Summer has definitely left us until next year and as the temperatures fall, on come the electric heaters in the workshop kindly supplied by our sponsor Sealey. This is not because we are a bunch of softies (we do after all live up north by the sea) but to maintain an optimum temperature range for application and curing of the epoxy.
In last month’s update we said that we would discuss more about both timber and epoxy this time around, in order to provide those following our venture, especially if they have no experience of such, with a little basic understanding about both subjects and how they marry together in constructing the hull for Longbow.
To a layperson wood can be something of a confusing subject as the following will hopefully demonstrate. For a start hardwoods and softwoods have completely different cell structures as shown in the following photos:
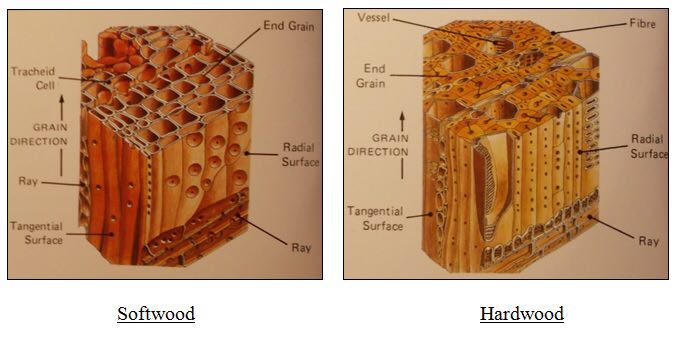
Credit Sovereign Chemical Industries Ltd
In general hardwoods are from trees that lose their leaves annually, such as oak and softwood trees are usually evergreen, primarily conifers. Despite the name not all hardwoods are hard, for example balsa is a hardwood that is very soft and not all softwoods are soft, for example yew is a very tough softwood. Are you confused yet?
You cannot talk about wood without discussing what causes it to decay, take for example a rotting fence post, why does it always tend to fail at the point it just comes out of the ground? Well first you need naturally occurring airborne spores of dry and wet rots – yes they are in the air all the time as microscopic reproductive units so you probably have some on you as you sit reading this. You also need timber as the food source for those spores, water, oxygen and a certain temperature range. Where all of these factors come together appropriately (and hence just where your fence post comes out of the wet ground), those little spores are going to germinate and grow like crazy devouring your timber. Rots do such a good job of doing this they even produce water as a by-product of eating the wood to aid further growth and wet ahead of itself to eat timber that otherwise would not have decayed, how clever is that?
In days of old the British naval fleet had timber ships being devoured by dry rot before they were even launched. So if we are going to stop our boat from being eaten by those pesky spores, in practical terms the only thing that can be realistically controlled is the moisture content of the wood. That is to say if timber is kept below 20% moisture content, then germination of those airborne decaying spores should not occur. So how do we stop our wooden boat getting wet and keep it as strong as the day it was built? We encapsulate it with epoxy coatings to keep the moisture and those pesky decay spores out.
Each species of wood has a different level of natural resistance to decay so we need to pick one which is not going to welcome those decay spores with open arms. It is untrue that all hardwoods are resistant to rot (beech is an example of a non durable hardwood) and it is also untrue that all softwoods decay easily, (Western Red Cedar is certainly durable softwood). If that was not confusing enough different parts of the same tree are more durable than others, with the outer sapwood being the living part of the tree being far less durable than the dead inner heartwood.
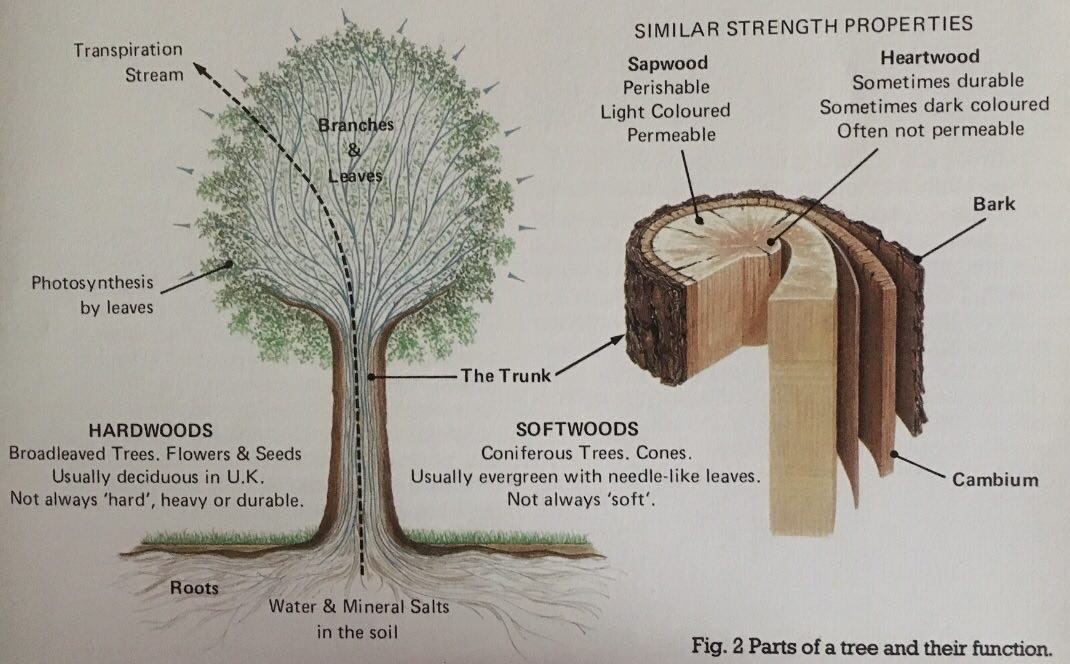
Credit Sovereign Chemical Industries Ltd
Different species of wood will also expand and contract (primarily across the grain) at different rates, as they seek to remain in equilibrium with the amount of moisture in the air, let alone if they get wet in a boat.
