An early monthly update this time around folks as our website guru Neil of Progress Concepts is off for a well deserved holiday, so we pestered him just before he goes away to squeeze this one in before he jetted off.
Fortunately for Neil and those who get bored easily I am able to keep this month’s update short and sweet as we are still in the process of collating all the different elements of our twin jet engine cradle together for fabricating. The following photo shows our metalwork sponsor John W. Laycock based in Keighley, W. Yorks cutting the steel plate material for our engine cradle using their newly acquired Kronos plasma cutting machine which is done extremely accurately by computerised numerical control (CNC) process. Excluding the round T45 tubes that make up the engine cradle assembly there are no less than 154 metal plate items that I have had to draw up individually in CAD for the Kronos software to read correctly. This being the case I hope my drawings for the plates are correct otherwise it is going to be somewhat embarrassing for myself.
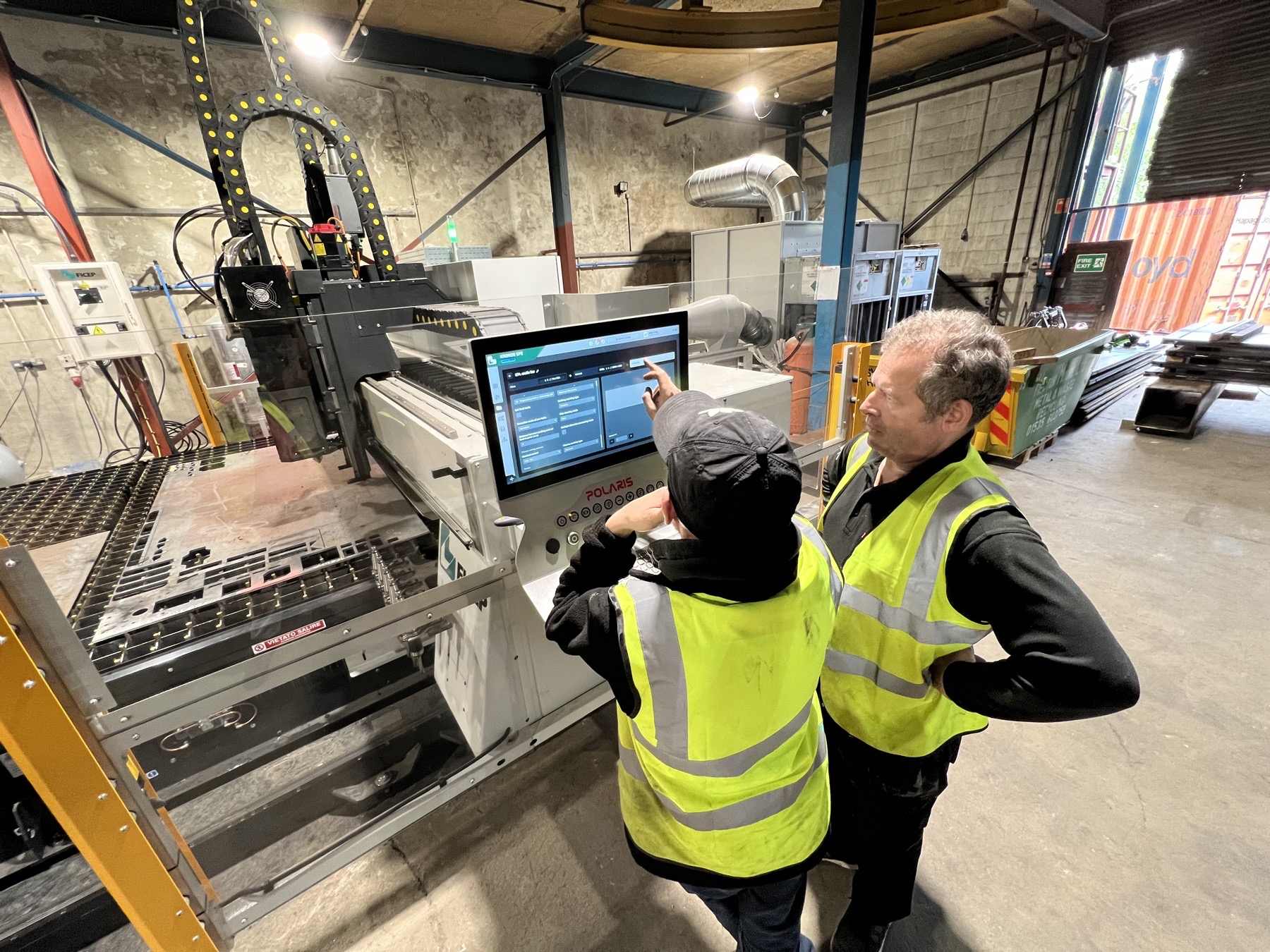
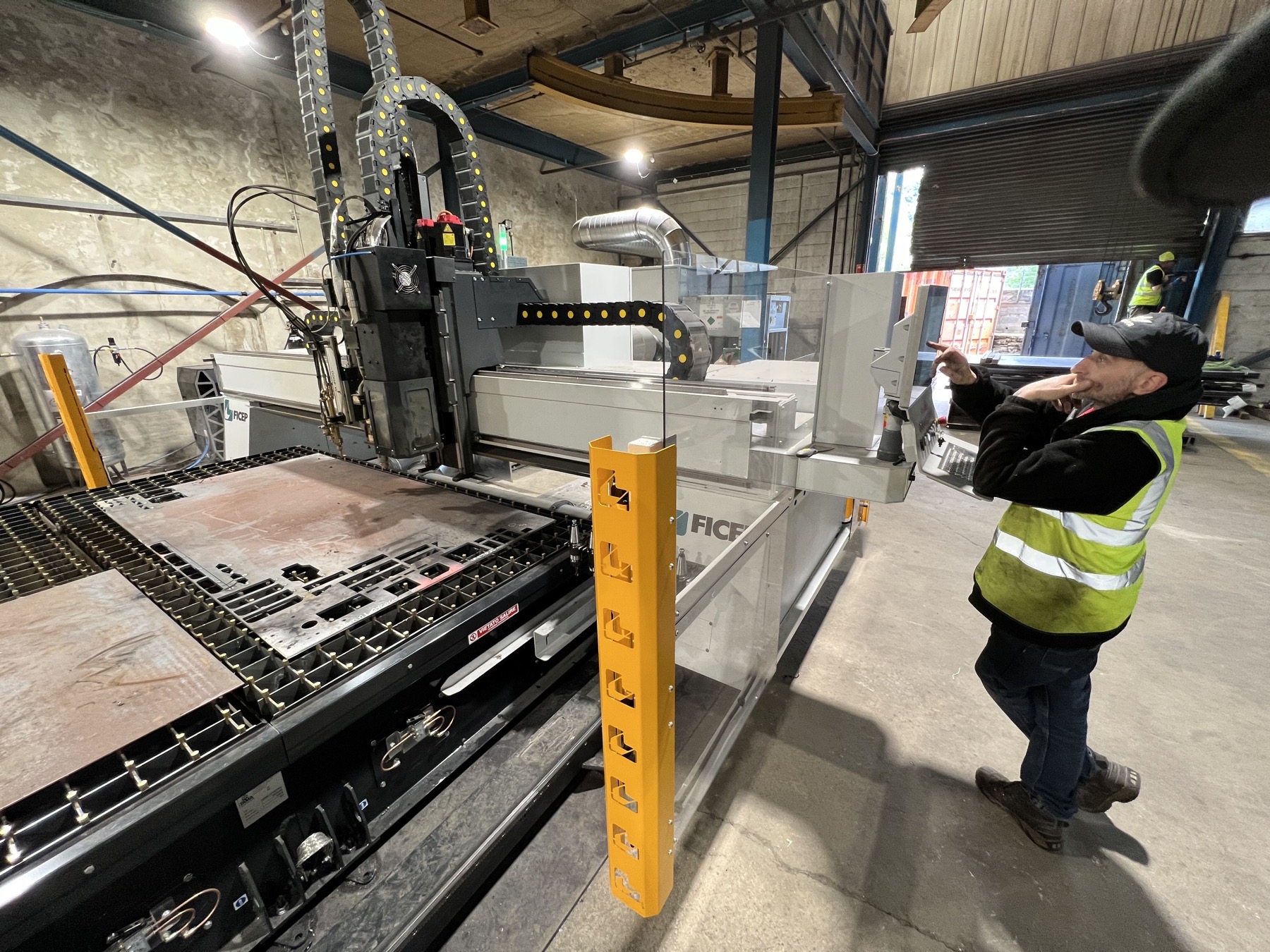
Meanwhile my good friend Ian from IAW Engineering at Blackpool has been undertaking work for the actual mounting of our twin Rolls Royce Viper Mk 535 jet engines on to the supporting cradle. I first came across Ian when working upon the loose replica of the iconic jet hydroplane Bluebird K7, the K777 over a decade ago and you can see Ian in the video below milling one of the trunnion mountings for us.
