Welcome to the November update of the building of our jet hydroplane Longbow. This month we are proud to announce a new product sponsor on board with our little venture by way of RACEPARTS who are based in Wallingford in Oxfordshire and was founded by Peter Bloore in the 1970’s. They supply a huge range of motorsport spares and equipment so it is great to have them on board for the times ahead. Please take a look at their website: https://race.parts/
Also this month saw our good friend Dave Warby and his team in Australia back at Blowering Dam for further development runs of their jet hydroplane Spirit of Australia 2. With good weather at this visit Dave and his team were able to reach their highest speed yet of an incredible 260mph so heartfelt congratulations on this brilliant achievement, so very well done.
Dave reports that he is really happy with the way the boat is now set up, such that he is looking forward to gently nudging away at increasing the speeds in the times ahead as they work towards attempting to break the current Outright World Water Speed Record (fastest boat in the world) of 317mph. The following superb photo courtesy of Jeff Barnett shows Dave in SOA2 last weekend during a high speed run:
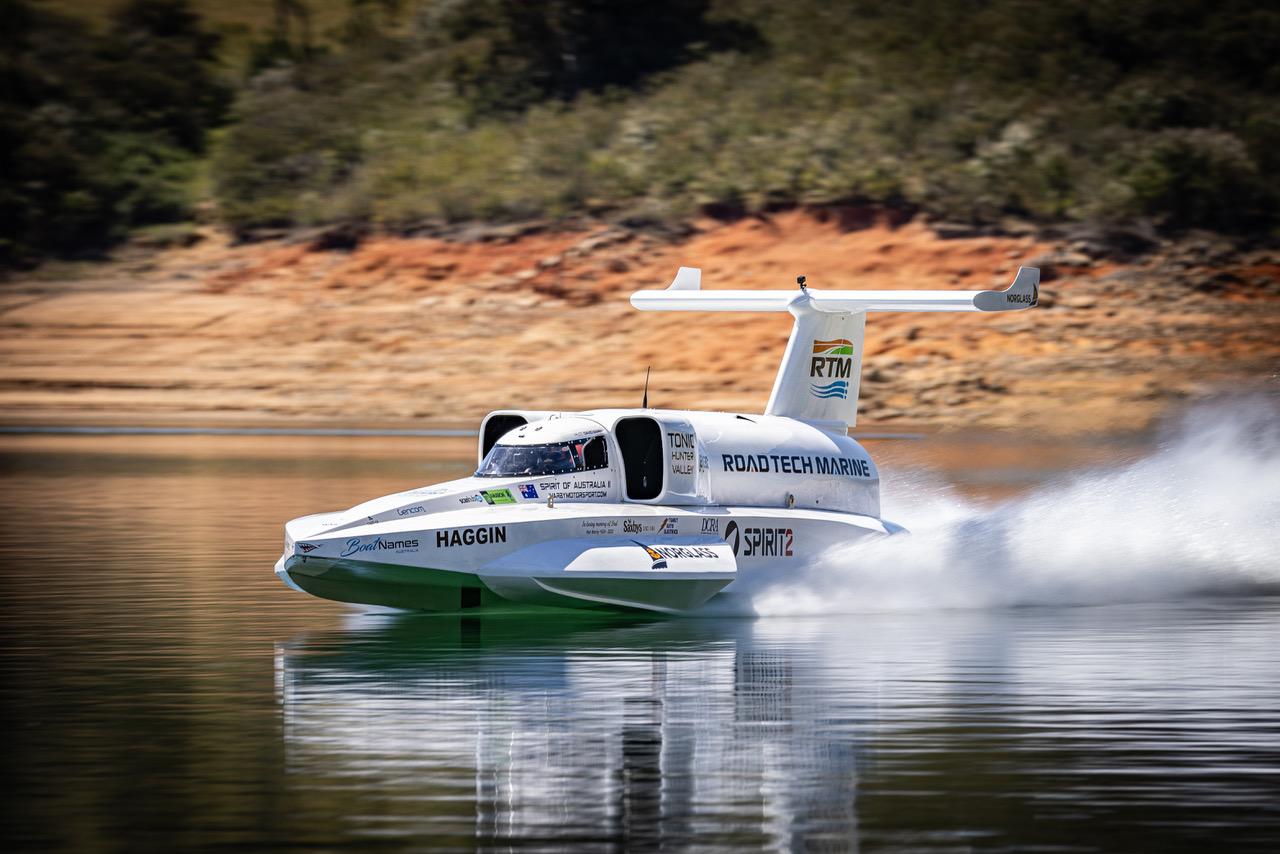
That was the good news but the not so good news was that during a run at the dam Dave unfortunately had a bird strike with the boat at a speed of around 220mph and the following photos show the ducks on the water just prior to impact, along with the aftermath.