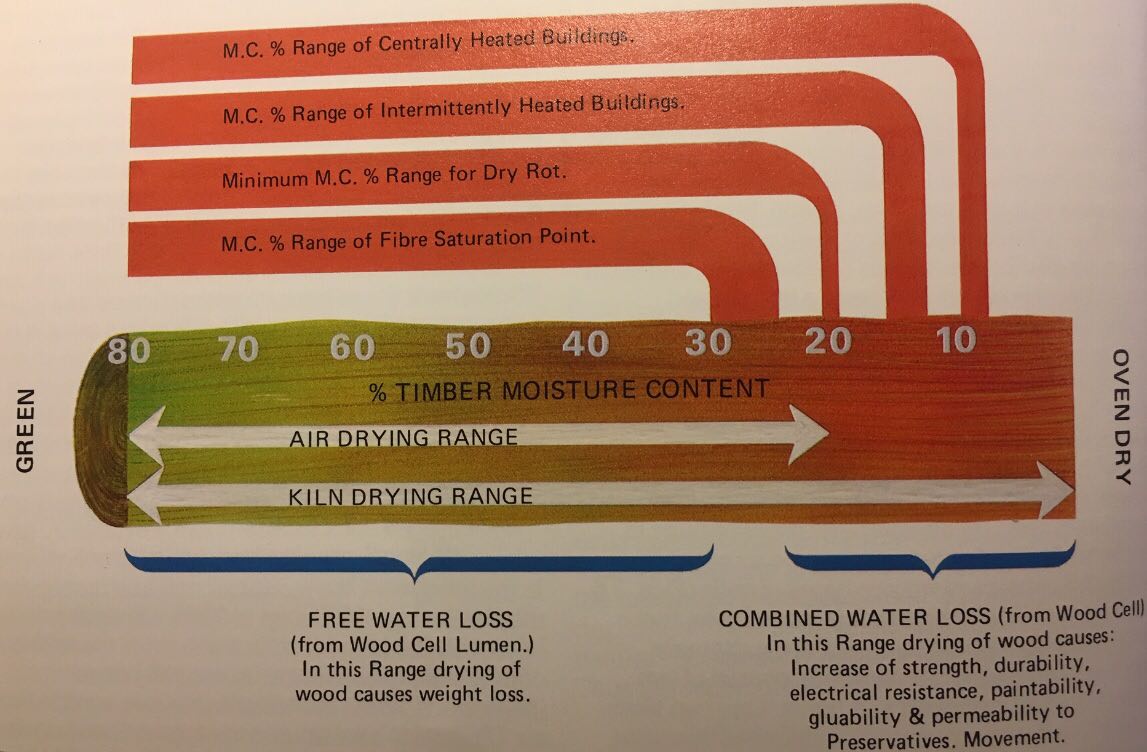
Credit Sovereign Chemical Industries Ltd
In amongst all this bewilderment we want a species of wood that is easy to cut saw and shape, that is not too heavy and is suitable for building the hull of our jet hydroplane Longbow.
