Well this month’s starter for 10 is what does a radio control set, a jazz band leader and a jet hydroplane all have in common? The answer is they all relate to a question I was asked this month by one of my friends following our little venture. That being had I ever considered of when we have finished building our jet hydroplane Longbow, about running her by remote control to check she performed as intended before putting a person in there to physically drive her. In effect like a 1:1 full sized model. They reasoned that surely the technology must be there to do that these days.
My reply to that question was yes indeed the technology is there to do it if the driver so wants to run with that option but that actually this was nothing new and had indeed been done over 60 years ago by a Canadian-American band leader called Guy Lombardo. Guy along with his brothers and orchestra called the Royal Canadians was at that time a celebrity on radio and television as a gifted musician who in his spare time had a great passion for powerboat racing. Guy had a full size jet hydroplane built called Tempo Alcoa and as part of its development had run it by remote control. The name Tempo Alcoa being in the first part a recognition of him being a bandleader and the latter half, Alcoa being short for the ‘Aluminium Company of America’ who had sponsored the build as a marketing platform for their materials.
From 1946-49 Guy was the National Boat Champion within the USA in addition winning a great many other hydroplane championships including the prestigious Gold Cup with his series of propeller driven hydroplanes mostly under the Tempo name. Not surprisingly in 1955 Guy and his boat racing friends had gone along to seen Donald Campbell running his jet hydroplane Bluebird K7 on Lake Mead in the USA and from that encounter Guy set his sights on wanting to beat Donald’s Outright World Water Speed Record.
To this end Guy commissioned a respected and successful hydroplane builder by the name of Les (Lester) Staudacher to build him a new pure thrust jet hydroplane using aluminium for the hull sponsored by the Aluminium Company of America. The design was tested as a scaled model in the wind tunnel of North American Aviation and was based upon a larger version of his racing propeller driven hydroplanes. A model of the craft is shown below:
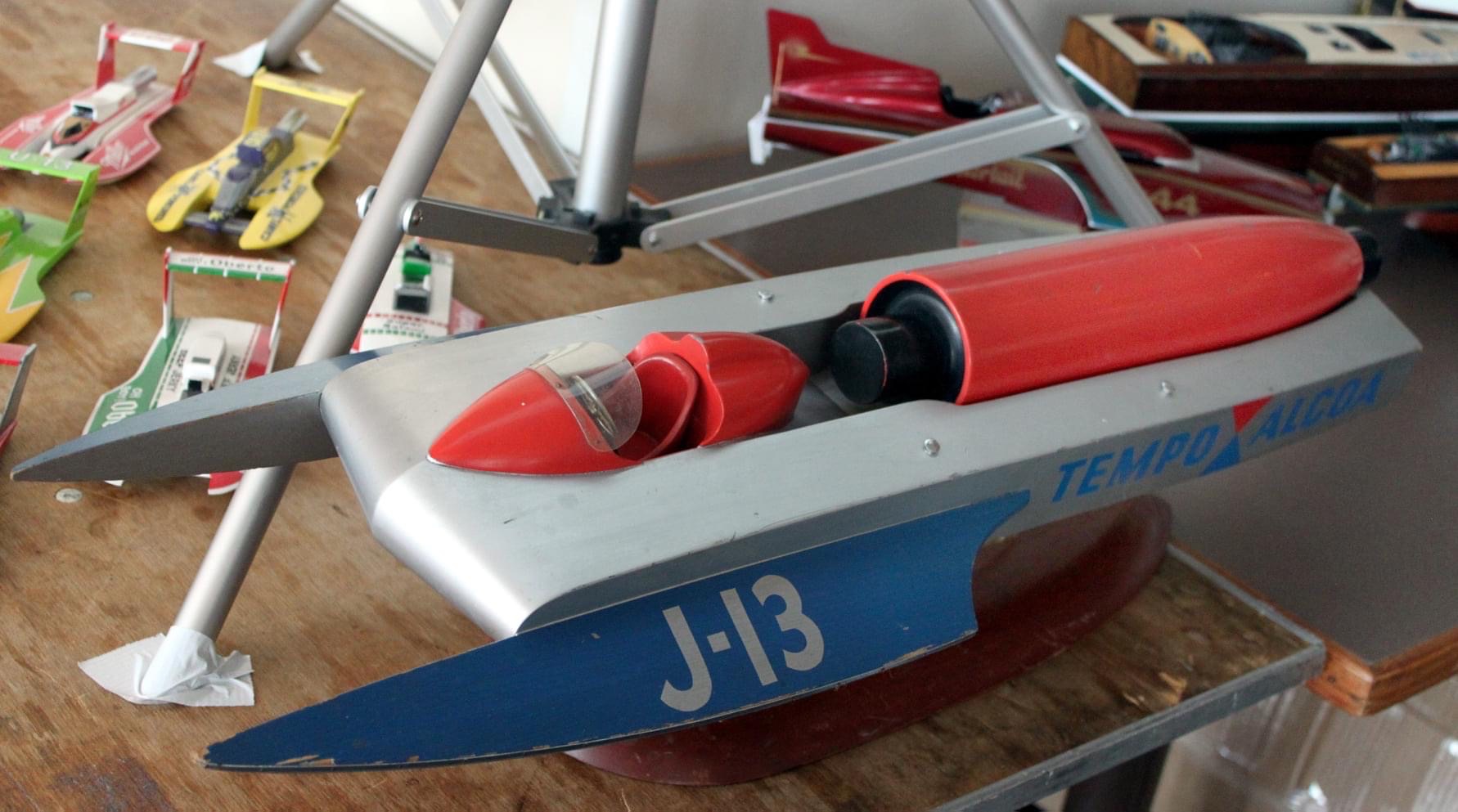
Courtesy of Leslie Field
The jet hydroplane was powered by an Allison J-35 turbojet developing over 5500 lbs of static thrust as used in the American F-84 Thunderjet fighter aircraft and Tempo Alcoa was launched in 1959 at Saginaw Bay, Michigan where it was tested to over 175mph. This engine in Tempo Alcoa developed 1500 lbs more thrust than the Metroplotan-Vickers F.2/4 ‘Beryl’ turbojet that Donald Campbell had won all his water speed records with, so in theory the craft had more than enough thrust to go quicker than Bluebird’s then fastest Water Speed Record of 248mph and bring the title back to the USA. Video of Tempo Alcoa under test is shown on the following YouTube link:
After this series of successful initial test runs Tempo Alcoa was taken to a larger stretch of water for higher speed tests with the venue chosen as Pyramid Lake, Reno, Nevada which is relatively close to Lake Tahoe where Guy was playing with his band at a Club so that he could mix work with pleasure. Les Staudacher was testing the craft for Guy and had reportedly reached peak speeds well in excess of the Water Speed Record and Guy was keen to take over the driving.