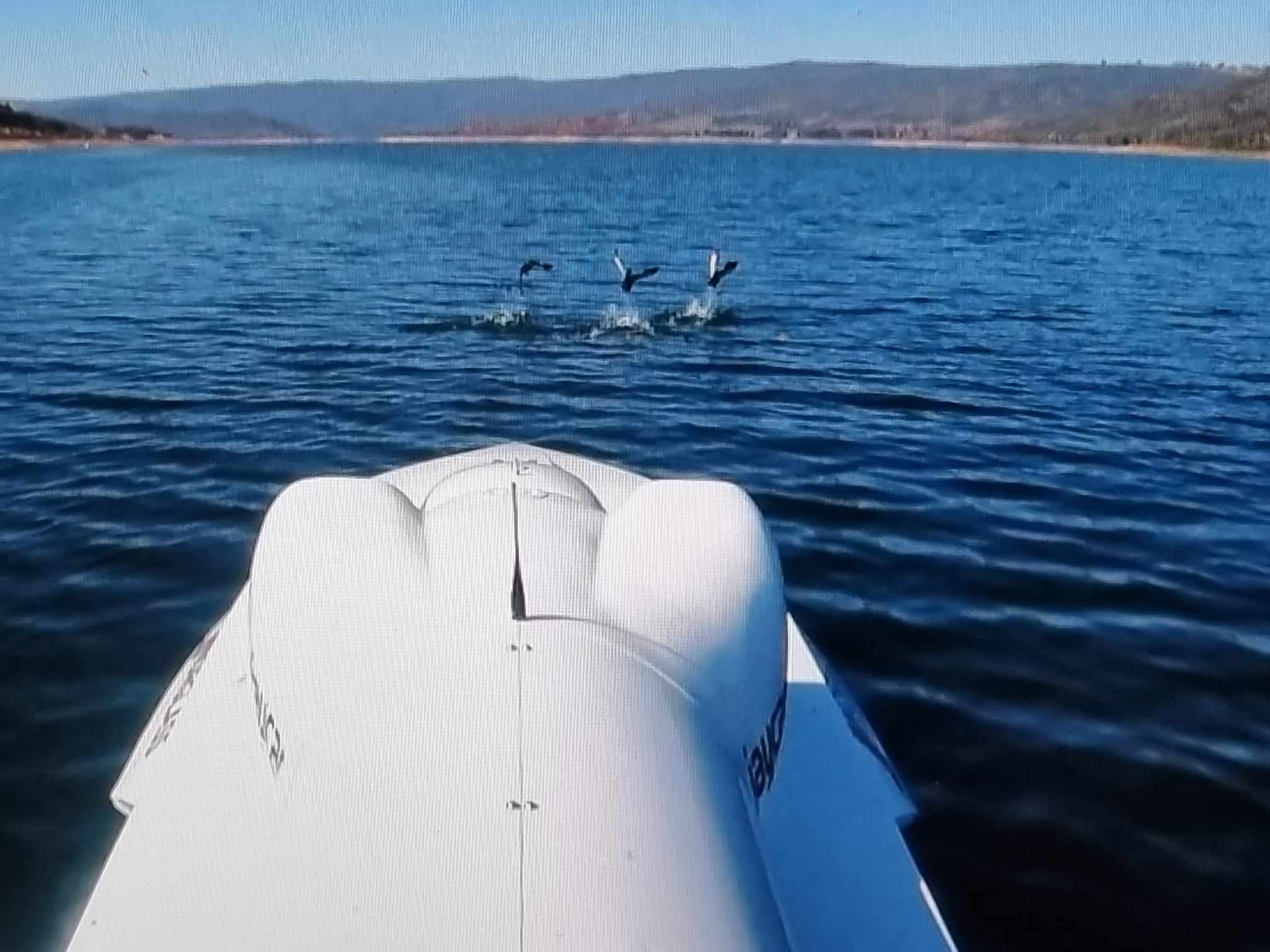
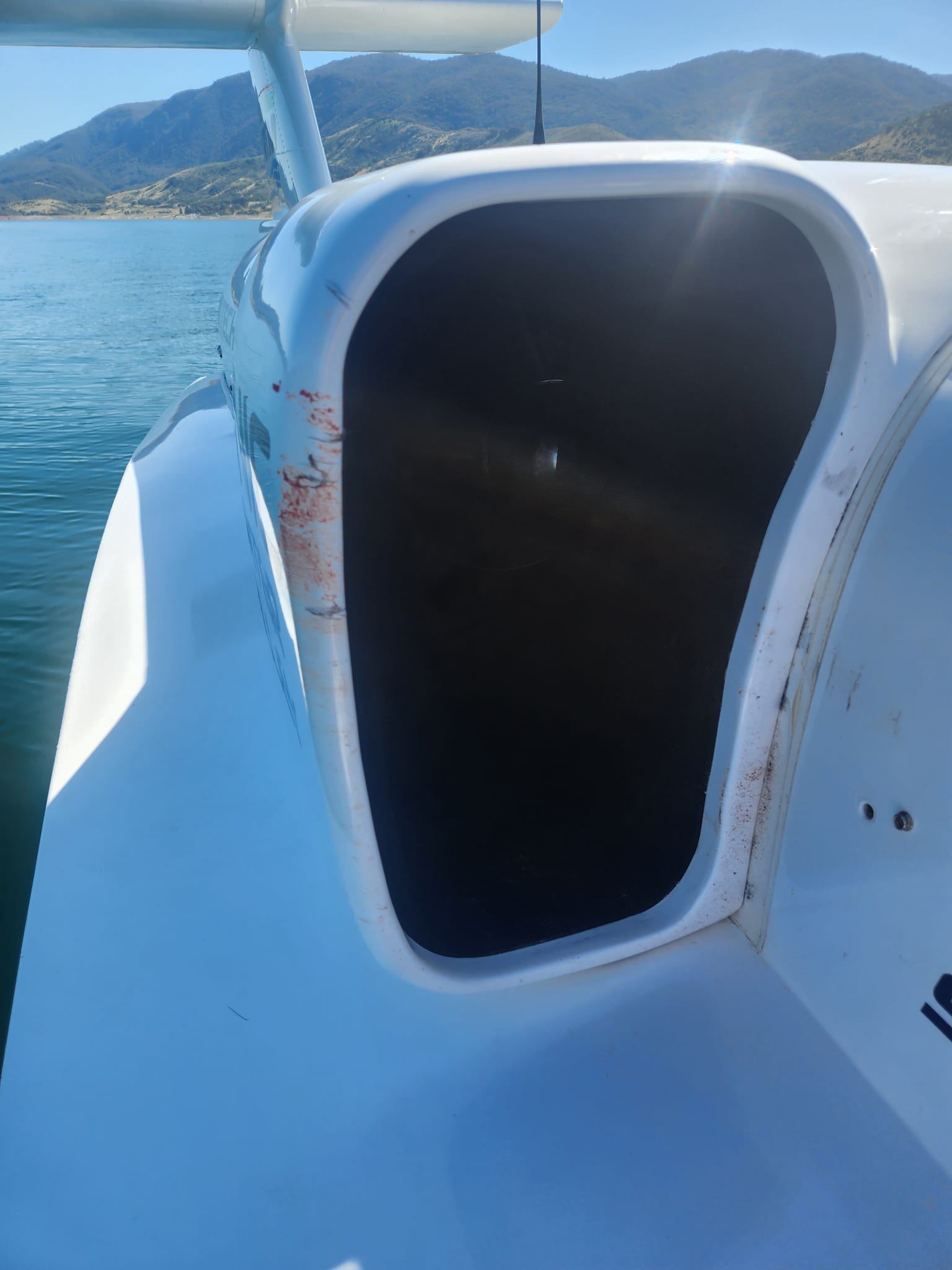
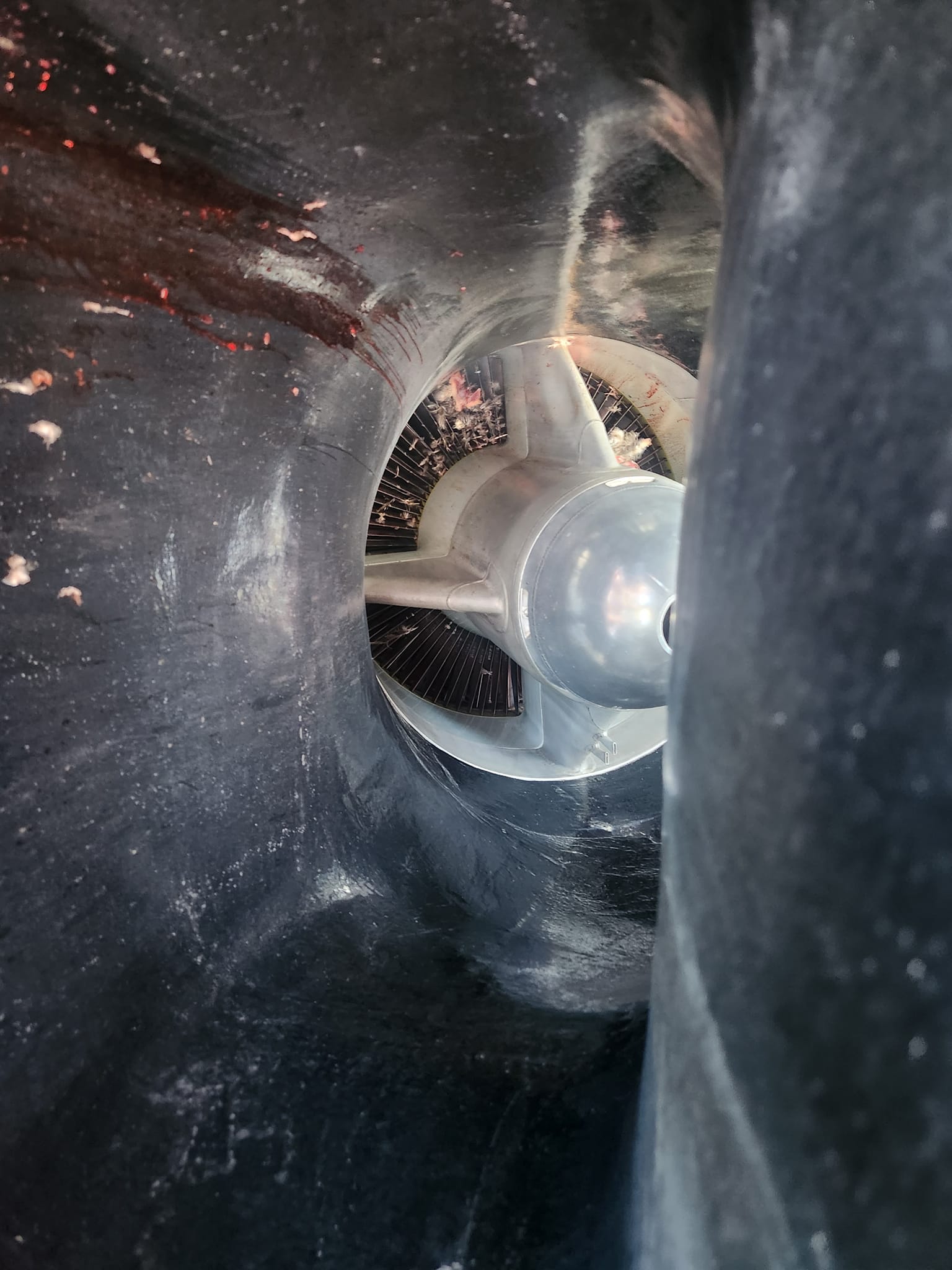
That unfortunately put an end to both the ducks and further testing of the boat for that weekend. If there was any good news to be had from the event it was somewhat lucky that the birds weren’t bigger, for example geese that famously wrecked both jet engines on an Airbus A320, bringing the aircraft down into the Hudson River back in 2009. Thankfully on that occasion all the crew and passengers survived and later made a great film (Sulley), with actor Tom Hanks playing the role of pilot.
You may appreciate that whilst bird strikes are thankfully somewhat rare for aircraft in flight, they are more likely to occur with a boat running at high speed, where waterfowl having a nice paddle about are something more of an occupational hazard. Both Dave’s father Ken Warby MBE in his jet hydroplane Spirit of Australia and Donald Campbell CBE in his jet hydroplane Bluebird K7 experienced bird strikes from waterfowl.
