Welcome to my little March diary update for the venture and what a mixed bag of things this month has been. Kicking things off was the apprentices at our sponsor WEC Group in Darwen, who so skilfully fabricated the trailer for our jet hydroplane Longbow having to pull it all apart and send the steel framework off by haulier to one of our sponsors, Manchester Galvanizing Ltd. If you have never seen an item of this size being galvanised you may find the following photos and video taken by their Commercial Manager Mark Waters showing our trailer being rust-proofed of interest. A huge bath of hot molten zinc is obviously not something you would want to fall into but no doubt you each have your own candidates for those you would quite happily throw in if nobody was looking.
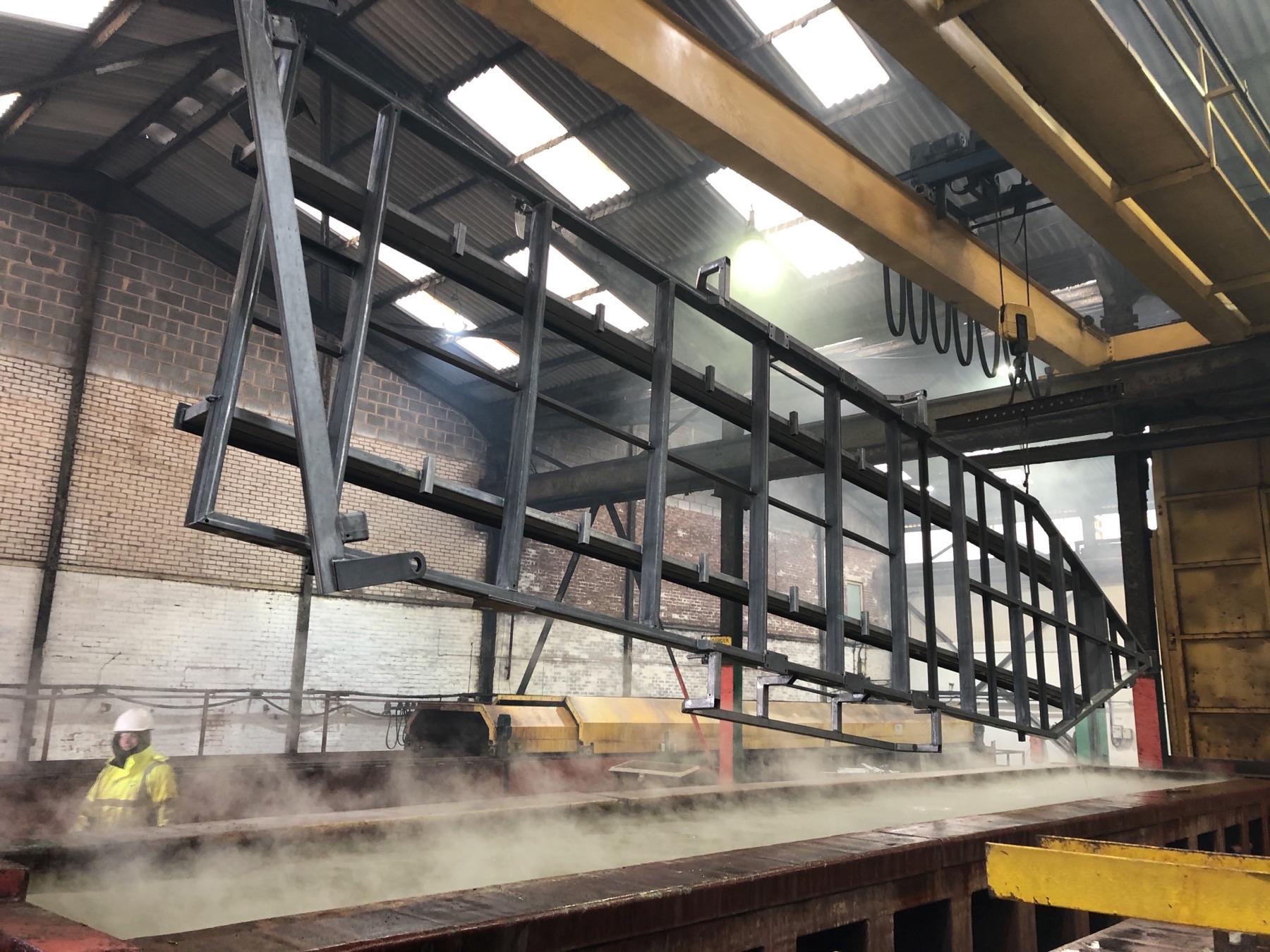
Once the galvanizing was completed the now gleaming trailer frame was then sent back to WEC for reassembly by their apprentices and the following photo shows their Training Manager, Kris Mercer and some of his apprentices who took part in the project for which we thank them and those that supplied product to build it so very much.
