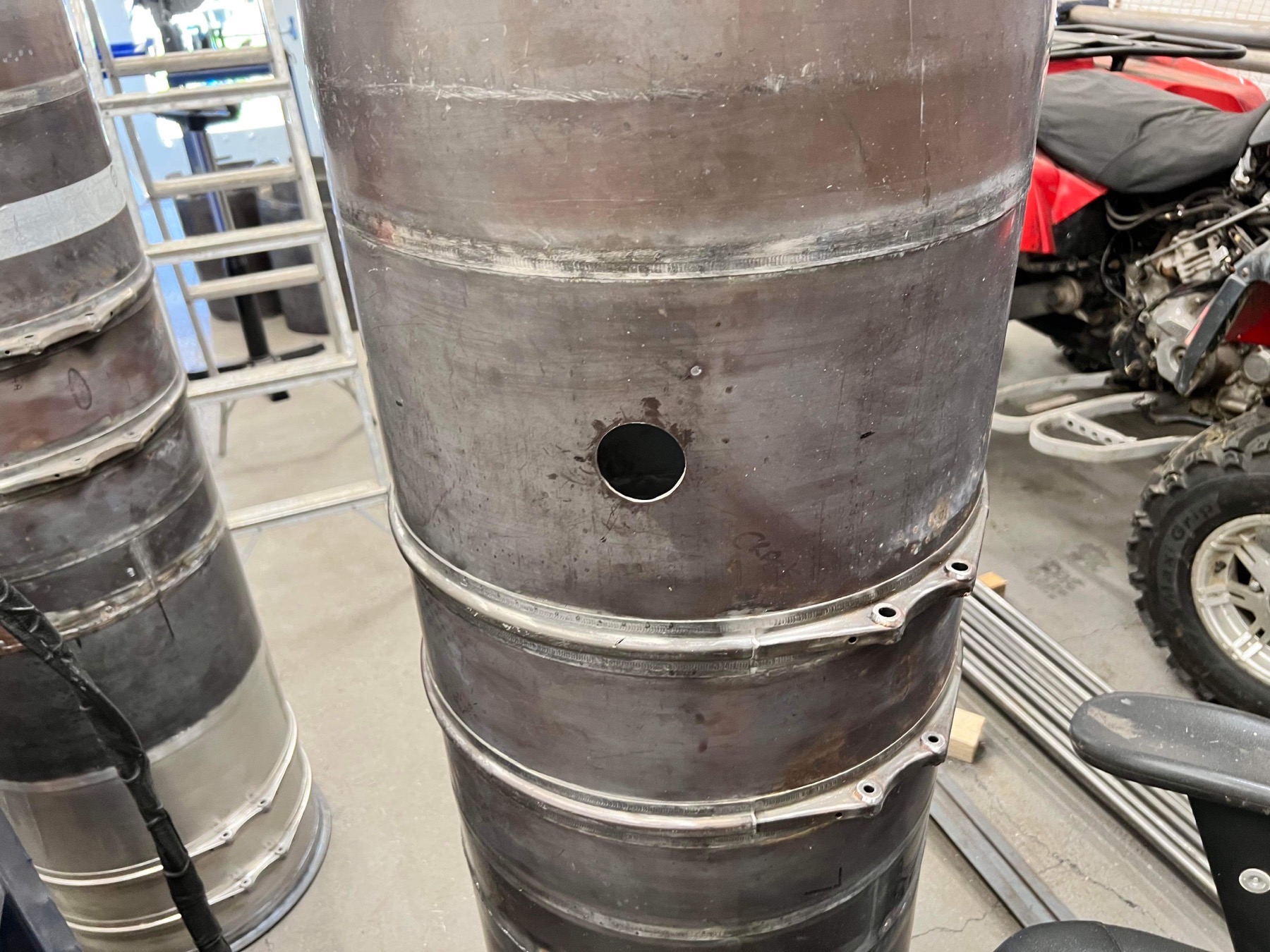
The fun part here was Steve’s arms were not long enough to weld the inside face of where these threaded mounting points are located and it was impractical to fill the inside of the jet pipe with Argon shielding gas. Steve’s solution to this was to make a temporary aluminium backing plate for inside the jet pipe and bolt it up through the thermocouple mounting point as shown in the photos below.
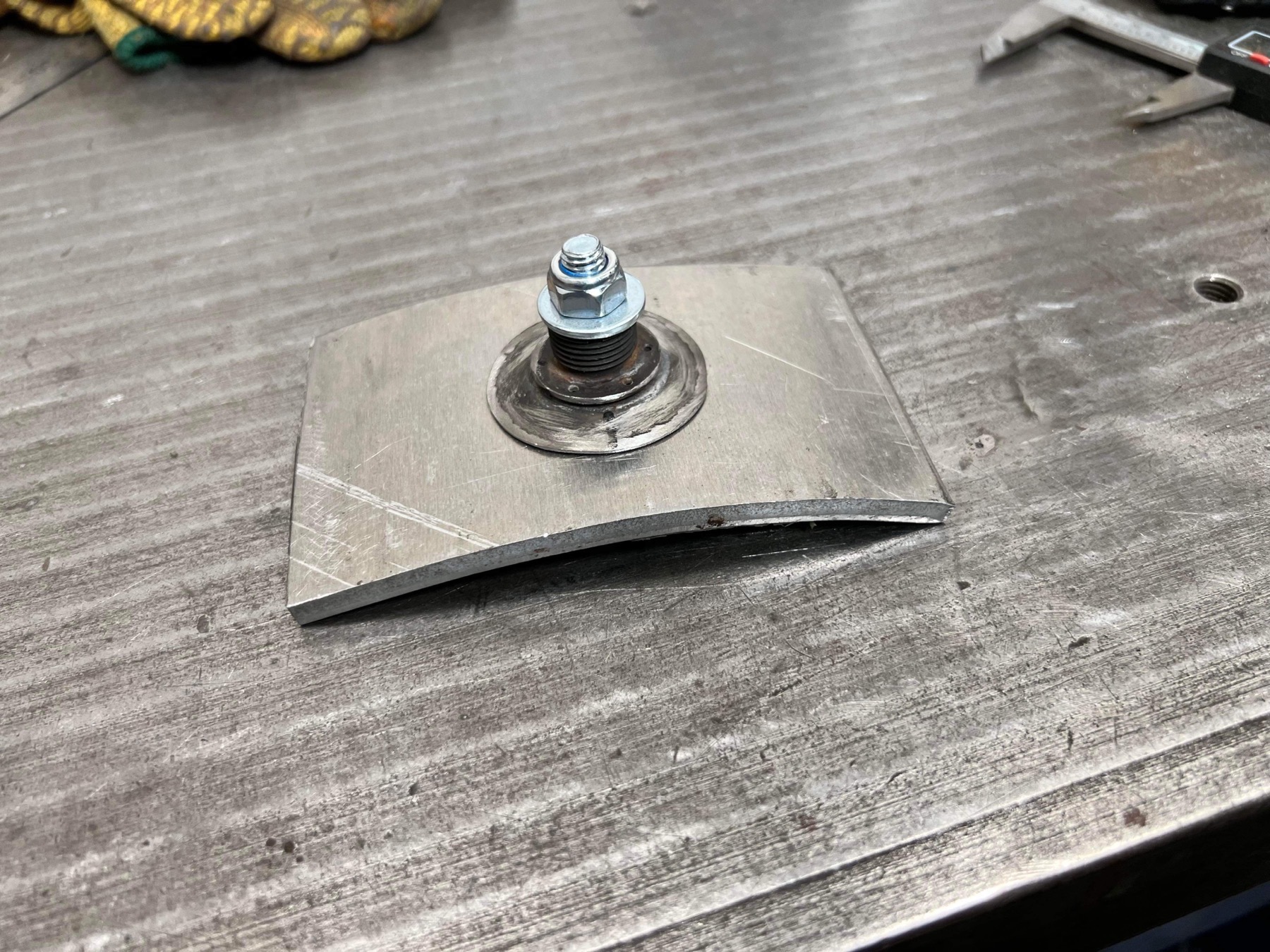
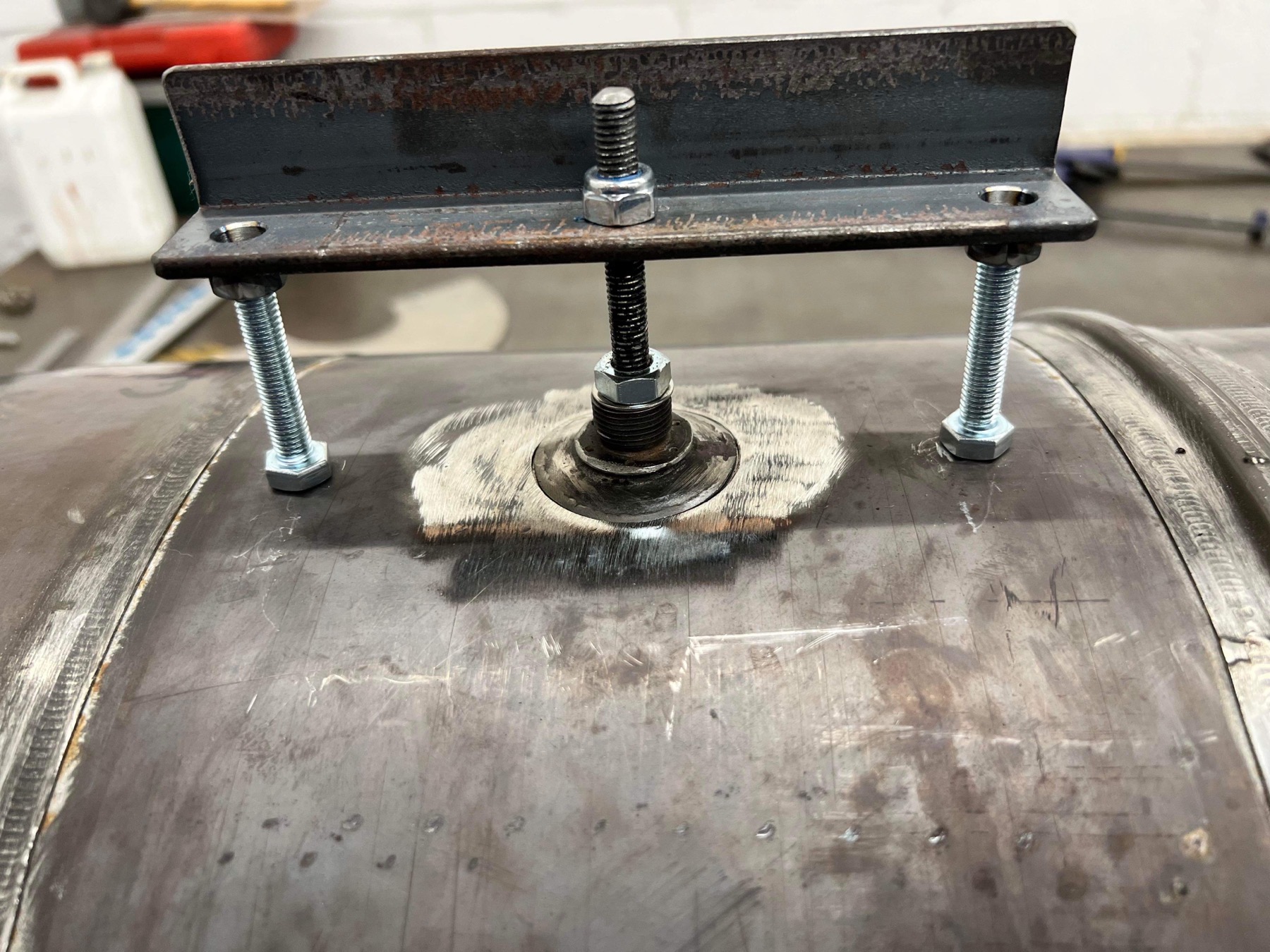
The aluminium acted as a heat sink to reduce distortion of the weld and kept air from contaminating the weld