Following the incident I did see some comments upon social media about why Dave’s jet engine intakes were not fitted with screens to prevent the birds being ingested into the engine. Screens of steel mesh are used in front of jet engines when they are fitted to jet cars for drag racing but the layout of such cars is typically with the engine further protected by the cars bodywork and / or the driver sitting directly in front of the engine intake. The mesh surrounding those engines is not really for protection from bird strikes, it is more to resist debris on the track or holding area whilst the engines are being run up, from being sucked into the engine.
Some helicopters for example the Chinook have screens / filters in front of their turbines. However that is primarily to protect the engines from debris being sucked into the engines as it is blown into the air the downwash of the main rotor, rather than bird strikes. Also the forward speed of the helicopter is significantly slower than craft attempting to break the Water Speed Record.
With fitting screens to the intakes of the jet hydroplane there are really three main points to consider. In the first instance the screens are going to degrade the performance of the engine when you want to go as fast as possible. Secondly you could mess up the airflow at the compressor face to the engine so much that you induce a surge of the engine which is never a good thing and can result in considerable damage.
Lastly with steel mesh in front of the engine, once you start going pretty quick, the chances are if you unfortunately hit a bird or a flock of them, not only are they still going down the intake but they are likely to be wearing a steel overcoat as they take the mesh with them. That my friend is guaranteed to do far more damage than if the birds are just in their birthday suit. Or think of it rather like the difference between putting just food into your kitchen blender, compared with throwing the cutlery in there too.
Perhaps it was something of an omen but the week before Dave had gone to the Dam with SOA2 we had arranged to send him a replacement turbine wheel for one of his engines that had been sitting in my workshop since before the pandemic. Dave also tells me that the Ruskin Museum have kindly sent him a pallet full of spare parts for his engines that they had in stock and which are now on their way to Australia.