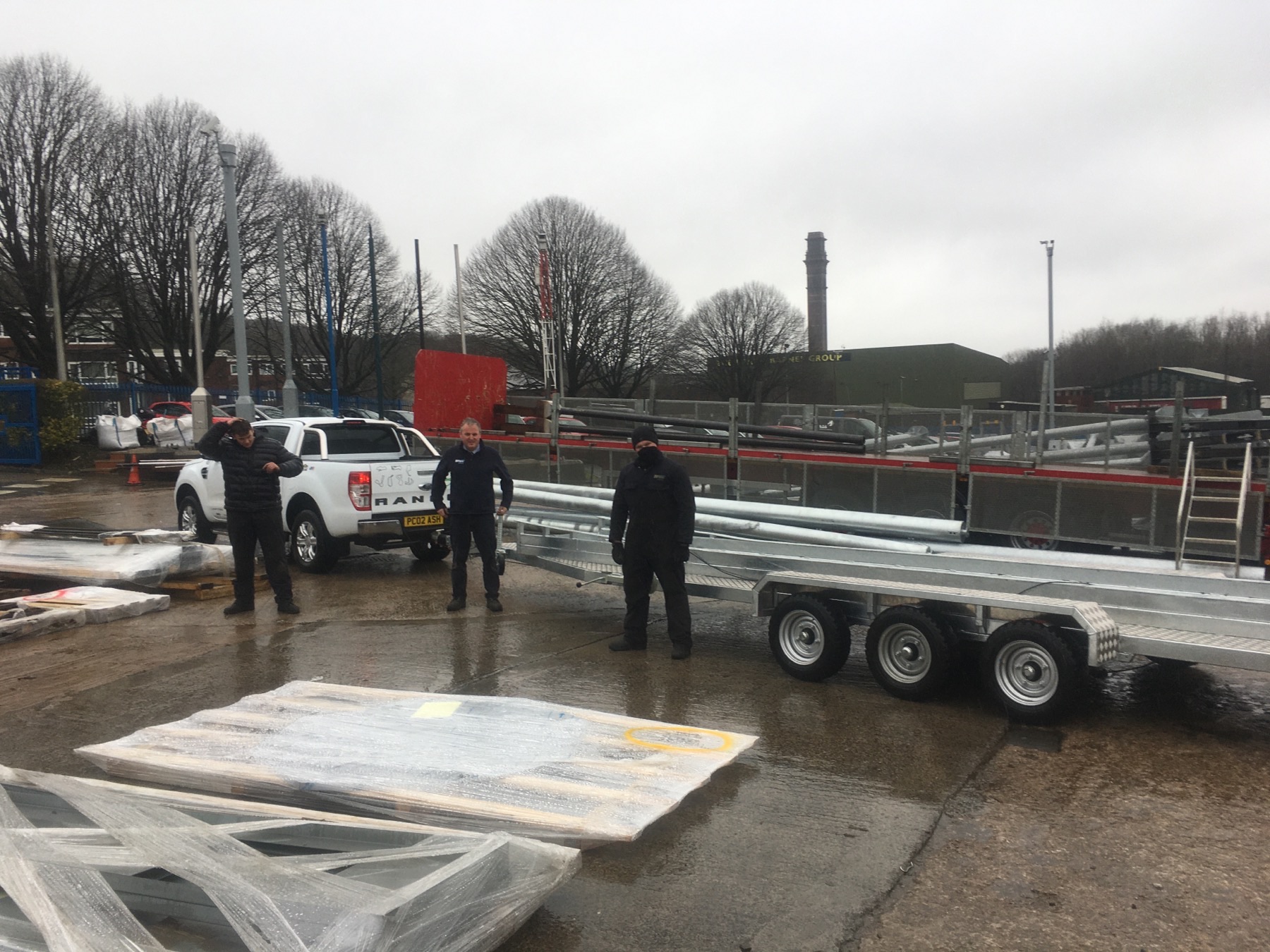
The completed trailer was then transported to my cottage workshop where we are building Longbow and thank you very much to my nephew Phil Ashworth for organising transport of the trailer to my driveway. At present the hull for Longbow is inverted upon the build table in the workshop and when the underside of the craft is completed we can then think about bringing her out of the workshop, turning the hull over and putting her on to the trailer. At that stage the build table can be removed and Longbow complete with trailer can then be taken back into the workshop for the rest of her construction to be continued.
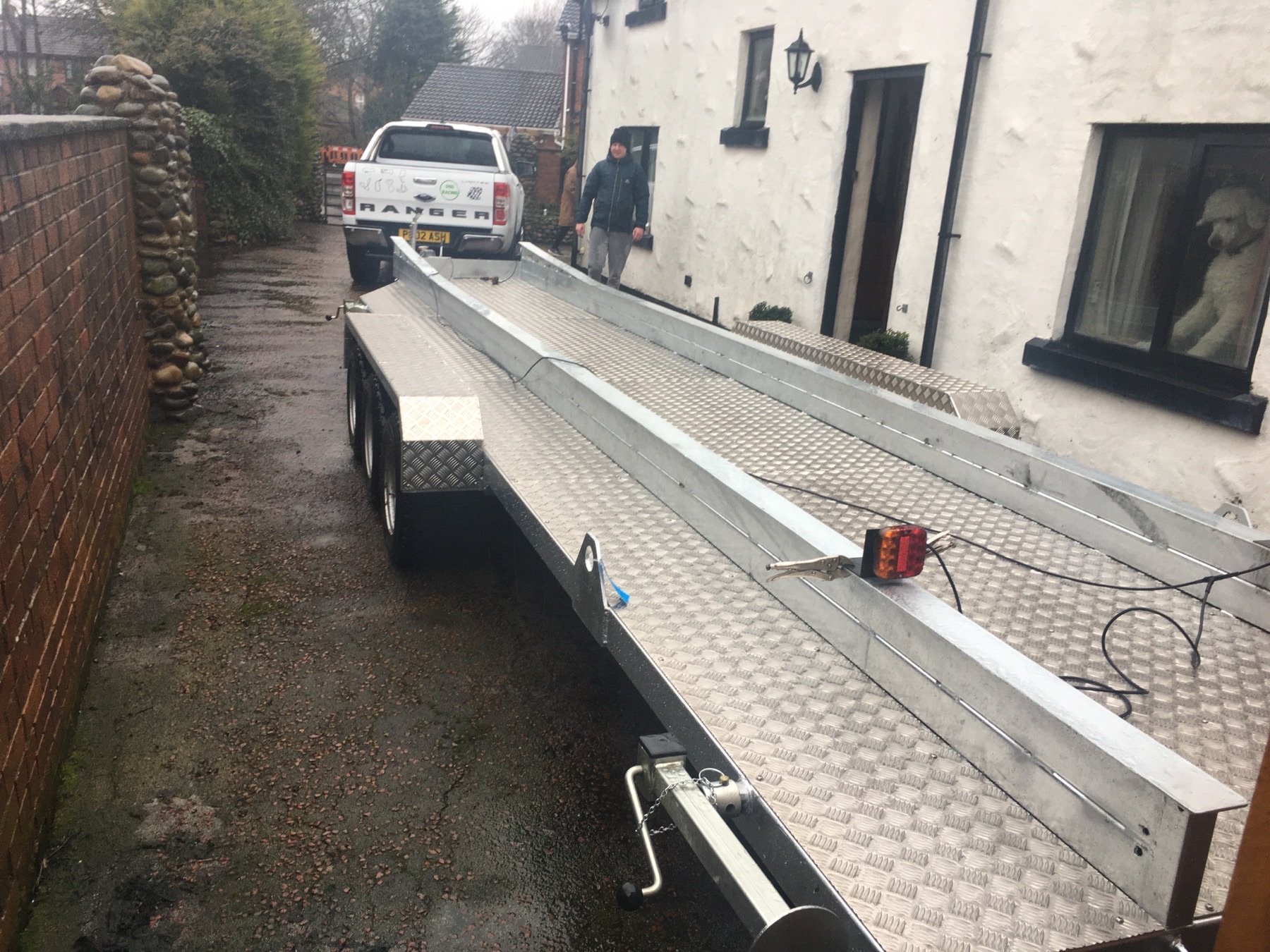
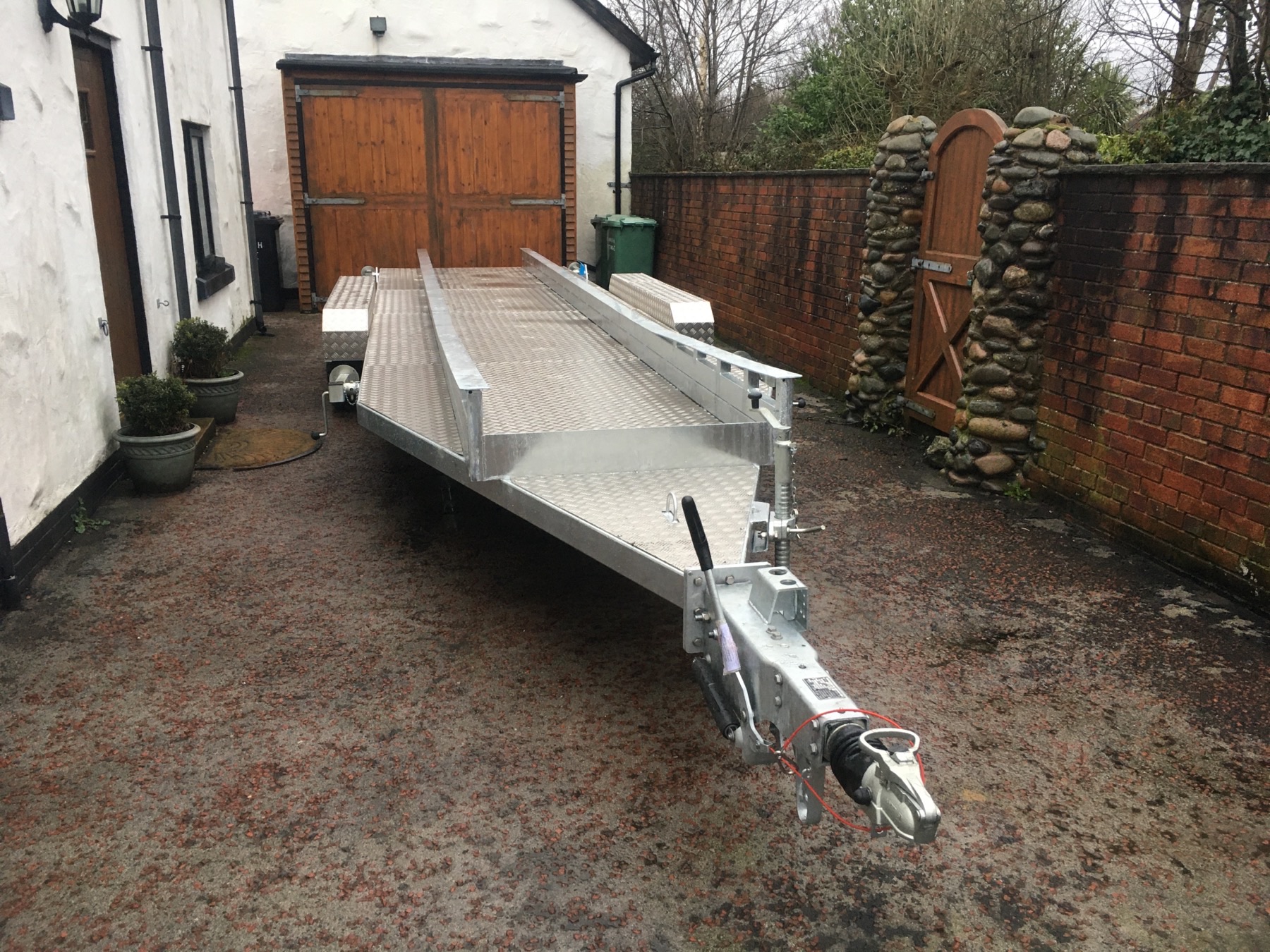
Having said in February’s diary update that I hoped the freezing winter temperatures were drawing to a close, the first couple of weeks in March plunged the UK back into ice cold weather which rather frustratingly held me up for using the WEST SYSTEM EPOXY from our sponsor Wessex Resins at the next stage of hull construction. All I could do during this unplanned cold weather downtime was to give the workshop something of a spring clean which was perhaps no bad thing given the amount of sanding dust from the hull build that had accumulated throughout the roof structure and everywhere else it had managed to find its way to settle upon.
Finally later in the month as the weather improved along with the heaters on full belt, the temperatures in the workshop came up to an acceptable level for epoxy work to proceed. We could then commence with the job of applying the Dynel fabric to the hull that we had sourced all the way from Australia thanks to our sponsor Colan.