inside the jet pipe whilst he welded the thermocouple mounting plate using argon shielding gas on the outside and his filler rods made from waste jet pipe material. The photo below shows the backing plate removed after the weld.
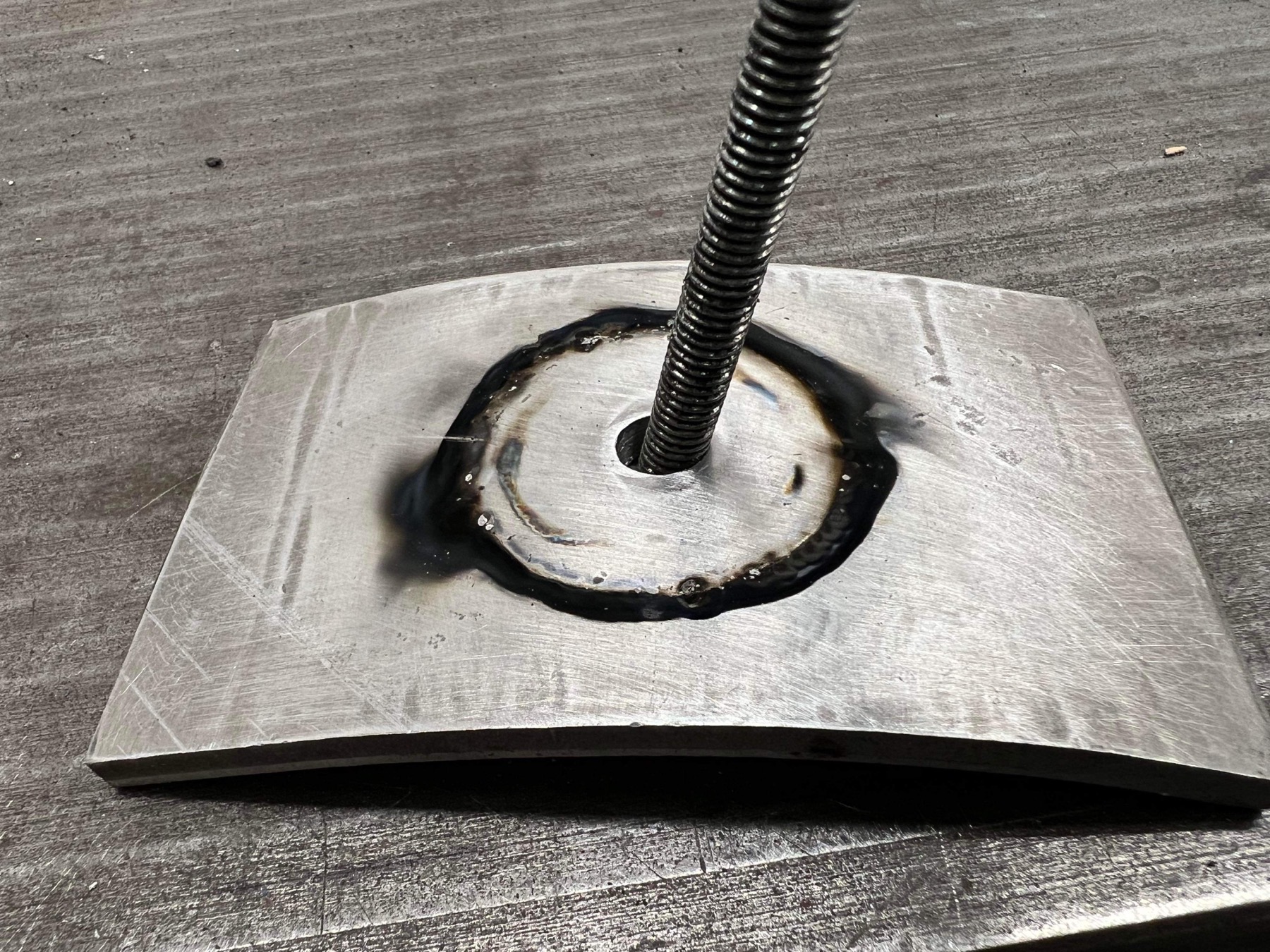
After Steve had done that on all eight thermocouple mounting points (four for each jet pipe) noting they all had to be orientated the correct way for the notch that locates the thermocouple in the right direction to the jet stream, he then applied dye to test all the welds before calling me up to say the jet pipes were all done and ready for collection.