In one pass late in the day Les was running at around 180mph close to shore for the benefit of the Press photographers present at the time who had requested he do so in order for them to shoot the publicity pictures they needed for the craft in action.
However by this time the weather had changed from being relatively calm to a windy rippled lake surface and that not being taken fully into account would be an issue with dire consequences.
Les commented that running upon calm water Temp Alcoa would take around half a mile to stop from 200mph once he had closed the throttle to the jet engine but in choppy conditions that stopping distance was found to be extended by three to four times. Running so close to shore for the benefit of the Press, Les now had a peninsular called Pelican Point (now no longer open to the public), looming ahead of him and he said that once he closed the throttle he could see the peninsula but with the choppy conditions Tempo Alcoa had no chance of stopping in time.
As a result the jet hydroplane crashed at high speed into the end of the peninsular and Tempo Alcoa then took off into the air, with the crash tearing off the rudder and damaging a sponson badly. Les had miraculously managed to escape the whole incident unscathed. Guy however who had witnessed all of this with his friends and spectators ran to the scene of the accident but in so doing Guy took a bad tumble on his way down to the shoreline in search of his friend. Somewhat bizarrely it was then the unhurt Les who had been driving Temp Alco that ended up driving Guy to hospital at Reno in his car to be patched up.
Les then took the Tempo Alcoa back to his boatyard and spent several months repairing the damage he could obviously get to but apparently some of the internals of the damaged sponson were not fully opened up for inspection and if necessary appropriate repair. After the repairs that were done the boat was taken on tour around the USA and then at a cost of $2,500 which was quite a sum in those days, North American Aviation devised a radio operated remote control system for the craft. This was undertaken at Guy’s insistence, so that they could run the jet hydroplane at speed to check the integrity of the hull and the repairs undertaken, prior to Guy or Les driving her.
Tempo Alcoa was therefore run completely by remote control in Saginaw Bay at ever increasing speed increments in several passes, which with no driver in the open cockpit must have been quite something to see. At around 200mph however disaster struck when it is thought the sponson previously damaged at Pyramid Lake, broke away resulting in her veering sharply to the right, rolling and then total loss of the craft as it sunk to the bottom of the Bay. Fortunate indeed that there was no driver aboard at the time.
The craft was later located by divers and subsequently recovered but was found to be a complete wreck. The Aluminium Company of American (Alcoa) offered to supply metalwork and finance a total rebuild using new material throughout but by this time Guy was under pressure from his wife Lilliebell and friends to go back to making music, which he duly did with three stars on the Hollywood Walk of Fame in Los Angeles and he passed away from natural causes at the age of 75.