The word trunnion comes from the French word ‘trognon’ meaning trunk was originally related to the cylindrical protrusion coming out of each side a military cannon allowing the angle of the cannon to be raised or lowered so you could hit the right target. The trunnion mounting also allowed the cast metal of the cannon itself to expand due to the heat generated from its repeated firing. If no such allowance were made for the thermal expansion there may have been a risk of the cannon cracking whilst being fired with obviously disastrous consequences.
In a similar way we want a facility to be able to rotate our jet engines within their mounting so we can set the angle of thrust coming out the back of the engine to what we desire and we also need to allow them to expand and contract relative to the varying amount of heat they are subjected to during operation and when not in use. The tops of the trunnion mounting points are also removable so that we can both install and remove the engines for servicing. The following sketch and photos show this discussion upon trunnion mounting points.
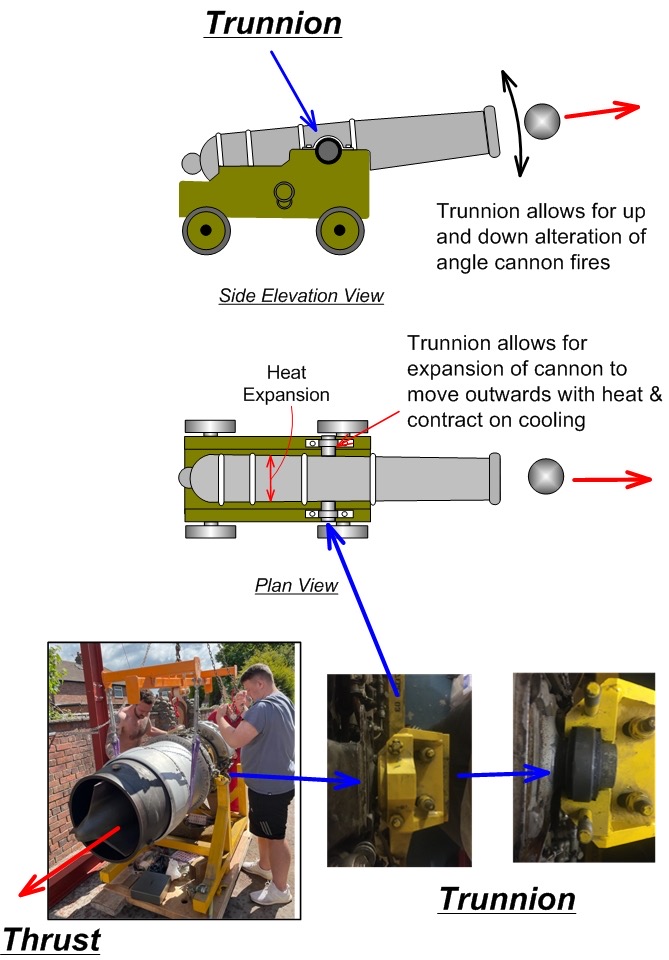
Other than being wrapped up in bringing everything together for this twin jet engine cradle to be fabricated, that is where we are currently up to with things at the moment.
Signing off for this month and as people around the world come to terms with the loss of our great Queen; the following quotation from Her Majesty Queen Elizabeth II seems very apt for those involved, assisting and supporting our little project of building and running our jet hydroplane Longbow:
“I know of no single formula for success. But over the years I have observed that some attributes of leadership are universal and are often about finding ways of encouraging people to combine their efforts, their talents, their insights, their enthusiasm and their inspiration to work together”.
God save our Queen, long live our noble King, Charles III.