Steve is his own worst critic and said would obviously have preferred to use purpose made TIG rods specific of the right size for the grade of Nimonic alloy he was dealing with as that would have given a more consistent sized weld puddle than using hand cut strips of parent material as the filler rod, plus in the case of the thermocouple mounting points he was having to weld close to material that had been previously welded. However I think you will agree it all worked out very well indeed and that is why you go to a time served Coded welder with a lifetime of experience for critical items such as this and the engine cradle on Longbow. We would have been lost without Steve’s ongoing help in making the venture happen and we cannot thank him enough for all that he does for us, a cracking bloke, great friend and absolute star.
The following photo shows the jet pipes ready for collection along with shielding gases as always kindly supplied by our sponsor Alan at SGS Gases and our sponsor ESAB for supply of their terrific AC/DC TIG welder.
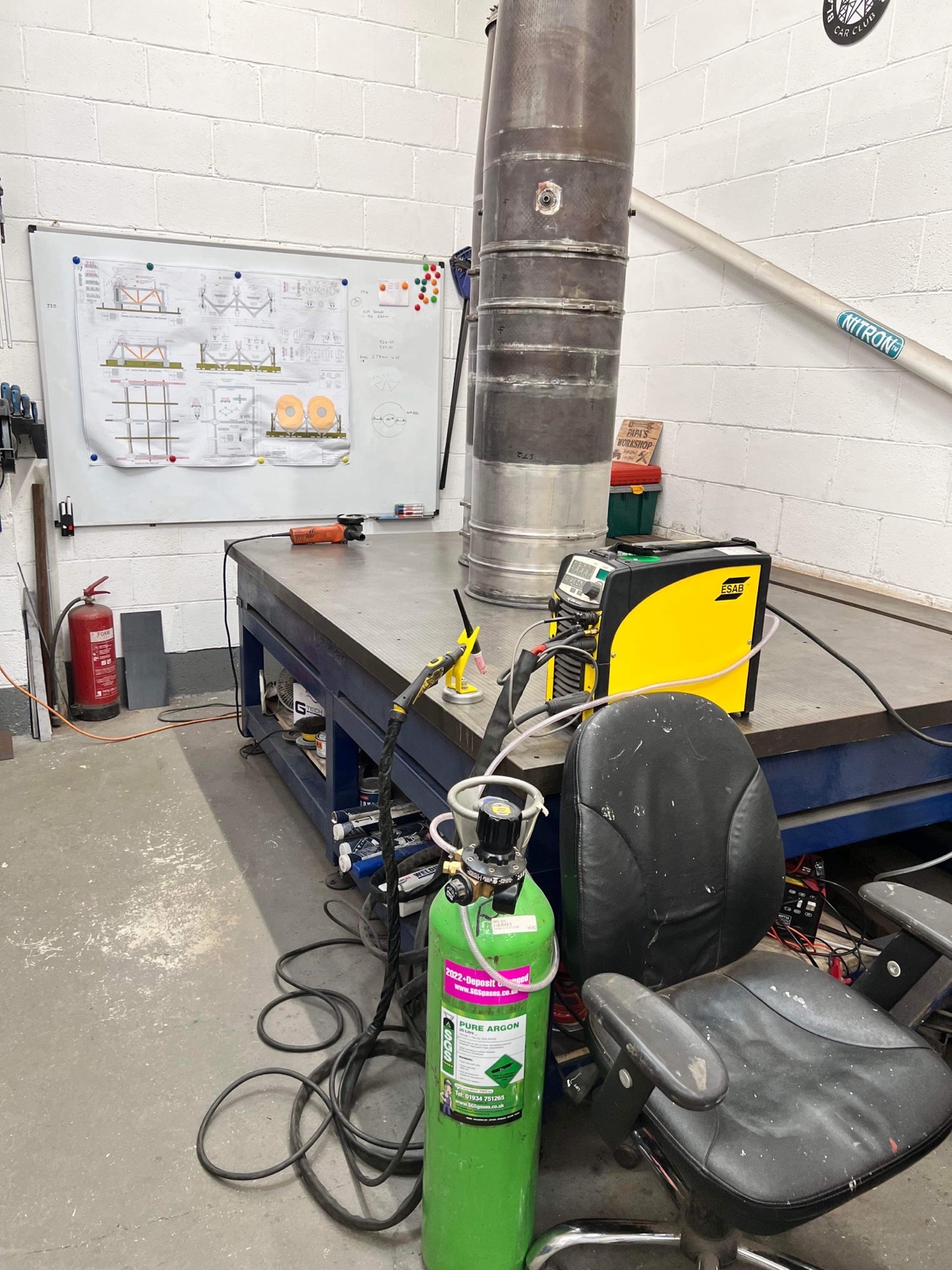
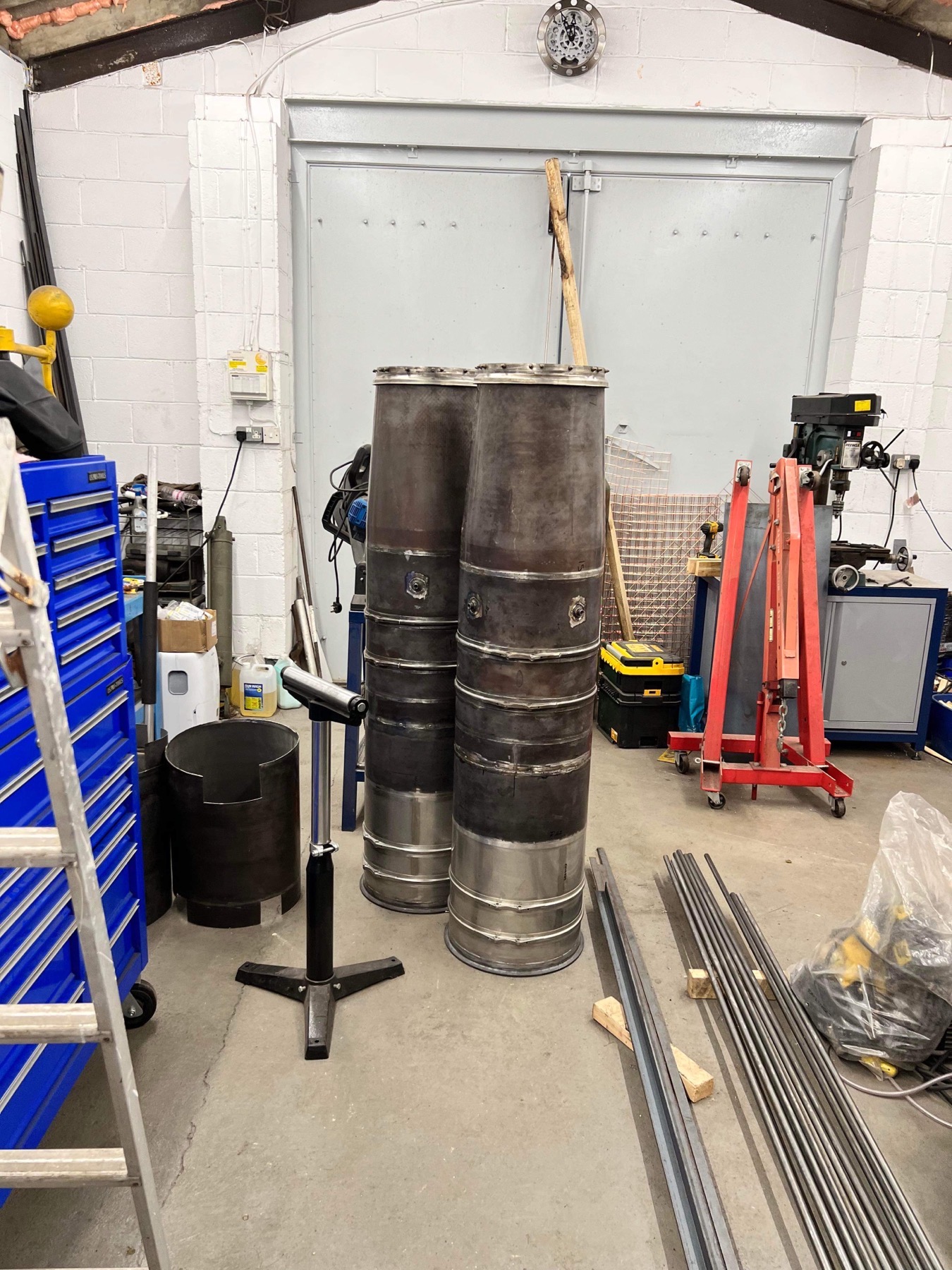