Les however was not finished with jet hydroplanes and went on to build another in the hope of achieving the World Water Speed Record such that we will return to his story in a future Longbow diary update.
Bringing things back up to date our good friend Dave Warby over in Australia has managed to have his new tailfin painted and fitted for his jet hydroplane Spirit of Australia II and a superb job they have made of it too. Dave is currently making a cowling for this new lay out that will extend over the very end of the jet pipe:
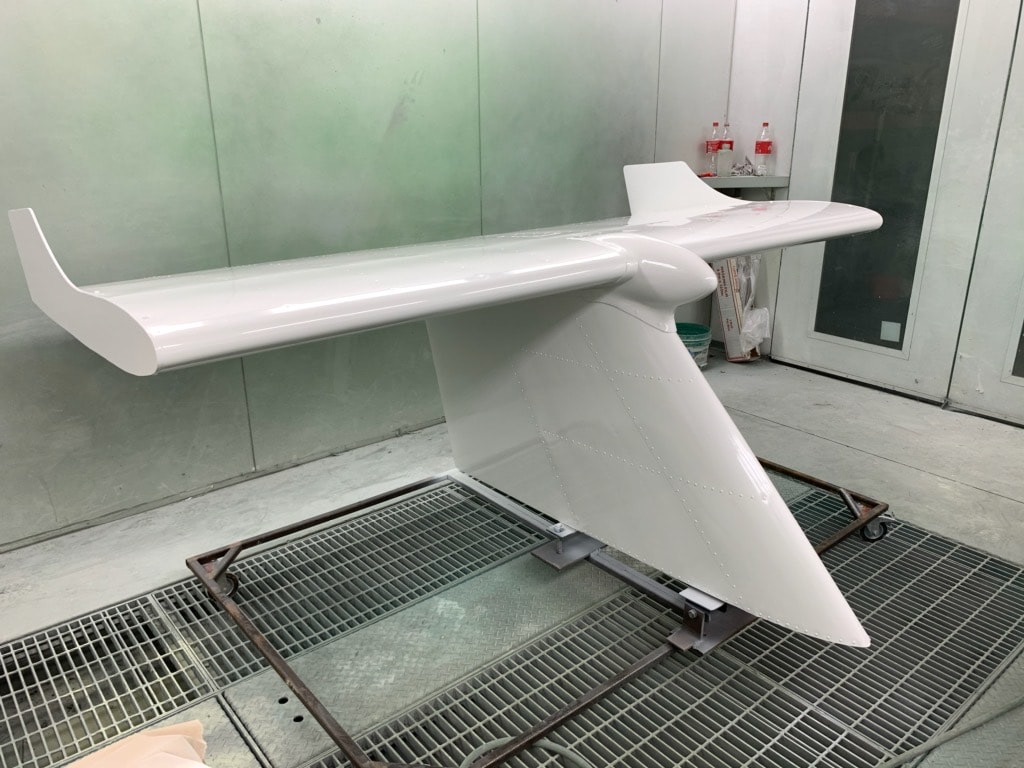
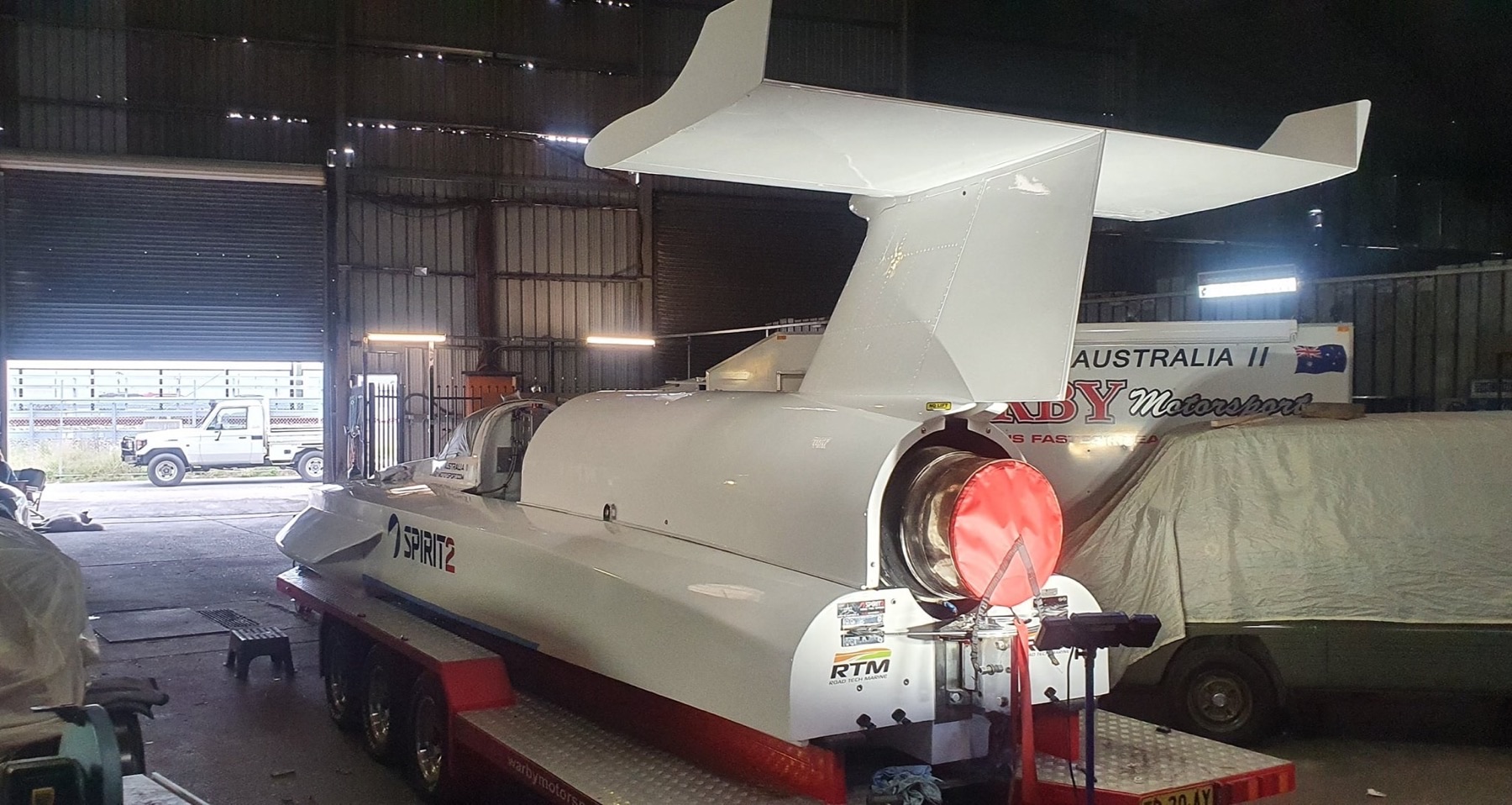
Dave and his team have also reinstalled the Orpheus turbojet back into the craft and were then able to do several successful static engine tests to run through all the systems in preparation for their next round of trials out on the water. This will hopefully be in November subject to COVID restrictions being lifted at Blowering Dam, which is reported to be currently 80% full. Unfortunately Dave got shunted from behind in a road traffic accident this month which gave his back and brain cells a right good rattle by all accounts though thankfully other than seeing stars for a while and walking like he fell off a horse it won’t stop the next round of tests. The conclusion appears to be that he is safer in his jet hydroplane out on the water than driving his car with work!
Back here with Longbow and my good friend and electrical engineer John Fielding who has been helping out with wiring up our jet engines has managed to catch COVID this month which wasn’t the news I wanted to hear. It has run through his immediate family but thankfully all of them seem to be making a good recovery. The last time we spoke John was struggling to obtain a test to confirm whether he is now negative or not for COVID, which has left him in limbo with regards to going out. However in any case the area within which we both live is now back in lockdown, due to the spike in local cases of the pandemic here so we cannot meet to work on the electrics for the craft in any case.
Darren Spinage of Trend Machinery & Cutting Tools Ltd who are sponsoring the project very kindly sent us everything we could possibly need to keep our wood chisels and planes razor sharp this month and it is great to have such ongoing support with such superb quality equipment.
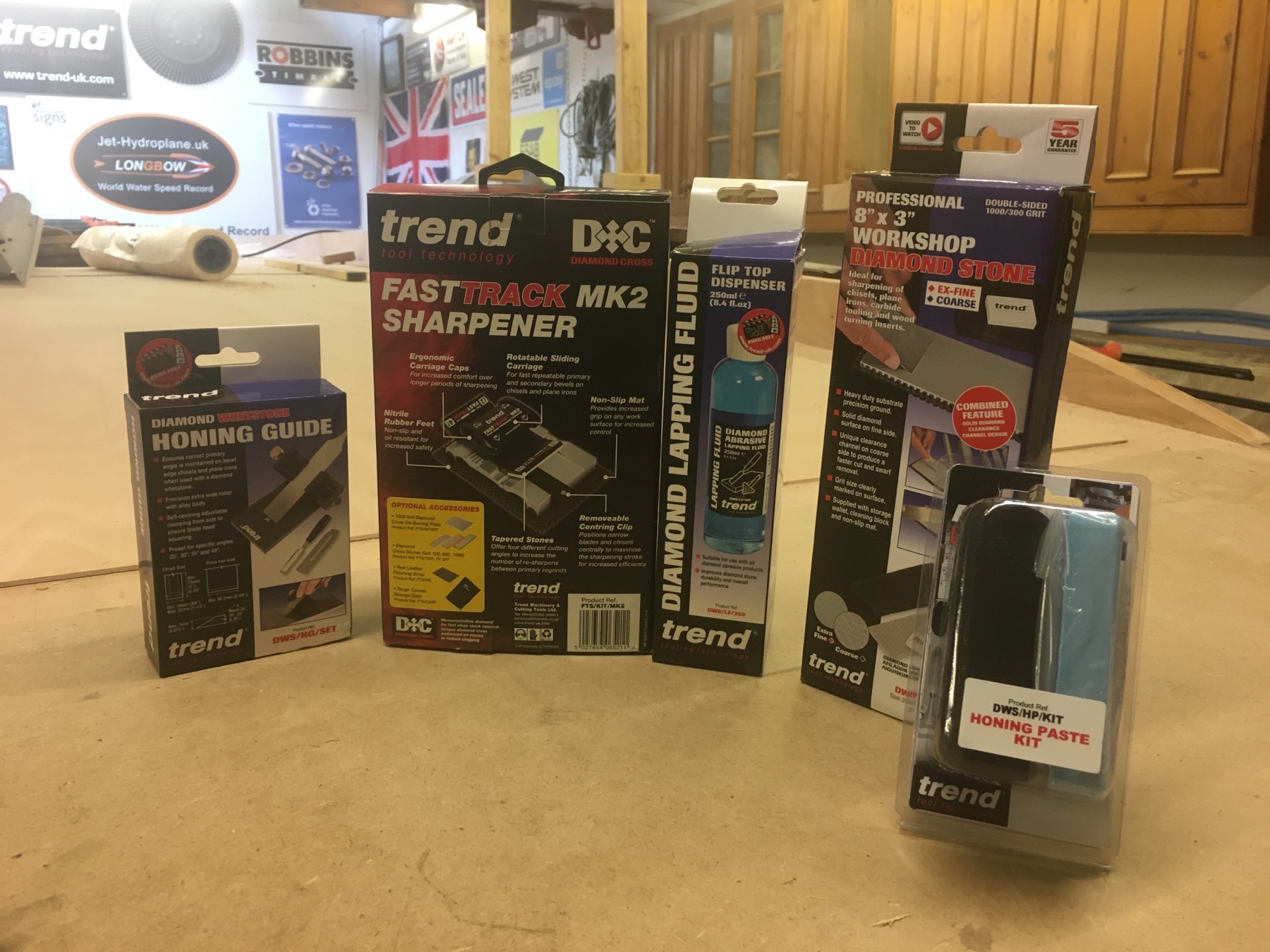
This month I finalised the drawing for the trailer which Longbow will continue the build upon, once I have completed the work on the underside of the hull and she can be turned over to be the right way up. This drawing was important to finish as we received great news from Kris Mercer at our sponsor fabricator, WEC Group that they should be able to start building the trailer next month with steelwork supplied by our sponsor John W. Laycock and running gear from Peak Dynamics being delivered to WEC Group for that process to begin.