Dynel is not to our knowledge manufactured in the UK or Europe. Similar sounding Dionel fabric is available in the UK but that is not the same thing as Dynel, so hence we had to ship the fabric from the other side of the world where they know a thing or two about jet hydroplanes.
Sometimes you can overthink a task and the subject of what fabric to cover Longbow’s timber hull in was for me certainly one of those moments that would keep me awake at night. My good friend Dave Warby in Australia had told me to just get on with covering the hull of Longbow in the Dynel fabric embedded within coats of epoxy as that was what he and his father Ken had used on their timber hull jet hydroplanes. It is certainly a proven product not only with their craft but thousands of timber framed racing hydroplanes across the world and indeed this has been the case for decades.
Not having sheathed a timber hull in fabric before nor indeed had much experience with composite fabrics I did consider using carbon fibre and / or Kevlar in addition to glass fibre be that E class or S class, rather than Dynel. Indeed we will be using a combination of carbon fibre and Kevlar to form the cockpit for Longbow so why not use them to sheath the outside of the timber hull? Well in the first instance no matter what fabric we sheathed the outside of the wooden hull with, if the fabric is only applied to the external surface, what you find is that under a test rig where you load a sample to the point of failure, it is the plywood element that fails first, then the fabric unable to carry the load on its own, fails pretty much instantly after that. This is clearly illustrated in the following test sample photographs albeit not marine grade plywood, for both carbon fibre and for a hybrid carbon fibre / Kevlar weave.