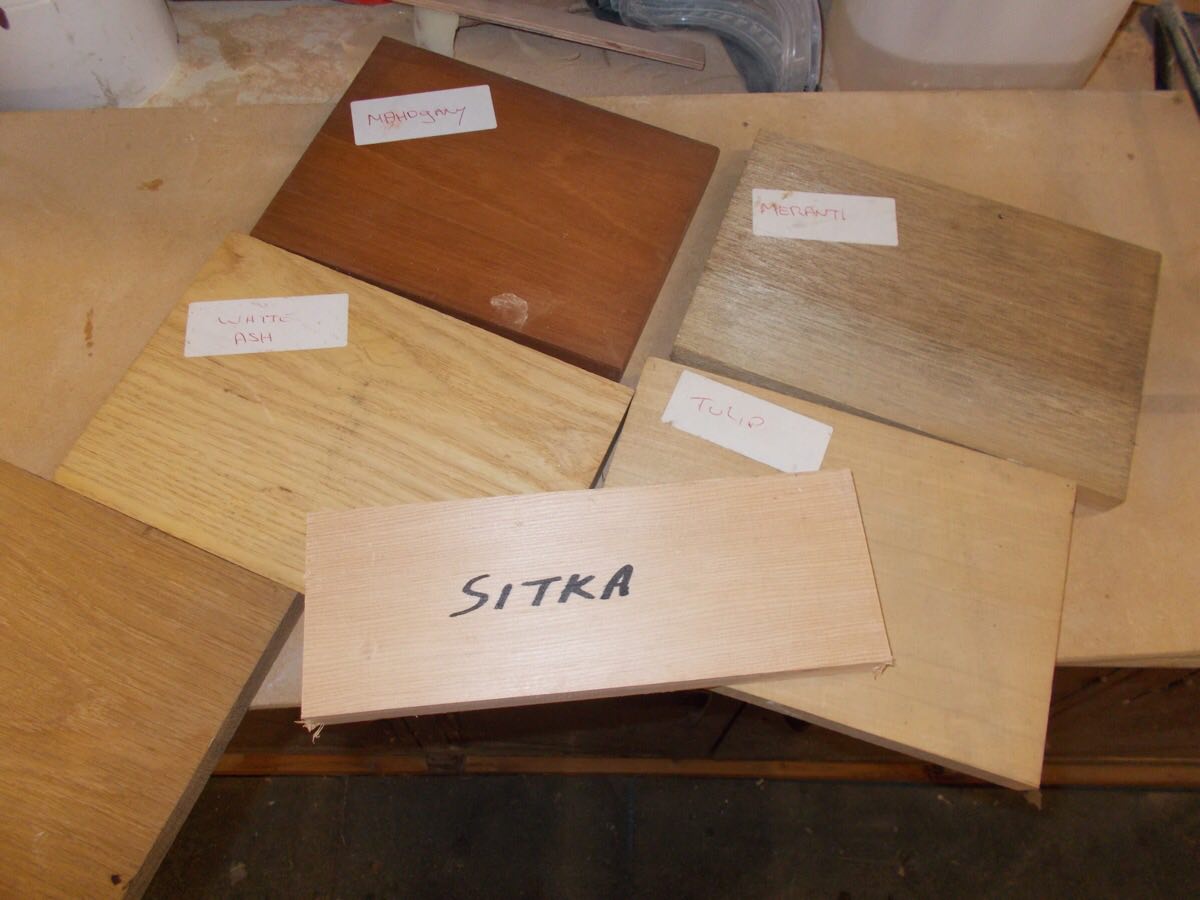
Some may say why not build her out of oak, as that is renowned for its strength and natural durability but in our case that is not our first choice. For a start not all oaks are highly durable given Red Oak decays far more easily than White Oak, due primarily to more vulnerable pore structure of red oak to moisture uptake. White Oak being so hard and dense has comparative to some other types of wood a very high rate of movement when exposed to moisture that can lead to unacceptable levels of stress resulting in cracks and joint failures. The power of wood expanding when absorbing moisture should not be under estimated. Timber wedges driven into holes in rocks then wetted was used by the Egyptians to split rocks weighing several tonnes!
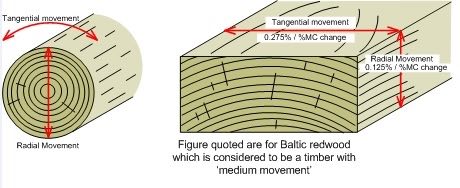
Oak contains tannic acid (the name being derived from when oak bark was used to tan leather – don’t you just love all these pub quiz facts) and this acid will continue to leach out over time, even if temporarily removed from oak surfaces by say wiping with acetone. Not surprisingly tannic acid inherently plays havoc with a bonded joint. Also whilst the high density of White Oak aids its natural durability, the downside is it does not take up epoxy resins into the grain structure particularly well. In other words the epoxy isn’t getting a good grip on the wood it is trying to hold together.
Given all of the above you will perhaps appreciate that to use White Oak was an added complication, that was in our case actually avoidable and hence why we used a different timber species for constructing the hull of Longbow.
The wood of choice for us, very kindly donated to the project by the UK’s leading specialist wood suppliers, Robbins Timber, is that which has been used traditionally and continues to be used in many aircraft and boat building projects throughout the world. That is to say Sitka Spruce sourced from America because trees of Sitka grow tall and straight, making their grain structure straight, their wood has high strength to weight ratio, it is relatively free of knots and it has an excellent take up of epoxy resin into its grain structure so our epoxy can get a good grip of it. All of this helps to ensure a fantastic bond using the WEST SYTSEM Epoxy Products, again very kindly supplied by another of our sponsors, Wessex Resins.