I have yet to figure out how I am actually going to turn Longbow over on my own given COVID restrictions which look set to be in place for some time that prevent others from coming to the cottage to assist as they have in the past. She is with the sponsons now attached too wide to spin over inside the workshop so one thing on the list of how and when that will happen is going to be not to attempt it whilst it is raining or indeed snowing as we go into the winter months here.
I am often asked how I arrived at the size to build Longbow so the following will hopefully give you the formula for how this was arrived at. At the transom of Longbow there is a couple of inches between the rear corner of the craft and the adjacent metal shelving, just enough to sand that area by hand and just 13 inches between the back of the hull and the rear of the workshop.
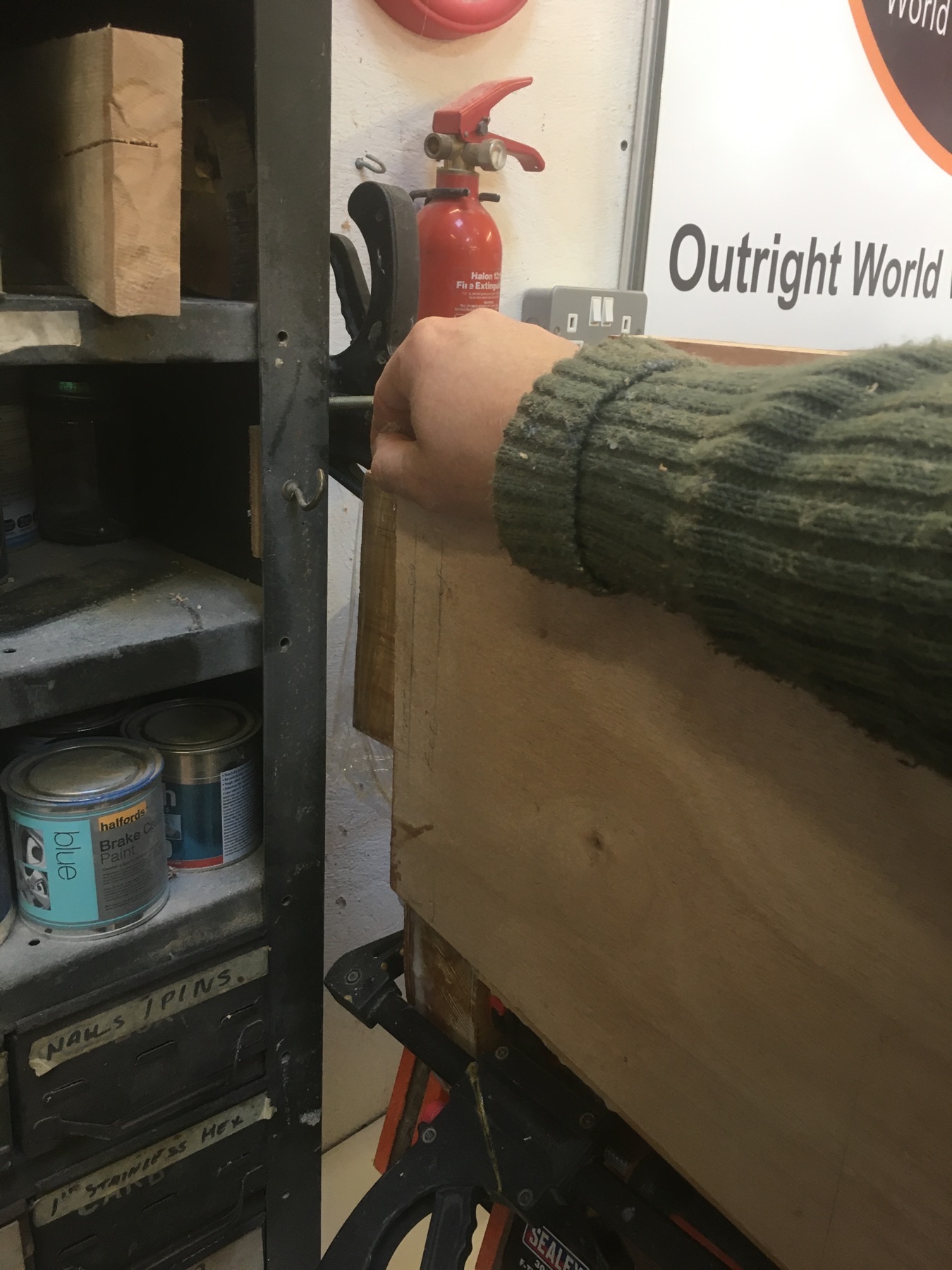
That 13″ gap should just about accommodate the rudder when fitted. When Longbow is taken out through the workshop doors there will be a 1″ clearance between the door frame and the side of each sponson at her widest and the front of the workshop is such that there is just enough gap to walk around the front of the boat between the bow and the workshop doors.