Hopefully damage to Dave’s engine will be minimal and it takes me back to stripping an Orpheus jet engine for the K777 jet hydroplane and being taught by the late Graham Pool who was a senior gas turbine engineer at Rolls Royce, how to blend the blades of the engine and so much more. How I wish I had been brought up surrounded by folk into jet engines like Dave in Australia and his trips to hang out with his father in the USA with the jet cars and trucks, where it was inevitable he would learn how to overhaul and repair jet engines from such an early age.
Back here with Longbow I managed to source the original part that connects the aircraft fuselage to the front of the engines as shown below.
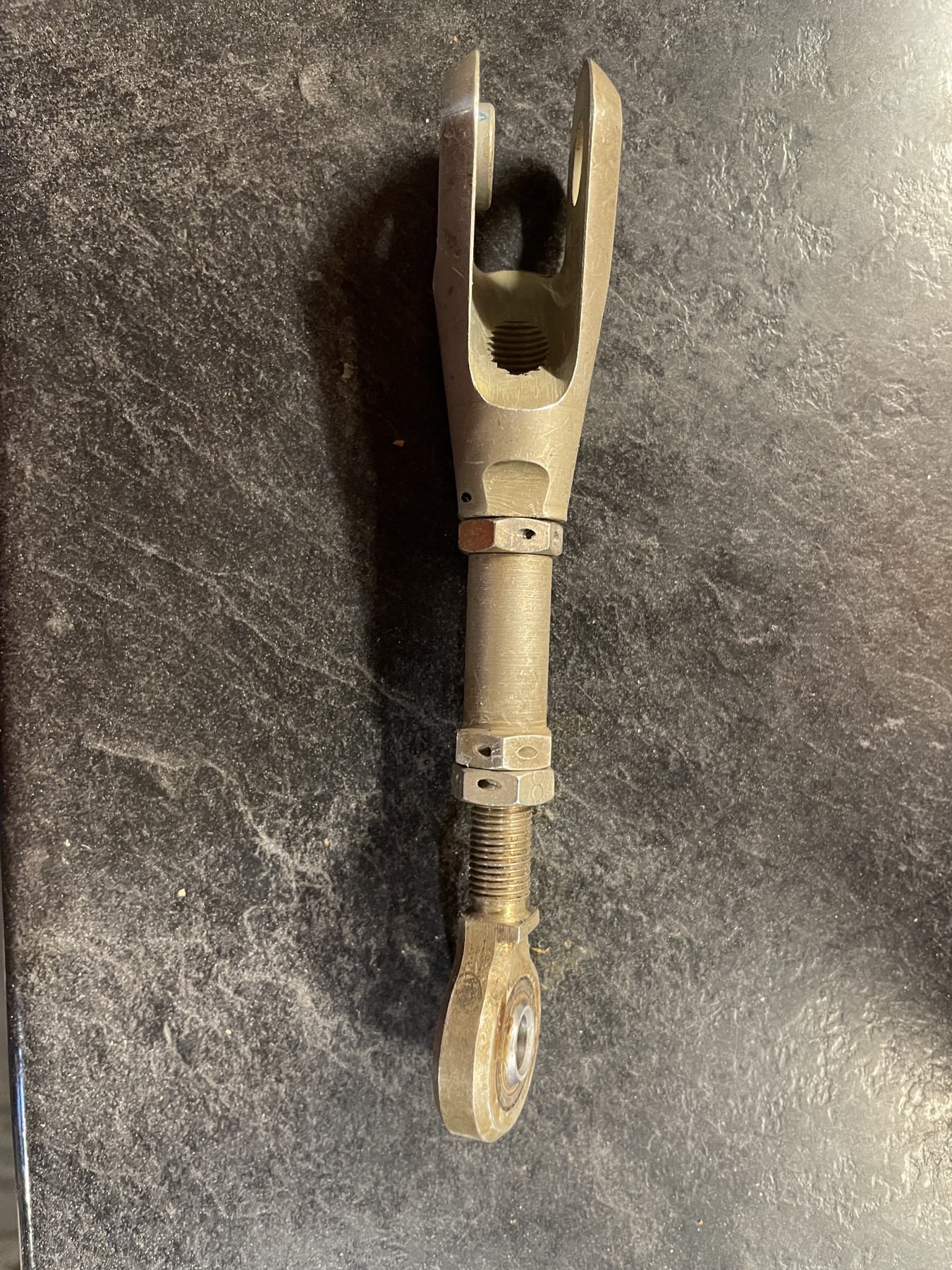
This is what acts as an engine steady and to set the angle of thrust coming out the back of the engine. The main thrust of the engines does not go through this part, that is the job of the trunnion mountings but nevertheless it is something that is an essential part of the engine installation. For our application in Longbow we need to manufacture a similar part for each engine but to different dimensions and somewhat stronger material but it is a very helpful starting point and was a lucky find indeed.
With most of the aspects of building Longbow I have posted photos and details of construction in the monthly diary updates but as we move into some other aspects of the build there are inevitably certain elements of her design and information that need to be held back from public disclosure. One of those elements this month has been where we have been working closely with Dave Warby on the design of our rudder and associated parts.