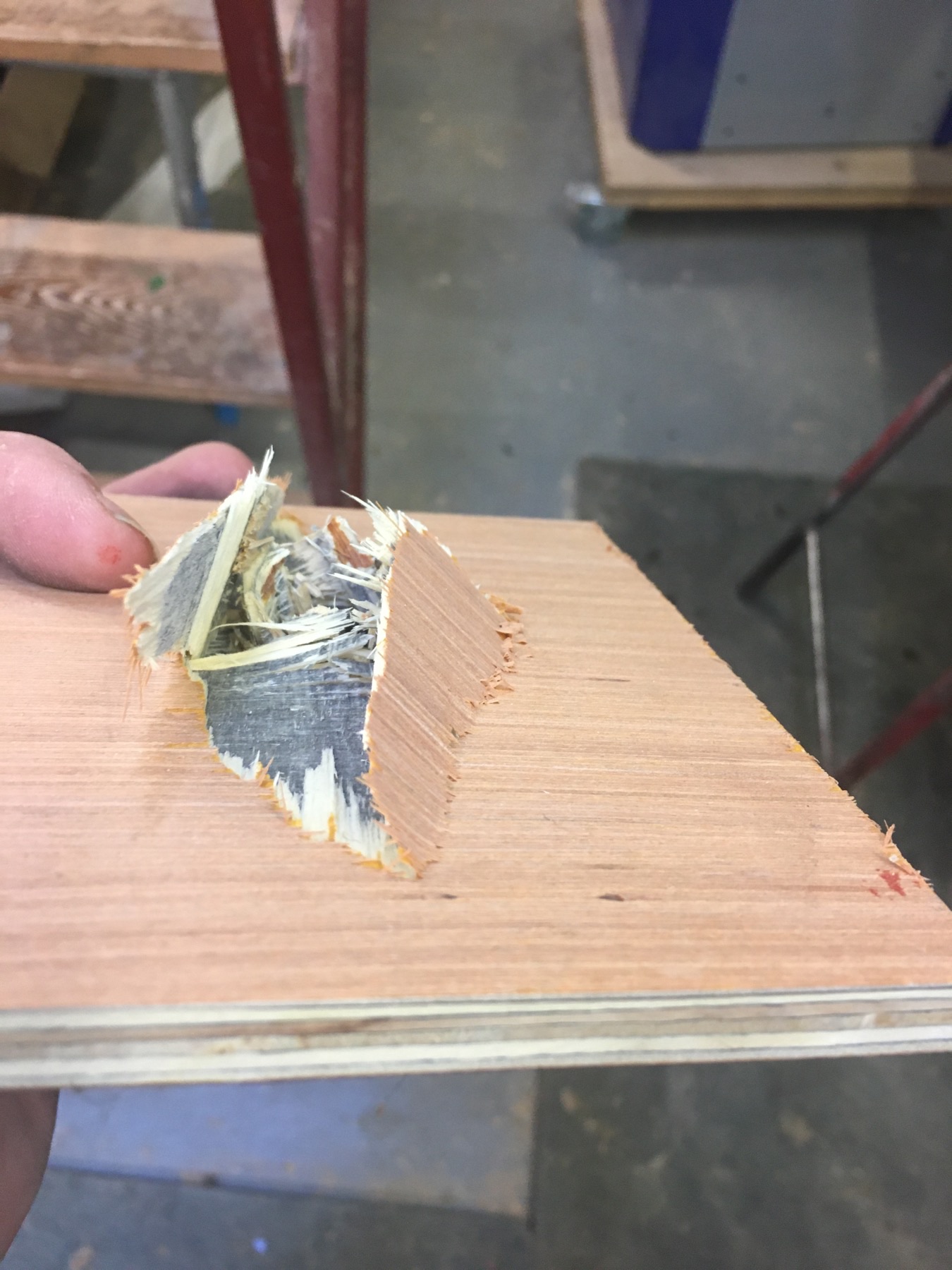
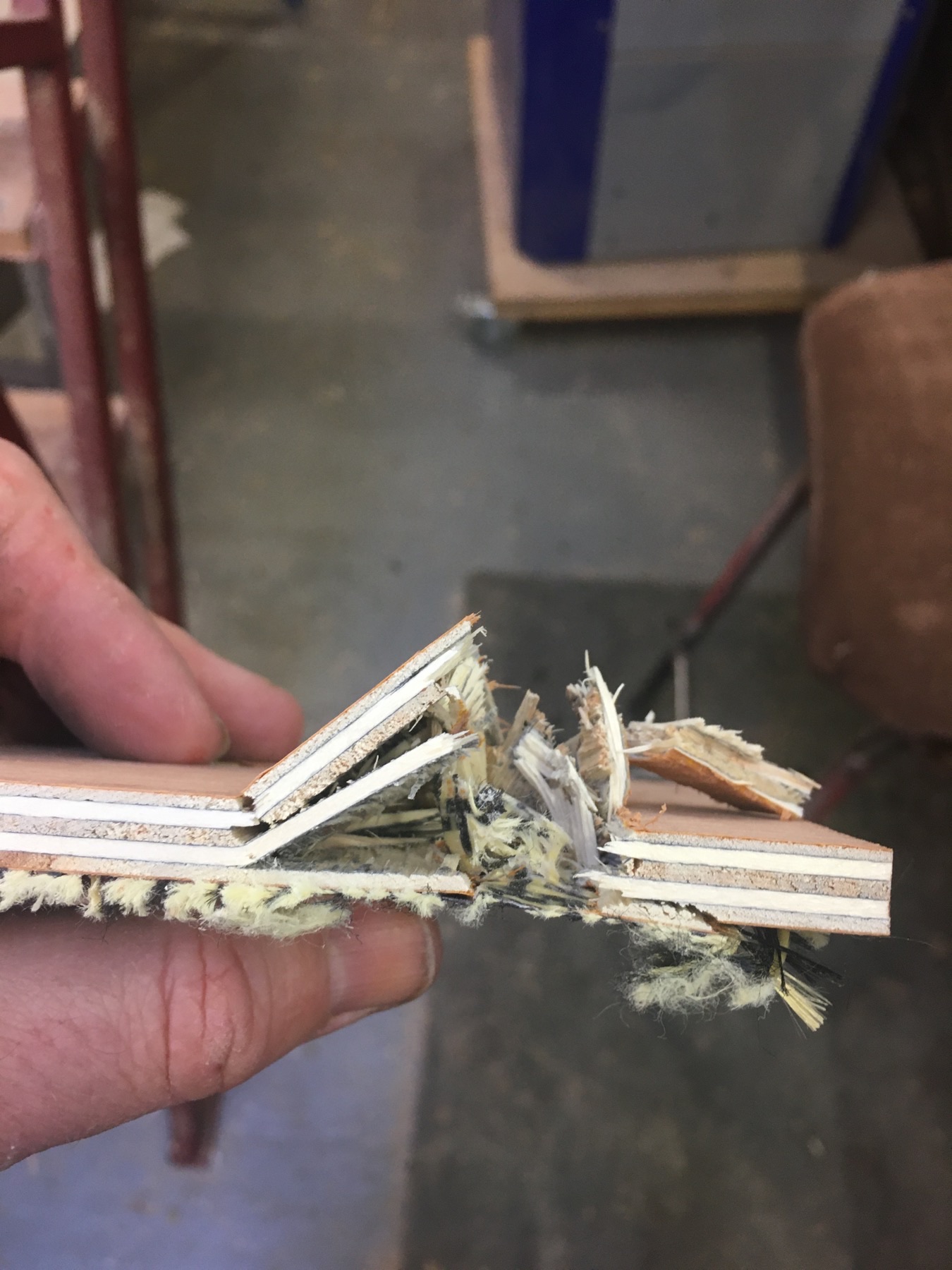
Discussing carbon fibre first we were advised not only by Dave Warby but also several other hydroplane constructors and drivers not to sheath the entire hull in this particular fabric. The reason being that whilst carbon fibre has considerable stiffness for its weight, it has very limited stretch to failure. This is a critical factor to consider when sheathing a timber hull in fabric where the construction is akin to our skeleton and outer skin. The wood is our skeleton carrying the primary loads and that timber will inevitably swell and shrink to such an extent that a carbon fibre skin would not be able to accommodate that inherent movement over a significant area. The result is fracture and catastrophic failure of the carbon fibre outer skin.