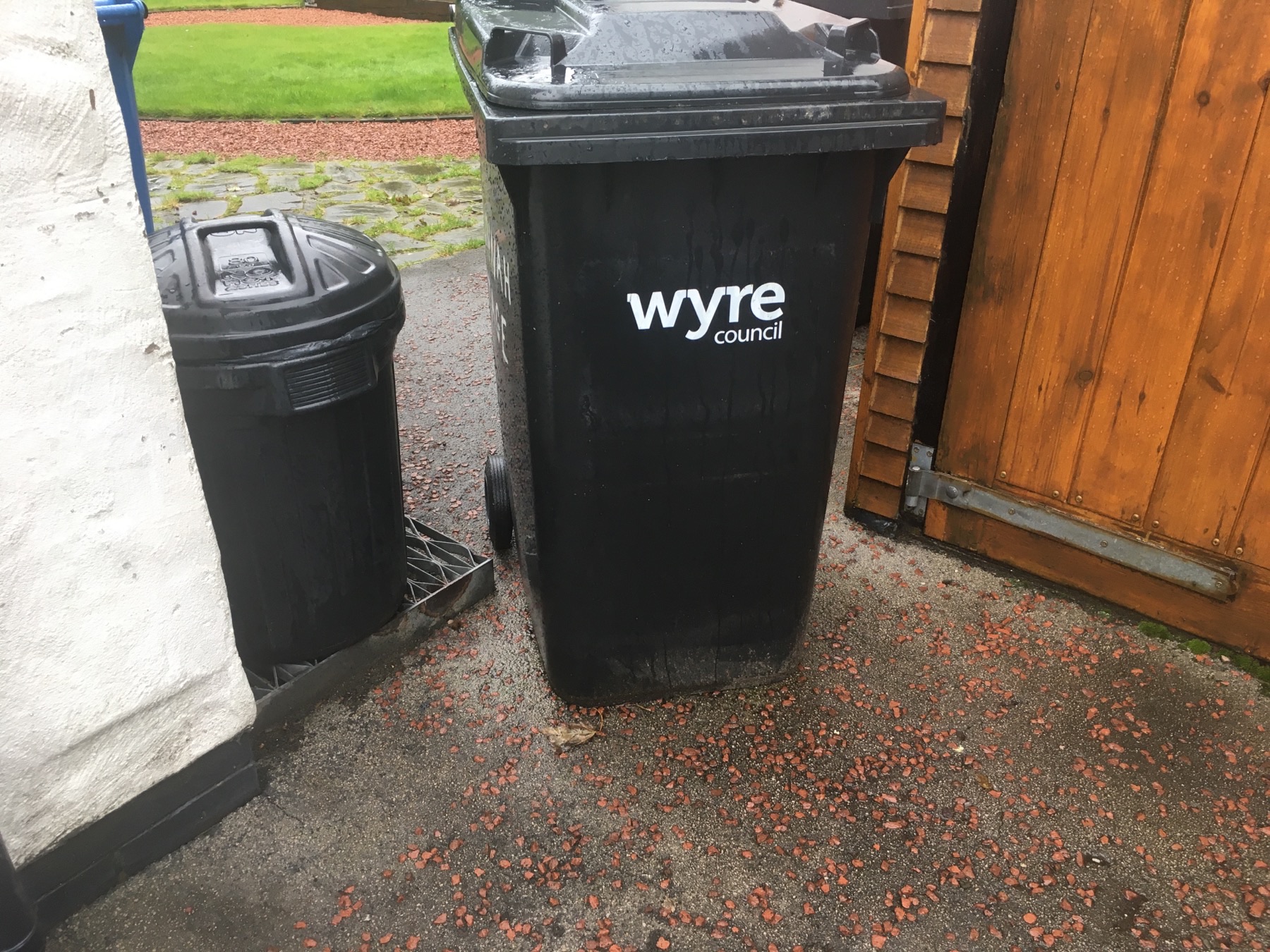
Those doors cannot come out any further and still allow the refuse bin to be wheeled through the gap between the cottage external wall and the workshop.
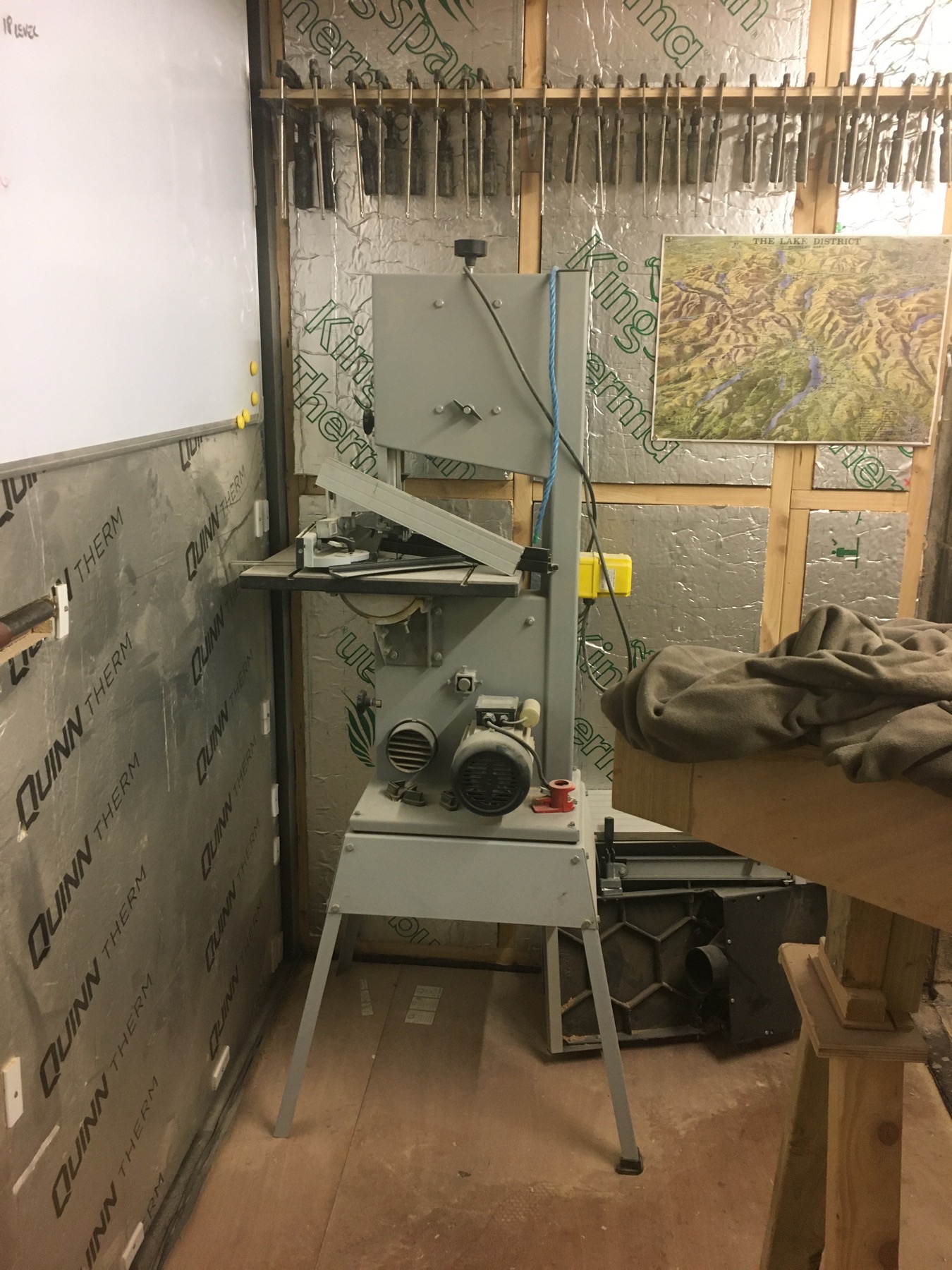
I hope that explains how big I decided to build my jet hydroplane!
