Welcome to the latest update for Longbow as at last the warmer weather of summer appears to have arrived here in the U.K.
As mentioned in the last update our design engineer Paul Martin was in the process of doing analysis for us on the cockpit for Longbow in relation to the forces that it would have to endure in the event of the craft coming to grief at speeds at and in excess of the current Outright World Water Speed Record of 317mph. Obviously the approach to the venture is not to have a crash in the first place but it would be reckless on our part if we did not consider and design for such an occurrence.
When we looked at this at the outset of the venture we approached Robert Martin of Martin Baker who have been manufacturing ejection seats for many aircraft throughout the world since 1946, to enquire whether they would partner the project by way of supplying an ejection seat for the pilot. Robert was very supportive of the venture and yes and they did manufacture an ejector seat that could be deployed from ground level.
However in our case there were issues of vibration that may deploy the seat inadvertently. Also as you may appreciate we could not guarantee the orientation of the seat being deployed would be upwards in the event of an accident such that there was an inherent risk the seat could be deployed at an angle that propelled it into support craft / the shoreline with the public in attendance and also the possibility if the craft was inverted at deployment that ejection would propel an unprotected pilot at over 300mph straight down into the lake with fatal outcome.
Lastly there was also the significant cost and program of development that would be required from the company to tailor and technically support one of their ejector seats specific for our application. For all of these reasons the option of using an ejector seat within Longbow became as you may appreciate a non starter.
Options for driver cockpit then really fall into two camps of either you retain the cockpit as an integral part of the hull or you design the cockpit in such a way that it is ejected from the main hull in the event of an accident. Many circuit racing hydroplanes with enclosed cockpits have that cockpit permanently fixed into the main hull. Indeed the H1 Unlimited class hydroplanes are built this way but with a trapdoor in the bottom of the cockpit from which the driver can be extracted as a secondary means of exit to the main canopy, if an accident results in the craft floating upside down.
The key phrase here is if an accident ‘results in the craft floating’ because if the craft sinks with the pilot still strapped inside then it is highly likely that they would not survive for all manner of reasons considering the depths of lakes / lochs in the U.K. and the time that it would take for rescue divers to find the cockpit in those murky depths and extract the driver then take them to the surface.
In other hydroplanes such as top fuel drag boats in the USA, because of the very high speeds that they run at, experience has shown that the hull is often destroyed in the event of an accident or at least is damaged to the point that it sinks despite having some degree of onboard floatation, so they opt for the driver cockpit / capsule to be ejected from the hull of the boat in the event of an accident. That cockpit / capsule then remaining floating upon the surface of the water with the driver inside.
Considering the speeds Longbow if successful would have the potential to run at, we felt that we could not guarantee that post accident there would be enough buoyancy in what was left of the main hull to keep the driver on the surface of the lake / loch. That being the case we felt the best option in our particular case is to have the driver cockpit / capsule detach from the hull in the event of an accident. It is therefore the calculations involved with that occurrence that Paul has been working upon to ensure that the driver capsule is able to withstand those loads and remain intact and remain floating upon the surface of the lake / loch.
Paul has now completed his analysis of the roll cage element of the driver cockpit / capsule and that has gone off to Tom Stanley who heads the UIM Cockpit Safety Committee for confidential peer review. We anticipate there will be discussion back and forth between Tom and Paul over the coming weeks regarding that analysis, and taking that forward that discussion to include analysis for the outer composite shell of the driver cockpit / capsule. It is a time consuming process where you will appreciate it is dependent upon all of those participating in the technical discussion to set aside time in amongst their day to day work, other activities, holidays, etc to digest and discuss the subject matter but hopefully we will get there in the end with a solution that provides a practical way forward that everyone is happy with.
As elements such as steering, fuel tanks and air intakes for Longbow’s engines are all built around her cockpit, all we can do is remain on hold with the build of the boat until the critical design of the cockpit is agreed between Paul and the UIM Cockpit Safety Committee. You will appreciate that I am as frustrated as everyone else that we are not cracking on with the build of Longbow but we ask all those following and supporting our little venture to be patient during this period of technical discussion between Paul and the UIM until we are able to resume the build for the reasons stated.
We have not been completely idle regarding jet hydroplanes during this downtime and will reveal more of that in further updates in conjunction with the others involved. In the meantime here is a photo of us taking our spare engine out of storage for Longbow.
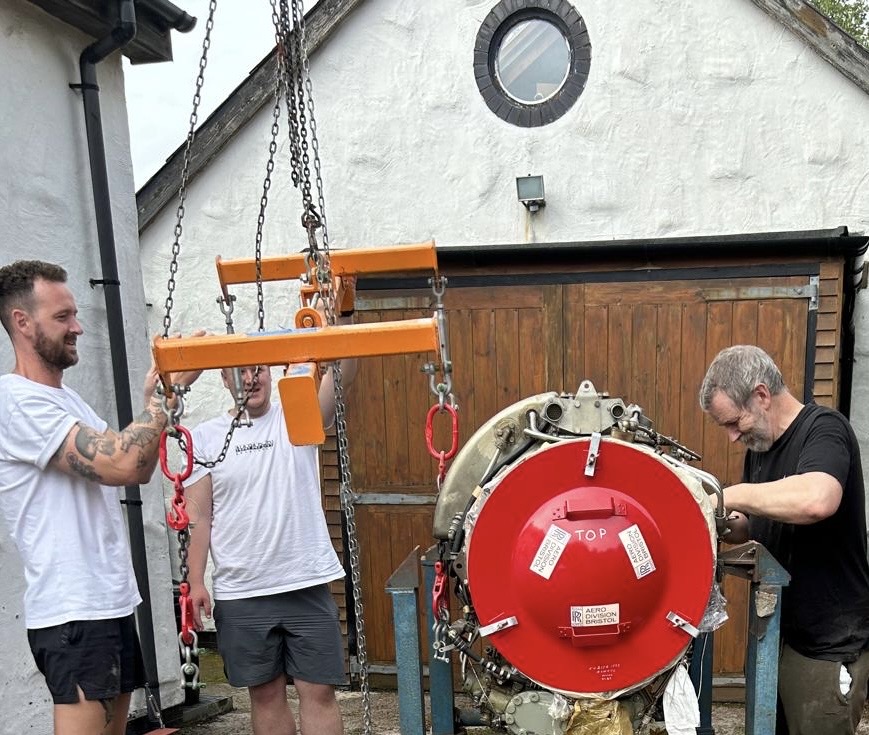
In the meantime we wish our good friend Dave Warby and his team every success in their return to Blowering Dam, NSW, Australia this coming weekend for further testing of their jet hydroplane Spirit Of Australia II and will report back in due course as to how they get on.