Back with the hull of Longbow the next job on the to do list was to commence forming the tops of the sponsons which are attached floats on either side of the boat up at the front. The ribs to these sponsons are a series of frames that I had previously roughly cut to shape but now they all needed sanding and lining up to their final shape so that the outer skins of the sponsons tops when fitted would flow smoothly.
Once the sponsons frames were aligned I could then cut and shape sections of plywood for the very front nose of the sponson tops and cut additional notches out of the frames to receive timber battens that outer covers would later fix to. On the side of each sponson I also had to cut and shape infill sections of timber to receive the bottom edge of the sponson covers to provide a continuous solid backing fixing point.
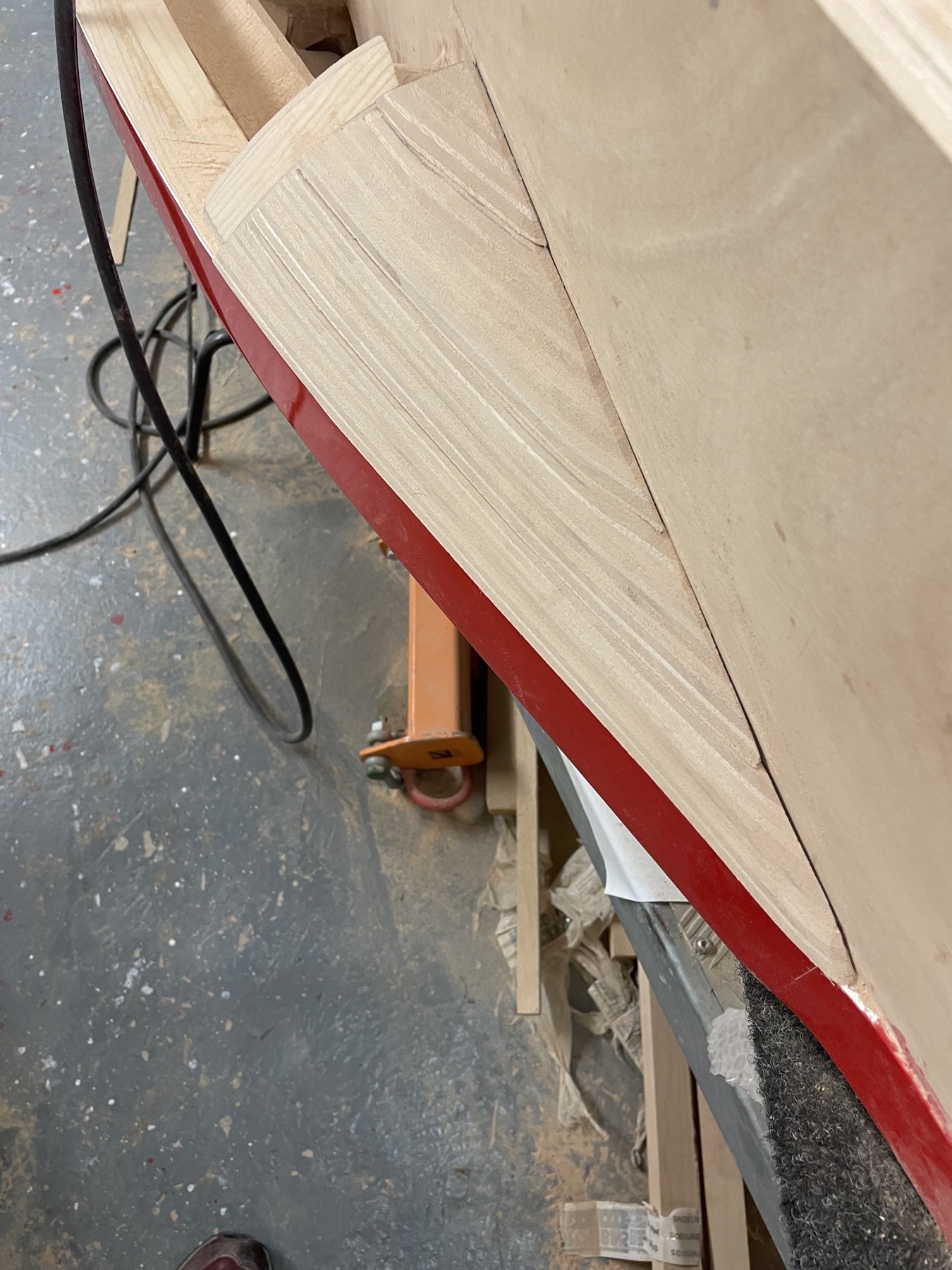
For the battens to the sponson tops these change angle most acutely at the front of each sponson which is beyond the 2-3% limit of bend before breaking that you could force the battens into as dry stock material. The tried and proven solution is to soak the timber battens over a couple of days and then steam bend them in a purpose made box that supports the wood on a series of dowels thereby allowing the steam to penetrate the wood over its full length and depth.