I cannot fit the rear planing shoe until I can confirm the actual finished depth of the sponsons when I have completed building them as it is easier to adjust the rear shoe fitting to match the sponsons depth than attempt to do it the other way round. In turn I cannot fit the rear shoe until the final sheet of plywood is in place on the transom so this month fitting that rear sheet was on the list of things to do.
As you will appreciate from the above with only 13 inches between the back of the hull and the rear of the workshop wall there wasn’t a great deal of room to squeeze in there to prepare the surfaces but claustrophobia is not something I suffer from given I go under floors for a living. That minimal space between rear of hull and rear workshop wall did however come in handy to place jacks and wedged props to hold the plywood flat against the transom whilst the superb WEST SYSTEM EPOXY supplied by our sponsor Wessex Resins cured.
Assisting with that task of holding the plywood in place were used tins of Aptimil baby milk courtesy of my grandaughter and more appropriately the use of our sponsor Raptor and their engineered composite fixings direct from the USA, the latter of which I cannot recommend highly enough as they can be sanded flush whilst producing a superb positioning fix during the curing of the epoxy.
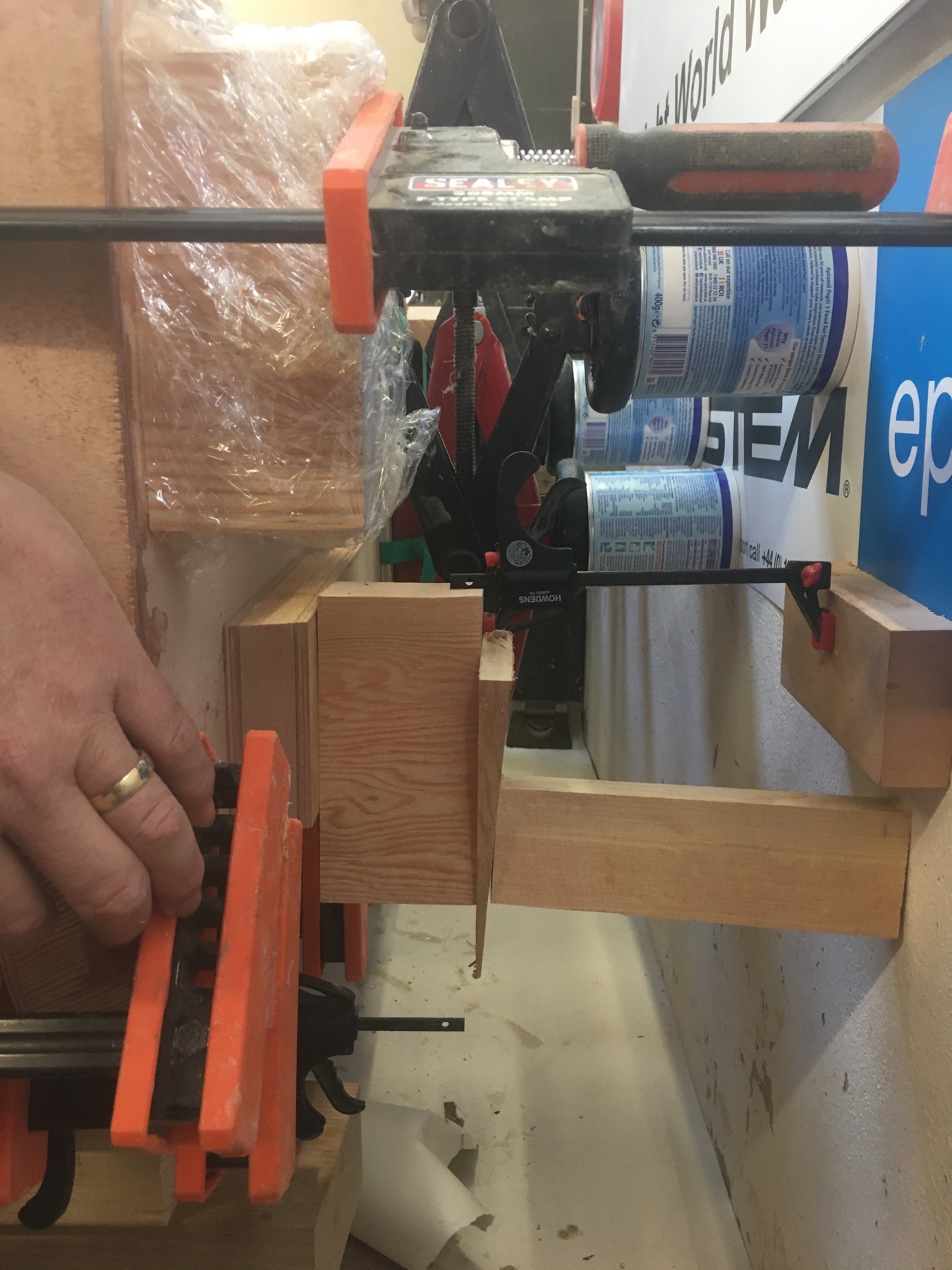
A quick word here about when wooden boat building using softwoods and plywoods, and the difference between using epoxy compared to say a powdered Urea Formaldehyde resin such as Cascamite, Aerolite, etc. In my experience epoxy is vastly superior in every respect for this task and an example of that would be that Urea Formaldehyde adhesives typically require a mechanical fixing to back them up such as screws and nails permanently fixed into place, whilst on the other hand epoxy timber joints do not need this additional assistance. Any fixings of wooden joints whilst using epoxy are there simply to hold the timbers in place whilst the epoxy cures. I also find that Urea Formaldehydes are far more brittle than epoxy whilst epoxy makes the material stronger, more stable and waterproof, thereby addressing many of the problems associated with wooden hull construction.