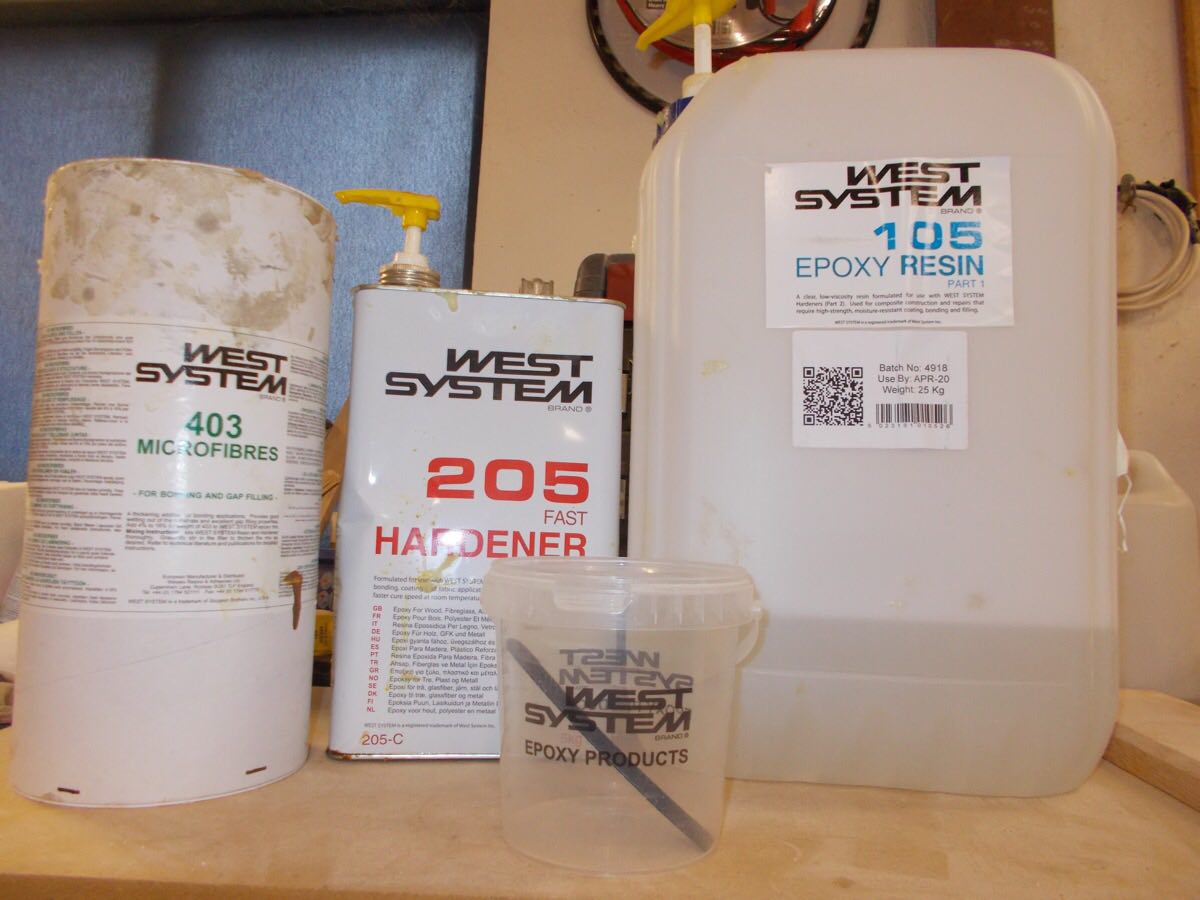
WEST SYSTEM Epoxy Products were developed by two American brothers, Meade and Jan Gougeon, who began building iceboats around 60 years ago just down the road from Dow Chemicals. As luck would have it Herbert Dow, the grandson of the founder of Dow Chemicals got into iceboating through a friendship with Meade and Jan, which in turn allowed the brothers access to Dow’s epoxy laboratory so you can guess what happened next. With Dow’s help the Gougeon brothers developed the formulations that their epoxy products are based upon. From that they built entire boats without the use of fasteners – I will just repeat that in case you missed it, there was nothing but the epoxy holding the entire boats together which just proves how good their epoxy was. Word spread fast and with further investment from middle brother Joel Gougeon, their Company went from strength to strength to make them a market leader in epoxy technology throughout the world.
The products we are primarily using at this stage of the build, on advice from David Johnson and Hamish Cook, of Wessex Resins, are the WEST SYSTEM 105 Epoxy Resin and the 205 Hardener. Allowing these two products to come together at a set ratio commences the exothermic reaction, which after appropriate surface preparation, we use in pure form to ‘wet out’ both surfaces being bonded prior to making the joints in order to prevent a resin starved joint occurring.
Once this layer of resin has become tacky, then depending upon the type of bond we require, using this same formulation with the addition of the manufacturer’s fillers to a ketchup, mayonnaise, or peanut butter consistency, depending upon what is required for each specific case, the joint is made and clamped into place with minimal pressure to cure.