The following photos show the black plastic soil pipe laid on the lawn into which the timber battens are placed then filled with water for soaking, then our old and well used steam box into which the battens are then placed and the steam introduced. Vent holes prevent the box become excessively pressurised with steam whilst providing a visual indicator that all is working as it should.
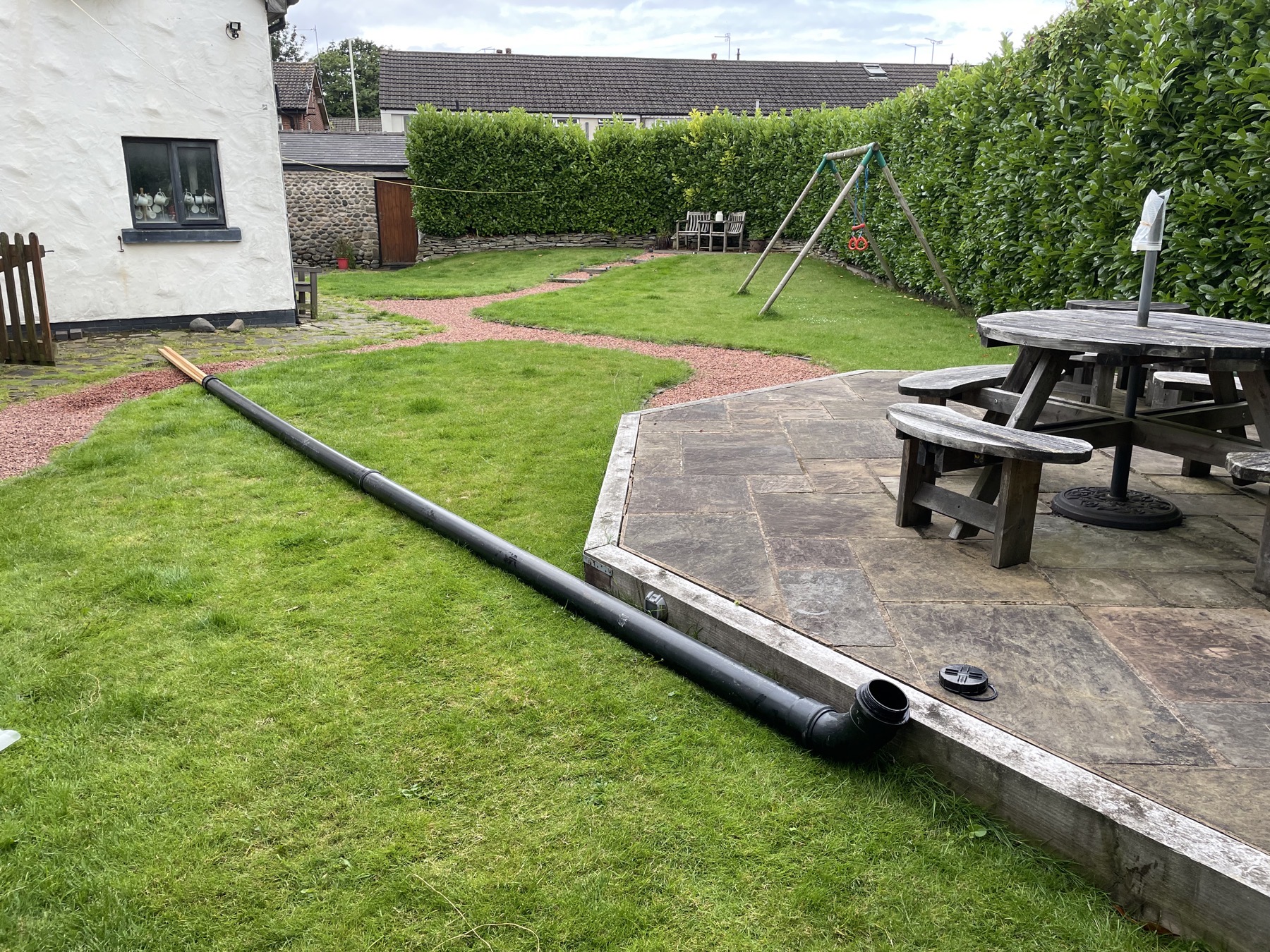
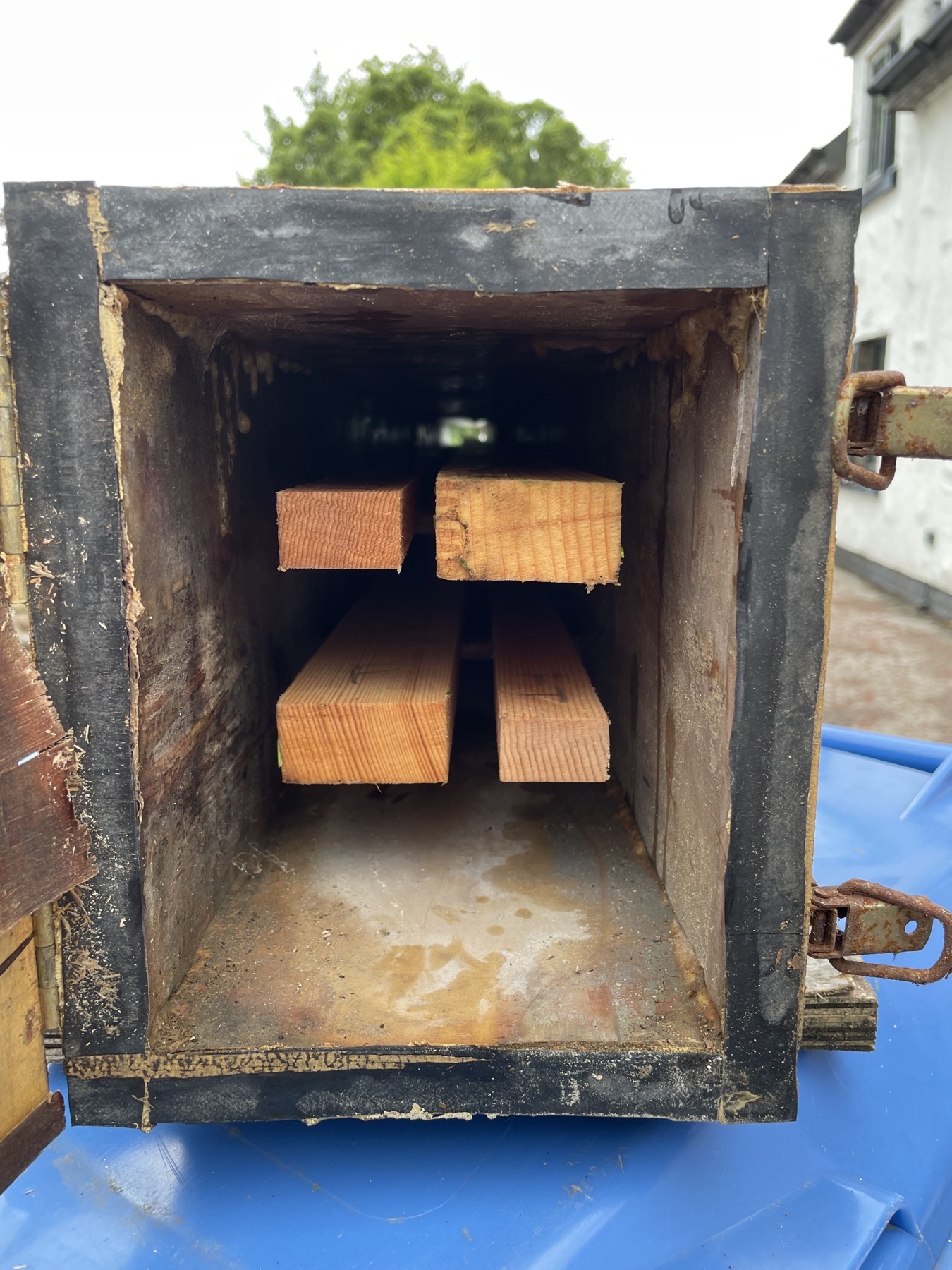
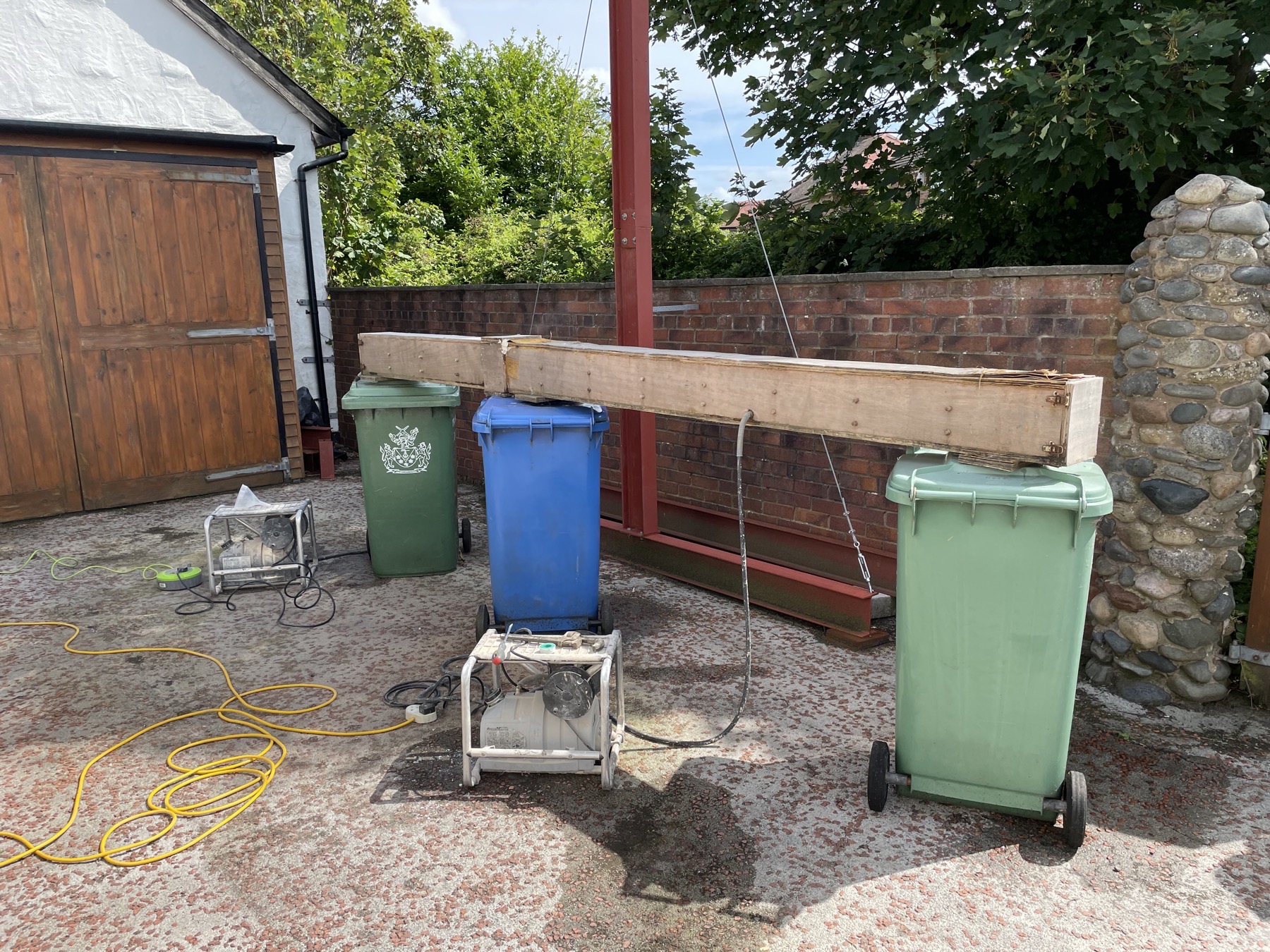
With this process the previously wetted out wood is kept at over 100ºC for a period of at least one hour per inch thickness of material whereupon the lignin in the wood softens allowing the molecules of it to deform in the cell walls for a few seconds after removal from the steam box so in this state the wood can be bent and twisted far more acutely than otherwise would be possible. Generally with this process it is more the inside of the curve that can be compressed as opposed to the outer face of the wood being stretched but nevertheless it works very well. The following photo shows my good lady wife Gill assisting with the steamed battens clamped into place by our sponsor Sealey Tools superb reversible F clamps for a couple of days allowing them to dry down and retain their newly bent shape with minimal spring back.