If you think wood movement is not capable of such forces sufficient to fracture carbon fibre then consider the Egyptians fractured rocks by pouring water onto wooden wedges placed into them. Carbon fibre also has, relative to Dynel, poor abrasion resistance and for our application abrasion resistance is highly desirable.
Moving on to Kevlar this fabric is widely known for use in bullet proof vests but that is not typically the same grade of Kevlar as that marketed for boat construction. Not only that it typically takes 21 layers of Kevlar to stop a bullet but in our case we are only talking about a single layer of fabric being bonded to the outside of a timber hull and whilst Kevlar is great in tension it is not very good at all in compression. This fabric is also hygroscopic meaning it absorbs water like a sponge which is not the best attribute when considering its use on the outside of a boat. It is expensive, its yellow colour fades in the sunlight and it is a pig to work with requiring special types of shears to cut it without quickly blunting and will readily fluff up into a stringy mess if you try and sand it.
In our case what we want is a fabric that provides great abrasion resistance, good impact resistance and will allow its fibres sufficient stretch to move with the timber hull that it is bonded to using the epoxy whilst, allowing the timber to carry the loads as intended. For all of these reasons you find that Dynel admirably fulfils these design requirements and hence why these fabrics are a proven product for this particular application on timber hull hydroplanes including the fastest boat in the world. This being the case I stopped trying to give myself a headache looking at why other fabrics are not as appropriate for this particular application and got on with laying the Dynel down on to the bottom of Longbow’s hull.
I know some folk with far more experience than me will have just put the Dynel down in a single operation to the entire hull but for my wife Gill who I had roped in to assist and myself doing this on our own and for the first time we figured it would be far easier to tackle the job in bite sized chunks over time. The thought of making a hash of getting the Dynel down through trying to do too much all at once for the pair of us and then having to try and sand off a fabric whose design function is abrasion resistance didn’t bear thinking about.
This being the case first applied the Dynel and epoxy to the rear of the sponsons to give us a small area to try, then the larger area of the transom, followed by the more complex sponsons, the rear planing shoe and then both air trap fences and their adjacent outer underside hull areas. As with anything the more you do the more confident you become and at time of writing this diary update that just left us with the area of the flat but long length of the centre hull to complete which we will probably split in half as two separate applications so we can crawl on one side whilst applying the Dynel and epoxy on the other. The following photo shows my good lady Gill using dress making scissors to cut the Dynel.
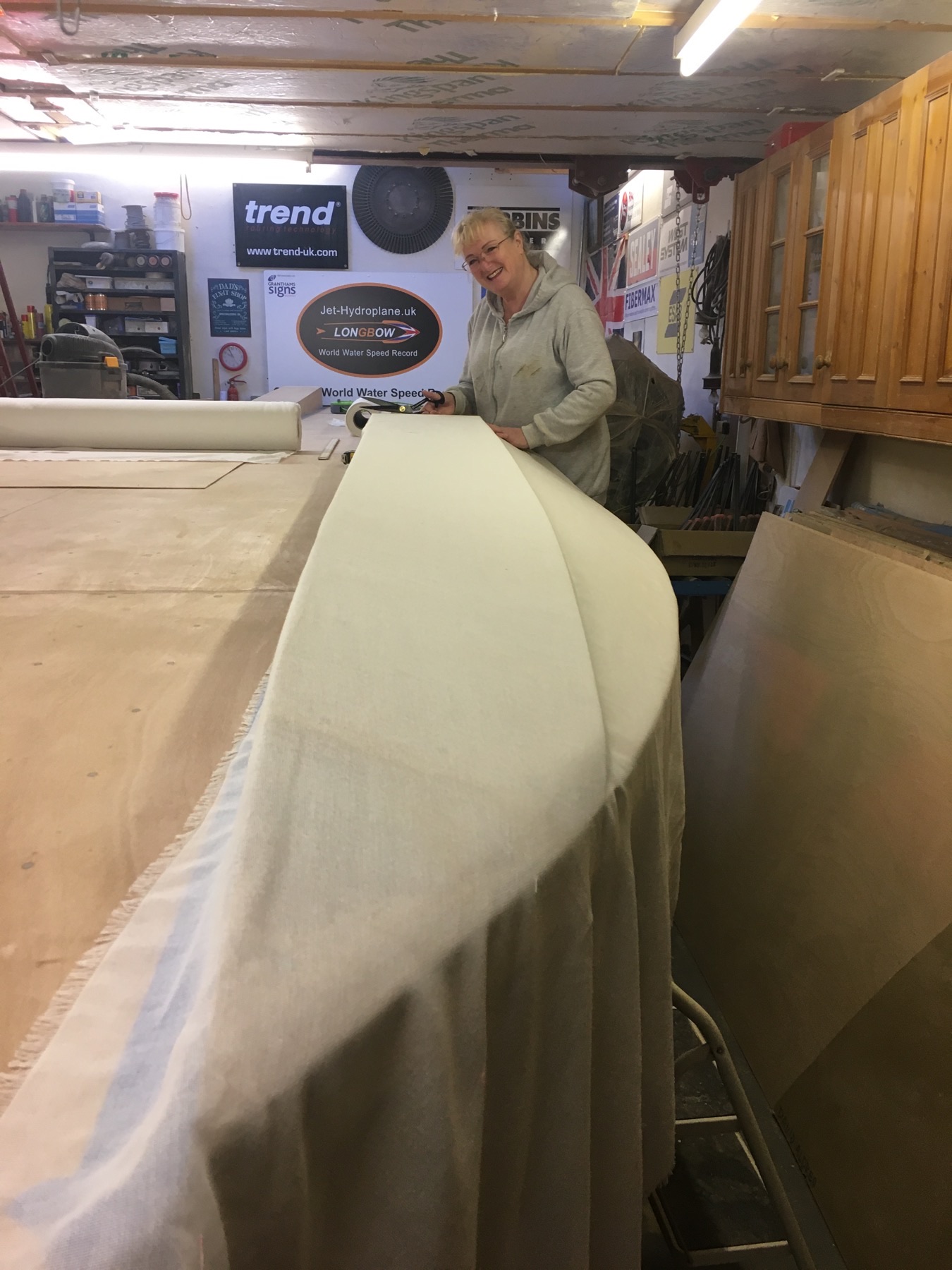
One method of applying the Dynel is to lay it on to the bare plywood which allows you to move it around to where you want prior to wetting out with epoxy but the disadvantage to this method is it presents difficulty with wetting out not only the timber beneath the fabric but also the underside of the cloth.