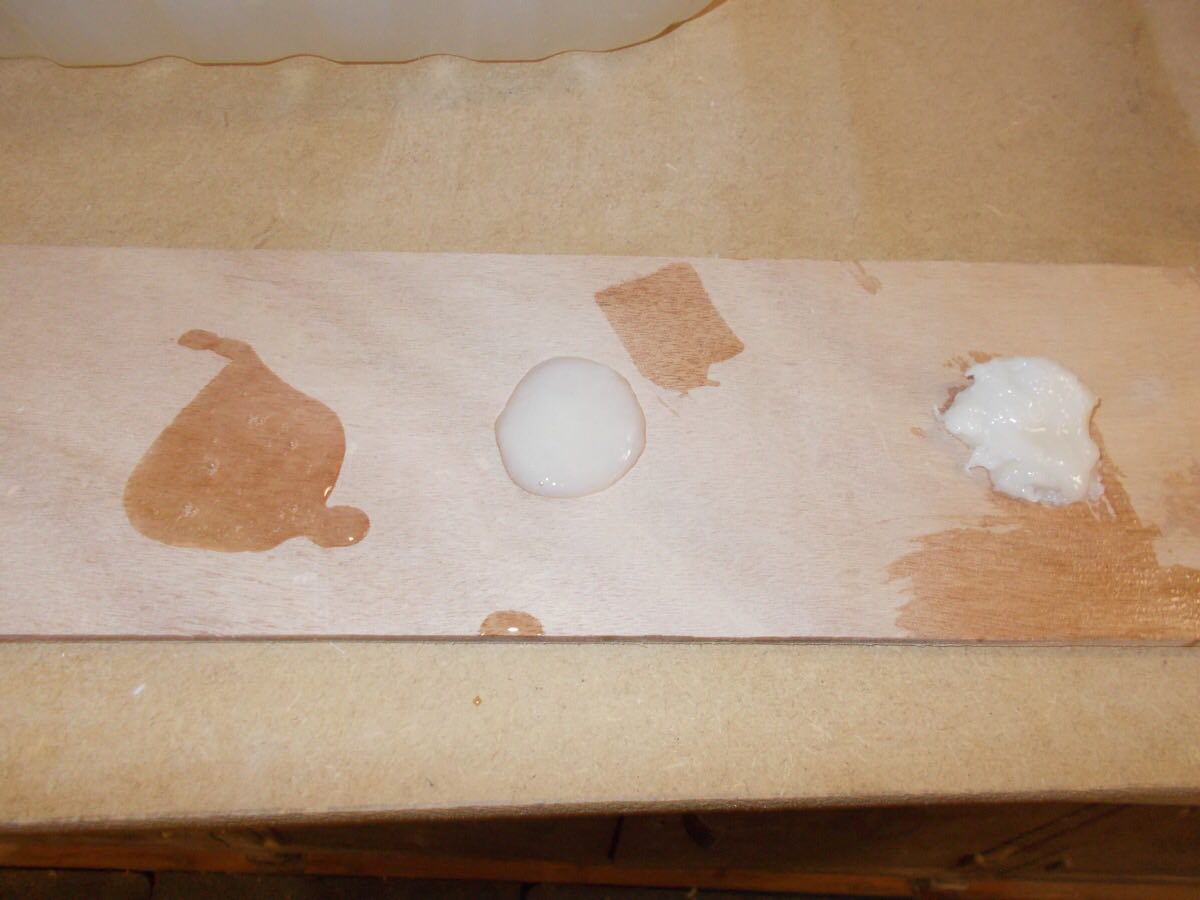
One thing you notice straight away when playing around with epoxy is the greater the volume of resin and hardener in the mixing container, the hotter the mixed epoxy becomes. 8 fl. oz or more of mixed epoxy can quickly generate enough heat to melt the plastic mixing cup! It is therefore important that once stirred together for the required time, the volume of mixed epoxy is placed on to the timber that is to be bonded without further delay, in order to dissipate the exothermic heat and allow the epoxy to cure relative to the ambient temperature within the workshop. For sizeable areas what you don’t want to do is mix a bucket of the product all in one go or you would quickly have an epoxy doorstop. What you need is several smaller containers on the go so it really is a team effort preferably with folk who are good at both counting the right amount of epoxy, hardener and filler whilst watching the clock for mixing time and application whilst trying not to be disturbed by somebody asking how many sugars do they take in a cup of tea.
As we go through into the Autumn and then Winter months we must also be mindful of (and remembering your physics class), the relative humidity (the amount of moisture vapour within the air held as a gas at any given temperature) within the workshop. This is because and referring to earlier comments, timber will readily absorb moisture just from the air in order to be in equilibrium with it and in so doing expand primarily across the grain.
Referring back to your physics class the warmer the air the more moisture vapour it will hold as a gas and conversely the colder the workshop gets the more likely we are to get condensation issues. Excessive moisture in the air will not only cause our wood to expand, it can also cause the epoxy to become cloudy, which would be unsightly, effect cure time and change its cured physical properties.
We therefore need to heat the workshop in the colder seasons but with what? If for example we were to heat the workshop with a propane or kerosene space heater then this is a ‘wet heat’ where it would yield around 0.8-1 gallon of water into the atmosphere for every gallon of fuel burnt. Whilst we could extract moisture from the air with a dehumidifier if necessary, using electrical heaters is a far better solution for our application since the radiant heat produces no moisture vapour into the atmosphere at all.