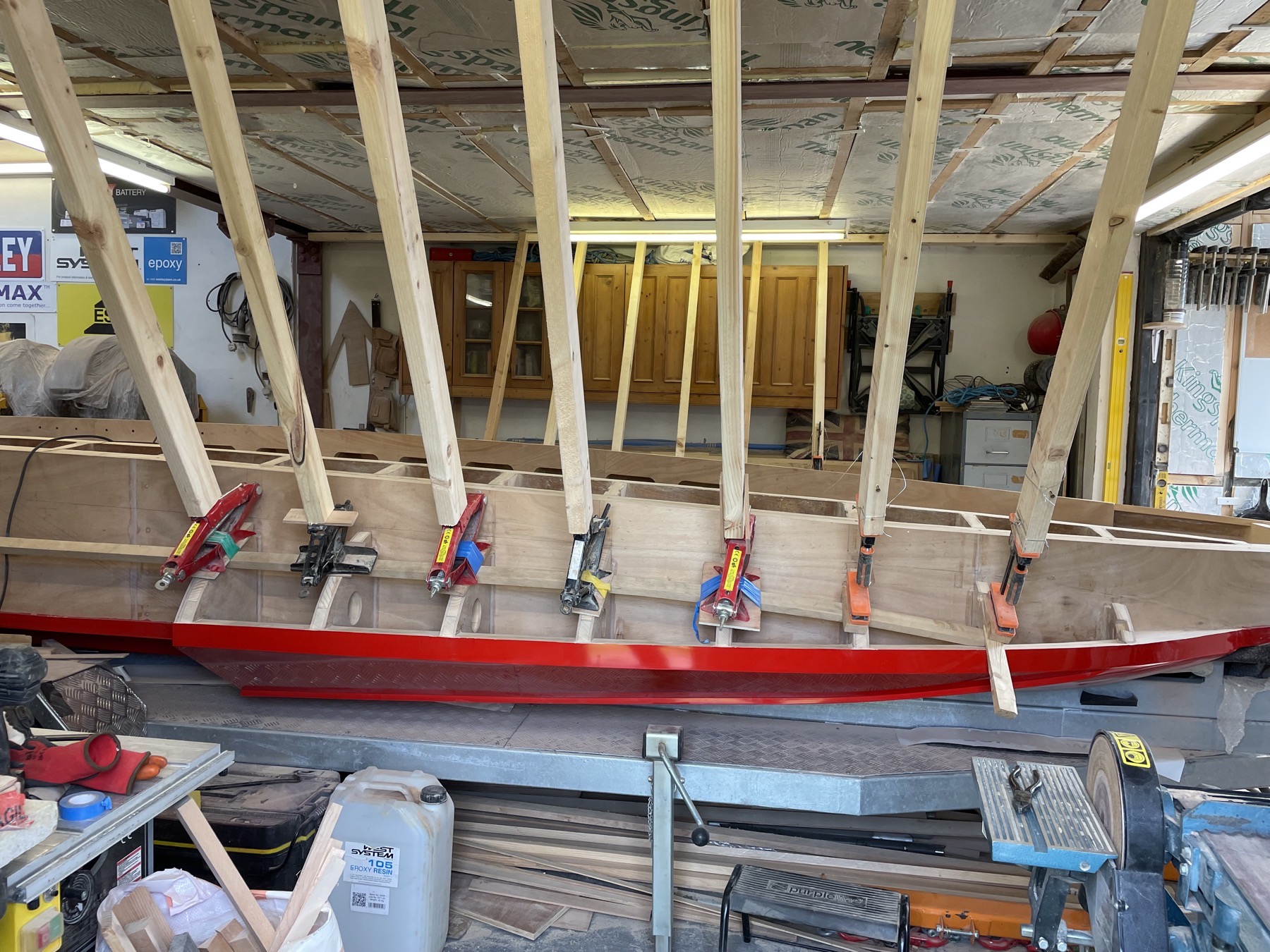
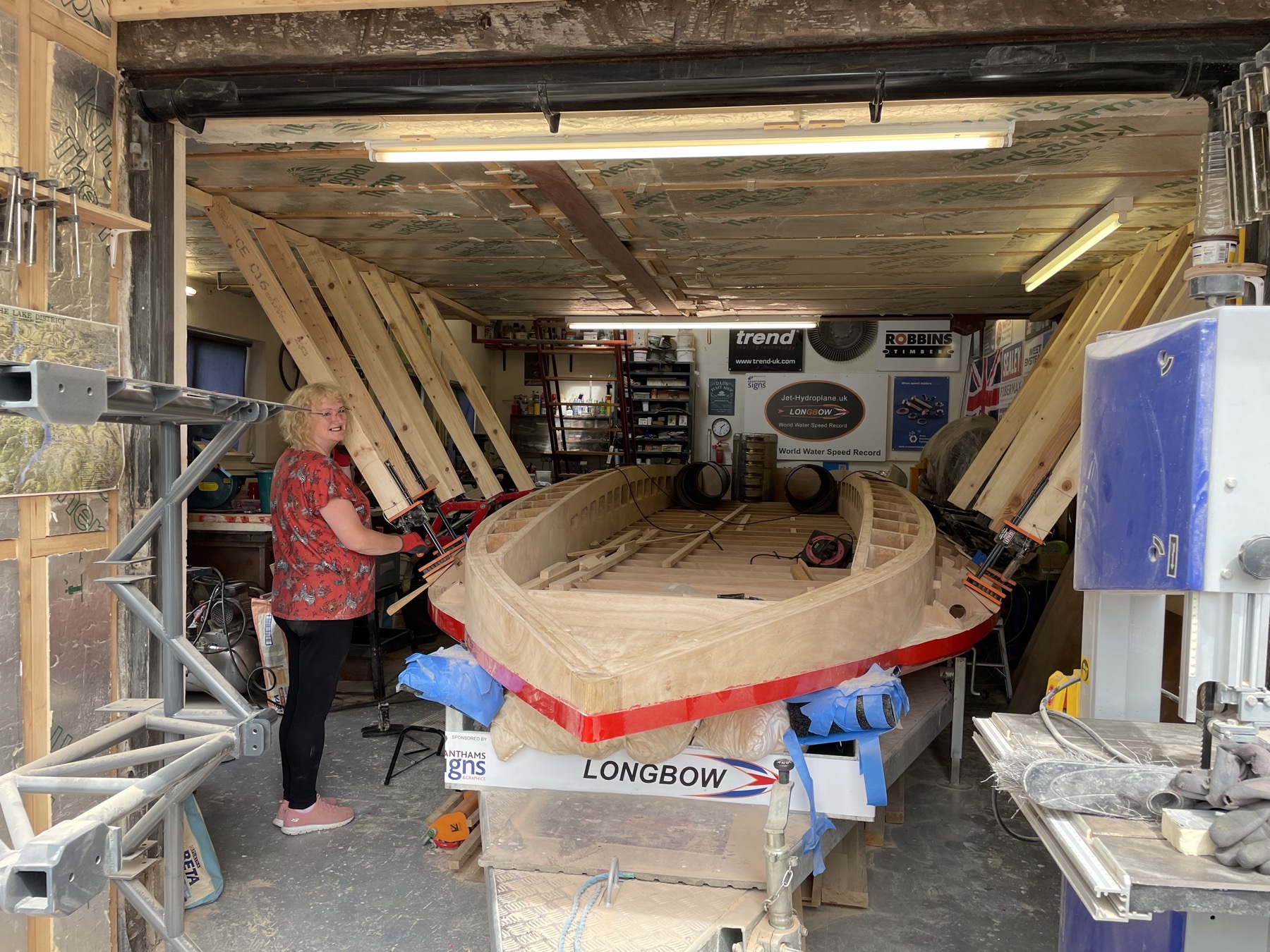
In order to fix the battens and laminate plywood nosing we used the WEST SYSTEM EPOXY mixed with their 403-3 new formulation microfibres adhesive filler material which combines to form a bond stronger than the wood itself.