The next task this month was to cut out of the frames that make up the sponsons in order to receive the last of the timber runners that form the backing for the shoes and chines (angled lower sides) of these critical running surfaces.
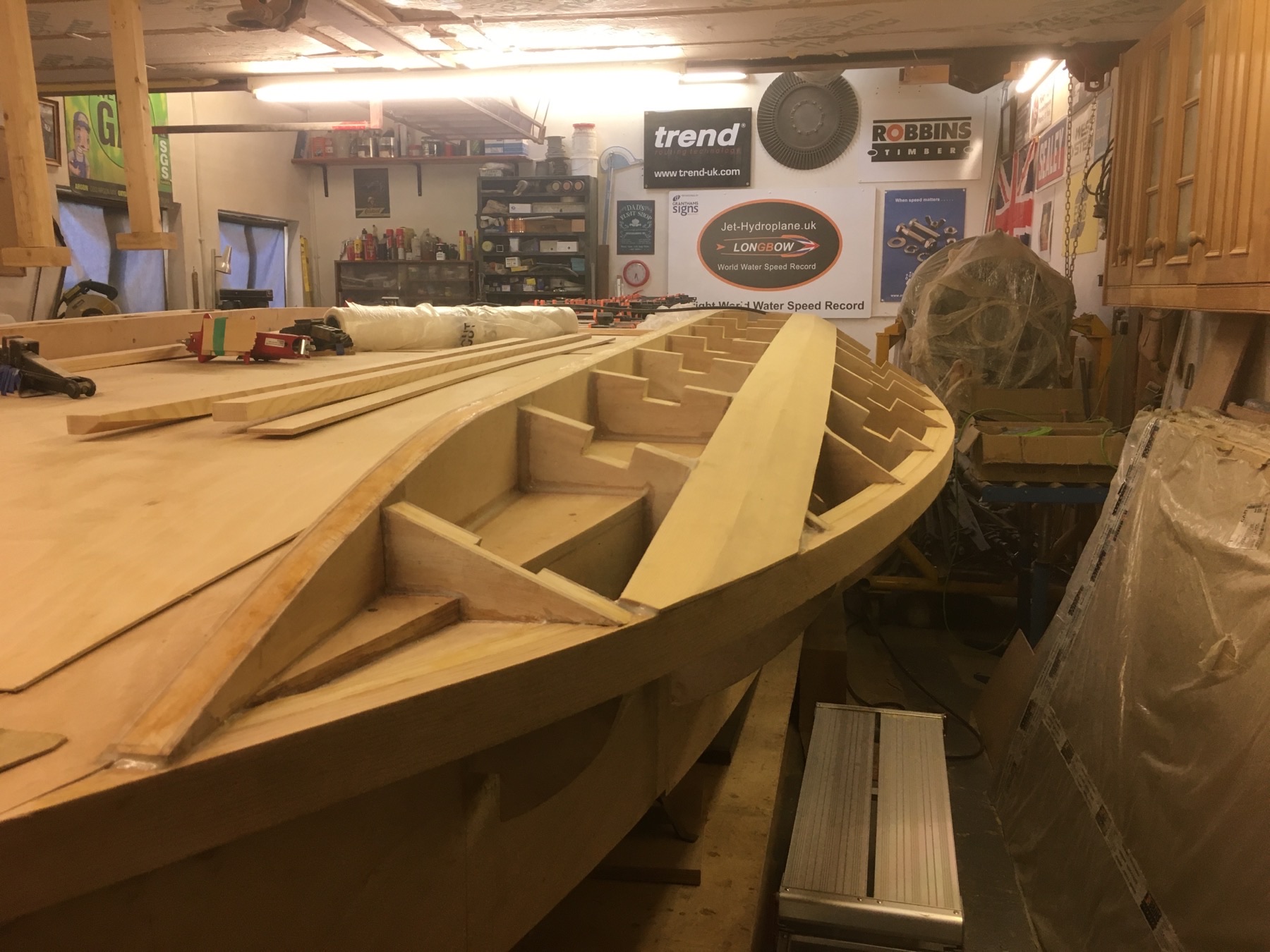
Once I had done this notching of the frames all at different angles, then areas which would be difficult to reach once the sponson shoes are in place, were sealed against water ingress with pure WEST SYSTEM EPOXY and then the timber runners could then be bent, twisted into place and jacked, wedged down from the floor above, whilst again the WEST SYSTEM EPOXY cured to permanently fix these elements into place. As you can see from the photo there are no actual screws or nails holding these runners in place, just total reliance upon the epoxy doing what it is designed for.