We therefore took Dave Warby’s advice and indeed that of Wessex Resins and wet out the plywood with the WEST SYSTEM epoxy first, let it reach a stage of becoming tacky and then applied the Dynel fabric smoothing it out by hand and Sealey spreader. Once down and before the epoxy has cured, a further coat of epoxy is applied over the top of the fabric to ensure a chemical bond is achieved.
Whilst this second layer of epoxy is still in its liquid state a layer of peel ply fabric from our sponsor Fibermax Composites is laid over the wetted out Dynel and the peel ply rolled down flat then wetted out with additional epoxy as necessary. The purpose of the peel ply is to capture the Amine blush which is a waxy by-product of using epoxy and to keep the surface clean and ready for the next layer of epoxy or coating. The peel ply can be left for a considerable period of time without any adverse effect and when ready for the next layer of epoxy or coating the peel ply is pulled off taking the Amine blush with it. The following photos show Gill cutting the peel ply and some of the completed Dynel covered by peel ply awaiting adjacent areas to be similarly completed.
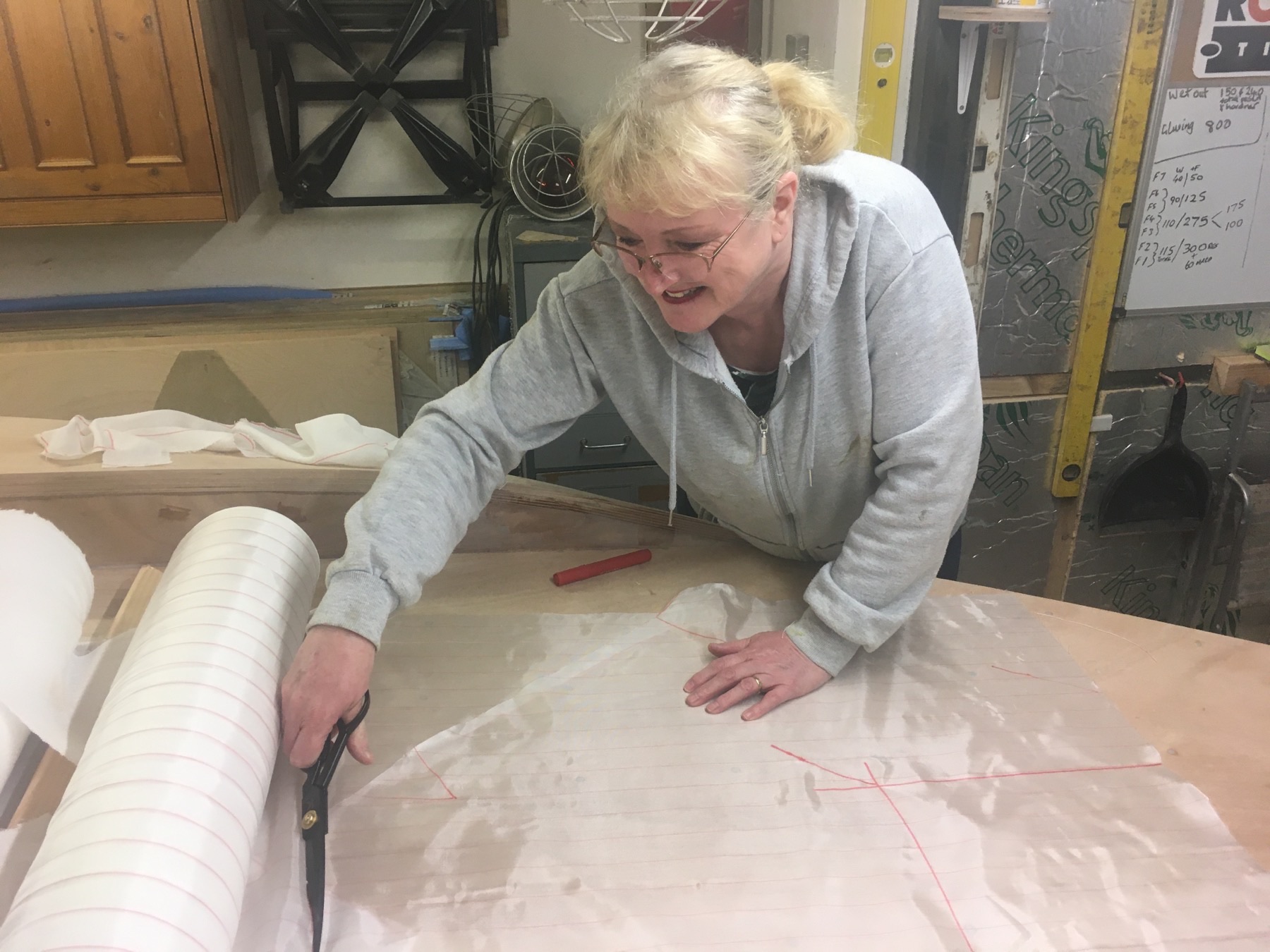
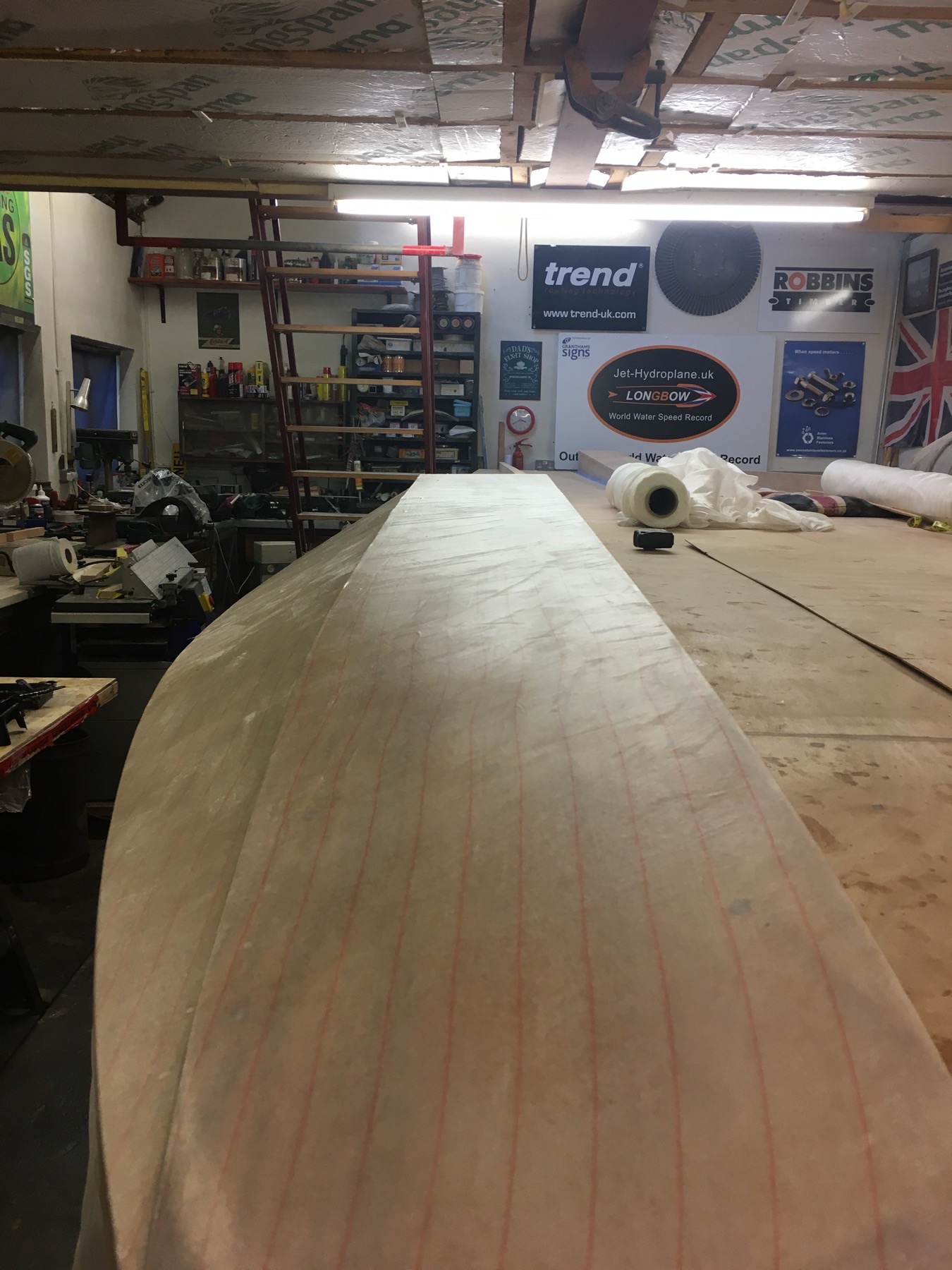
My good friend and mentor Dimitrios Apostolakis of Fibermax Composites also so very generously sent us three more of their vacuum connectors in preparation for when start vacuum bagging and resin infusion of some elements to the craft.
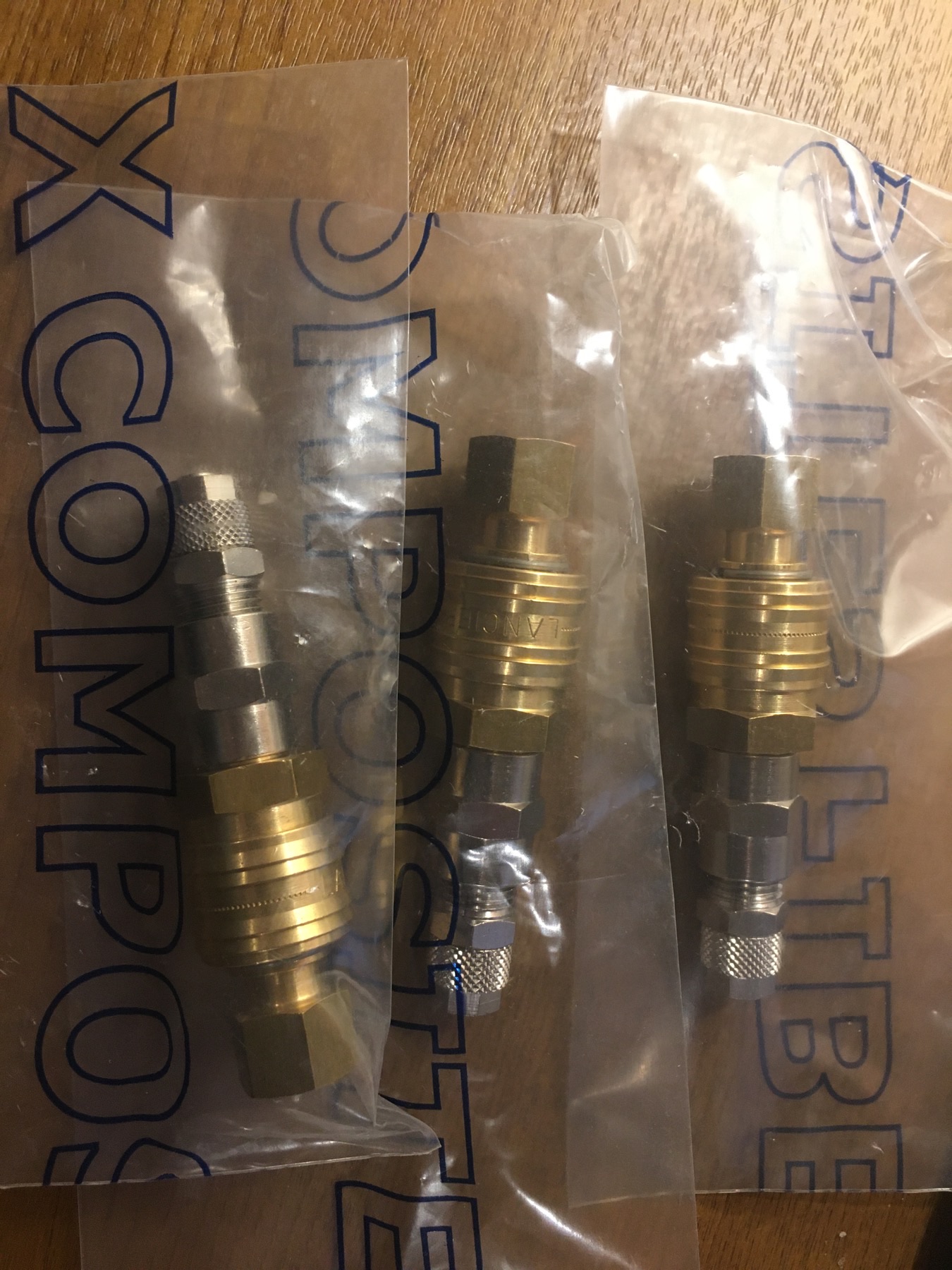
This month I received my first jab of the vaccine against COVID which has been something of a relief given my wife is a childminder for infants without masks whose parents are teachers, or who work in care homes, whilst I run my own business of surveying people’s houses. Recently I have undertaken work in Coniston, Kendal, Newby Bridge and Gosforth in the Lake District alone, then Manchester followed by Middlewich; all where I am face to face with different homeowners for a couple of hours at a time. So whilst I have had to wait my turn to receive the vaccine you may appreciate I was very thankful indeed to be part way to being safe and indeed keeping others safe in such situations where even the residents of rural Coniston have seen cases of this terrible virus occur.