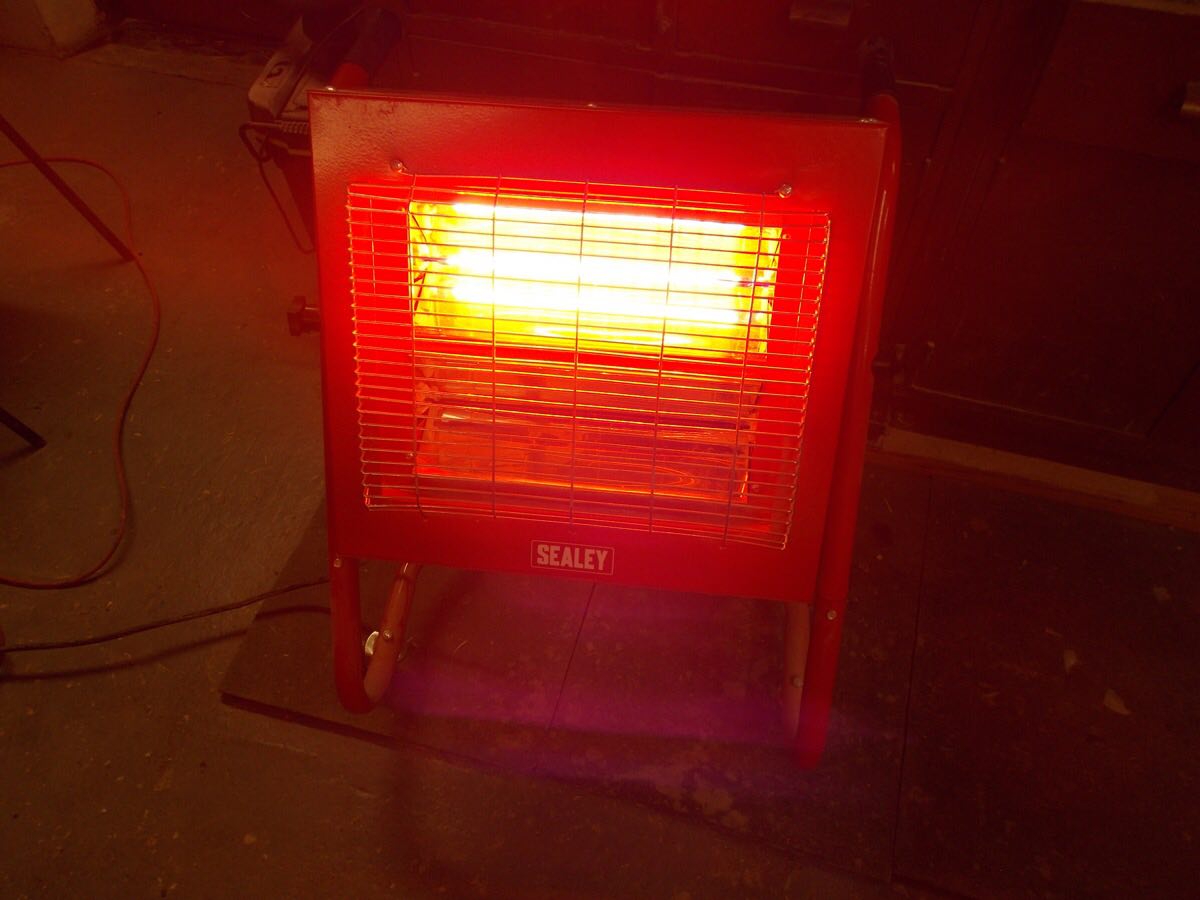
This month we had a visit from our good friend and design engineer, Paul Martin who came for a face to face catch up with the lads, have a look at the construction of the hull to date and to discuss the design and future fabrication of the all important composite driver capsule. We all took a deep breath as Paul cast his eye over things but thankfully we passed inspection and he was duly impressed by our progress, quality of the work and the considerable size of the hull for Longbow taking shape. All of which was great to have such encouraging feedback as this was the first time he had seen the build taking place in our home workshop.
From the photos we released of the build within last month’s update, you will remember that the hull for Longbow is at this stage, being built upside down so what you can see in the photos that we are releasing of the build within this month’s update, are that of the first stage of the frames to the underside of hull being cut and fitted into place.