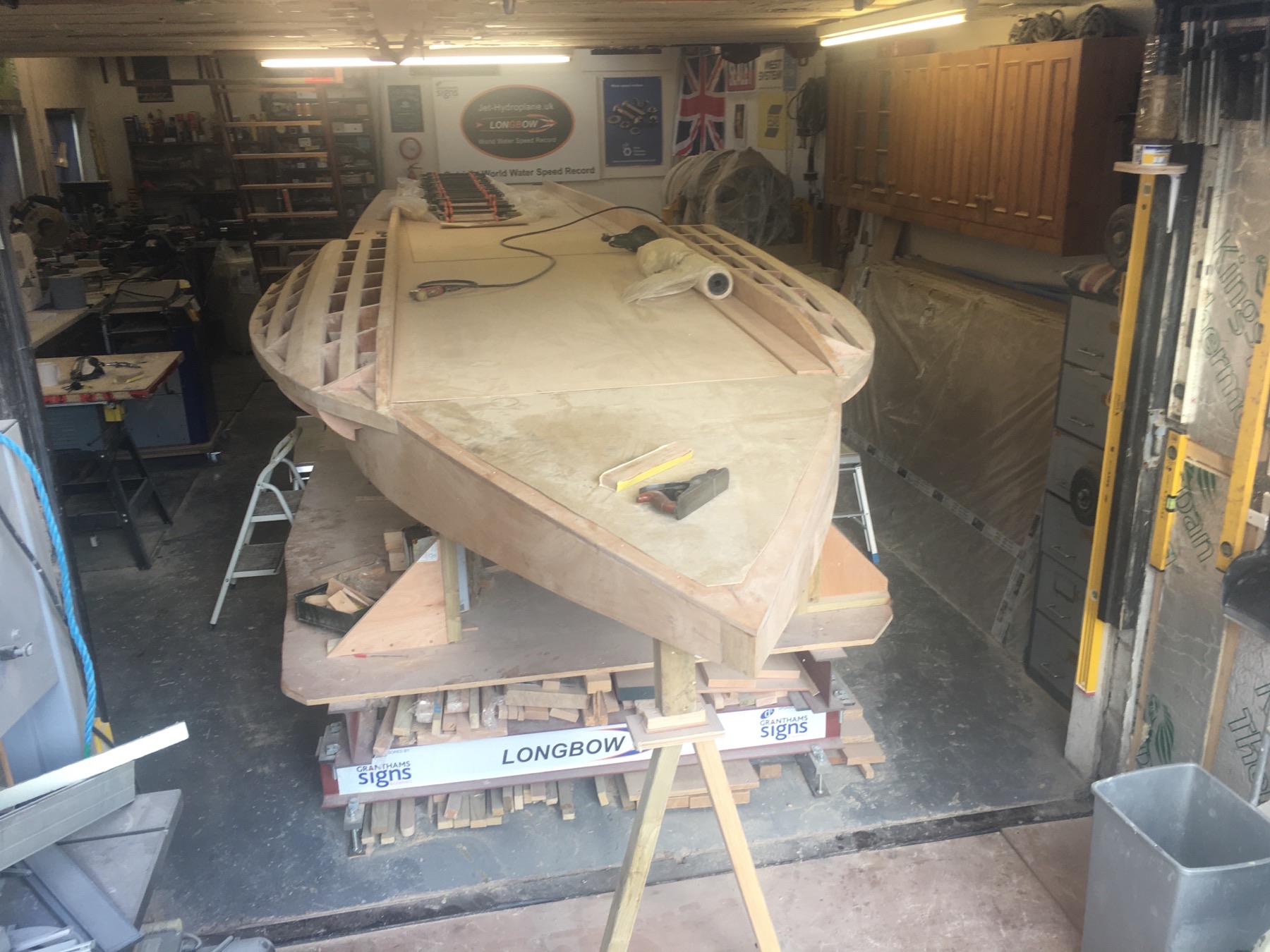
Having then cleaned the area up I was rather pleased with the sponsons taking shape and whilst you may think that all there was to do next is to cover them with plywood laminates, there is actually a great deal more work to do to them by way of shaping, sanding and providing drainage pathways within the sponsons before I can reach that challenging stage.
Also this month we had a wonderful present from my good friend and gas turbine engineer Paul Davidson by way of the specialist wiring needed between the jet pipe thermocouples and the respective exhaust gas temperature (EGT) gauges. This is critical to ensure that the gauges receive the correct signals from the thermocouples and hence you cannot use any old wiring or connectors as that would alter the reading dramatically. So typical of Paul, the best of friends to supply me with such, so a very big thank you there.
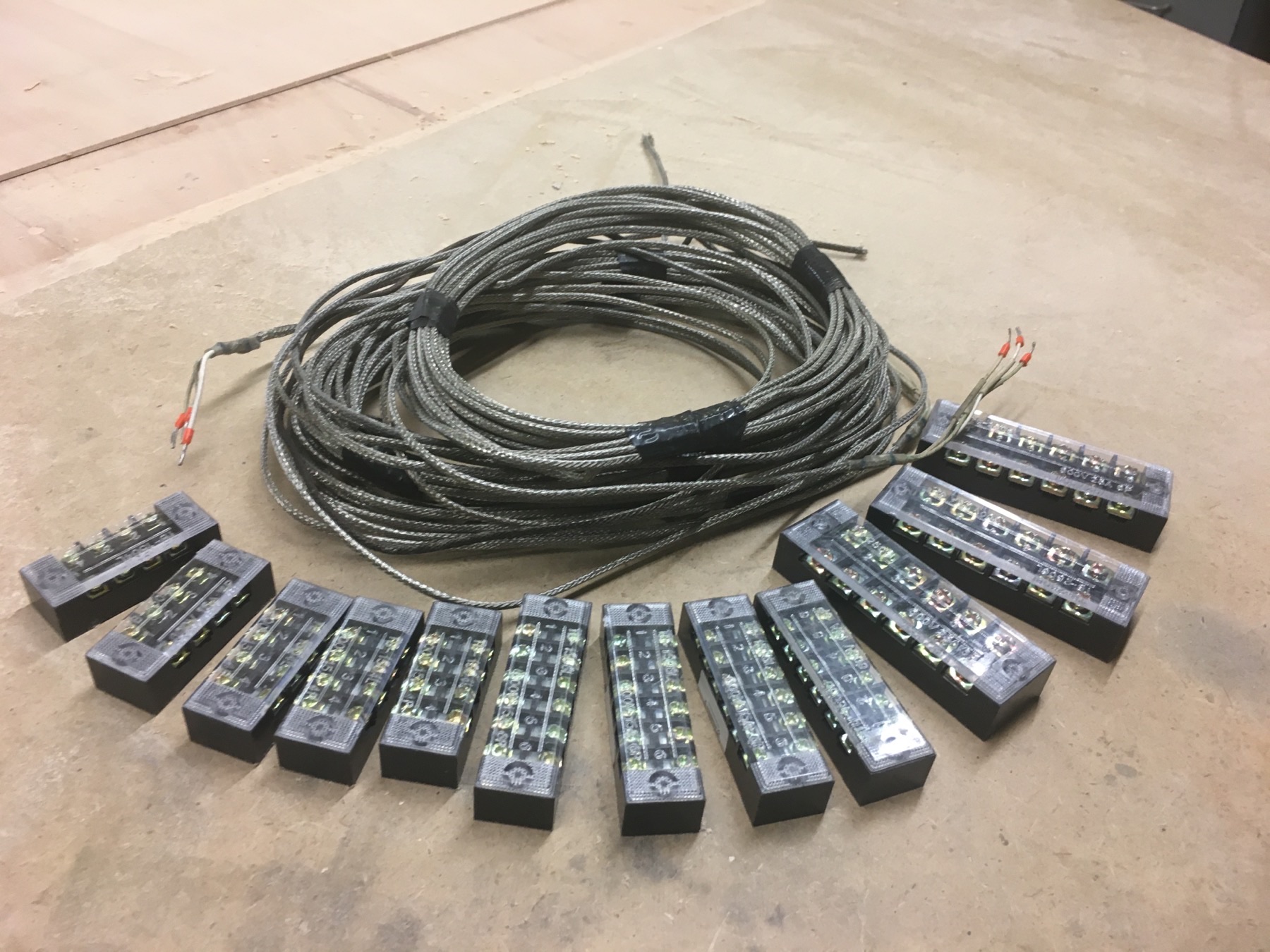
Well that is all for this month folks, thank you for dropping by for a catch up, stay safe out there in these most challenging times as we patiently hope for normality to resume as opposed to hopefully not becoming a patient.