Speaking of Coniston the 23rd March also marked the 100th year since land and water speed record breaker Donald Malcolm Campbell CBE was born and this was commemorated by the Trustees of the Ruskin Museum working with the RAF to arrange for two Hawk aircraft to undertake a low level high speed flight over the length of Coniston Water where Donald broke the Outright World Water Speed Record (fastest boat in the world), in his jet hydroplane Bluebird K7 on five separate occasions between 1956 and 1959.
Donald’s only child, Gina Campbell QSO, herself having achieved not just once but twice the Ladies Outright World Water Speed Record, was present at the flypast and to say happy birthday to her dad. So much has been said about Donald, his family and their Bluebirds there is nothing that I could write here in my clumsy way that could convey what an inspiration, this great man, this great family and all of their great Bluebirds have meant to me personally throughout my life and likewise I imagine to so many people in a similar way throughout the world.
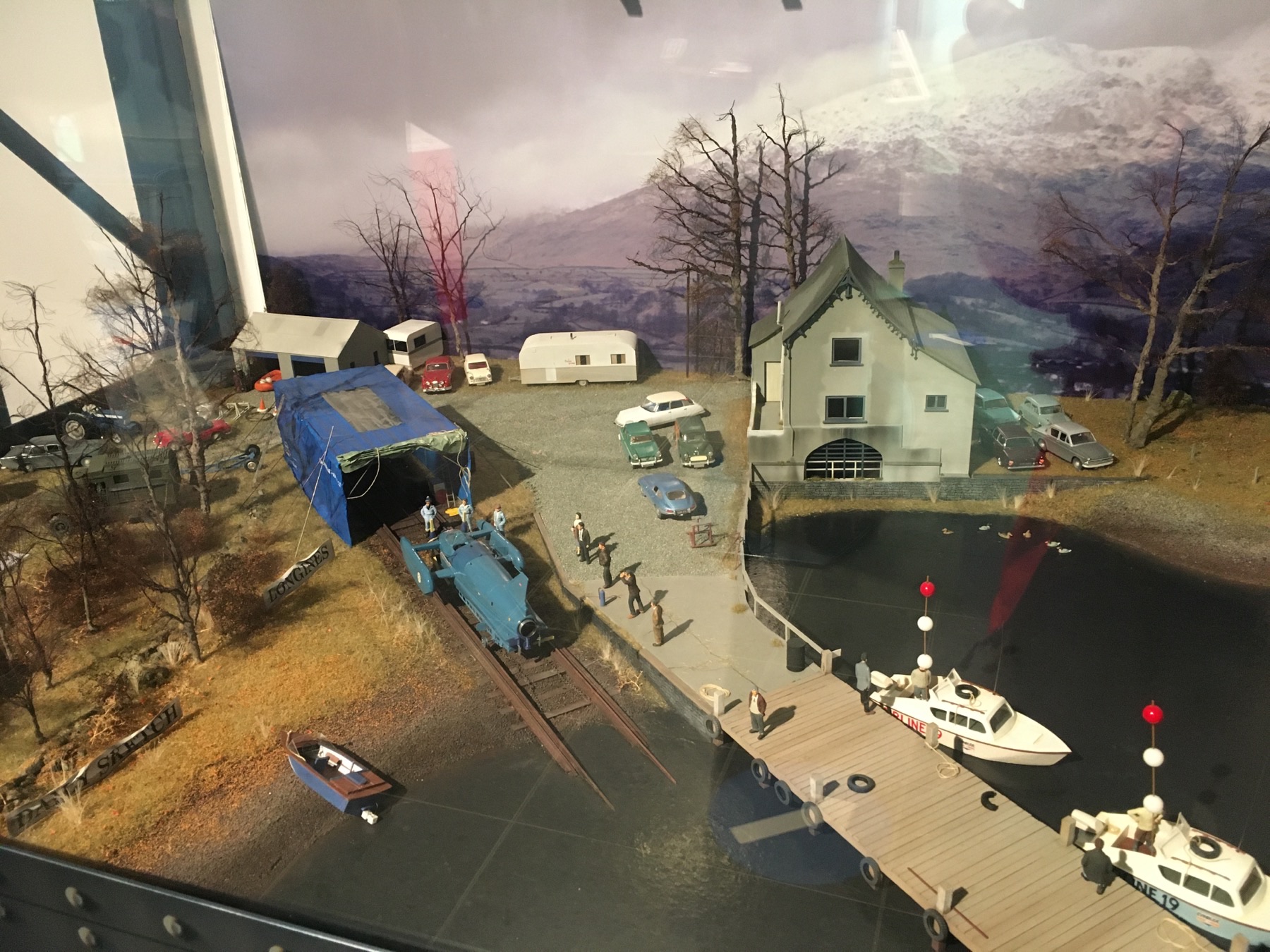
Perhaps a rough quote of Sir Stirling Moss interviewing the charismatic James Hunt asking the latter how he went so fast, how did he do it, to which James famously quipped in reply ‘Big balls’ is the best way I could sum up my total respect and admiration of Donald, his equally colourful life and the charisma he clearly had in abundance with that smile and a wink.
Happy Birthday Donald………