Dave and ourselves are more than aware that there are other folk building jet hydroplanes around the world who would love to know the development of rudder profiles Dave has been using to get to where he is now. All I can say is I am forever in Dave’s debt for the amount of information that he so generously shares with me regarding the development of his boat. This feeds down into the building of Longbow and it says everything about our decades of friendship that he trusts me enough to do that.
What I can give you an insight into this month is the amount of what I knew would be head scratching over cutting out the transom of the boat in order to allow the jet pipes to pass partially through it. The actual cutting out of the transom is the easy part and takes no time at all but it is a decision of just how low in the hull we can get the twin jet engines to sit that has had me pondering over the last few weeks.
Ideally from a stability point of view when running at speed skimming over the surface of the water, you want the thrust of the engines to be as close to the lake surface as possible. However at rest the bottom of the jet pipes doesn’t want to be so low that the surface of the water is running down and into the jet pipe / hull and potentially sinking your boat.
If you look at Bluebird K7 and K777 at rest you can see just how perilously close to the water the bottom of the jet pipe is to the lake surface with the craft at rest. Bear in mind the craft when complete, fully loaded with fuel and pilot only has to be sitting one degree down at the stern from horizontal and over the length of the boat that equates to a few inches difference in where the lake surface will be lapping at the jet pipes.
There are so many variables to consider and if you think it is an exact science then you are sadly mistaken. For example the highly gifted Chartered design engineers, Ken and Lew Norris who designed Bluebird K7 were drastically wrong in their calculation of how their craft would sit in the water when at rest. When first built and trialled on Ullswater in the Lake District the front of the boat was disastrously awash as shown in the following photo.
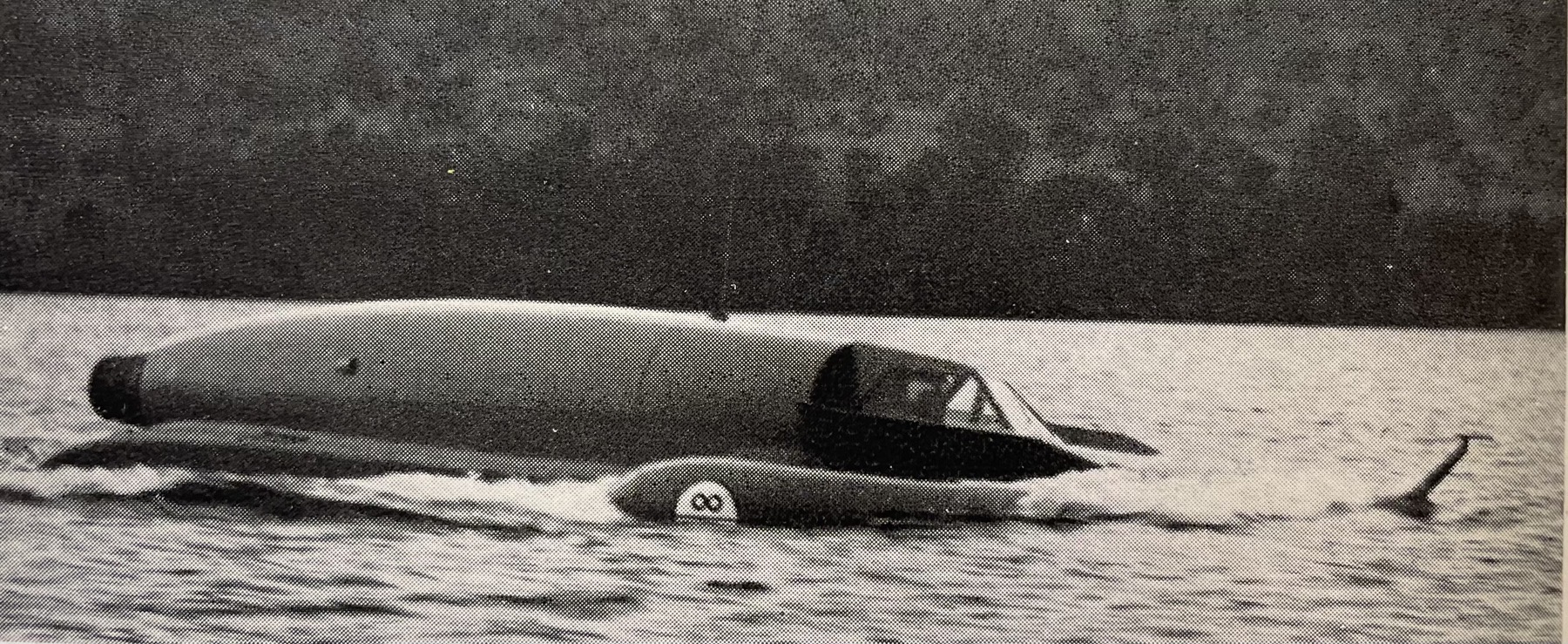
There was no way she would ever have ever planed and been the success she was without a major re-design and structural alterations to her hull involving cutting away and moving primary elements. If these brilliant engineers could get it so very wrong it was certainly going to keep me awake at night.