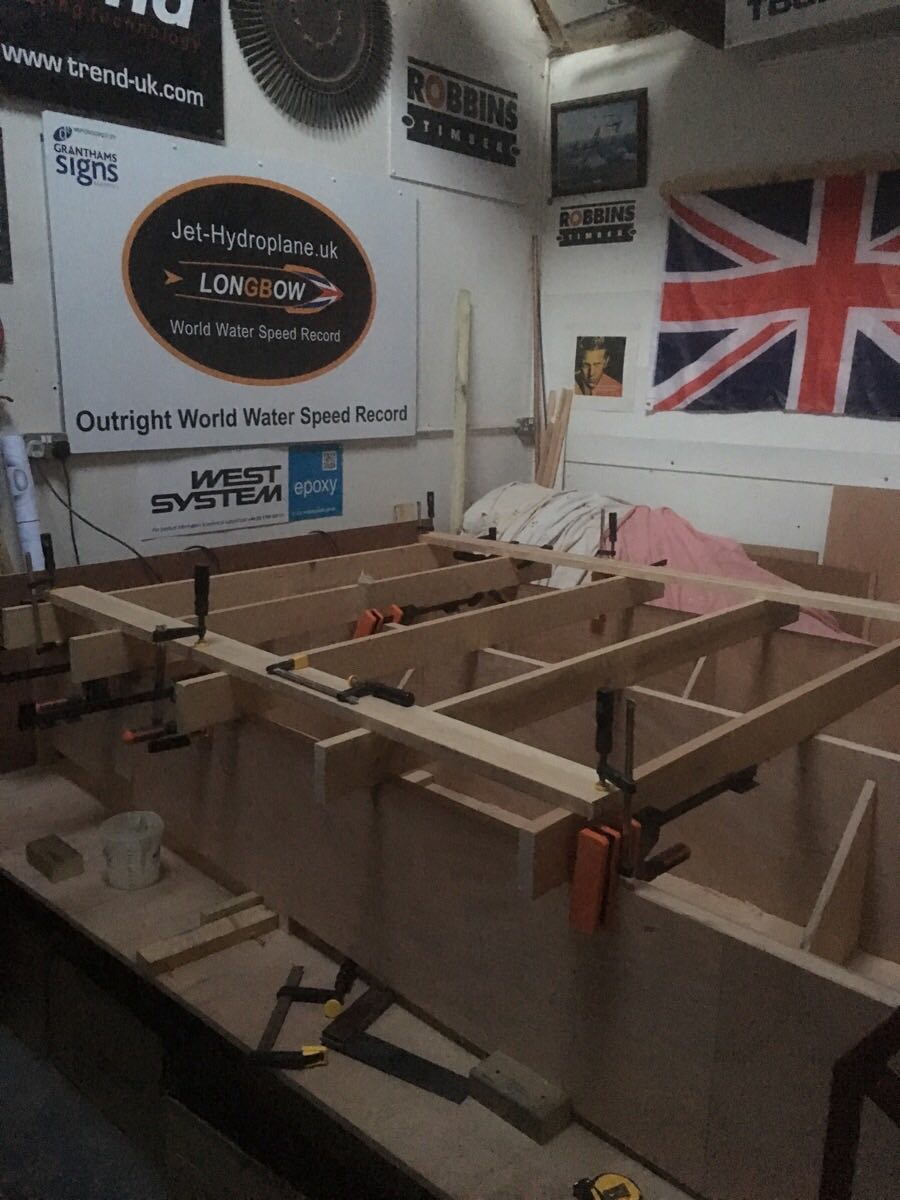
Whilst these may look to be at regular intervals this is not actually the case, as they are positioned to reflect loadings.
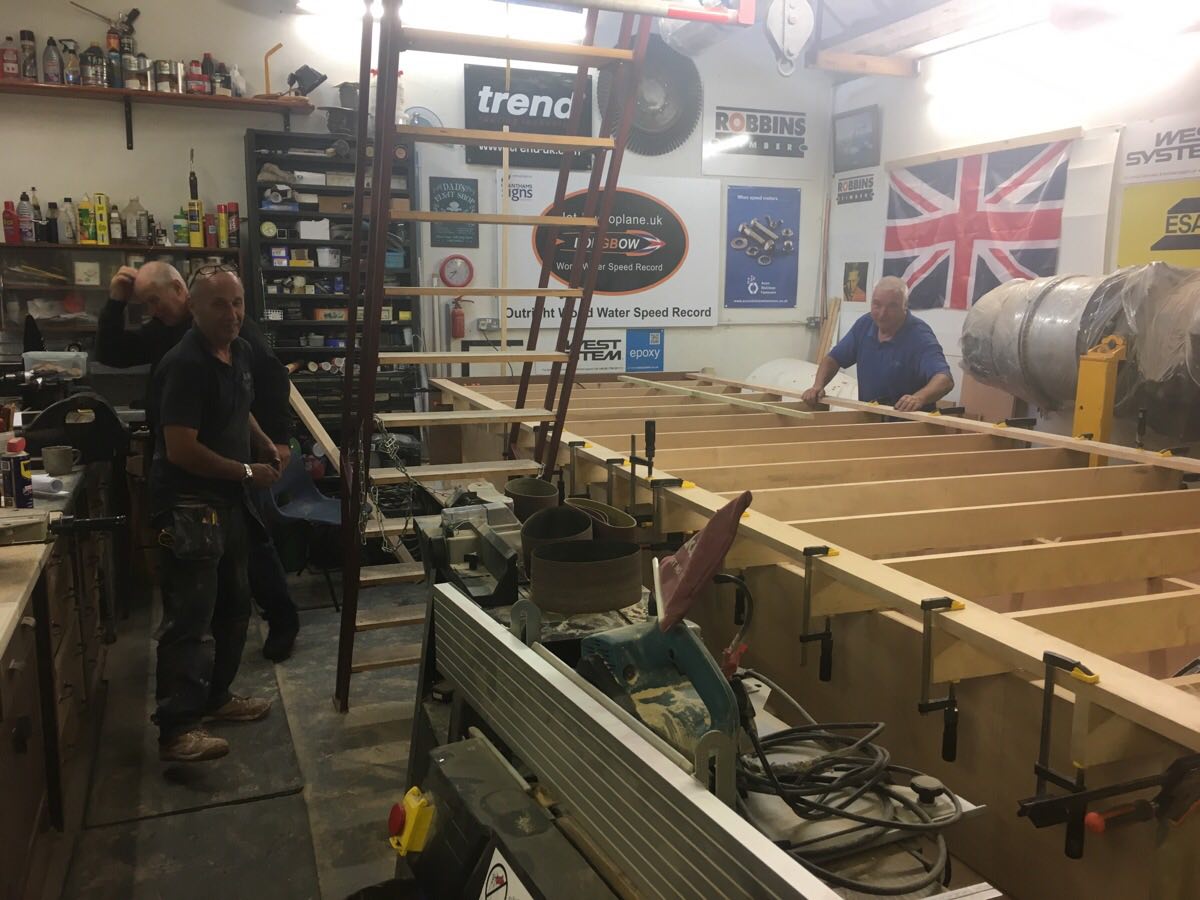
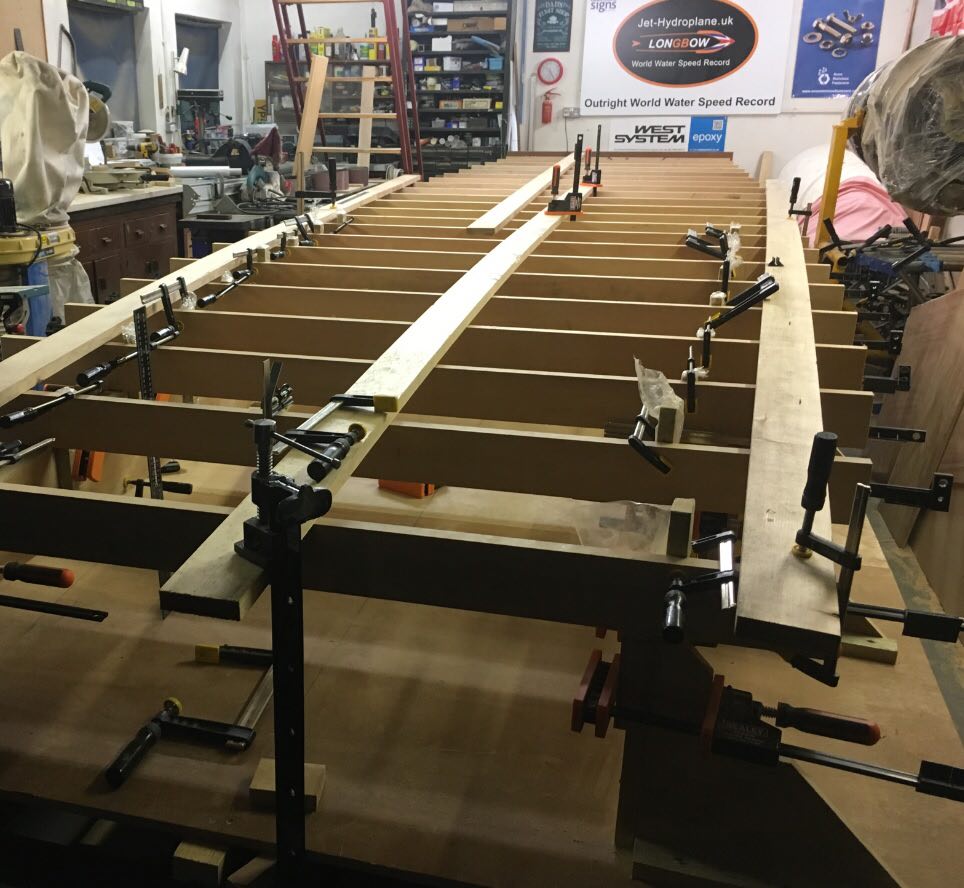
If you have the opportunity, you may wish to take a trip to Coniston Water in the Lake District, to attend the annual Coniston Power Boat Records Week that commences on 29th October, through to 2nd November, weather permitting. This popular event attracts all classes of boats from the smallest hydroplanes, through to large offshore powerboats from both the UK and abroad. Last year television personalities Jeremy Clarkson, Richard Hammond and James May along with Ed China competed at the event with their amphibious vehicles.
In next month’s update we will discuss further matters in relation to Longbow, along with revealing the next stage of how the build progressed.
Sorry if we have bored you with talking about wood and epoxy this month but they are pretty fundamental to the hull construction and perhaps you will have a better understanding of what is going on in the photos herein and to follow as a result. Once again thank you for tuning in to our little venture as Longbow progresses in taking shape and we hope that you continue to spread the word that this is a project worth following, to which people at home can relate to and see actually happening for this British Attempt upon the Outright World Water Speed Record.
Remember clocks go back this weekend, happy Halloween and stay safe on bonfire night, from all at the Longbow Project !