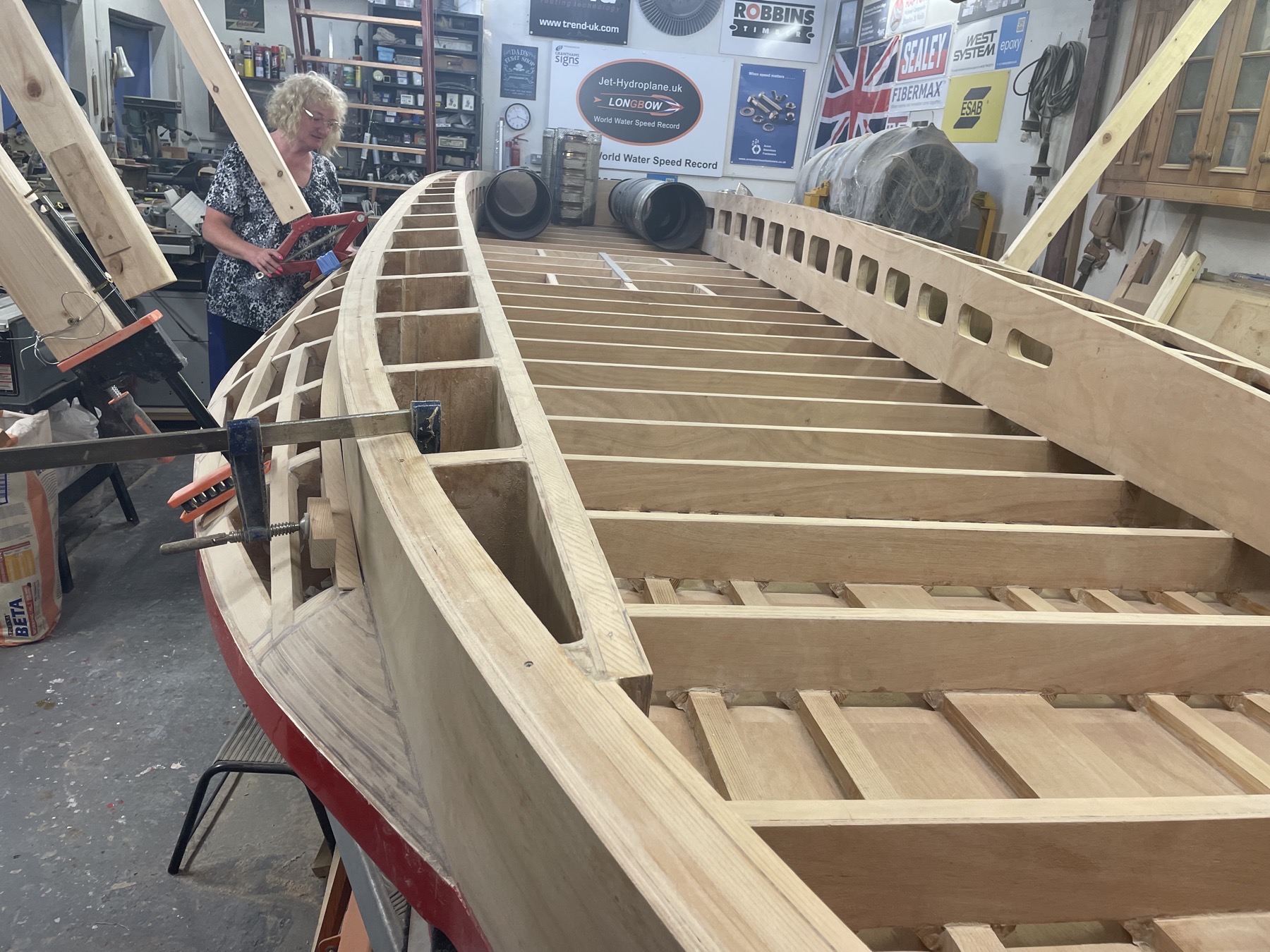
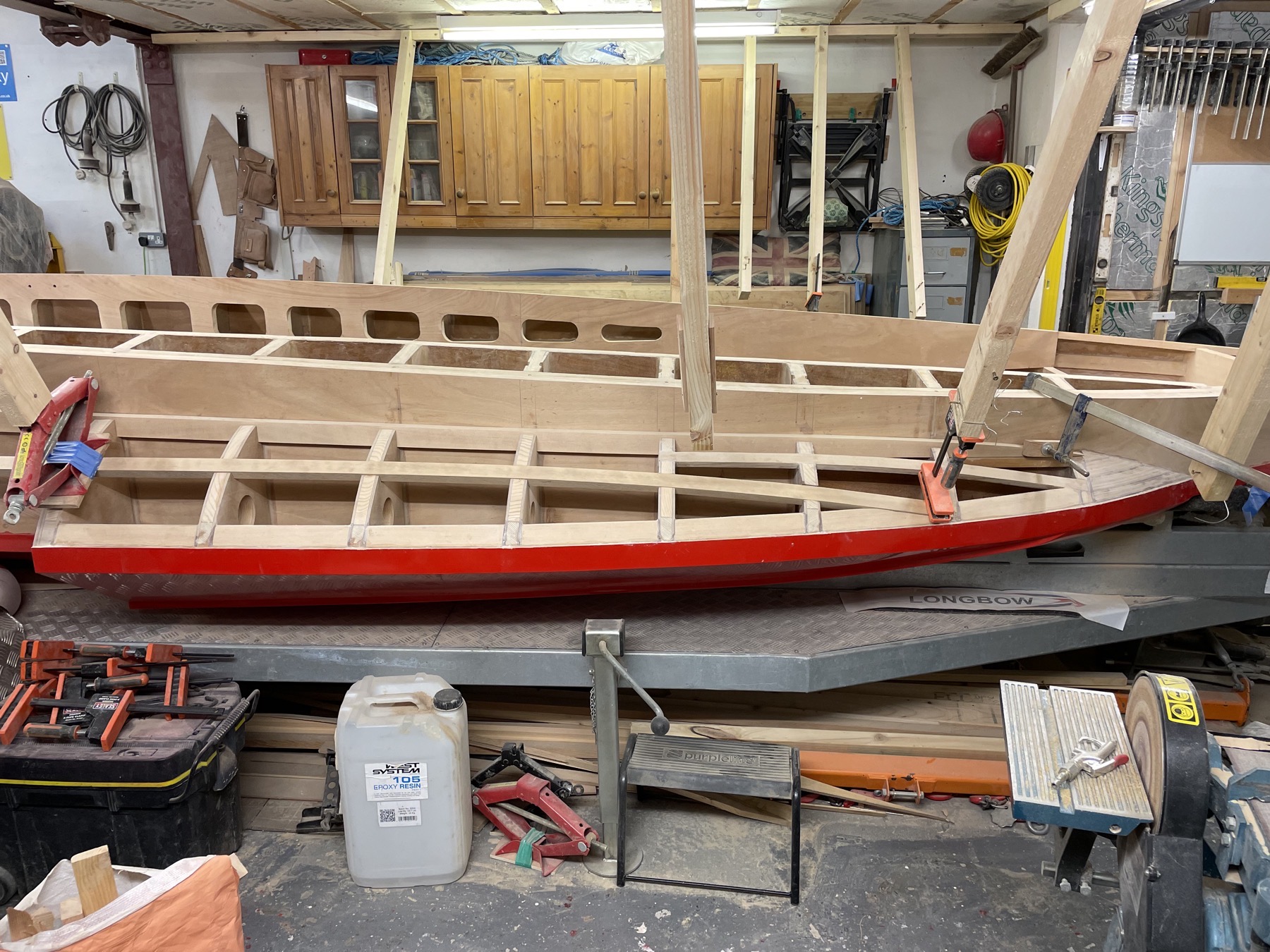
The sponson tops and rear of sponson need further work before they are complete but I trust that you can now see them starting to come together now.
Well that is all for this month’s update folks and hope I have not bored you too much with this particular update. If you have not done so already please take a moment to like our Facebook page and drop by towards the end of next month for the next update on progress as we build our jet hydroplane Longbow to run and develop upon lakes and lochs within the U.K.