So after much head scratching out has come the saw and the cuts for each jet pipe in the transom have been made.
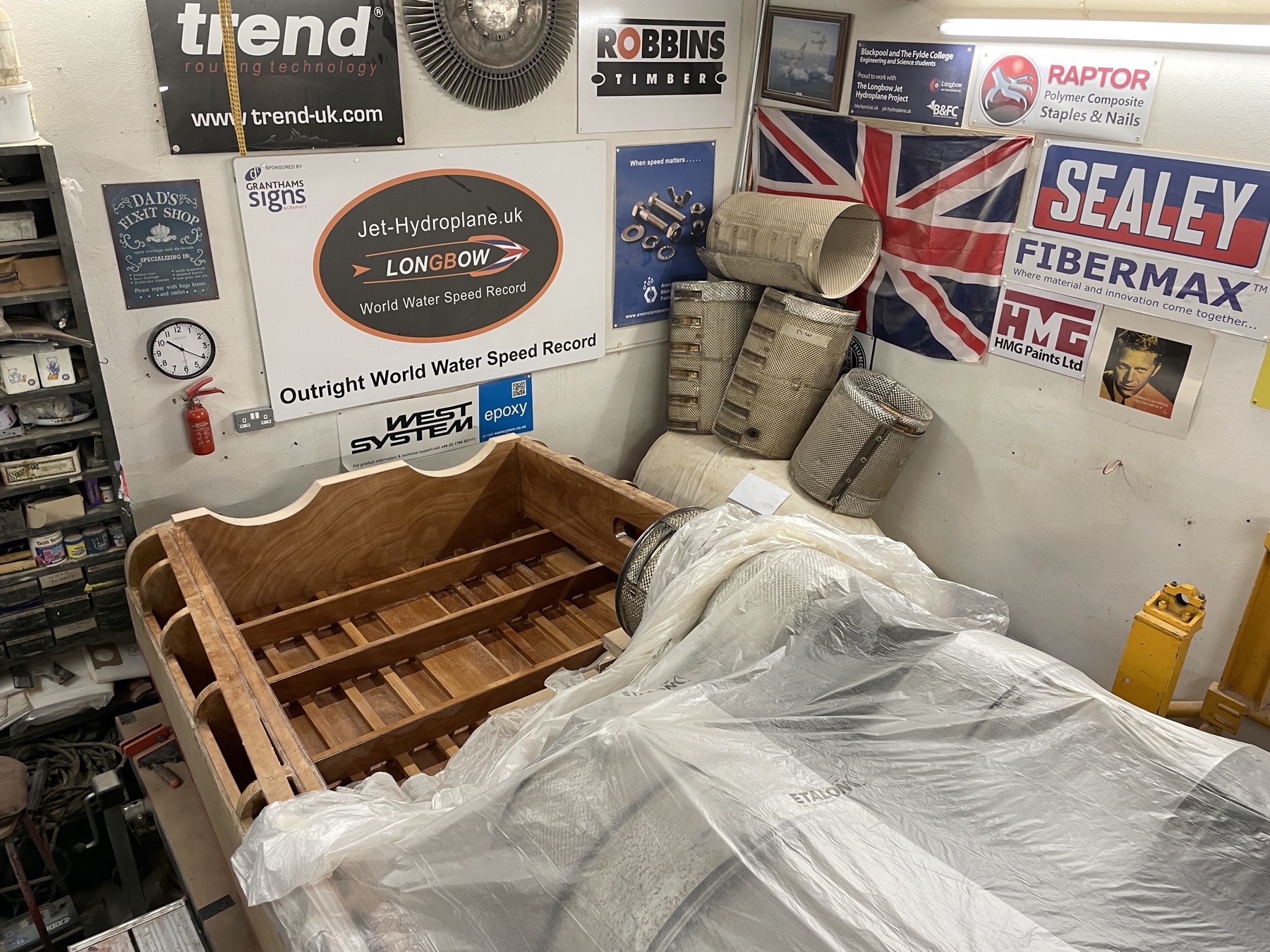
It is always easier to cut more material out than having to reinstate it so better at this stage to err on the side of being cautious. This being the case the plan is to sit the engines in the hull on the high side, do a static floatation test when we are further along with the build and if we can as a result of those tests, lower the engines in the hull then we will. Fortunately with the twin engines being a relatively small diameter we are fortunate in that the thrust line even with the engines positioned at the high setting will still be on a par with other very successful jet hydroplanes.
The following photo shows one of the jet pipes resting upon the transom.
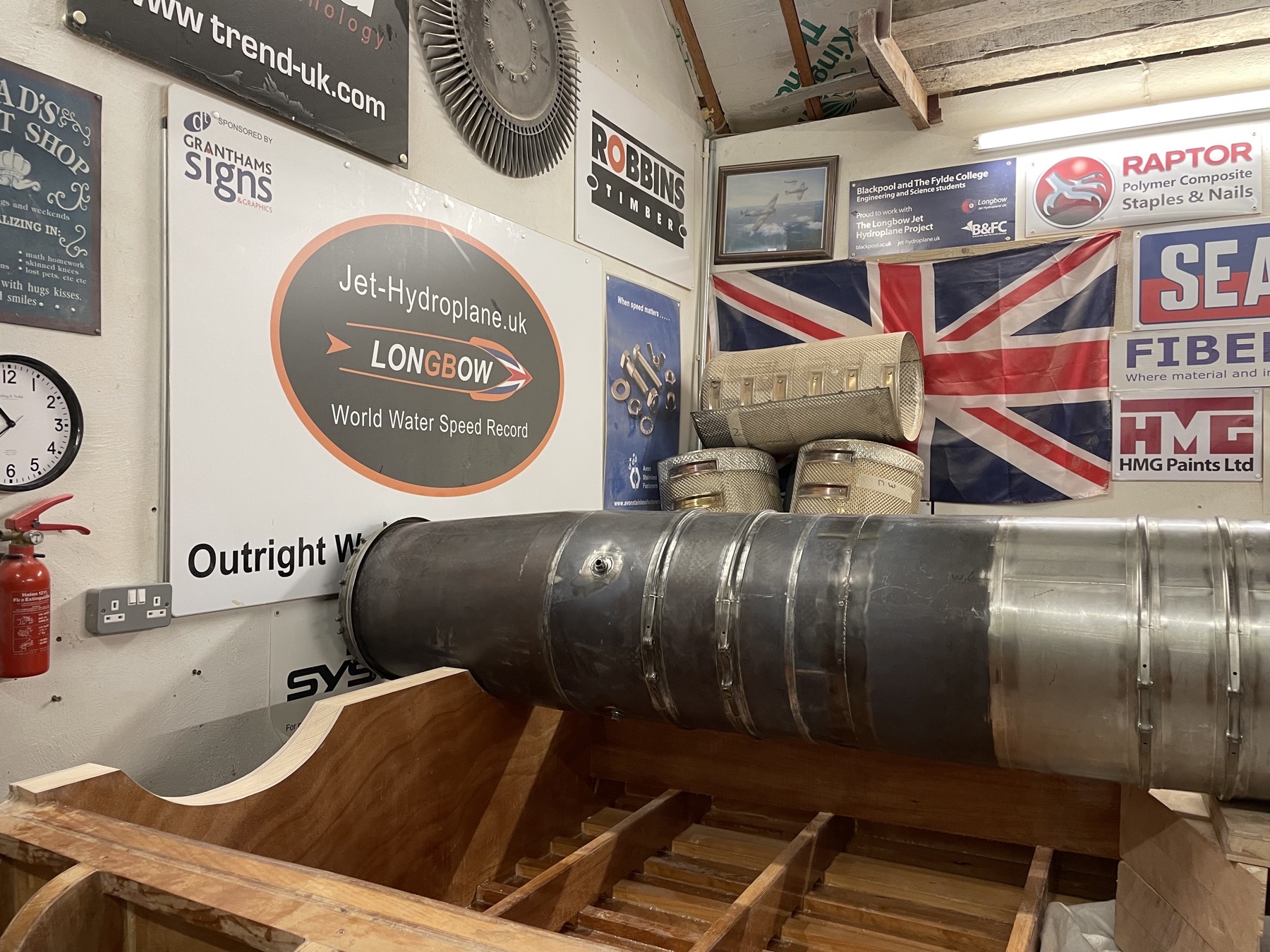
I have said it before and will say it again how big did I build her, as big as I could just fit in my cottage workshop and I really do mean, ‘just fit’ !
Dave recently posted the following on social media and it is a well known comment by President Roosevelt but never a truer word spoken:
‘It is not the critic who counts, not the man who points out how the strong stumbles, or where the doer of deeds could have done better. The credit belongs to the man who is actually in the arena, whose face is marred by dust and sweat and blood; who strives valiantly; who errs, who comes short again and again; who spends himself in a worthy cause; who at the best knows in the end the triumph of high achievement, and who at the worst, if he fails, at least fails while daring greatly, so that his place shall never be with those cold and timid souls who neither know victory or defeat’.
So on that happy note that’s it for this month folks. If you have not done so already please take a moment to like our Facebook page and drop by towards the end of next month for the next update on progress as we build our jet hydroplane Longbow to run and develop upon lakes and lochs within the U.K.